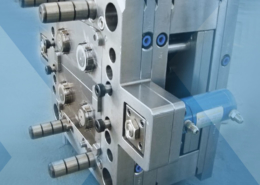
Chemical Recycling of Polycarbonate Reaches Major Milestone - polycarbonate inje
Author:gly Date: 2024-09-30
The input data, definitions, and units are different, and to unify the samples, the data are normalized, as shown in Eq. (22).
From Table 4 and Fig. 11, it can be seen that the influence of the moulding process parameters on warpage deformation is pressing pressure (C) > heating temperature (A) > pressing time (D) > heating time (B), with the pressing pressure having the greatest influence on the warpage deformation of the closed plastic impeller. The best combination of moulding parameters is A3B3C1D4, i.e. heating temperature of 190 °C, heating time of 700 s, pressing pressure of 15 MPa and pressing time of 90 s. Simulation of the process parameters was carried out by ANSYS software to obtain the closed type plastic impeller with the minimum warpage, as shown in Fig. 12. The minimum warpage was 0.0215 mm, which corresponds to a wall thickness of 3.4 mm, and the data was substituted into Eq. (17) to obtain a volume shrinkage rate of 0.628%.
where, \(\upeta \)—The contact friction coefficient between the inner wall of the cavity of the closed plastic impeller and the plastic raw material; \({\mathrm{P}}_{\mathrm{r}}\)—The uniformly distributed pressure of plastic raw materials in the radial direction, \(\mathrm{MPa}\).
Thanikodi, S. et al. Influence of compression molding process parameters in mechanical and tribological behavior of hybrid polymer matrix composites [J]. Polymers 13(23), 4195–4195 (2021).
The closed plastic impeller model is solved to obtain the numerical simulation results of the closed plastic impeller compression molding process under thermodynamic coupling conditions.
The deformation direction is consistent with the direction of the warpage deformation gradient, and the warpage deformation is equal to the maximum value of the gradient, as shown in Eq. (16), i.e. the warpage deformation parameters obtained by ANSYS simulation.
Sixteen sets of process parameters from the orthogonal tests were analyzed by numerical simulation to obtain the simulation results corresponding to each set of process values, which are the warpage deformation of the closed plastic impeller obtained under each set of experimental data.
Jianhan Zhang et al.9 investigated textile composites based on the stereoscopic compression molding properties of three-dimensional surfaces, and numerically simulated the hemispherical molding of the material by the NURBS method. For the shortcomings of the traditional NURBS method, the use of NURBS interpolation curves was proposed to analyze the material forming. The spatial coordinate positions of the warp and weft yarn interweaving points in the fabric under three-dimensional conditions are obtained, which provide a theoretical basis for the prediction of molding defects affecting the product quality.
There are four closed plastic impeller compression molding process parameters and two evaluation indicators, so four neurons are selected for the input layer and two neurons for the output layer29.
For GA-BP neural networks with different nodes inside the hidden layer, the results can be obtained by calculating their mean squared deviation; the higher the number of nodes, the smaller the network error in general, and the higher the overall accuracy, as shown in Fig. 15. When the number of nodes is 9, the network error reaches its minimum value, and the recognition accuracy reaches the highest position, so the final number of nodes in the hidden layer is chosen as 9.
The prediction model of the GA-BP neural network for closed plastic impeller was determined, and a set of process parameter combinations satisfying both warpage deformation and shrinkage were obtained by the multi-objective search function of the NSGA-II algorithm: heating temperature of 187 °C, the heating time of 785 s, pressing pressure of 19 MPa, and pressing time of 85 s.
It can be seen from Table 9 that the warpage of the impeller optimized by the NSGA-II algorithm is reduced from 0.0215 mm to 0.0198 mm, and the shrinkage is reduced from 0.398 to 0.353%. It shows that the NSGA-II algorithm can get better results by optimizing process parameters, and can get a group of process parameters with optimal warpage and shrinkage at the same time.
The BP neural network model is to predict the results by varying the process parameters and is trained on the data obtained from orthogonal experiments of the closed plastic impeller. Therefore, a single implicit layer is sufficient to meet the current demand, and together with the input and output layers, a three-layer structure can be used in this paper.
Kamran, M. J. et al. Optimization and fabrication of pure poly lactic acid (PLA) using hot press compression moulding [J]. IOP Conf. Ser. Mater. Sci. Eng. 1136(1), 012012 (2021).
The comparison of the predicted and true values of warpage deformation and shrinkage obtained for the four process parameters is shown in Fig. 21. As can be seen from the figure, the curves of the GA-BP predicted values and the true values basically overlap, indicating that the GA-BP neural network has a high accuracy to meet the demand.
Sign up for the Nature Briefing: AI and Robotics newsletter — what matters in AI and robotics research, free to your inbox weekly.
