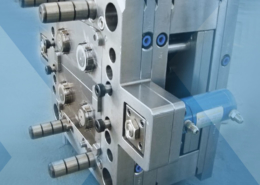
Fakuma exhibit: Injection compression moulding of IML thin-walled cups - thin wa
Author:gly Date: 2024-09-30
● Good surface finish. The molded parts can achieve a Ra value of 3.2 to 18 μm, depending on the mold quality and process parameters.
According to the company, the ECO Polisher is a high-performance ultrasonic polishing machine at an attractive price point ideal for precision polishing and deburring. Its light weight, stable body design and smooth vibration prevent fatigue even after long-time operation making it an operator-friendly tool, Boride explains. The polishing tool is specially designed for efficient use of detail polishing stones including Ceramic Super Stones and Cristones.
This is the last step of injection molding, where quality control engineers check whether the molded parts meet the required specifications and quality standards or not. Only then, the injection molding service provider will ship the ready parts to your home or factory.
USA – Boride Engineered Abrasives has added the Ultrasonic ECO Polisher to its offering of mould polishing equipment and supplies.
China, 6th Sep 2024 - ProleanTech is proud to announce the introduction of its advanced injection molding capabilities, aimed at revolutionizing precision manufacturing. With cutting-edge technology and state-of-the-art machinery, ProleanTech can now offer greater accuracy, faster production times, and enhanced customization for complex parts and components. These new capabilities enable the company to meet the increasingly stringent demands of industries such as automotive, healthcare, and electronics, where precision is critical. By utilizing innovative processes and materials, ProleanTech ensures that clients receive high-quality, cost-effective solutions tailored to their specific requirements, positioning itself as a leader in the precision manufacturing space.
This portal is a brand of Vogel Communications Group. You will find our complete range of products and services on www.vogel.com
Plastic parts manufacturing uses several techniques to transform raw plastics into required shapes, including 3D printing, extrusion, and injection molding. The Injection Molding
After cooling, the mold opens as an ejection system pushes the finished part out. Some parts or custom injection molding might require additional processing, such as trimming, polishing, or assembly.
Injection molding is a precise and cost-effective method for producing consistent plastic parts in large volumes. The injection mold and other tooling setup can be used for millions of cycles under regular maintenance, significantly lowering the per-part cost. The parts can achieve a tolerance of ±0.1 mm to ±0.025 mm throughout the batches. Next, the custom injection molding can make unique and special parts and components for particular needs,
An injection molding machine fixes the mold and other tooling. The machine setup generally includes a feeder that can melt and inject the molten form material through a nozzle connected at one end of it.
Once the injected material is injected, it flows inside, filling all the cavities. Next, the cooling phase provides the timeframe for solidifying it into a final part or product. The cooling time depends on the molding material and what material the mold is made of. For example, aluminum molds cool quickly and are ready for the subsequent cycle, whereas steel molds require more time to cool due to their properties.
Trade confidently with insights and alerts from analyst ratings, free reports and breaking news that affects the stocks you care about.
View source version on King Newswire:ProleanTech Introduces Advanced Injection Molding Capabilities to Enhance Precision Manufacturing
First, what is injection molding? It is a manufacturing process that involves melting and injecting material into a pre-designed mold of steel or aluminum alloys. The mold then cools and solidifies into the final product.
Injection molding is widely popular in thermoplastic parts, ABS, Delrin, Polycarbonate, etc. However, it is not limited to thermosets, composites, and metals. The mold design adjustment and appropriate molding parameters allow for the injection molding of some metals & composites.
Imprint Cookie-Manager About Media Subscription cancellation Privacy General Terms and Conditions Help AI-Guidelines
Next, the plastic pellets are fed into the machine's hopper. The material is then heated until it melts and is injected into the mold cavity under high pressure through a screw or ram injector. The temperature can range from 200°C to 430°C. Meanwhile, the typical injection pressure is 1000 and 5000 psi.
process is popular for precise and large-volume production of plastic parts. This method involves first creating a mold with detailed cavities replicating the intended geometry. Then, the molten plastic is injected into this mold at high pressure. This mold can be used for up to millions of production cycles for identical items.
The ECO Polisher is available through Boride’s network of distributors or online. The supplier offers a demonstration program, offering customers to try the ECO Polisher risk free for 10 days. Customers can learn more about the new Ultrasonic ECO Polisher on the company website.
GETTING A QUOTE WITH LK-MOULD IS FREE AND SIMPLE.
FIND MORE OF OUR SERVICES:
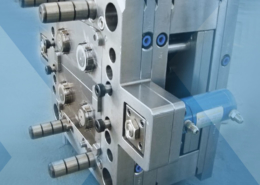
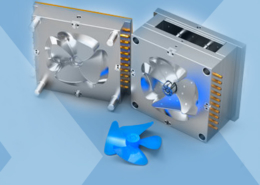
Plastic Molding

Rapid Prototyping
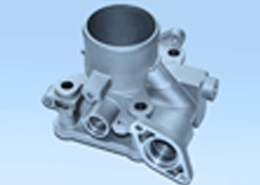
Pressure Die Casting
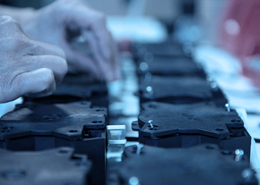
Parts Assembly
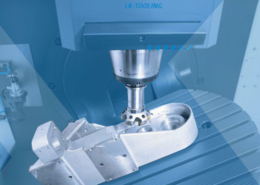