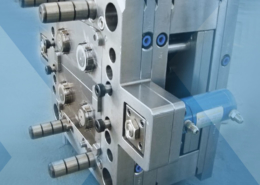
Converting Silicone-Coated Airbag Scrap into Injection-Grade Polyamide 66 - inje
Author:gly Date: 2024-09-30
Join Engel in exploring the future of battery molding technology. Discover advancements in thermoplastic composites for battery housings, innovative automation solutions and the latest in large-tonnage equipment designed for e-mobility — all with a focus on cost-efficient solutions. Agenda: Learn about cutting-edge thermoplastic composites for durable, sustainable and cost-efficient battery housings Explore advanced automation concepts for efficient and scalable production See the latest large-tonnage equipment and technology innovations for e-mobility solutions
Plastics Technology’s Tech Days is back! Every Tuesday in October, a series of five online presentations will be given by industry supplier around the following topics: Injection Molding — New Technologies, Efficiencies Film Extrusion — New Technologies, Efficiencies Upstream/Downstream Operations Injection Molding — Sustainability Extrusion — Compounding Coming out of NPE2024, PT identified a variety of topics, technologies and trends that are driving and shaping the evolution of plastic products manufacturing — from recycling/recyclability and energy optimization to AI-based process control and automation implementation. PT Tech Days is designed to provide a robust, curated, accessible platform through which plastics professionals can explore these trends, have direct access to subject-matter experts and develop strategies for applying solutions in their operations.
Founded in 1973 by Sholtis’ father, Charles E. Sholtis, in Bridgeport, Conn., as Prototype Molding Co. with one Arburg C4B press in a 19th century mill building, PMT began life with a lot of medical molding business. After opening a satellite facility in 2001 in El Paso, PMT completely shifted operations to Texas in 2004, trading medical customers for ones in automotive, business equipment and industrial goods, as it took on more work with NAFTA-propelled maquiladoras.
Gifted with extraordinary technical know how and an authoritative yet plain English writing style, in this collection of articles Fattori offers his insights on a variety of molding-related topics that are bound to make your days on the production floor go a little bit better.
Say “manufacturing automation” and thoughts immediately go to the shop floor and specialized production equipment, robotics and material handling systems. But there is another realm of possible automation — the front office.
No one’s 2020 plans survived the pandemic unscathed, including those of Plastic Molding Technology Inc. But this injection molder’s vision of how it would continue to thrive as it approaches its fifth decade was simply deferred, not denied.
Exhibitors and presenters at the plastics show emphasized 3D printing as a complement and aid to more traditional production processes.
Ultimately, PMT did not proceed with the expansion it announced at the beginning of February, first pausing and then canceling the move. That call ultimately benefited its building neighbors, who were no longer in a position to move, amidst the pandemic.
In this collection, which is part one of a series representing some of John’s finest work, we present you with five articles that we think you will refer to time and again as you look to solve problems, cut cycle times and improve the quality of the parts you mold.
St. Joseph Plastics grew from a simple grinding operation and now pursues growing markets in recycled PP, food-grade recycled materials, and customized post-industrial and post-consumer compounds.
Once completed, the class 100,000 cleanroom addition will include a new material drying and conveying system, placed outside the room, delivering resin in a closed system to the presses, with space for assembly and packing. Each machine will feature automation and run “basically a lights-out operation tied in to IQMS Real Time,” Sholtis says.
While the major correction in PP prices was finally underway, generally stable pricing was anticipated for the other four commodity resins.
Plastics Technology covers technical and business Information for Plastics Processors in Injection Molding, Extrusion, Blow Molding, Plastic Additives, Compounding, Plastic Materials, and Resin Pricing. About Us
In this collection of articles, two of the industry’s foremost authorities on screw design — Jim Frankand and Mark Spalding — offer their sage advice on screw design...what works, what doesn’t, and what to look for when things start going wrong.
The Plastics Industry Association (PLASTICS) has released final figures for NPE2024: The Plastics Show (May 6-10; Orlando) that officially make it the largest ever NPE in several key metrics.
Resin drying is a crucial, but often-misunderstood area. This collection includes details on why and what you need to dry, how to specify a dryer, and best practices.