Fang, M., Zhu, Z. & Zhang, Z. Numerical simulation of closed plastic impeller molding process and its parameter optimization. Sci Rep 12, 17335 (2022). https://doi.org/10.1038/s41598-022-22260-7
With the help of the Ansys Workbench platform, the closed plastic impeller was simulated numerically with thermal coupling. The model was first imported into the model module Geometry, as shown in Fig. 4. Then each of the imported bodies was numbered to facilitate the selection of parameters and meshing for the subsequent simulation. The material parameters are set in the material module Engineering Date, and the UTR9000 material parameters are shown in Fig. 5.
where, \({q}^{*}\)—Heat flux density, \(\mathrm{W}/{\mathrm{m}}^{2}\); \({k}_{nn}\)—thermal conductivity, W/m °C, Along the \(\frac{\partial T}{\partial n}\) temperature gradient, the minus sign means that heat is transferred from places with high temperature to places with low temperature.
Fan Guangpo, Yu., Guangwen, X. L., Liangzhuo, L. & Difu, Z. Improved PSO-BP algorithm for pressure guidewire temperature and nonlinear compensation [J]. Autom. Instrum. 37(06), 16–20 (2016).
Tansig was selected for the implicit layer, and Purelin was selected for the output layer. The training functions were Traingd, Trainlm, and Trainbfg30. The performance curves of each function were compared, and the Trainlm function with fast convergence and small error was selected. Figure 16, Fig. 17, and Fig. 18 show the performance curves of the three functions, respectively.
In the process of thermoplastic pressing, it is necessary to apply pressure to the mold and keep it for a period of time to ensure that the closed plastic impeller is fully formed21. Proper pressing time can ultimately produce high-quality products, which is of great help in reducing the warpage deformation, and shrinkage of the closed plastic impellers and improving surface gloss, physical and mechanical properties.
Thank you for visiting nature.com. You are using a browser version with limited support for CSS. To obtain the best experience, we recommend you use a more up to date browser (or turn off compatibility mode in Internet Explorer). In the meantime, to ensure continued support, we are displaying the site without styles and JavaScript.
With cellulose powder as its principal ingredient, this new composite will boast the same processability as conventional plastic. Further, the composite’s use of woody biomass as its main constituent will help to cut greenhouse-gas emissions by minimizing the use of fossil-fuel-derived virgin material.
where, \(K_{mn}\)——The sum of the values of the evaluation indicators at the level of the mth process parameter n, \(Q_{mn}\)——The value of the evaluation index at the level of the mth process parameter n, \(k_{mn}\)——The mean value of Kmn, \(R_{m}\)——The nth process parameter extreme difference, \(k_{m\max }\), \(k_{m\min }\)——The maximum and minimum values of the mean value at the mth process parameter.
Huaiqin, X., Hui, C. & Shuangquan, F. Numerical simulation of the curing degree and unsteady temperature field of polymer matrix composite molding process [J]. J. Compos. Mater. 05, 73–76 (2003).
Determine the number of BP neural network layers, the number of neurons in each layer, and the training function of each layer, to establish the structure of the closed plastic impeller BP neural network.
Simplify the theoretical model and approximate the pressure PZ to the average pressure on the section, as shown in Fig. 3.
The closed impeller is an important working element of the centrifugal pump and the core flow-through component1. Its manufacturing technology and quality directly affect the hydraulic performance, cavitation performance, and operation stability of the pump. As one of the main molding processes of the closed plastic impeller, molding has the advantages of simpler mold structure, better dimensional accuracy, and surface smoothness compared with injection molding2. Manufacturing defects such as volume shrinkage and warpage will occur in the molding process of the parts, and the process parameters are one of the important factors affecting the volume shrinkage and warpage of the parts3,4,5. In order to reduce the volume shrinkage and warpage of the parts, the selection of process parameters has been optimized by constant mold trial and mold repair, but this method has not met the requirements of modern design6. The intelligent algorithm is a key link and quality assurance of intelligent industrial manufacturing, and the advantages of the intelligent algorithm in optimizing parameters are applied in many fields. The process parameters can be optimized through the combination of an intelligent algorithm and CAE software so as to reduce the warping deformation and volume shrinkage of plastic parts7.
As there are many curved surfaces on the impeller and die, and the structure is relatively complex, this paper adopts unstructured mesh division23. Under the mesh project of the project, first insert the patch forming method, select tetrahedrons for the method in details of "patch forming method," then insert body sizing under the mesh project, and enter 5 mm for element size; In details of "mesh," click size function in sizing, select proximity and curvature, select medium in correlation center, and select slow in transition. Other settings are shown in Fig. 6.
Equation (15) shows the pressure distribution of the plastic material in the closed plastic impeller cavity in the Z-direction, and the distribution shows obvious exponential characteristics. If the heating temperature of the plastic material in the closed plastic impeller is low, higher pressing pressure is needed, and if the heating temperature is high, the pressing pressure needs to be reduced appropriately.
