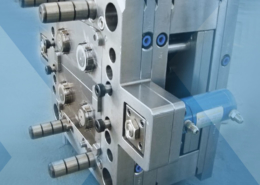
BASF customers showcase prototypes made from chemically recycled material - prot
Author:gly Date: 2024-09-30
Tritone’s MoldJet is unique as an Additive Manufacturing process – not Binder Jetting, Material Extrusion, nor Material Jetting, the MoldJet pr...»
Research at the Department of Mechanical Systems Engineering, Tokyo Metropolitan University, Japan, has been focused on Ceramic Injection Moulding to produce alumina artificial bone material and, in particular, the research has investigated the effects of CIM conditions, such as alumina powder loading and binder composition and content in the CIM feedstock, in order to control the porosity, grain size and mechanical properties of the sintered CIM alumina material. A paper by T Osada, Y Nagai, and S Kobayashi, recently published in Open Ceramics (Vol. 13, 2023, 100328, 7pp) entitled: ‘Fabrication and mechanical characterization of biocompatible oxide ceramic parts by injection molding’, outlined the results of their research. The authors stated that it is possible to control the density of CIM alumina parts by controlling the binder components and amount of binder added, or adjusting the powder loading. Even if the obtained bending strength of the CIM alumina parts decreased slightly with increasing porosity, they stated it was still found to be sufficient for use as artificial bone material.
Don't miss any new issue of PIM International, and stay up to date with the latest industry news. Sign up to our fortnightly newsletter.
Reach a truly international audience that includes component manufacturers, end-users, industry suppliers, analysts, researchers and more.
The expansion of MIM materials expands the application range of products, from traditional materials as iron-nickel alloys (Fe-2, 4, 8Ni to 50Ni), 304/316, 304L/316L, 420J2/440C stainless steels, W- Ni-Cu, expanded to 201, 430, 17-4PH and PANACEA® stainless steels, Fe-50Co (HiperCo®), Fe-3Si, W-Ni-Fe, etc.
Type 420 martensitic stainless steel covers a wide carbon range of 0.15% to 0.45%. Demand for this material from the 3C, automotive, biomedical and...»
Reach a truly international audience that includes component manufacturers, end-users, industry suppliers, analysts, researchers and more.
The free-to-access PIM International magazine archive offers unparalleled insight into the world of MIM, CIM and sinter-based AM from a commercial and technological perspective through:
A deeper exploration of what MIM can offer to customers has begun, with success for hinges of 3C devices (Fig. 3), sewing machine components, fasteners and tags for luxury bags and goods, kitchen knives, nail clippers, jigs and tools, and golf club heads. MIM has even begun to be put into some internal components of electric vehicles – for example in transmissions and the lithium battery pack, thus changing the nature of MIM components from something with a low cost and necessarily short lifespan, such as fashion, where the lifecycle of a garment isn’t equal to the lifecycle of its parts, to something intended to last as long as possible.
In addition, the promotion of titanium and titanium alloys in the past three years has also achieved positive results in domestic production, spurring on the creation of titanium and titanium alloy feedstocks and accelerating the MIM process for these materials.
The alumina powder and binders were mixed in a kneader for 1 h at 180°C with powder loading of 47, 50, and 52 vol.%. Viscosity measurements were performed on the feedstock compounds obtained to investigate their rheological behaviour. The authors stated that it was possible to select the powder loading and binder composition according to the viscosity of the sample. In particular, PP has higher strength and lower viscosity than LDPE and HDPE, which they suggest gives it advantages when used to produce artificial bone material from alumina.
However, after almost five years of observation, I found that at the start of the COVID-19 epidemic at the end of 2019, orders for MIM parts for smartphones manufactured in China declined significantly. Then, in early 2023, I learned that the rear camera frame of Apple’s iPhone 15 may have eliminated the use of MIM, which undoubtedly will be a major concern amongst China’s MIM producers. So, after the huge successes of the past decade, how should MIM companies progress into their post-smartphone era?
