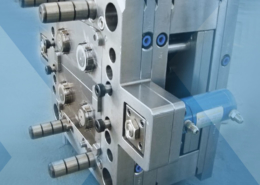
Conventus Polymers Now a Distributor for SABIC Specialties in North America - ul
Author:gly Date: 2024-09-30
“We’ve not eliminated jobs and, in fact, automation has increased the number of jobs we have,” said Ignatowski. He acknowledges that the jobs are more technical in nature: “The people who run the plants are called Process Technicians. Robotics do the repetitive tasks while people perform the technical jobs, [but] we have never replaced a person because of the implementation of technology,” stressed Ignatowski.
Ignatowski told of a recent high-level meeting with a customer in Prism’s Texas plant. The customer told Prism that it was “one of the best suppliers but that it wanted to put as much business in Mexico, as possible.” They wanted us to site a plant in Mexico, said Ignatowski. “I told them we’ll do that, but we’ll have to add cost to the components because we have no labor content at the Texas plant, which means we won’t realize any labor savings, and the infrastructure costs are higher in Mexico. We’re now getting a significant amount of business from the customer as it localizes its requirements in Texas, and we’re shipping parts to its plant in Mexico. We’re able to do that because of our automation and subsequent quality record. It comes down to the right jobs for the right work.
The natural-fiber bumpers developed by Bcomp are a sustainable alternative to the GT4’s existing carbon-fiber panels, matching their mechanical performance while improving safety.
A full sustainability analysis concluded that the natural-fiber bumpers offered a total material emission reduction of 90% compared with the carbon-fiber parts as well as an 85% reduction in CO2 emissions from cradle-to-gate, considering all production steps from raw material to final part.
Prism recently installed a new molding line with three collaborative robots. One robot hands a part to another robot, which hands it off to a third robot, which performs a final inspection and places the part in a box.
Swiss sustainable lightweighting company Bcomp is now supplying its high-performance natural-fiber technologies to HWA AG — development partner of Mercedes-AMG — for the new front bumpers on Mercedes-AMG GT4 race cars. Bcomp’s bodywork will provide a sustainable alternative to the GT4’s existing carbon-fiber panels, offering equivalent mechanical performance in stiffness and weight and improving safety.
The company’s “Technology First” approach allows it to compete on a global scale and win back jobs from Europe, China and Mexico.
Until she retired in September 2021, Clare Goldsberry reported on the plastics industry for more than 30 years. In addition to the 10,000+ articles she has written, by her own estimation, she is the author of several books, including The Business of Injection Molding: How to succeed as a custom molder and Purchasing Injection Molds: A buyers guide. Goldsberry is a member of the Plastics Pioneers Association. She reflected on her long career in "Time to Say Good-Bye."
One advantage of Prism’s operating philosophy is that it has allowed the company to build its human resource requirements around its installed automation technology. Ignatowski explained that while some companies might hire a large number of people at first, then decide to automate and lay off 80% of their work force, Prism deployed automation technology from the get go.
Technology has also brought another benefit to Prism. Because of its rapid growth, the company identified a need for additional warehouse space. While some companies might knock out a wall and add on a brick-and-mortar solution, Prism resolved its problem with technology. “We came up with the Very Narrow Aisle Racking system that greatly reduced the space separating rack units,” Ignatowski explained. “Pallets are placed and retrieved using an automated forklift that follows an embedded wire in the floor. An operator drives the fork lift, but in the aisle they can only go forward and backward. That system allows us to have three inches of clearance on the fork lift in the aisle. We implemented this in Chesterfield and the new acquisition in Pennsylvania, as well.”
“We are incredibly excited to see HWA and the Mercedes-AMG GT4 race car program embracing sustainable, natural-fiber bodywork,” said Christian Fischer, CEO and co-founder of Bcomp. “With equivalent stiffness and weight, increased safety, and an 85% reduction in carbon emissions, it is a fantastic improvement that we reached together. Development coincided with the height of the pandemic, and it was challenging at times. In fact, our first bumper build, design fitting, optimizations, and revisions were all achieved during the pandemic — a testimony to the hard work and persistence of all involved,” said Fischer.
As manufacturing became global, Prism relied on its automation technology to remain competitive. Under the Technology First banner, the company has removed almost all manufacturing labor costs from its cost model. “We’re not showing labor in our cost model breakout—that is what technology has done for us,” said Ignatowski.
Furthermore, part of the project was to validate the HWA in-house paint processes with ampliTex and powerRibs, optimizing the A-surface quality of the part up to a level that meets the quality standards of HWA and Mercedes-AMG motorsport. Production of the old carbon-fiber bumpers has now ceased, and all customer teams will receive the new Bcomp version with their next orders.