As can be seen from Fig. 22, the influence of the critical parameters of the forming process on the warpage deformation through neural network analysis is as follows: as the heating temperature increases, the warpage deformation first becomes larger, then smaller, and then larger, with the optimal value between 180 °C and 190 °C; as the heating time increases, the warpage deformation first becomes larger, then smaller and then stable, with the optimal value after 600 s; as the pressing pressure increases, the warpage deformation first becomes smaller and then larger, with the optimal value between 15 and 20 Mpa; as the pressing time increases, the warpage deformation first becomes larger and then smaller, but the pressing time is not too long, with the optimal value between 15 and 20 Mpa. With the increase of pressing pressure, the warpage deformation first becomes smaller and then larger; the optimal value is between 15 and 20 Mpa; with the increase of pressing time, the warpage deformation first becomes larger and then continues to become smaller, but the pressing time is not too long, the optimal value is around 90 s.
The larger the proportion of training samples, the better the results. Generally, 4/5 of the sample data is used for training. There are 16 groups of data in the experiment. 12 groups of data are randomly selected as training samples, which are 2, 3, 4, 6, 7, 9, 10, 11, 13, 14, 15 and 16, respectively. The remaining four data groups are test samples, which are 1, 5, 8 and 12, respectively. The iteration algebra is 50 generations, and convergence is achieved after 19 iterations, as shown in Fig. 20.
Take a group of process parameters of the closed plastic impeller molding process as a group of factors of the orthogonal test, and select the experimental range of process parameters, as shown in Table 3.
Xie Huaiqin et al.8 performed theoretical analysis and calculation based on the theory of curing kinetics and heat transfer, used DSC experiments to obtain the raw data of curing kinetics, and fused both finite difference and finite unit methods. The mathematical model of the relationship between the curing degree values and the temperature field was designed, and the Euler iteration method was proposed to decouple the mathematical model. The relationship between the curing degree and the unsteady temperature field is determined by numerical simulation, which provides sufficient theoretical guidance for the selection of the compression molding process.
Closed-type plastic impeller molding is done through the mechanical pressure generated by a hydraulic press to make the concave and convex mold close the mold, thus pressing the plastic material into the required shape. The closed-type plastic impeller molding process is to heat the mold to a certain temperature and then add the preheated plastic material through the charging chamber. The plastic is heated to a given heating temperature, pressed, and cooled after a certain time of holding pressure, and finally, the product is obtained after demolding11,12,13,14,15,16,17.
The mean value of each parameter on the shrinkage rate can be obtained from Eq. (18), as shown in Table 8. The degree of influence of each parameter on the shrinkage rate is shown in Fig. 13.
Based on the theoretical equation of pressing pressure for thin sheet-type plastics, the theoretical derivation of pressing pressure suitable for cylindrical cavities was obtained, and the theoretical derivation of pressing pressure suitable for closed plastic impeller molding was obtained. By calculation, it is obtained that the pressing pressure of closed type plastic impeller is 15 MPa.
Fan, R. Research on large scale earthquake emergency material demand prediction based on PSO-BP neural network [D] In 2021 IEEE 3rd International Conference on Civil Aviation Safety and Information Technology (ICCASIT) (Beijing Jiaotong University, Haidian, 2020).
The main component of the plastic raw material used in the closed plastic impeller is UTR9000, whose melting point is generally about 170 °C and the decomposition temperature is about 260 °C. The closed plastic impeller molding mainly relies on the UTR9000 material becoming molten. The heating temperature is based on the UTR9000 molding temperature and ensures that the temperature is not too high to cause the decomposition of UTR9000.
Aimed at bringing to market a new biocomposite that offers a high level of stability in terms of both quality and supply, the tie-up will see the partners tap into their material supply chains and leverage the advanced material manufacturing and development technologies they have cultivated over many years.
Mitsui Chemicals aims to combine cellulose powder from Nippon Paper with the compounding technologies cultivated by the Mitsui Chemicals Group to develop a strong, readily workable biocomposite with a high cellulose powder content. Plans are to tap into the existing sales network for Mitsui Chemicals’ own compound resins and use this to offer samples to customers.
In order to obtain the degree of influence of the process parameter combination on the two evaluation indexes and the process parameter combination under the best situation of both evaluation indexes, polar difference analysis is required for each result of the closed plastic impeller compression molding orthogonal experiment. The larger the extreme difference, the greater the influence of the process value on warpage and shrinkage, and the smaller the extreme difference, the smaller the influence of the process parameter on warpage and shrinkage, and the extreme difference equation is shown in Eq. (18).
Chen Xiaoshan, S. U. & Ping, S. Application of genetic neural network in the evaluation of the effectiveness of equipment assurance command system [J]. Mil. Autom. 28(03), 15–18 (2009).
To study the trend of impeller evaluation index changing with process parameters, the minimum volume shrinkage and warpage under the condition of changing a single process parameter are predicted by using the prediction function of the established neural network based on the optimal process parameter combination, and the effects of heating temperature, heating time, pressing pressure and pressing time on the warpage deformation and shrinkage are obtained, as shown in Fig. 22 and Fig. 23.
By submitting a comment you agree to abide by our Terms and Community Guidelines. If you find something abusive or that does not comply with our terms or guidelines please flag it as inappropriate.
