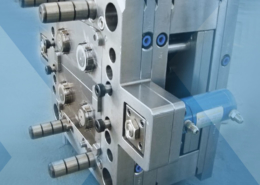
Engel’s Wintec Brand of Injection Molding Machines Starts Distribution in
Author:gly Date: 2024-09-30
“Reynolds American was really successful in bringing multiple suppliers from different areas together and the discussions were really fruitful,” said Diogo de Almeida, regional sales director at Amcor, a key packaging supplier to Reynolds American. “We all have things that we can learn from Reynolds American and hopefully collaborate towards achieving fantastic results in the future for the planet and for all of us.”
“We are continuously researching and developing innovative ways to simplify our packaging to lessen our material use. Where able, removing packaging materials that do not affect the product’s quality or adult consumer experience, is a great stride forward in minimizing Reynolds American’s environmental impact,” said Michael Davis, Master Scientist, Materials Development with the Reynolds American organization.
The polypropylene wrap removal for Vuse Alto Pod and Power Unit has been completed, and the updated packaging is available nationwide.
The P-200 printer, with a build volume of 200 x 200 x 150 mm, is produced on a CNC platform that combines printing and machining for superior accuracy and surface finish. The F-200 furnace sinters parts and can support multiple printers.
Using its patented TrueShape technology, Mantle’s flagship products, the P-200 printer and F-200 furnace, have already cut tooling lead times and costs by more than 50%, the company said. Toolmakers who have installed beta systems include Tessy Plastics, Nicolet Plastics, Fathom Manufacturing, and Westminster Tool. The first full production systems are slated for delivery in the first half of 2023.
A new metal 3D-printing system from San Francisco’s Mantle promises to dramatically reduce the time and cost of creating injection mold tooling.
Westminster Tool integrated a Mantle beta system into its mold-making operations, finding that the printer’s precision lets them bypass many internal manufacturing processes, said founder and president Ray Coombs. “Mantle far surpasses any additive metal technology that we have seen previously.”
Wesley Jones, Senior Director, Packaging & Materials at Reynolds American Inc. brings 24 years of experience in packaging and materials development with extensive expertise in structural design, printing, converting, laminations, and injection molding. His work spans a broad range of materials including fine papers, films, rigid plastics, paperboard, and metals. He is a leader in packaging and material sustainability initiatives and holds a B.S. in Chemical Engineering and an M.S. in Management.
Wisconsin’s Nicolet Plastics will install one of Mantle’s first production systems to bring tool production in house and increase tool complexity. Mantle’s system will let Nicolet “significantly reduce the time it takes to produce production-quality tools and be able to start production in weeks versus months,” according to CEO Tony Cavalco. “Our tool designers and project managers will utilize the Mantle system for projects involving high-volume part manufacturing. Mantle technology will allow us to design conformal cooling channels to reduce molding cycle time and ensure the highest quality products for our customers.”
For example, previously, R.J. Reynolds Vapor Company reduced the use of virgin plastics by removing the polypropylene outer wrap on Vuse Alto Pod and Power Unit vape products, helping to keep approximately 165,000 pounds of plastic out of landfills. But the company didn't stop at removing the plastic wrap, as Alto's packaging is also made of 100% recycle-ready cardboard. While we are proud of this progress, we recognize that there is still work to be done to fully integrate sustainable practices and improve circularity.
Despite design advancements aimed at increasing the recyclability of packaging, infrastructure to recycle many technically recyclable materials remains largely unavailable. Addressing this gap is essential to fostering a circular economy with a self-sustaining ecosystem of materials.
New category products that support our vision to create "A Better Tomorrow" by "Building a Smokeless World" rely on different resources, presenting unique challenges in sourcing materials, production, and responsible disposal. Our operating companies are consistently working to improve circularity and to create less overall waste.
“This is a significant packaging advancement for Reynolds American given that R.J Reynolds Tobacco Company is the organization’s largest operating company. Not only was the conversion to a paper liner the right thing to do for the planet, but it also makes sound business sense,” said Laya Horton, director, packaging development, with the Reynolds American organization.
On-demand digital platform Fathom Manufacturing cut toolmaking time 45%, from 200 to 110 hours, by eliminating or reducing operations including CNC milling, EDM, and polishing.
“There is a massive skills gap in the injection mold-making industry,” said Hillary Thomas, Westminster Tool Vice President. “Mantle’s technology is so intuitive that, with minimal training, we can have someone quickly operating and running this machine. Mantle will help Westminster Tool change how we do business.”
