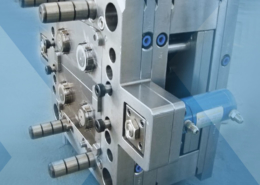
Fakuma exhibit: Injection compression moulding of IML thin-walled cups - thin wa
Author:gly Date: 2024-09-30
1,346 polymer and metal AM companies and 143 end-users. Consumer products AM generated $2.6 billion in 2023. Segment expected to grow to $28 billion by 2033 at 26.8% CAGR. This new market study fro...
Hi-Tech also has a strong presence in similar markets, served from its existing facilities in Waterlooville, Hampshire and Kosice, Slovakia. The addition of Sabre to the Group is anticipated to bring further benefits for customers and employees of both Sabre and Hi-Tech.
Thanks to a tip from Anna Chase, Senior Additive Manufacturing Engineer at the LEGO Group, pointing to an entry on the New Elementary LEGO fan blog, we learned that the duck is actually the second official LEGO 3D printed piece. The very first one, released in 2019, was perhaps even more appropriately, the arm of a drafting machine. It was found inside – and probably never made it out of – a very unique LEGO set that represented the opening ceremony of the System House, a flagship office in Billund built in 1958.
Neil Sibley, CEO of Hi-Tech, said: “I am delighted with the acquisition of Sabre, they have some innovative solutions, a complimentary range of customers and products, and are a really good fit with Hi-Tech.”
Sabre is a manufacturer of technical injection mouldings and assemblies. Their moulding machines are all processor controlled and range in clamp size from 7 to 380 tonnes, with the ability to mould components weighing just fractions of a gram up to 1,500 grams. They have been operating since 1995 from their facility in Letchworth, Hertfordshire.
As explained in a story by Brickfanatics.com, the classic wooden duck is a piece of LEGO history, recreated in modern bricks for 2020s 40501 The Wooden Duck, which is available exclusively at the LEGO House in Billund, Denmark. While that 621-piece set includes a display stand, the real magic happens when you lift it off and pop it on a flat surface: pulling the string turns the wheels and snaps the beak, just like the wooden duck from 1935.
Sabre will remain in its existing facility in Letchworth, and the current director, Keith Jenkins will remain with the business to enable a smooth transition.
Keith Jenkins, director of Sabre, said: “We are thrilled to be part of the Hi-Tech Group and are looking forward to the opportunities and added services this will bring to Sabre and its customers.”
When you visit any web site, it may store or retrieve information on your browser, mostly in the form of cookies. Control your personal Cookie Services here.
Although surface quality is lower than injection molded parts, the use of 3D printing made sense for LEGO as this is an extremely rare piece produced in very low numbers (whereas the duck shows integrated functional capabilities that are just not possible with injection molding). It is particularly appropriate that LEGO used 3D printing on this part as a drafting machine is a device for producing technical drawings that engineers, product designers and architects use before the advent of computer-aided design (CAD).
The set was made available as part of the “Inside Tour” goodie bag distributed during one of the very exclusive events accessible to a small group of fans, with tickets selling out almost instantly. The lucky participants are given behind-the-scenes access to LEGO HQ, hang out with designers and receive all manner of goodies. The 2019 set is especially contained the drafting machine arm. It even has an ID number: Element ID 6286866|Design ID 66237.
Hi-Tech is part of Buckland Group and offers services from design and prototyping through to tooling, manufacturing of engineered plastic injection mouldings and logistics.
As a natural evolution of “toy-technology”, instead of the rigid wire used in the original toy, though, 40501 The Wooden Duck uses a combination of LEGO Technic elements to achieve its internal mechanism. As the next logical evolution, the tiny LEGO 3D printed duck handed out to LEGO House visitors recreates all the same functions of its bigger siblings on a much (much) smaller, fully integrated, scale, as a single piece 3D printed by polymer powder bed fusion.
Showing the capabilities of PBF technology, the diminutive red duck is smaller than a LEGO minifigure, but still manages to pack in all the same functionality of turning wheels and snapping beak when pushed along. According to one Instagram user who got their hands on one, the duck is the ‘first ever official 3D printed LEGO element’, but its availability beyond yesterday’s LEGO House AFOL Day is uncertain. In all likelihood, it’ll probably be exclusive to attendees.
Visitors to the LEGO House’s adult fan event were gifted a LEGO 3D printed duck, which was an ongoing AFOL (Adult Fan Of LEGO) project at the LEGO House development studio. Ronen Hadar, LEGO’s Senior Director Additive Design and Manufacturing proudly shared the project on his LinkedIn feed adding that “the team has been working hard to develop, approve and manufacture this super cool element, in collaboration with our talented designers. This is an important milestone for the team. We are looking forward to share more news with you in the coming future.”
Sabre Plastics Tooling will continue to operate independently under the ownership and leadership of Robin Stimson and the two businesses will cooperate and work closely together providing solutions to the customers of Sabre and Hi-Tech.
A drafting machine comprises a counterbalanced arm leading to a protractor head with a right-angled ruler attached. This enables the draughtsman to draw lines accurately at any angle from anywhere on the page, and it can also be locked to either the horizontal or vertical axis. The LEGO version isn’t quite that flexible but it can move more than an injection molded part would be able to.
GETTING A QUOTE WITH LK-MOULD IS FREE AND SIMPLE.
FIND MORE OF OUR SERVICES:
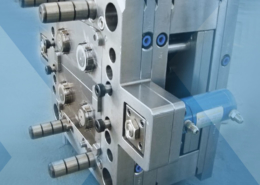
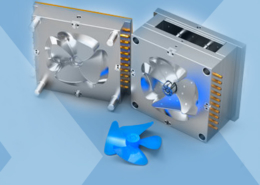
Plastic Molding

Rapid Prototyping
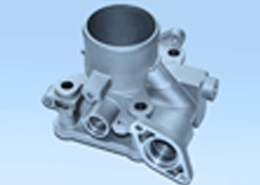
Pressure Die Casting
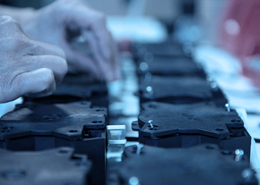
Parts Assembly
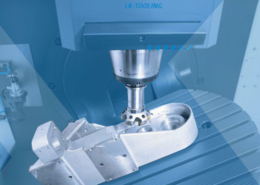