This year marks the year after MIM’s fiftieth anniversary. In 1972, the technology’s developer, Parmatech, could not have imagined the breadth of MIM’s future adoption, nor that manufacturers in the Greater China region would so fully embrace the process. We are very grateful to those pioneers for bringing this new technology to the world and we now strive to make the MIM process the norm in metal processing, along with casting, forging, machining, and press and sinter Powder Metallurgy.
Bioceramics is a class of materials that have found use as artificial bone materials for repairing or replacing damaged bone tissue because of their excellent biocompatibility and mechanical properties. Bioceramics can also directly interact with the surrounding tissue, either supporting tissue growth or inducing new tissue regeneration. In many biomedical applications, bioceramics such as alumina must often be fabricated to a specific and often complex shape such as artificial hip joints, artificial knee joints, bone screws, maxillofacial reconstruction, dental implants, etc. Alumina oxide is a bioinert material with excellent biocompatibility and mechanical properties, but its high hardness and brittleness make it difficult and costly to machine to the highly complex and precision shapes often required in artificial bone replacements.
MIM’s fruitful results in Greater China are due to the concerted efforts of the global MIM industry and the large number of orders from customers. At this time, even if the MIM industry is affected by uncertainties in the post-smartphone era, the outlook is bright. We sincerely welcome friends from all over the world to come and see the changes in MIM which have taken place in Greater China over the past thirty years, which has seen us using more advanced equipment and more cost-effective metal powder, making more precise MIM parts, and changing human civilisation.
Porosity of the sintered CIM alumina parts could be modified by changing the powder loading and porosity could also be increased when needed by increasing the backbone polymer content. Higher powder loading was found to show larger grain sizes in sintered alumina, whereas parts with lower powder loading showed smaller grain size and higher porosity. Bending tests showed fracture occurring along the grain boundaries. The bending strengths of the CIM alumina specimens showed that they were sufficient for use as artificial bone material.
The technological improvement of MIM materials and equipment has allowed precision MIM components to replace CNC and other high-accuracy processes. As an example, Donggung Yujia Precision Technology Co., Ltd. (a branch of Hongkong Vigor Precision Co., Ltd., the world’s largest toy gearbox manufacturer) produces small module gears by MIM (diameter ~ 3-30 mm/m=0.1~1 mm), and has received interest from the leading international robotic vacuum cleaner manufacturer. In the future, heavy-duty ‘wet and dry’ cleaners and next-generation robots will feature MIM components.
The authors reported that the higher viscosity of PP, which has the higher bending strength, makes this binder more suitable when the green CIM parts need to be machined before sintering. The bending strength of LDPE specimens increased with increasing POM and LDPE content. The authors suggested that the molecular weight or content of the backbone polymer affected the strength of green CIM alumina compacts.
Apple began to use MIM parts in its smartphones. This is the era when the MIM industry began to take off in China, with the demands of Apple being met by MIM factories such as TPT Technology, the former parent company of Suzhou CPT Technology, and Shanghai Future High-Tech. At that time, the main components were the SIM card tray ejector mechanisms and various internal parts of the phones. With the investment of Taiwan’s SZS, the hinges on Apple’s laptops also gradually switched to MIM.
Taiwan’s HTC, which was acquired by Google in 2017, began to use MIM to produce the main body of the SIM card tray, which indirectly began a trend amongst domestic smartphone brands, starting with Huawei, before extending to OPPO, Vivo, and Xiaomi. MIM components in smartphones now included camera lens protection rings and covers, side buttons for volume and power, the connector interface of I/O port, and so on (Fig. 2). From 2018, domestic Chinese smartphones producers also started to use micro gear reducers featuring many MIM parts for motorised ‘telescopic’ camera modules. MIM parts gradually reached their peak usage in smartphones.
