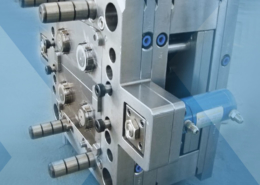
Conformal cooling: How Additive Manufacturing benefits injection moulding - moul
Author:gly Date: 2024-09-30
Lucon TX5007 reportedly has excellent electrical conductivity and mechanical properties. In addition, its outstanding heat resistance makes it suitable for the electrostatic in-line painting process used by automakers that operates at temperatures of 200°C and higher. At the same time, the alloy delivers dimensional stability thanks to its low coefficient of linear thermal expansion (CLTE).
In general, using plastics in place of steel/aluminum contributes to automotive lightweighting. When a plastic fender is used, the weight of the vehicle is reduced by about 4 kg, which also improves fuel efficiency.
Stephen has been with PlasticsToday and its preceding publications Modern Plastics and Injection Molding since 1992, throughout this time based in the Asia Pacific region, including stints in Japan, Australia, and his current location Singapore. His current beat focuses on automotive. Stephen is an avid folding bicycle rider, often taking his bike on overseas business trips, and is a proud dachshund owner.
So you’ve enjoyed the rapid prototyping and low trial costs with 3D Printing and are now ready to go into production with the final design. To help with this process we are going to look at some of the best injection molding companies and compare our experience with them.
In addition to Lucon TX5007, LG Chem offers a broad portfolio of compounds that can be used for large automotive exterior parts that undergo the powder coating process. These grades can be customized to meet automotive suppliers’ diverse parts requirements for fenders, bumper panels, hoods, tailgates, fuel doors, and side mirrors.
The front fender is located on the side of the vehicle and not only acts as a key factor in the exterior design but also protects wheels from road debris. Consequently, it must be mechanically robust while having an exterior quality that maintains design integrity with the rest of the car body.
Korea’s LG Chem has started supplying carbon nanotube (CNT)–filled engineering plastic compounds to Japan’s Mitsubishi Motors for the front fenders of its RVR, Delica D:5, and Outlander models. The injection-molded fenders can be powder-coated thanks to the electrical conductivity of the CNT-filled polyphenylene ether (mPPE) and polyamide (PA66) alloy, dubbed Lucon TX5007.
LG Chem is using CNT, a filler that delivers excellent conductivity even at low loadings, in its engineering plastics to support the diverse requirements of customers. Since this material can cover a wider range of electrical conductivity compared with other carbon fillers such as carbon black and carbon fiber, it is considered an optimal solution for powder coating. LG Chem is currently expanding its capacity for CNT, with a fourth plant expected to come on stream in 2024, which will ensure reliable supply of high-quality products for powder coating, according to the company.
GETTING A QUOTE WITH LK-MOULD IS FREE AND SIMPLE.
FIND MORE OF OUR SERVICES:
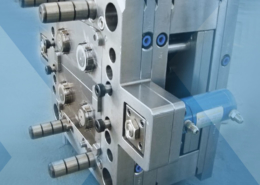
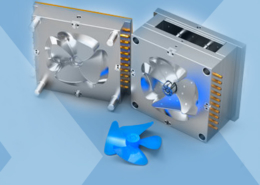
Plastic Molding

Rapid Prototyping
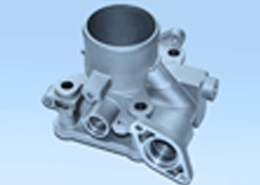
Pressure Die Casting
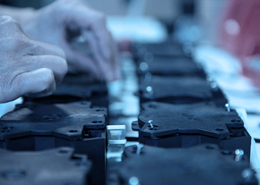
Parts Assembly
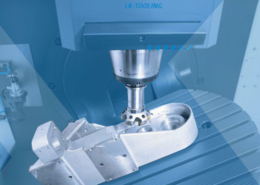