The paper-based packs have begun appearing on retail backbars across the country and will continue rolling out through the year.
The simplified toolmaking system comes at a critical time for the $265-billion molded parts market, asserted one expert.
These packaging swaps support Reynolds American’s circular economy strategy, which encompasses the organization’s commitment to simplifying packaging to improve recyclability, and to reduce the use of virgin materials and finite resources. RJRT’s foil-to-paper improvement additionally supports the organization’s goal of having 100% recycle-ready packaging by 2025.
Learn more about our packaging environmental sustainability initiatives by visiting our website at www.reynoldsamerican.com/product-stewardship/.
Global contract manufacturer Tessy Plastics surpassed 1.25 million cycles on a deodorant packaging mold built with Mantle components and slashed production time 60%, from 150 to 60 hours.
One fundamental substitute has been critical to achieving this milestone: swapping the foil inner bundle in most R.J. Reynolds Tobacco Company (RJRT) cigarette packs.
Swapping packaging materials and design components increases portfolio packaging recyclability and decreases virgin resource use.
Like many other consumer goods organizations, Reynolds American faces ongoing challenges in sourcing and identifying food-grade alternative materials to achieve 100% recycle-ready packaging. In response, the organization recently hosted its inaugural Supplier Sustainability Summit at its largest manufacturing facility, the Reynolds Operations Center outside Winston-Salem, North Carolina. The two-day event brought together senior leaders and sustainability experts from top key suppliers, underscoring their essential role in Reynolds American achieving its sustainability ambitions. By collaborating early and closely with suppliers, the Reynolds American organization aims to leverage its expertise and capabilities in the development of additional innovative packaging solutions.
Geoff Giordano is a tech journalist with more than 30 years’ experience in all facets of publishing. He has reported extensively on the gamut of plastics manufacturing technologies and issues, including 3D printing materials and methods; injection, blow, micro and rotomolding; additives, colorants and nanomodifiers; blown and cast films; packaging; thermoforming; tooling; ancillary equipment; and the circular economy. Contact him at [email protected].
In the previous packaging used by RJRT, foil-lined paper was incorporated inside a paper box. The recent switch substitutes the inner bundle with paper, instead of a foil-paper lamination, thereby making both the liner and box paper-based and increasing recyclability. All packs are enclosed in a polypropylene wrap for benefits such as product freshness to maintain a consistent product experience. This wrap must be removed by the adult consumer prior to recycling.
Reynolds American portfolio products and packaging are subject to extensive regulation, which substantially limits product and packaging changes. All product and packaging changes are implemented in compliance with all applicable regulations.
The system employs Mantle’s H13 and P2X tool steels, which perform like traditional materials in secondary operations such as machining, polishing, coating, and laser welding. Tool paths and machine instructions are automated with the system’s easy-to-use software.
The new RJRT packs continue to be made from paperboard certified by the Programme for the Endorsement of Forest Certification, advancing sustainable forest management. Furthermore, 95% of cigarette packs across the portfolio are labeled to educate adult consumers on proper waste disposal and recycling.
Reynolds American is championing circular economy principles by swapping and reducing product packaging materials to increase recyclability and reduce use of virgin materials. The packaging trades have resulted in over 90% of the packaging in the Reynolds American organization’s portfolio being recycle-ready and the use of fewer finite resources.
GETTING A QUOTE WITH LK-MOULD IS FREE AND SIMPLE.
FIND MORE OF OUR SERVICES:
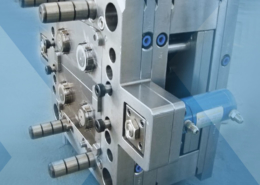
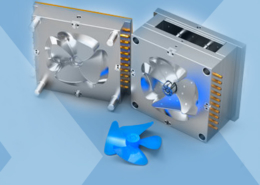
Plastic Molding

Rapid Prototyping
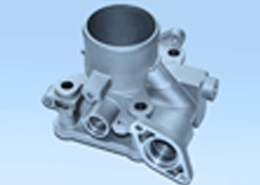
Pressure Die Casting
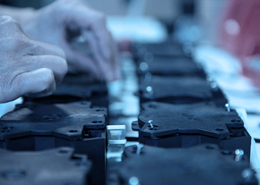
Parts Assembly
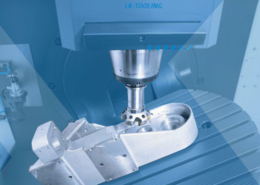