The alumina feedstock was injection moulded into tensile bar shaped specimens. It was established that the optimum conditions for CIM of the alumina feedstock are 50–52 vol.% powder loading or 30–40 mass% in POM/PP and POM/PE in the binder composition. Bending strength was measured on both the green and sintered CIM alumina parts. Fig. 1 shows the relationship between relative density and bending strength in sintered samples, depending on the effect of powder loading, and Fig. 2 shows the same relationship, depending on the different binder compositions used.
Discover suppliers of these and more in our advertisers’ index and buyer’s guide, available in the back of PIM International.
Ceramic Injection Moulding is a manufacturing process which can meet many of the requirements for complex geometries and high precision alumina components for artificial bone materials and, where necessary, the alumina parts can be easily machined to the required shape in the green state after injection moulding and prior to sintering. This can result in low-cost custom-made alumina artificial bone structures that match the exact shape of the defective bone being replaced. The CIM alumina parts can also be produced with some porosity to allow cell ingrowth and tissue regeneration.
Based on customer demand, the use of magnetic functional materials produced via MIM has greatly increased. This has included the application of soft magnetic materials and magnetic permeable materials, the introduction of cobalt elements (e.g., Fe-50Co and F75) into the MIM process. There are a large number of applications in the magnetic guidance, electromagnetic interference shielding of electronic products.
The ability to produce these high-strength precision gears by MIM to the American Gear Manufacturers Association’s (AGMA) Q9 class accuracy is significant. Tempering after H900 heat treatment with 17-4PH significantly increases the wear resistance of the gear, allowing MIM to replace traditional PM gears and brass cut gears. As shown in Fig. 5, the technology of insert moulding plastics with MIM has also been adopted. Overall, technological improvements have enabled MIM to expand its offerings in a wider range of directions, a key to the success of MIM companies, as noted above.
In terms of known data, the combined revenue from MIM part sales in Greater China (Mainland China and Taiwan) surpassed North America, Europe, and Japan in 2011. By 2020, it past US $1.5 billion (CNY ¥10 billion) and the number of MIM factories had increased from fewer than fifty to over 200. China had become the country with the largest number of MIM applications in the world, as well as supporting a thriving industry for MIM processing equipment such as feedstock pelletisers, injection moulding machines and catalytic debinding and sintering furnaces.
Discover suppliers of these and more in our advertisers’ index and buyer’s guide, available in the back of PIM International.
The free-to-access PIM International magazine archive offers unparalleled insight into the world of MIM, CIM and sinter-based AM from a commercial and technological perspective through:
Don't miss any new issue of PIM International, and stay up to date with the latest industry news. Sign up to our fortnightly newsletter.
The weight of MIM parts ranges from less than 10 g to more than 500 g, and MIM parts are now gradually replacing parts made by investment casting and die casting. There are two favourable factors influencing this. Firstly, China’s environmental policy now strictly controls polluting wax-based casting and forging factories, which restricts the development of these industries. Secondly, China’s metal powder production industry has invested in increasing capacity. Because China’s general stainless steel production usage is high, the wide availability of stainless steel scrap for recycling and atomisation has reduced powder prices. In this way, it has become more economical to produce larger parts with MIM. As an example, the average price of MIM 304 stainless steel powder is slightly less than US $6/Kg (<40 RMB/Kg), which is close to the typical price of the same powder for conventional press and sinter PM. As time goes on, MIM 201 powder is expected to cost less than US $4.5/ kg (< 30 RMB/kg), again allowing it to directly replace the traditional low-cost stainless steel powder used in PM.
The authors used alumina (Al2O3) powder, to which was added the binder comprising polyacetal (POM) and polyolefin (PO), three types of polypropylene (PP) with different melt flow rates, low-density polyethylene (LDPE) and high-density polyethylene (HDPE)), paraffin wax (PW), fatty acid amide, and an antioxidant. POM and PO acted as the backbone polymers. Powder loading and binder composition are shown in Table 1.
