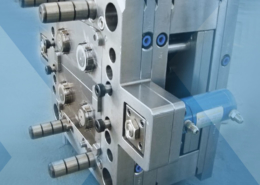
Better, More Flexible Eyeglasses Through Materials Science and Digital
Author:gly Date: 2024-09-30
Luke Smoothy, founder and director, Get It Made, delves into why injection moulding still holds the sceptre in the medical industry and highlights the key benefits it brings.
Strategic Moves and Urbanization Uplift Market Horizons In addition to advancements within the industry itself, an array of external factors has been identified as influencing market growth. Urbanization and industrial development, especially in burgeoning economies, have elevated the market’s prospects. Furthermore, strategic alliances and an augmented focus - and concurrent investment - in research and development to further innovate within the MIM sphere are bolstering the market landscape. These factors collectively contribute to a dynamic market environment poised for continued evolution. Market Segmentation Highlights and Regional Outlook The market report segments the global metal injection molding market based on material, end-use industry, and region. A comprehensive analysis shows significant demand across varied segments, including stainless steel and low alloy steel, each catering to diverse industries from automotive and electronics to medical and defense sectors. Regional analysis notes a robust market presence in North America and the Asia-Pacific region, with countries like the United States, China, and India at the forefront of market consumption and innovation. The Competitive Landscape The market’s competitive environment is dynamic, with key players focusing on technological advancements and capacity expansions to meet the rising demand for MIM products. The comprehensive competitive landscape includes prominent industry participants, reinforcing the market's vigorous nature and the relentless pursuit of excellence and innovation among competitors.
About ResearchAndMarkets.comResearchAndMarkets.com is the world's leading source for international market research reports and market data. We provide you with the latest data on international and regional markets, key industries, the top companies, new products and the latest trends.
Thin wall moulding: A specialised form of conventional injection moulding that focuses on the mass production of ultra-thin (less than 1mm) and light plastic parts to make material cost savings. This is used to create portable medical devices enabling clinicians and patients to transport and operate them more easily - such as wearable devices, micro surgical tools, and invasive equipment like catheter ablation tools and endoscopes.
Well-suited for products with straightforward shapes, injection moulding delivers unrivalled precision and finish quality. For medical applications such as moving machine parts or implantable devices, the procedure gives a vital smoother finish.
Since the need for devices and components in the medical sector is always increasing, injection moulding stands out for its effectiveness and capacity to handle large-scale orders. The method is best suited for high-volume production, making it the preferred method for mass-producing medical components. That said, even though 3D printing is hailed for having cheaper initial costs in small-scale production, its cost advantage diminishes as production volume rises.
The indelible imprint of injection moulding in medical manufacturing underscores its pivotal role in delivering efficient, high-quality, and cost-effective solutions to the industry. As the medical field continues to evolve, the synergy between injection moulding and emerging technologies like 3D printing is poised to drive innovation further, ensuring the continual enhancement of patient care and medical advancements.
In the realm of medical device manufacturing, the tussle between traditional injection moulding and modern 3D printing technologies continues. However, injection moulding has held its ground firmly, especially when high-volume production, cost-effectiveness, and precision are all paramount.
An expansive range of materials are available with injection moulding, making it easier to produce medical equipment that adheres to the strict biosafety and chemical stability criteria of the medical sector. Techniques such as thin wall moulding and gas-assisted injection moulding enable the production of both practical and aesthetically appealing parts.
Dublin, May 09, 2024 (GLOBE NEWSWIRE) -- The "Metal Injection Molding Market Report by Material Type, End Use Industry, and Region 2024-2032" report has been added to ResearchAndMarkets.com's offering.The global metal injection molding industry is experiencing significant growth, with expectations to almost double from a value of US$ 4.2 billion in 2023 to US$ 9.1 billion by 2032. This growth is anticipated to occur at a compound annual growth rate (CAGR) of 9% over the forecast period from 2023 to 2032. The expansion has been largely attributed to the method's precision and cost-efficiency, which cater to the demanding automotive sector and the increasing need for lightweight and high integrity components. The metal injection molding (MIM) market has seen a surge, driven by factors such as the transition of manufacturers from traditional fabrication methods to MIM, due to its various operational benefits. MIM enables the production of components that exhibit excellent corrosion resistance, thermal and dimensional stability, and high mechanical strength. This scalability promotes a wide array of industrial applications, including an influencing presence in the medical field for the creation of intricate surgical tools.
Perhaps intriguingly is the fact that 3D printing and injection moulding are not exclusive of one another. Injection moulding is frequently preceded by 3D printing, which assists with prototyping and even helps create moulds for the injection moulding process.
Gas-assisted injection moulding: In certain medical device applications, gas-assist moulding can provide solutions that conventional injection moulding can’t. The process consists of injecting a pressurised gas into the mould cavity after the initial plastic injection, expelling the molten plastic and forming hollow areas within the final product. It is suited to the manufacturing of complex parts without visual blemishes, for instance, tube- or rod-shaped parts which typically include handles and foot pedals, as well as large, cover-shaped structural parts e.g. side panels and covers for medical devices.
Liquid silicone injection moulding: This produces pliable, durable parts in high volume, and is used in fabricating tubes and respiratory masks requiring high levels of hygiene and chemical resistance.
GETTING A QUOTE WITH LK-MOULD IS FREE AND SIMPLE.
FIND MORE OF OUR SERVICES:
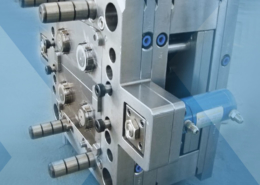
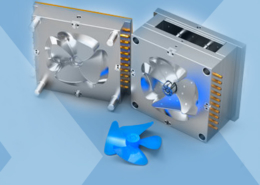
Plastic Molding

Rapid Prototyping
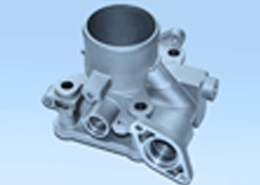
Pressure Die Casting
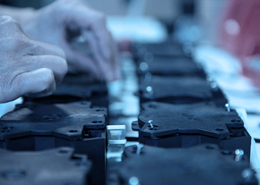
Parts Assembly
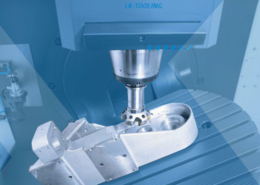