Kamran10 used hot compression molding to optimize PLA preparation and PLA samples to obtain PLA with the highest tensile strength, flexural strength, and hardness values. The role of different processing variables such as temperature, pressure, compression time, and holding and cooling time on PLA molding was investigated. These variables were investigated to optimize PLA properties and to produce composite samples using the optimized processing parameters.
The orthogonal test results of closed type plastic impeller compression molding were analyzed to obtain the influence trend of each process parameter on warpage deformation: compression molding pressure (C) > heating temperature (A) > pressing time (D) > heating time (B) and the optimal combination of warpage deformation compression molding process parameters A3B3C1D4. The influence trend of each process parameter on shrinkage rate: heating temperature (A) > pressing pressure (C) > pressing time (D) > heating time (B) and the combination of optimal compression molding process parameters for shrinkage A2B4C1D3.
Giboz, J., Copponnex, T. & Mélé, P. Microinjection molding of thermoplastic polymers: morphological comparison with conventional injection molding [J]. J. Micromech. Microeng. 19(2), 1–12 (2009).
Huang-Bin, Z., Zhou, Y.-H. & Zhu, L.-J. Implementation and comparison of improved BP neural networks based on MATLAB [J]. Comput. Technol. Autom. 1, 28–31 (2008).
The heating time is the time when the closed plastic impeller is heated to the time when it can be molded. The closed plastic impeller molding mainly heats the UTR9000 material into a molten state, and the heating time is based on the UTR9000 molding temperature. Through the numerical simulation and analysis of the transient thermal analysis module in the workbench, the change of the temperature of the plastic raw material in the closed plastic impeller mold with the heating time can be obtained. The appropriate heating time can ensure that the temperature of the plastic raw material in the mold reaches a more appropriate molding temperature.
Xiaobin, Y. Analysis of the current situation and development direction of domestic plastic centrifugal pumps [J]. Chem. Equip. technol. 36(06), 44–46 (2015).
Bo, C. Domestic and foreign composite material process equipment development review of the sixth—molding [J/OL]. Compos. Sci. Eng. 2, 1–28 (2022).
A GA-BP model for the prediction of the process parameters of closed plastic impeller compression molding was developed, which represents the corresponding relationships between all values between the minimum and maximum levels of the four process parameters and their resulting warpage deformation and shrinkage, and predicts the warpage deformation and shrinkage, respectively. The GA-BP model was verified to be correct by comparing the predicted values with the true values of the desired output 26,27,28. Then the data obtained from GA-BP were fitted using the global optimization-seeking function of the NSGA-II algorithm, which led to the optimal combination of process parameters for closed plastic impeller compression molding.
The purpose of the structural analysis is to obtain the two evaluation indexes of warpage deformation and shrinkage of the closed plastic impeller under a certain set of process parameters, and the simulation results of the structural analysis are shown in Fig. 10.The simulation analysis shows that the overall deformation distribution and the maximum deformation of the closed plastic impeller occur at the inlet of the front cover of the closed plastic impeller and at the blade connected to the inlet.
According to the transient thermal analysis \(\mathrm{q}=\frac{\mathrm{du}}{\mathrm{dt}}\) (indicating that the rate of heat conduction inflow or outflow \(\mathrm{q}\) is equal to the change of internal energy of the system), during the heating process of closed plastic impeller compression molding, the whole compression mold system is divided into micro elements, and the governing differential equation of heat conduction of closed plastic impeller compression mold can be obtained by Eq. (2):
M.F. had made substantial contributions to design, experimental research, data collection and result analysis; Z.Z. made critical changes to important academic content; Z.Z. made the final review and finalization of the articles to be published.
Jinping, Qu. Recent research advances in plastic processing and molding technology [J]. China Eng. Sci. 13(10), 58–68 (2011).
The mean value of each parameter on warpage deformation can be obtained from Eq. (18), as shown in Table 7. The degree of influence of each parameter on warpage deformation is shown in Fig. 11.
Equation (4) is the mathematical model of the heating process of a closed plastic impeller at a certain heating temperature. The heating process of plastic raw materials at a certain heating temperature is simulated by the transient thermal analysis module in a workbench19.
The selection operation uses roulette to simulate the survival of the fittest, and the better individuals are retained as much as possible. Variation and crossover are effective methods to avoid falling into local optimum, in which crossover is mainly used to improve population diversity and variation is used as a supplement. The crossover rate is chosen to be 0.7, and the variation rate is chosen to be 0.1, which can achieve a faster convergence speed and ensure global superiority seeking.
Xiaoqing, W. Innovative Design and Simulation Optimization Analysis of Small Savonius Fan [D] (Yantai University, Yantai, 2013).
Fu-Cheng, G. Optimization of Injection Molding Process Parameters for Automobile Front-end Wing [D] (Anhui University of Engineering, Huainan, 2019).