Introduced by Zeiger and Spark Industries at the PTXPO, the nozzle is designed for maximum heat transfer and uniformity with a continuous taper for self cleaning.
Negri Bossi, for its part, has shipped in a hand-operated unit that was built in 1946 (background in the photo), one year before the company was officially incorporated. The NB28 15-tonne press was the first machine manufactured in Italy and it was sold to a factory near Bergamo for 450,000 lira (€232 in today’s money) to mold buttons from polystyrene.
Learn about sustainable scrap reprocessing—this resource offers a deep dive into everything from granulator types and options, to service tips, videos and technical articles.
Located on the frontier between offshore and the onshore, just 10 minutes from the Ysleta Port of Entry on the border with Mexico, PMT has a unique perspective on the flow of manufacturing work to and from the U.S. and overseas.
Take a deep dive into all of the various aspects of part quoting to ensure you’ve got all the bases—as in costs—covered before preparing your customer’s quote for services.
Mold maintenance is critical, and with this collection of content we’ve bundled some of the very best advice we’ve published on repairing, maintaining, evaluating and even hanging molds on injection molding machines.
Processors with sustainability goals or mandates have a number of ways to reach their goals. Biopolymers are among them.
The aim of this presentation is to guide you through the factors and the numbers that will help you determine if a robot is a smart investment for your application. Agenda: Why are you considering automation? What problems are you trying to solve? How and why automation can help Crunch the numbers and determine the ROI
Across the show, sustainability ruled in new materials technology, from polyolefins and engineering resins to biobased materials.
Despite price increase nominations going into second quarter, it appeared there was potential for generally flat pricing with the exception of a major downward correction for PP.
That expansion was part of the company’s revised strategic plan, initiated back in 2019. As we know now, events were already in motion that would render moot the best laid plans of every company and individual in 2020. Just two days before PMT’s press release about its expansion, the U.S. declared a public health emergency in response to the coronavirus, some three days after the World Health Organization (WHO) declared a global health emergency.
In this three-part collection, veteran molder and moldmaker Jim Fattori brings to bear his 40+ years of on-the-job experience and provides molders his “from the trenches” perspective on on the why, where and how of venting injection molds. Take the trial-and-error out of the molding venting process.
Join Wittmann for an engaging webinar on the transformative impact of manufacturing execution systems (MES) in the plastic injection molding industry. Discover how MES enhances production efficiency, quality control and real-time monitoring while also reducing downtime. It will explore the integration of MES with existing systems, emphasizing compliance and traceability for automotive and medical sectors. Learn about the latest advancements in IoT and AI technologies and how they drive innovation and continuous improvement in MES. Agenda: Overview of MES benefits What is MES? Definition, role and brief history Historical perspective and evolution Longevity and analytics Connectivity: importance, standards and integration Advantages of MES: efficiency, real-time data, traceability and cost savings Emerging technologies: IoT and AI in MES
Thousands of people visit our Supplier Guide every day to source equipment and materials. Get in front of them with a free company profile.
Both celebrate their 75th anniversary this year, both companies have red in their logo, and both are now under the same roof at K 2022 in Düsseldorf, Germany. Japan’s Nissei Plastic Industrial and Italy’s Negri Bossi are exhibiting jointly for the first time in hall 15, booth B22, after Nissei acquired Negri Bossi in 2020. Also present at the booth is robot maker Sytrama, part of the Negri Bossi group.
The coronavirus pandemic never forced PMT to cease production, fulfilling a commitment to customers. “We never did shut down,” Sholtis says. “We ran 24/7 even if it meant running with a skeleton crew.” This was achieved by focusing on protecting its people, Sholtis explained, as PMT worked to procure PPE and look at countermeasures and resources to keep its workers safe and working. “It all paid off in the long run because we were able to stay open. We had a few close calls with respect to COVID and the factory, but as it turns out, the factory is one of the safest places to work during COVID.”
Successfully starting or restarting an injection molding machine is less about ticking boxes on a rote checklist and more about individually assessing each processing scenario and its unique variables.
