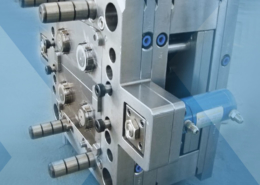
BEVERAGE CARTON RECYCLING: Palurec plant for recycling plastic-aluminium
Author:gly Date: 2024-09-30
iQ process observer, which monitors the entire process. This AI platform analyzes hundreds of parameters simultaneously, displaying deviations and corrective measures.
iQ weight control, which detects fluctuations in the injection volume and material viscosity and automatically compensates for them within validated limits in the same cycle.
Engel said it is increasingly receiving requests for custom solutions in the extremely high clamping force range. Clamping forces of 10,000 tons and more are possible. Machines of this size can process individual shot weights of several hundred kilograms or pounds and achieve two-ton-per-hour material throughput.
The Engel e-motion 160 combi M will make its debut at the K show in Düsseldorf, Germany, in October. Featuring just 160 tons of clamping force and a horizontal indexing table, the combi M boasts two injection units — one fitted on the stationary platen, the second on the moving platen. Two molds can operate in parallel thanks to the indexing table dividing the mold closing area in the center.
Geoff Giordano is a tech journalist with more than 30 years’ experience in all facets of publishing. He has reported extensively on the gamut of plastics manufacturing technologies and issues, including 3D printing materials and methods; injection, blow, micro and rotomolding; additives, colorants and nanomodifiers; blown and cast films; packaging; thermoforming; tooling; ancillary equipment; and the circular economy. Contact him at [email protected].
Getting the 8,000-ton machines from Austria to the Infiltrator Water Technologies plant in Kentucky was a logistical challenge.
At the IWT site in Winchester, new manufacturing facilities had to be built to house the large machines. As 29 truckloads of machine parts were arriving from Austria, the 59,000-square-foot building expansion went forward. A 150-ton overhead crane was installed to move molds in and out of the machine and was also used to help assemble the new press.
The process will be assisted by a pair of robots — an Engel viper 20 will remove the two-component parts and place them in trays, and an e pic robot will stack the trays in boxes, then discharge them via an integrated tray server.
Engel was recently awarded a gold sustainability rating by EcoVadis, which relies on data from more than 90,000 evaluated companies and global supply chains to rank companies.
The Engel e-motion 160 combi M will be molding medical diagnostic components under cleanroom conditions at the event in October.
The duo injection molding machines each have two 85,000 cm³ injection units, which allow for injecting a total shot weight of 270 lb (122 kg). Despite the clamping force and shot size, the machines have a relatively small footprint — 96 ft. (29.3 meters) long and 37 ft. (6.4 meters) wide — enabled by Engel’s two-platen design.
The combi M takes up approximately 20% less space because of its horizontal indexing table. A comparable 32-cavity mold with a vertical rotary table would require a machine with at least 280 tons of clamping force, the company noted.
“We have made significant investments in new equipment, and this will allow us to produce our products more effectively and efficiently,” said Bryan Coppes, vice president of engineering and R&D at Infiltrator. “It is the new capabilities and opportunities for continued product development that are truly exciting. This new equipment will allow us to continue to bring new and innovative products to market and meet and exceed our customers' needs.”
Engel added in the news release that it shares a commitment to sustainability with ADS, which claims to recycle more plastic than any other company in North America.
iQ flow control, which ensures constant temperature control ratios by controlling temperature differences in the individual cooling circuits based on a set value.
Special shipping and ground transportation arrangements were needed to move the machine from Austria to the United States and even within Austria. The platens were transported to and from the St. Valentin manufacturing facility along the Danube River on barges. “Each machine was fully assembled and tested prior to shipping and then disassembled to be shipped to the United States,” said Jim Moran, business development manager at Engel North America.
Two injection molding machines with a clamping force of 8,000 tons each have now been delivered by Austrian injection molding machine maker Engel to the Infiltrator Water Technologies (IWT) plant in Winchester, KY. IWT took delivery of the first Engel duo 130000/130000H/8200 combi US machine, the largest machine ever built at Engel’s St. Valentin facility in Austria, in February of last year. A second machine, a replica of the first, arrived at the facility this month. IWT, a subsidiary of Advanced Drainage Systems (ADS), produces water management products.
A new all-electric injection molding machine and accompanying AI-driven work cell from Engel reduces footprint on the production floor as well as energy consumption, while also doubling output.
Engel said it received the purchase order in November 2020 and completed handover of the first machine in February 2022. The second machine, a replica of the first, was delivered this month.
One ideal application for the combi M is the molding of sample vessels for medical diagnostics under cleanroom conditions. These two-component parts will be demonstrated during the K at stand C58 in hall 15. First, primary parts with cylindrical cavities are injected using black-dyed polycarbonate. The cylinders are then sealed with transparent polycarbonate in a second molding step enabled by the indexing table rotating 180 degrees.
GETTING A QUOTE WITH LK-MOULD IS FREE AND SIMPLE.
FIND MORE OF OUR SERVICES:
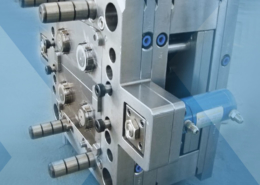
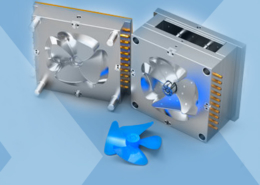
Plastic Molding

Rapid Prototyping
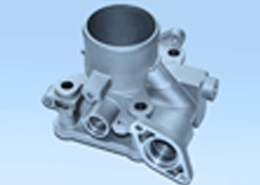
Pressure Die Casting
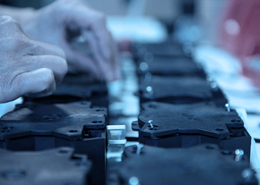
Parts Assembly
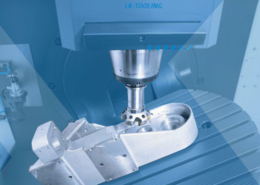