Stephen has been with PlasticsToday and its preceding publications Modern Plastics and Injection Molding since 1992, throughout this time based in the Asia Pacific region, including stints in Japan, Australia, and his current location Singapore. His current beat focuses on automotive. Stephen is an avid folding bicycle rider, often taking his bike on overseas business trips, and is a proud dachshund owner.
Japan is somewhat of a hotbed for development of biocomposites based on cellulose derivatives. Japanese auto parts maker Toyoda Gosei recently developed a cellulose nanofiber (CNF) reinforced polypropylene (PP) compound. Polyplastics, meanwhile, roped in regenerated cellulose in a long-fiber thermoplastic PP compound. Japanese pulp and paper companies have been working for some time on the development of cellulose fiber for composite applications.
The average quality of the results in the < Element Quality > module reached 0.84, which is within the range; the average value of the results in the < Jacobian Ratio > module reached 1.0029, which is within the range; the average value of the results in the < Skewness > module reached 0.21808, which is within the range. The analysis shows that the mesh quality meets the requirements, so the heating process of the plastic material in the mold can be simulated numerically.
In this paper, the inner diameter of the closed plastic impeller cavity is R = 100 mm, the relationship function between the radial pressure and axial pressure a, and the product of the contact friction coefficient n between the inner wall of the closed plastic impeller cavity and the plastic material aη = 0.1, the distance between the plastic material and the bottom of the convex mold of the closed plastic impeller Z = 150 mm, P0 = 27 MPa, substituting into Eq. (15), we can get the closed plastic impeller compression molding The pressure is 14.82 MPa, rounded to 15 MPa.
The warpage deformation and shrinkage of the closed plastic impeller for each combination of process parameters can be obtained by Eq. (16) and Eq. (17), as shown in Table 6.
Qingqing, X. Comprehensive Electromagnetic-thermal-mechanical Analysis of CFETR Helium-cooled Solid-state Cladding under Plasma Transient Accidents [D] (University of Science and Technology of China, Hefei, 2019).
The warping deformation and shrinkage are two evaluation indexes that are very important for the molding quality of the closed plastic impeller, so the weight of warping deformation and shrinkage is set to 0.5. After the NSGA-II algorithm is used to solve the problem, the output feasible solution set results are subjected to data processing and screening, and the best combination of process parameters is finally determined as [187, 785, 19, 85], that is, the heating temperature is 187 °C, the heating time is 785 s, the pressing pressure is 19 Mpa, and the pressing time is 85 s.By combining the molding process parameters for simulation, the warpage of the impeller is 0.0198, as shown in Fig. 26. The warpage is 0.0198 mm, and the wall thickness of the spot workpiece is 5.6 mm. The data is substituted into Equation (17) to obtain a volume shrinkage of 0.353%.
Wang, Z. D., Zeng, Y., Wang, J. L. & Hu, C. D. Intrusion detection based on improved aspen swarm algorithm optimization of BP neural network [J]. Sci. Technol. Eng. 20(32), 13249–13257 (2020).
In the case of neglecting the blade parting, the cavity of the mold can be approximated as a cylinder. The inner diameter of the cavity is R, and the mold direction is Z. The uniform pressure in this direction is set to Pz, the radial uniform pressure is set to Pr, and a plastic material microelement dz in the closed plastic impeller cavity is taken for analysis. The pressure distribution has a pressure gradient, as in Fig. 2.
Hongyang, W., Jinzhu, Li. & Liming, L. process optimization and weld forming control based on GA-BP algorithm for riveting-welding hybrid bonding between magnesium and CFRP [J]. J. Manuf. Process. 70, 97–107 (2021).
Bo, C., Dianrong, G., Yang Chao, Gu. & Shaofeng, Z. G. Multi-objective intelligent collaborative optimization of structural parameters for high-powered long-range fog shooters [J]. J. Mech. Eng. 53(06), 166–175 (2017).
The mold material was selected as 45 gauge steel, and the plastic material was selected as UTR9000. In the heating stage, the heat of UTR9000 mainly comes from the high-temperature nitrogen in the molding furnace, thus defining the thermal boundary conditions. Set the < initial temperature value > to 80 °C. Set the step end time > to 1000 s and the < time step > to 100 s. The other settings remain unchanged, as shown in Fig. 7. The set temperature is 80 °C at 0 s, 170 °C at 1 s, and 170 °C at 1000 s; that is, the initial temperature of the mold and material is 80 °C, and the molding temperature in the furnace is 170 °C. Due to the high thermal conductivity and strong heat absorption capacity of the metal mold, it can rise to 170 °C in a relatively short time. During the heating process, put the impeller and the mold into the heating workstation for heating. The electric heating plate directly heats the upper and lower molds, so the heating boundary is the whole mold surface. After the temperature is set, it is shown in Fig. 8.
Chen, Z. & Turng, L.-S. A review of current developments in process and quality control for injection molding [J]. Adv. Polym. Technol. 24(3), 165–182 (2005).
