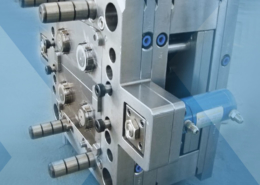
CLA Advises on Sale of PM Mold Company to NewCo Plastics - plastic injection mol
Author:gly Date: 2024-09-30
Sales into auto applications increased by 15% in 2022, of which compound sales for new energy vehicles (NEVs) were up 100%. Kingfa estimates that upwards of 40 kg of its plastic compounds are used in the typical Chinese NEV compared with 30 kg for an internal combustion engine (ICE) car. Kingfa also offers a variety of PP, ABS, PC, and PC/ABS grades with recycled content of 30% to 50% for automotive applications.
In automotive and other applications, “the hidden risk factors of PCR must also be addressed,” said Dennis Wang, Kingfa’s Global Director of Auto Materials, at Chinaplas 2023. “These include wide molecular weight distribution, metal ion residues, and reactive hydroxyl groups. Technologies such as metal passivation and end-capping can be employed to resolve these issues.” Wang estimates that the three major European auto brands and three major OEMs in Japan will require about 400,000 tonnes of PCR annually by 2025.
Chinese compounding giant Kingfa is upbeat on the prospects for plastic compounds with recycled content: By 2025 it aims to have in place one million tonnes/year of capacity in China and overseas for processing post-consumer recycled (PCR) resins. Key consumers of these materials include the automotive and appliance sectors.
Editor in chief of PlasticsToday since 2015, Norbert Sparrow has more than 30 years of editorial experience in business-to-business media. He studied journalism at the Centre Universitaire d'Etudes du Journalisme in Strasbourg, France, where he earned a master's degree.
The 3D-printed molds for the first and second iterations cost less than €2,000 combined. And the technology enabled a two-day design cycle, which is more than 90% faster than conventional metal tooling.
SPT Vilecon said it has begun expanding the range of injection mold prototyping with silicone, metal, and ceramic materials to provide medical device manufacturers with an even wider selection of product development and verification services.
SPT implemented Nexa3D’s Freeform Injection Molding (FIM) technology to help customers shorten time-to-market on complex medical devices in demanding medical-grade materials and to expand on the range of materials that can be quickly and reliably used in prototyping and early device test manufacturing.
Freeform Injection Molding technology from Nexa3D compresses design, iteration, and validation cycle times into a matter of hours rather than weeks.
Injection-molded silicone parts were produced within two days, allowing early verification of key design and performance aspects.
Certified to ISO 13485, Denmark-based SPT Vilecon describes itself as a fully integrated provider of development and manufacturing services to the medical device industry. It offers in-house tool making and injection molding along with other manufacturing services to companies in northern Europe.
The company’s 2.46 million tonnes of compounds shipped in 2021 incorporated 182,000 tonnes of PCR material, including PP, PE, ABS, and PC compounds for appliance, automotive, and packaging applications, with PCR production capacity already pegged at 400,000 tonnes/year. To serve this capacity with high-quality feedstock, Kingfa has established a network of 500-plus recyclers across China.
Kingfa is also working toward expansion of base resin capacities by starting up new polymerization plants for ABS (300,000 tonnes/year) and polypropylene (300,000 tonnes/year) this year, on top of 180,000 tonnes/year of new bioplastics capacity. An additional 400,000 tonnes/year of PP polymerization capacity is slated for startup in 2025, when overall PP resin capacity will have reached 1.2 million tonnes/year.
The patented FIM process uses high-speed Nexa3D printers and xMOLD resin to print injection molding tools that are compatible with thousands of off-the-shelf injection molding materials, including reinforced high-performance feedstocks. The process reduces design, iteration, and validation cycles using end-product materials to a matter of hours rather than weeks.
Medical device manufacturers are tasked with developing elaborate test protocols to ensure that the product in development is safe and meets essential requirements. If these tests are conducted late in the development process, the more onerous and risky they become. SPT Vilecon often works with silicone, a material that is extensively used in medical applications because of its chemical resistance, mechanical performance, and biocompatibility. However, silicone parts are notoriously difficult to prototype and test, since most grades need to be injection molded to achieve their full performance potential, said the company. FIM enabled SPT Vilecon to offer an alternative to a customer developing an intravenous (IV) silicone product — the use of 3D-printed tooling to perform early design and material verification at a fraction of the cost of conventional methods.
Robust and valid prototyping and verification are key to minimizing cost, time, and risk factors in developing medical devices, said SPI Vilecon. FIM is a new toolbox for medical device companies seeking to accelerate their innovation and obtain early verification of part performance and moldability, added the company.
With compounding capacity exceeding 2.5 million tonnes/year positioning the company as the largest plastics compounder globally, Kingfa has traditionally maintained a strong presence in the automotive sector; new capacity in compounding plants in Vietnam and Poland will augment its global supply chain for automotive as well as support other key industries such as electrical & electronics and appliances. Capacity doublings are also on the cards for Kingfa’s Indian and Malaysian compounding assets.
Kingfa has also established polymerization capacity for several advanced engineering plastics including partially bio-based polyamide (20,000 tonnes/year), LCP (6,000 tonnes/year), and PPSU/PES (800 tonnes/year), together with 40,000 tonnes/year of associated compounding capacity. With this portfolio, the company can supply compounds spanning the gamut of performance requirements.
Design input collected from the first tests was integrated in a second iteration that took only a couple of hours to complete. By contrast, conventional metal tooling would have taken more than six weeks to design and procure, and the adjustments needed for the second iteration would have taken an in-house tool-shop a week to complete.
Based on input collected from the first two iterations, the design of the silicone part was approved and manufacturing of a metal tool was initiated with full confidence of part moldability and performance. The in-house tool shop built the final metal tooling in four weeks without iterations.
A supplier of development and manufacturing services to medical device OEMs used Freeform Injection Molding from Nexa3D to accelerate time-to-market and slash prototyping costs for a complex silicone-based IV device. SPT Vilecon explained the process in a recent press release.
The Chinese mega-compounder also plans to expand plastics recycling capacity to one million tonnes/year in China and overseas by 2025.
GETTING A QUOTE WITH LK-MOULD IS FREE AND SIMPLE.
FIND MORE OF OUR SERVICES:
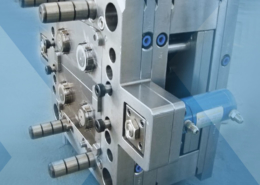
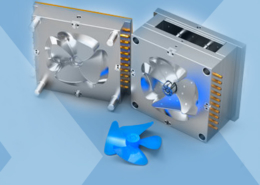
Plastic Molding

Rapid Prototyping
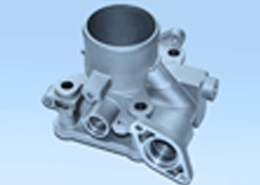
Pressure Die Casting
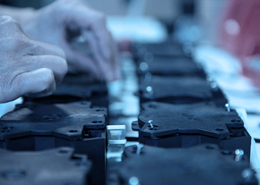
Parts Assembly
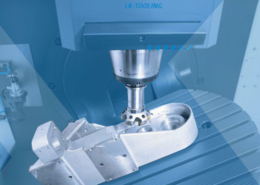