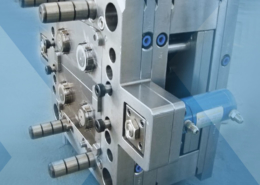
Conformal cooling: How Additive Manufacturing benefits injection moulding - inje
Author:gly Date: 2024-09-30
The engineering students took on the challenge of making a mini-recycling unit as part of the global Precious Plastic initiative, an open-sourced recycling project which allows anyone to create their own plastic recycling facility.
We acknowledge Aboriginal and Torres Strait Islander peoples as the First Australians and Traditional Custodians of the lands where we live, learn, and work.
The United Nations last year warned that unless people changed their habits, there would be more plastic than fish, by weight, in the world's oceans by 2050.
"It would be the dream for everyone to be able to recycle their own plastic and reduce our waste," project materials manager Gabi Newman said.
The team, made up of undergraduate and masters students from a range of different engineering disciplines, will now continue to refine, test and professionalise the unit.
This service may include material from Agence France-Presse (AFP), APTN, Reuters, AAP, CNN and the BBC World Service which is copyright and cannot be reproduced.
Backyard plastic recycling plants could be step closer to reality, with a group of Monash University engineering students creating a portable unit that can fit on the back of a ute.
Comprised of four small machines, the unit first shreds hard plastic — such as flower pots and milk bottles — into pellets before they are melted down.
"In schools they could have this machine and students could make their own rulers. In offices, for example, they could make their own plastic paper clips," project manager Joel Ibrahim said.
From automated robot doctors to water filters, performance drills to medical endoscopes, the engineering and manufacturing of these items involve the inception of ideas, rigorous testing and the relentless pursuit of engineering perfection. Singapore-based company Fu Yu embodies this philosophy through its cutting-edge, one-stop-shop services, which include design and tool fabrication, precision injection moulding, metal injection moulding, product assembly and secondary processes.
Monash University Dean of Engineering Elizabeth Croft said the project was a great example of how students could work towards solving real-world problems.
"All the daily products that use plastics, why can't we take the waste and turn it into things that are useable, structural things? Day-to-day use things," Professor Croft said.
With a presence in Singapore, China and Malaysia, Fu Yu’s comprehensive services cater to various industries, manufacturing precision plastic components for sectors such as medical, automotive, printing, industrial and consumer goods. Its subsidiary, Fu Yu Biomedical, aims to innovate and manufacture medical diagnostics equipment, envisioning a future where simple medical tasks, like blood tests, can be conveniently conducted at home. Fu Yu also offers product design services, rapid prototyping, and full product assembly to meet the ever-evolving needs of the medical sector.
The Monash team wanted to make a portable plant that could be toured around schools and workplaces to raise awareness of how easy and important it is to recycle plastic.
“Our strategic and ambitious expansion plans in the medical field start in Singapore, with future plans to extend our reach into the greater Asean region. We have plants located in Singapore, Malaysia and China, and are actively exploring opportunities in emerging markets like Indonesia, Thailand, Cambodia and Vietnam to meet the growing demand for manufacturing in those regions,” Seow said.
The melted plastic can then be passed through an extruder to make filament for 3D printers, a compressor to make objects such as bowls or structural beams, or an injector which squeezes plastic into moulds.
"So that means bowls, phone cases, we can even make gears. We've just found out we can laser cut, which unlocks numerous potential to make a whole range of products."
Fu Yu is looking to form alliances with complementary service providers in the electronics, batteries, metals, coating, and sterilisation sectors, enabling it to offer an all-in-one solution suite to its customers.
Bottles, containers, trays and plastic bags can be broken down by the machine and transformed into anything that can be made in a mould, including phone cases, bowls and even structural beams.
“We are focused on scaling up and upgrading our capabilities, transitioning from traditional case parts manufacturing to a niche specialisation in high-precision products,” said David Seow, group CEO and board member of Fu Yu. “Our exceptional capabilities in precision tooling and precision moulding and unique ability to engage with our customers at the early product development stage are what truly set us apart.”
"The reason it's such a small unit is so we can pack it up and put it on a ute and transport to wherever we want," Ms Newman said.
GETTING A QUOTE WITH LK-MOULD IS FREE AND SIMPLE.
FIND MORE OF OUR SERVICES:
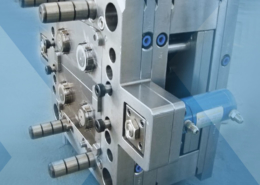
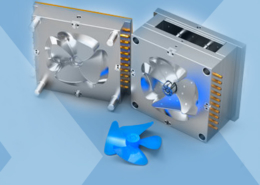
Plastic Molding

Rapid Prototyping
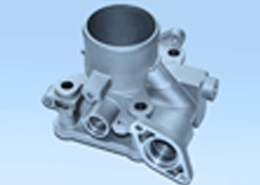
Pressure Die Casting
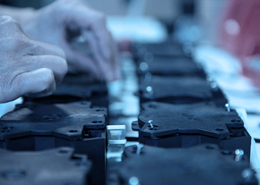
Parts Assembly
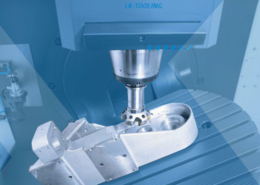