The heating plate is used to heat the convex die of the closed plastic impeller pressing mold, and the heating ring is used to heat the concave die of the closed plastic impeller pressing mold so that the closed plastic impeller mold and the plastic material can reach the necessary pressing and molding temperature18. The proper temperature not only heats the plastic material faster with quality assurance, but also reduces the pressing time of the closed plastic impeller, making the production process compact and efficient.
Lianji, Z. Design and experimental study of plastic chemical centrifugal pump [J]. Rubber Plast. Technol. Equip. 42(12), 89–90 (2016).
According to the main parameters of the plastic centrifugal pump, the structural parameters of the closed plastic impeller are calculated and designed. The structural parameter design of the closed plastic impeller is the most fundamental and important part of the process of its molding die technology research and parameter optimization. The structural parameters are calculated by the formula, and the calculated parameters are shown in Table 2.
where, \(l_{1}\)—The coordinate value of maximum value point after molding, \(l_{2}\)—The coordinate value of maximum value point in an ideal state.
where, \({V}_{x},{V}_{y},{V}_{z}\)—Media conductivity; \(\frac{\partial T}{\partial x}, \frac{\partial T}{\partial y}, \frac{\partial T}{\partial z}\)—Temperature gradients along directions \(\mathrm{x},\mathrm{y},\mathrm{z}\) respectively.
The orthogonal experiment takes four levels for each of the four process parameters, and there is a large interval between each two levels. The sixteen data sets from the experiment cannot include all the values between the minimum and maximum levels of each process parameter. Therefore, the optimal combination of process parameters obtained from the orthogonal experiments is relatively rough, and the number between the maximum and minimum values of each level that has not been taken may be the best process parameter required. To obtain the optimal combination of process parameters, the GA-BP and NSGA-II algorithms were used to train the sixteen sets of orthogonal experimental data obtained25.
Japan’s Nippon Paper Industries and Mitsui Chemicals are set to partner in the development of a new biocomposite with a high cellulose powder content. The two companies intend to develop products and bring them to market at the earliest possible opportunity, with plans to expand into a range of fields, including consumer products, housewares, containers, building materials, household appliances, and automobile parts.
Substituting Eq. (14) into Eq. (13), the equation for calculating the pressure of closed plastic impeller molding can be obtained, as shown in Eq. (15):
The material used for the closed plastic impeller in this paper is URT9000 resin, which is a modified ABS-like resin with excellent durability, excellent chemical stability, and excellent mechanical properties. It is widely used in machinery, automobile, electrical appliances, and other fields22. Table 5 shows the performance parameters of URT9000 ABS resin.
Xing, Xu., Guangzhong, S. & Kunyun, T. Application of GA-BP neural network in discriminating water sources of sudden water in coal mines [J]. Coal Technol. 37(10), 172–174 (2018).
The data predicted by the GA-BP neural network were functionally fitted by the polyfit function in MATLAB, and the NSGA-II algorithm was used for multi-objective optimization34. With a population size of 50, 200 iterations, a crossover probability of 0.85, and a variance probability of 0.1, the expectation values under a certain process parameter were solved separately to obtain better warpage deformation and shrinkage, as shown in Fig. 25.
Nippon Paper and Mitsui Chemicals partner to produce biocomposite material for auto, home appliance, and other applications.
Using the genetic algorithm to optimize the weights and thresholds of the BP neural network can prevent the BP neural network from falling into local optimum and can significantly accelerate its convergence speed. Choosing the appropriate population size can make the computation speed not too slow, and the computation error can be more reasonable. In general, the population size is between 10 and 200, and the population size in this paper is 50, according to the actual choice.
Goharpey, F. et al. Determination of twin-screw extruder operational conditions for the preparation of thermoplastic vulcanizates on the basis of batch-mixer results [J]. J. Appl. Polym. Sci. 107(6), 3840–3847 (2008).
The mean squared error (E) is used in the BP neural network algorithm to represent the recognition accuracy, and it is concluded that the smaller the value of the mean squared error, the higher the accuracy, as shown in Eq. (21).
As can be seen from Fig. 23, the neural network analysis of the critical parameters of the molding process on the impact of shrinkage rate, it is concluded that: with the increase of heating temperature, shrinkage first becomes smaller and then becomes larger; the optimal value between 180 °C and 190 °C; with the increase of heating time, shrinkage first becomes larger and then becomes smaller, but the heating time is not too long, the optimal value between 750 and 800 s; with the increase of pressing forming pressure, shrinkage first becomes larger and then becomes smaller and larger, the optimal value between 20 and 25 Mpa; with the increase of pressing time, warpage deformation first becomes larger and then becomes smaller and stabilizes, the optimal value between 80 and 90 s.
Based on the principle of orthogonal test, orthogonal test table \({L}_{16}\left({4}^{5}\right)\) is established, as shown in Table 4.
The NSGA-II algorithm has good convergence in dealing with multi-objective optimization aspects of the problem31,32. In this paper, the NSGA-II algorithm is applied to derive the optimal combination of process parameters for closed plastic impeller compression molding with warpage deformation and shrinkage as the objectives. The NSGA-II algorithm in dealing with the multi-objective optimization process33, as shown in Fig. 24.