“Because of NAFTA, we’re in great shape and can boast that our components are 100% made in the USA,” Ignatowski added. “We can compete with low-cost countries because of our approach to technology, lean operations and designing in quality throughout the process. In fact, while others are shipping parts from China, we’re shipping products to China.”
Bcomp’s award-winning technologies are already used in 16 racing series around the world, but their applications are not restricted to motorsport. From automotive interior panels and bodywork to luxury yachting and the European Space Agency’s latest natural-fiber satellite panels, Bcomp’s technologies are relied upon wherever weight, stiffness, and sustainability are important. With the GT4 cars closely based on their road-going counterparts, these racing projects open up opportunities for future high-performance road applications.
Those are just two examples of how Prism’s Technology First approach solves problems, but the benefits are far reaching. It helps Prism maintain lean operational costs, which allows the company to compete on a global scale and win back jobs back from Europe, China and Mexico.
Anne Mink, Manager Technical Development, HWA AG, commented: “The topic of sustainability plays a major role in our company. Several awards for our efforts in the area of environmental protection are proof of this. Part of our sustainability concept is to evaluate and optimize the product life cycle with regard to environmental aspects as early as in the product development stage. Furthermore, it is our aspiration to constantly adapt our long-standing engineering know-how to current environmental requirements in order to be able to offer our customers sustainable products at the highest technological level. In Bcomp, we have got a development partner with extensive experience in sustainable materials. The result of our cooperation shows that technologically equivalent components can be created from alternative materials.”
Currently, Prism operates four molding facilities: In addition to the plant at its Chesterfield headquarters, the company has a molding footprint in Port Huron, MI; Harlingen, TX; and Meadville, PA. Prism serves the automotive and industrial markets with various components including safety parts, connectors and sensors, electronics housings and steering and drivetrain parts.
Since the new bumper is full natural fiber, it can be used for thermal energy recovery, turning approximately 80% of the energy stored in the part into renewable energy, resulting in a process without hazardous carbon waste or parts that need to go into landfill.
The new bumper uses Bcomp’s ampliTex and powerRibs technologies, which harness the natural advantages of flax fiber. The powerRibs reinforcement grid uses the high specific bending stiffness of flax to efficiently build up height, significantly boosting the flexural stiffness of thin-walled shell elements. The new bumpers are also safer in the event of a crash or collision and decrease the risk of punctures. Unlike the sharp fracturing and splintering of carbon fiber, ampliTex technical fabrics are more ductile on impact, whereas the powerRibs confine the damage zone, minimizing debris and risk to drivers, marshals, and spectators.
The “Technology First” mindset has been a constant at Prism Plastics (Chesterfield, MI ) since the day the custom injection molding company was founded in 1999. “That was a time when molders were plentiful,” said Jeff Ignatowski, Director of Marketing, during a phone interview with PlasticsToday. “We decided then that we’d use technology. We chose the highest technology available in molding machines and robotics. We then standardized equipment: By blending automation and the human element, we have become efficient and cost effective. That mindset exists across the board, so that each of our plants operates exactly the same way.”
As Prism wins more programs, keeping manufacturing on American soil, the result is more high-tech jobs for skilled American workers.
Reverse engineered from HWA’s original, the natural-fiber bumper’s design has been collaboratively optimized over the past 12 months. To ensure that the bumper met all racing regulations and requirements, the HWA team performed extensive mechanical testing and validation. On the HWA testbench, the stiffness of the complete front end of the Mercedes-AMG GT4 was measured, simulating the aerodynamic drag and front diffusor downforce. The tests were conducted with a carbon-fiber bumper as the benchmark and afterward with the new natural-fiber bumper, validating that the newly designed part performs to the same high-performance level.
GETTING A QUOTE WITH LK-MOULD IS FREE AND SIMPLE.
FIND MORE OF OUR SERVICES:
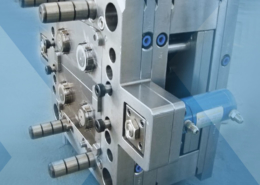
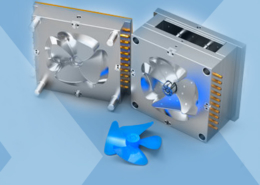
Plastic Molding

Rapid Prototyping
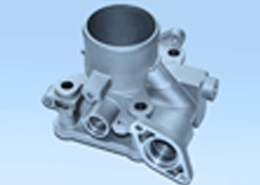
Pressure Die Casting
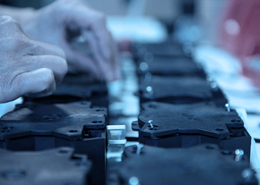
Parts Assembly
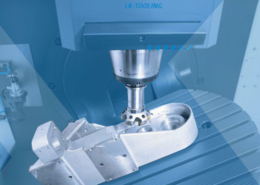