On Feb. 5, 2020, Plastic Molding Technology Inc. (PMT) announced plans to lease the unoccupied 39,000 ft2 of its building in El Paso, Texas. To be completed by the fourth quarter of last year, the move would give the 47-yr-old custom injection molder nearly 100,000 ft2 of total space, with room to add more value-added operations and cleanroom molding.
Additive technology creates air pockets in film during orientation, cutting down on the amount of resin needed while boosting opacity, mechanical properties and recyclability.
Stephen has been with PlasticsToday and its preceding publications Modern Plastics and Injection Molding since 1992, throughout this time based in the Asia Pacific region, including stints in Japan, Australia, and his current location Singapore. His current beat focuses on automotive. Stephen is an avid folding bicycle rider, often taking his bike on overseas business trips, and is a proud dachshund owner.
Despite the coronavirus, PMT pivoted to a new plan, and in February 2021, one year after it announced the now abandoned expansion, it took delivery of two new all-electric 110-ton Maruka Toyo injection molding machines. Those machines will occupy a new 1400-ft2 white room, which is to be completed by March. That space will eventually be a class 100,000 cleanroom that can house five machines, as the company seeks to complete its ISO 13485 certification for medical-device production by July. Those weren’t the only investments the company made last year, adding five new injection molding machines—four 200-ton and one 300-tonner—with accompanying robotics.
PMT was bullish about medical prior to COVID-19, but since the pandemic laid bare the shortcomings of OEMs’ far-flung global supply chains, the company is feeling even more optimistic about its prospects to win and keep new business. “I think we can see the writing on the wall,” Sholtis says. “The strategy for a lot of pharmaceutical companies and healthcare companies is they want to reshore.”
technotrans says climate protection, energy efficiency and customization will be key discussion topics at PTXPO as it displays its protemp flow 6 ultrasonic eco and the teco cs 90t 9.1 TCUs.
In its 45th year, Precision Molded Plastics has carved out a technology and market niche, growing not just when opportunities arise but when they make sense, after its leader changed careers to keep the family business from changing hands.
This Knowledge Center provides an overview of the considerations needed to understand the purchase, operation, and maintenance of a process cooling system.
Nissei and Negri Bossi have brough some of their oldest injection molding machines to the show. The YD-2 in the foreground of the photo dates back to 1960; it was Nissei’s first production model after it was incorporated as an injection machine maker in 1957. With a clamping force of 30 tonnes, the YD-2 on show was used for more than 40 years by a processor molding various resins, including polyacetal, polystyrene, and PVC, before being donated to the Nissei museum.
Reinvention is essential at Capital Polymers, a toll recycler that has completely transformed its operation in a short period of time.
“We were focused on technical auto markets,” Sholtis says, “so we’re getting back to our roots, but this time we’re embracing it in a more straightforward fashion, building out a white room and eventually going to a full cleanroom.”
One year after canceling one expansion plan, in the midst of implementing a different expansion plan, Sholtis sees the pandemic as a teachable moment with a silver lining of optimism as the world and the country moves past it. “We have a lot of lessons learned from it, that’s for sure,” he says. “It’s an exciting time to be a manufacturer. I think plastics is going to play an even greater role with the reshoring. We may be beaten and battered after the pandemic wave of recession last year, but we are back on track and we are unbroken.”
After successfully introducing a combined conference for moldmakers and injection molders in 2022, Plastics Technology and MoldMaking Technology are once again joining forces for a tooling/molding two-for-one.
Sholtis says the anecdotal talk of work coming back to the U.S. is more than idle chatter. “I’m seeing a surge in cost studies, requests for quotes, everything from straight injection molding to small subassemblies, so whether we use automation to make the subassembly here or we use direct labor in Texas.”
Formnext Chicago is an industrial additive manufacturing expo taking place April 8-10, 2025 at McCormick Place in Chicago, Illinois. Formnext Chicago is the second in a series of Formnext events in the U.S. being produced by Mesago Messe Frankfurt, AMT – The Association For Manufacturing Technology, and Gardner Business Media (our publisher).
Across all process types, sustainability was a big theme at NPE2024. But there was plenty to see in automation and artificial intelligence as well.