Qiuyun, C. Exploring the research progress of fiber-reinforced resin matrix composite manufacturing technology [J]. Sci. Technol. Wind 19, 183–184 (2021).
where, \(\overline{q }\)—Heat generation per unit volume, \(\mathrm{J}/{\mathrm{m}}^{3}\); \({h}_{f}\)—Convective heat transfer coefficient; \({T}_{B}\)—Temperature of fluid, ℃; \(\mathrm{\delta T}\)—Virtual variable of temperature, ℃; \({S}_{2}\)—Area of applied heat flux, \({m}^{2}\); \({S}_{3}\)—Convection applied area, \({m}^{2}\).
The linear distance between the mold corresponding to the point position of the maximum value and the mold corresponding to the other side with the same warping deformation gradient direction is a. The Shrinkage equation of the closed plastic impeller is shown in Eq. (17).
Some scholars only numerically simulate the molding process alone, and there are few in-depth studies on the molding process parameters of plastic materials; some scholars only experimentally study the effects of different molding processes on the molding quality and cannot comprehensively and completely numerically simulate the molding process and optimize the molding process parameters. In this paper, theoretical calculations and the design of a closed plastic impeller are carried out to obtain a closed-type plastic impeller with better molding quality. The orthogonal experiments on the process parameters and the numerical simulation of the heating process and compression molding process using the ANSYS function are carried out to obtain a set of process parameters with better warpage deformation and shrinkage.
Chongzhou, W. Principles and Applications of Plastics Processing [M] (Chemical Industry Publishing House, Beijing, 2008).
Barrera, M. A., Vega, J. F. & Martínez Salazar, J. Three-dimensional modelling of flow curves in co-rotating twin-screw extruder elements [J]. J. Mater. Process. Tech. 197(1), 221–224 (2007).
Yu, S. H., He, X. M. & Zhang, G. Y. Processing optimization of injection molding based on response surface model and NSGA-II algorithm [J]. Suxing Gongcheng Xuebao J. Plast. Eng. 21(3), 15–19 (2014).
Jing, Z. & Nailfan, Z. Finite element analysis of glass moulding based on ANSYS [J]. Mod. Manuf. Technol. Equip. 10, 106–108 (2016).
Aiming at the warping deformation and volume shrinkage of the closed plastic impeller, the relevant compression molding process parameters were optimized.Based on the theoretical equation of the pressing pressure for general sheet plastics, the theoretical derivation of the pressing pressure suitable for cylindrical cavities was carried out, and the theoretical derivation of the pressing pressure suitable for closed plastic impeller molding was derived, and the pressing pressure was calculated to be 15 MPa. The warpage deformation and shrinkage rates under different combinations of process parameters were obtained, and the influence of process parameters on warpage deformation and shrinkage rates, as well as the two combinations of process parameters that satisfy the best warpage deformation and shrinkage rates, respectively, were obtained by extreme difference analysis. A GA-BP neural network model was established for the prediction of the process parameters of closed plastic impeller compression molding, and the prediction curves were fitted into a function to obtain a set of process parameter combinations with optimal warpage and shrinkage at the same time by using the multi-objective optimization function of NSGA-II algorithm.
This paper belongs to "Major Natural Science Foundation of Anhui Province Universities Project (KJ2021ZD0144)". This paper belongs to the "Major Natural Science Foundation of Anhui Province Project (KJ2021A1201)". This article belongs to "Anhui Province First-class Undergraduate Major Construction Project (2020ylzyjsd02)".
where, m—the number of design warp elements inside the implicit layer; n— the number of neurons in the input layer; t— the number of warp elements inside the output layer God; a— a constant from 1 to 10.
The pressing pressure is the force exerted on the plastic raw material after the upper and lower mold of the closed plastic impeller is closed20. The heating temperature of compression molding can be reduced by appropriately increasing the compression molding pressure, so that the product density is appropriate, the dimensional accuracy and the surface contour are clear, but the compression molding pressure should not be too large, otherwise the service life of the closed plastic impeller mold will be reduced and the residual stress in the closed plastic impeller molding parts will be increased.
Open Access This article is licensed under a Creative Commons Attribution 4.0 International License, which permits use, sharing, adaptation, distribution and reproduction in any medium or format, as long as you give appropriate credit to the original author(s) and the source, provide a link to the Creative Commons licence, and indicate if changes were made. The images or other third party material in this article are included in the article's Creative Commons licence, unless indicated otherwise in a credit line to the material. If material is not included in the article's Creative Commons licence and your intended use is not permitted by statutory regulation or exceeds the permitted use, you will need to obtain permission directly from the copyright holder. To view a copy of this licence, visit http://creativecommons.org/licenses/by/4.0/.
