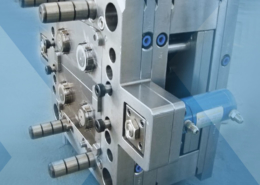
Chemical profile: Middle East polyethylene - polyethylene moulding
Author:gly Date: 2024-09-30
Sanichi has been loss-making for its prior three financial years. More recently, the group returned to the black with a RM470,000 net profit for the third quarter ended Sept 30, 2023 (3QFY2023) versus a net loss of RM12.24 million a year earlier, despite revenue slipping 20.8% to RM3.42 million from RM4.32 million in 3QFY2022.
KUALA LUMPUR (Feb 6): After more than five years in talks, precision plastic mould maker Sanichi Technology Bhd has aborted plans with Singapore-based FKS Holdings Pte Ltd to provide fresh produce such as seafood, wagyu beef, fruits and vegetables to international food and beverage (F&B) industry players. It did not reveal the reason.
Engaging with a partner that knows the inside and out of process temperature control can help in every step of the away from surveying the sites to understanding where efficiencies can be made – recommending bespoke, fully packaged, process-designed chillers and TCUs based on tried and tested processes.
Until recently, all the manufacturers could do with a standard TCU was setting a temperature range, flow rate and test it until the desired quality was achieved. The latest developments in the TCU’s designs, have brought precision temperature control to a new level, a level that allows the manufacturer not only to achieve the precise temperature, but is also reducing the power consumption of the system.
With these new pumps, operators gain control over temperature differentials (ΔT) across the mould. Once the desired temperature is achieved, operators can configure the desired ΔT and this will adjust pump speed accordingly. This dynamic adjustment isn't just a solution to demand for heightened precision in plastic moulding, it's a game-changer that reduces power consumption by between 50 and 90% at the pump level, depending on the application. Moreover, it reduces cycle times, a critical gain for industries seeking to ramp up production speed.
In December 2018, Sanichi and FKS had inked the MOU with the intent of forming a joint venture (JV) to supply fresh produce for the international F&B industry, as well as provide Japanese fine dining cuisine for regional markets, namely Singapore, Malaysia, Indonesia, China and Australia.
To provide accurate and reliable process temperatures for equipment that is designed to operate at high temperatures creates a real challenge. It’s not only because of the extremely high operating temperatures required, but also because each composite and product being manufactured on the machine requires a very precise temperature level.
In a bourse filing on Tuesday, ACE Market-listed Sanichi said the two companies had mutually agreed to terminate the memorandum of understanding (MOU) signed in December 2018. Both companies also agreed that each party will not make any claim against the other party due to the termination.
Temperature control technology plays a pivotal role in plastic injection moulding processes, ensuring consistent product quality and production efficiency. Temperature control and stability have also a direct effect on cycle times and output. Manufacturers’ economic success depends to a high degree on the development of reliable production, and the ability to efficiently control and maintain the right process temperatures within the various stages of the process is critical to achieve this.
To illustrate the impact, consider a manufacturing line currently producing a mould every 10 seconds. If the goal is to accelerate this pace to one mould every eight seconds for increased output, enhanced cooling is essential to expedite the solidification process. With speed control pumps on the TCUs, operators can fine-tune the desired ΔT and cooling levels, achieving precise control over the cooling process.
There is just a handful of expert companies that would look at the manufacturer’s critical processes, and deliver a detailed, documented plan to keep his operations running. If it came to the worst and a chiller broke down, that partner should be able to say exactly what, when and where it happened and provide a solution to keep the plant up and running in matter of hours. Either by fixing the issue or providing a contingency solution to fill the gap. This is the part of the production that directly influences whether a plant can maintain the quality, keep their production running and keep their end customers satisfied.
In the continuously changing environment, the manufacturers face many challenges embracing and understanding the new technology, wanting to provide customers with the best quality products while also reducing their operating costs. The fact that around 60% of a plants’ total lifecycle cost can be attributed to process cooling and refrigeration systems, makes it a vital investment that shouldn’t be overlooked.
Traditionally, a Temperature Control Unit (TCU) has three main functions – to heat, to cool and to control. It works alongside a process-grade chiller to provide enhanced cooling power, and at elevated temperatures provide accurate temperature control with minimum temperature deviation. It does so by regulating the heating elements contained within the TCU, teamed with the cooling capacity provided by the chiller.
Dave Palmer, general manager for UK at ICS Cool Energy shares how to optimise plastic moulding with the latest temperature control technologies.
When the group announced the MOU, it noted that the JV was expected to set up 25 Japanese fine dining outlets over three years and collaborate with suppliers in Japan for fresh produce to be supplied to international F&B players.
However, the return to quarterly profit was insufficient to offset the group’s losses recorded in preceding quarters, leading to a cumulative net loss of RM13.08 million for the nine months ended Sept 30, 2023 (9MFY2023).
A comparison between a system equipped with centrifugal pumps and utilising ΔT control, and a device featuring unregulated peripheral impeller pumps speaks volumes. In a three-shift operation, the contrast in annual electricity consumption is 14.495 kWh versus a mere 1.160 kWh with the new systems. For manufacturers operating multiple moulding machines with TCUs, the cumulative energy savings can be significant, contributing to both cost reduction and environmental sustainability.
The group has since changed its financial year end from Dec 31 to March 31, citing “to have a better planning of its financial resources”.
Across the industries and applications like medical manufacturing where precision, product consistency and process repeatability are especially vital, there is a growing demand for higher energy-efficiency and reducing cycle times.
GETTING A QUOTE WITH LK-MOULD IS FREE AND SIMPLE.
FIND MORE OF OUR SERVICES:
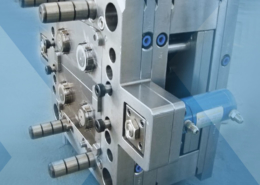
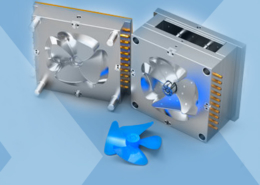
Plastic Molding

Rapid Prototyping
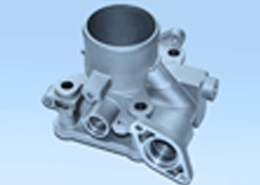
Pressure Die Casting
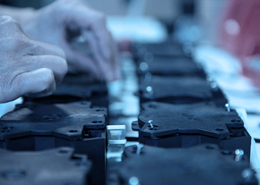
Parts Assembly
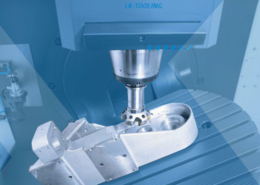