Ultradent's entry of its Umbrella cheek retractor took home the awards for Technical Sophistication and Achievement in Economics and Efficiency at PTXPO.
Discover how artifical intelligence is revolutionizing plastics processing. Hear from industry experts on the future impact of AI on your operations and envision a fully interconnected plant.
While the melting process does not provide perfect mixing, this study shows that mixing is indeed initiated during melting.
Mike Sepe has authored more than 25 ANTEC papers and more than 250 articles illustrating the importance of this interdisciplanary approach. In this collection, we present some of his best work during the years he has been contributing for Plastics Technology Magazine.
“We actually had a reasonably good January and February; March was kind of telling; and then came April,” PMT CEO Charles A. Sholtis recalls. As customer shutdowns began last spring, Sholtis says PMT saw a 45% drop in sales, month over month, last April.
This month’s resin pricing report includes PT’s quarterly check-in on select engineering resins, including nylon 6 and 66.
After more than two decades in the industry, Rodney Davenport was given the opportunity to create an injection molding operation in his own vision, and — in keeping with the product he was making — to do so from the ground up.
Negri Bossi brought a molding machine to the K that is older than the show itself, which is marking its 70th anniversary this year.
In the before times, PMT laid out in its strategic plan an intent to return to medical, with a boost from BIO El Paso-Juarez, a nonprofit created in part to accelerate the formation, expansion/retention and attraction of biomedical enterprises in the region. PMT received a training grant from the nonprofit to support its bid for ISO 13485 certification, including auditor training.
More recent highlights at the joint Nisse/Negri Bossi booth include an injection molding machine outfitted with an injection blow molding tool from Spanish mold builder Molmasa that employs factory compressed air. The production cell is being demonstrated molding 500-ml biodegradable PLA jars with in-mold PLA labeling.
While prices moved up for three of the five commodity resins, there was potential for a flat trajectory for the rest of the third quarter.
In a time where sustainability is no longer just a buzzword, the food and beverage packaging industry is required to be at the forefront of this innovation. By adopting circular packaging processes and solutions, producers can meet regulatory requirements while also satisfying consumer demand and enhancing brand reputation. Join Husky to learn more about the broader implications of the circular economy — as well as how leading brands are leveraging this opportunity to reduce costs, increase design flexibility and boost product differentiation. Agenda: The cost and operational benefits of embracing circularity Key materials in circular packaging — including rPET and emerging bioplastics How to design a circular food and beverage package Strategies for selecting sustainable closures to future-proof packaging solutions Optimization and streamlining of production processes for enhanced efficiency How Husky Technologies can enable your sustainable success
Join KraussMaffei for an insightful webinar designed for industry professionals, engineers and anyone interested in the manufacturing processes of PVC pipes. This session will provide a comprehensive understanding of the technology behind the production of high-quality PVC pipes: from raw material preparation to final product testing. Agenda: Introduction to PVC extrusion: overview of the basic principles of PVC pipe extrusion — including the process of melting and shaping PVC resin into pipe forms Equipment and machinery: detailed explanation of the key equipment involved — such as extruders, dies and cooling systems — and their roles in the extrusion process Process parameters: insight into the critical process parameters like temperature, pressure and cooling rates that influence the quality and consistency of the final PVC pipes Energy efficiency: examination of ways to save material and energy use when extruding PVC pipe products
Sholtis said these discussions might have led to team members being encouraged to take mental health days, but there were zero lost work days in 2020, despite everything. That was a result of a renewed focus on safety in 2019. “The number one thing coming into the pandemic was take care of our team members, be safe,” Sholtis says. “We’ve got to take care of ourselves, because if we don’t, we’re not going to have a business.”
When, how, what and why to automate — leading robotics suppliers and forward-thinking moldmakers will share their insights on automating manufacturing at collocated event.
The challenge of navigating that fog made PMT’s weekly management meeting, now held virtually, a must-attend. “I think it’s vital that we at least show up,” Sholtis says. “It’s non-negotiable.” These get-togethers addressed many normal to-do-list items—onboarding a new employee, locating a raw material that’s in short supply, air shipping a tool—as well as how not normal the situation was. “We’d also check into everybody’s health,” Sholtis says. “We’d talk up overall health and the psychological aspects of this new paradigm—working remotely and working under some stress with respect to the pandemic. I think it’s important that leaders take that into account.”