The numerical simulation of the whole molding process of the closed-type plastic impeller was carried out with a certain set of process parameters as an example. According to the simulation results obtained, the warpage deformation and shrinkage rate are selected as the evaluation indexes of closed type plastic impeller molding, and the numerical simulation of the molding process is carried out for 16 sets of process parameter combinations of plastic raw materials of closed type plastic impeller, respectively.
where, \(\overline{q }\)—Heat generation per unit volume, \(\mathrm{J}/{\mathrm{m}}^{2}\); \(\uprho \)—Material density,\(\mathrm{kg}/{\mathrm{m}}^{3}\); \(\mathrm{c}\)—Specific heat capacity of material, \( {\text{J}}/{\text{kg}}, \)°C; \(\frac{dT}{dt}\)—Heat changes with time.
The transient thermal analysis was performed to obtain the molding temperature that the plastic raw material reaches by heating for a certain time at a certain heating temperature24. The specific value of the heating time is obtained by simulation and the temperature field data of the thermal coupling are obtained, and the simulation results are shown in Fig. 9. Through the simulation analysis, the plastic raw material shows a gradual change in temperature during the heating process, and the set molding temperature of 170 °C can be reached. The transient thermal analysis can effectively avoid the problem of edge rupture caused by molding the plastic raw materials before they all reach the pressing temperature, and there is no need to determine the time parameters of the heating stage.
where, \({\mathrm{P}}_{\mathrm{Z}}\)—Uniform pressure above micro \({\mathrm{d}}_{\mathrm{Z}}\), \(\mathrm{MPa}\); \(\left({\mathrm{P}}_{\mathrm{Z}}+{\mathrm{dP}}_{\mathrm{Z}}\right)\)—Uniform pressure under micro \({\mathrm{d}}_{\mathrm{Z}}\), \(\mathrm{MPa}\); \(\mathrm{A}\)—Bottom area of closed plastic impeller cavity cylinder, \({\mathrm{mm}}^{2}\); \(\uptau \)—Shear force of the cavity of the closed plastic impeller with plastic raw materials in Z direction, N; \(\mathrm{R}\)—Inner diameter of closed plastic impeller cavity, \(\mathrm{mm}\); Z—Distance between micro element \({\mathrm{d}}_{\mathrm{Z}}\) and the bottom of closed plastic impeller punch, \(\mathrm{mm}\).
Wang, X. Y., Yu, Y. L. & Lv, L. H. The discussion of manufacturing peanut hull and TPU composites by hot pressing [J]. Adv. Mater. Res. 1793, 3527–3530 (2012).
The pressing time was set to 60 s, and the pressing pressure was set to 15 MPa. During the molding process, as the inner surface of the product is close to the surface of the mold, the normal displacement of the entire inner surface of the product is considered to be constrained, and the molding pressure is applied to the outer surface of the convex mold. The transient thermal analysis simulation was carried out to obtain the thermodynamic coupled temperature field data loading.
The heating temperature, heating time, compression molding pressure, and compression time were determined as a set of process parameters affecting the molding of the closed plastic impeller, and the warpage deformation and shrinkage rate were used as indicators to evaluate the goodness of the product. The orthogonal experiment table was designed, and the orthogonal test results of closed type plastic impeller compression molding were obtained by numerical simulation of the heating process and compression molding process of plastic raw materials through ANSYS.
Table 5 and Fig. 13 show that the influence of the moulding process parameters on the shrinkage rate is the heating temperature (A) > pressing pressure (C) > pressing time (D) > heating time (B), with the heating temperature having the greatest influence on the shrinkage rate of the closed type plastic impeller. The optimum combination of molding process parameters was A2B4C1D3, i.e., a heating temperature value of 180 °C, a heating time value of 800 s, a compression molding pressure value of 15 MPa, and a compression time value of 80 s. The process parameters were simulated by ANSYS software, and the warpage amount obtained is shown in Fig. 14. The warpage amount of 0.0278 mm and the corresponding wall thickness of 7 mm were substituted into Eq. (17) to obtain the minimum volume shrinkage of 0.398%.
GETTING A QUOTE WITH LK-MOULD IS FREE AND SIMPLE.
FIND MORE OF OUR SERVICES:
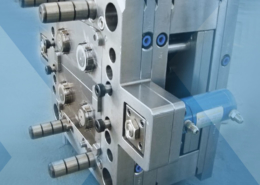
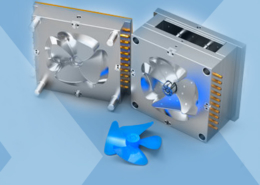
Plastic Molding

Rapid Prototyping
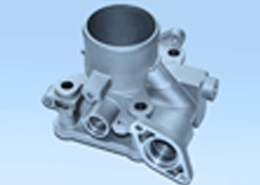
Pressure Die Casting
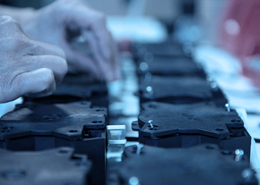
Parts Assembly
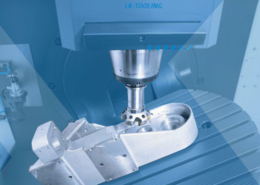