Nowhere is this more evident than in the fact that PMT’s value-added offerings not only include typical services like pad printing, hot stamping, welding, assembly, and packaging, but what it calls “supply-chain value added.” That means offering services like local daily deliveries to customer production lines, vendor-managed inventory, stocking agreements, global sourcing for components and Mexican assembly options.
In this collection of content, we provide expert advice on welding from some of the leading authorities in the field, with tips on such matters as controls, as well as insights on how to solve common problems in welding.
While prices moved up for three of the five commodity resins, there was potential for a flat trajectory for the rest of the third quarter.
Immediately prior to joining PMT in 1986, Sholtis served as a U.S. Navy officer for three years, and to this day he emphasizes tactics and strategy in business planning. “One of the things I’ve always been a proponent of is: stop, make your assessment, and the put together an action plan going forward.” In the very fluid early days of the pandemic, PMT’s management team identified and evaluated its business options, laying out what steps would need to be taken on a daily, weekly and monthly basis. “We just set up a clear line of communication with our supply base, our employee team, and our customers,” Sholtis says. “One of the biggest factors was being able to peer through the fog of war to see where things were going.”
Multiple speakers at Molding 2023 will address the ways simulation can impact material substitution decisions, process profitability and simplification of mold design.
Core Technology Molding turned to Mold-Masters E-Multi auxiliary injection unit to help it win a job and dramatically change its process.
“We did medical in New England,” Sholtis says, “but when we relocated the plant in 2004, we lost a lot of that business because it was regional.”
Join this webinar to explore the transformative benefits of retrofitting your existing injection molding machines (IMMs). Engel will guide you through upgrading your equipment to enhance monitoring, control and adaptability — all while integrating digital technologies. You'll learn about the latest trends in IMM retrofitting (including Euromap interfaces and plasticizing retrofits) and discover how to future-proof your machines for a competitive edge. With insights from industry experts, it'll walk you through the decision-making process, ensuring you make informed choices that drive your business forward. Agenda: Maximize the value of your current IMMs through strategic retrofitting Learn how to integrate digital technologies to enhance monitoring and control Explore the benefits of Euromap interfaces and plasticizing retrofits Understand how retrofitting can help meet new product demands and improve adaptability Discover how Engel can support your retrofitting needs, from free consultations to execution
Second quarter started with price hikes in PE and the four volume engineering resins, but relatively stable pricing was largely expected by the quarter’s end.
Sustainability continues to dominate new additives technology, but upping performance is also evident. Most of the new additives have been targeted to commodity resins and particularly polyolefins.
Mixed in among thought leaders from leading suppliers to injection molders and mold makers at the 2023 Molding and MoldMaking conferences will be molders and toolmakers themselves.
August 29-30 in Minneapolis all things injection molding and moldmaking will be happening at the Hyatt Regency — check out who’s speaking on what topics today.
GETTING A QUOTE WITH LK-MOULD IS FREE AND SIMPLE.
FIND MORE OF OUR SERVICES:
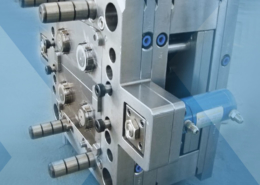
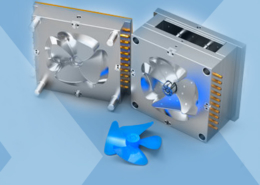
Plastic Molding

Rapid Prototyping
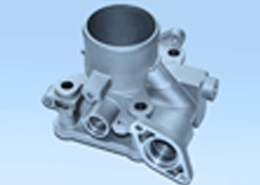
Pressure Die Casting
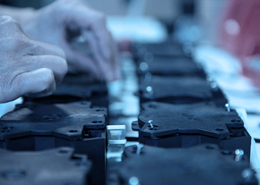
Parts Assembly
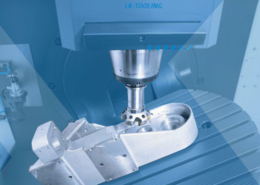