The ability to change from W-Ni-Cu heavy alloy, which is difficult to control during sintering, to W-Ni-Fe has also been advantageous. With production in graphite vacuum sintering furnaces operating at 1480-1500°C, the risks of using hydrogen atmospheres in sintering is eliminated and the efficiency and safety of production greatly increased.
MIM producers in Greater China anticipated a downward trend since the beginning of the COVID-19 pandemic. To combat this, many adopted the following strategy changes:
Fig. 1 shows total annual MIM sales in Greater China as well as a breakdown of the total sales of 3C (Computer, Communication and Consumer Electronics) MIM parts used in smartphones, tablets, laptop PCs, desktops PCs and servers, and smart wearable devices. The three bold numbers in Fig. 1 identify the start of three distinct stages of MIM’s usage in smartphones.
At this point, Apple began to use the MIM cobalt-chrome-molybdenum alloy, F75, to make the rear camera frames of smartphones and tablets. Unfortunately, this was also when domestic smartphone producers began to eliminate the MIM process, citing cost considerations. What compounded the situation was that the top ten MIM suppliers were contracted with Apple with very strict specifications on production equipment, quality and specifications, so many MIM producers could not compete for business. Non-Apple smartphones switched from MIM to sheet metal and plastic products. However, the arrival of COVID-19 increased the demand for laptops and, in combination with the emergence of folding smartphones with their complex MIM hinges, a deeper slump in sales was prevented.
At the beginning of the third stage, MIM part producers in Greater China were already feeling the winds of change. Those MIM makers that originally supplied domestic smartphone producers saw demand plummet to the point that some companies had no orders to fulfil; they needed to change direction to survive. As a result, the following developments have emerged.
In March 2007, the very first issue of PIM International featured a review of Metal Injection Molding in Asia. China’s MIM industry was estimated...»
The manufacturing of golf club heads is of growing interest, and the MIM process can be better utilised than traditional manufacturing processes to provide enhanced surface effects and detailed features. This has reached the point where the United States Golf Association (USGA) now considers the MIM process to be a standard golf head manufacturing process.
Extensive MIM, CIM industry and sinter-based AM industry news, plus the following exclusive deep-dive articles and reports:
There are also opportunities for the MIM industry in the growth of metal Additive Manufacturing, in particular Binder Jetting technology. The source of everything is powder and binder, and for each of these technologies is only a matter of combining these materials. We have to understand these powders and feedstocks in a scientific way to achieve the best results in any of these processes. Striving forward with countless materials, mathematics is our only stalwart – including, of course, our diligence and tireless efforts.
Potentially with a more universal appeal, at least four MIM factories in the southern Chinese city of Yangjing make kitchen knives from MIM 420/440 stainless steel and produce more than 10 million MIM nail clippers per year; these have become staple products both domestically and overseas (Fig. 4).
There has been a significant increase over the past fifty years in the number of elderly people in the global population, which in turn has led to the need to raise awareness of osteoporosis caused by ageing and the growing demand for artificial bone materials as bones become more fragile and fracture and require to be repaired or replaced.
Extensive MIM, CIM industry and sinter-based AM industry news, plus the following exclusive deep-dive articles and reports:
A technical session, comprising three papers, at the Euro PM2021 Virtual Congress, organised by the European Powder Metallurgy Association (EPMA) a...»
GETTING A QUOTE WITH LK-MOULD IS FREE AND SIMPLE.
FIND MORE OF OUR SERVICES:
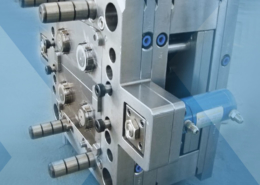
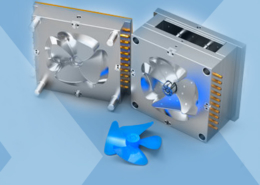
Plastic Molding

Rapid Prototyping
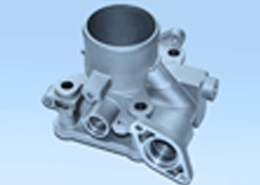
Pressure Die Casting
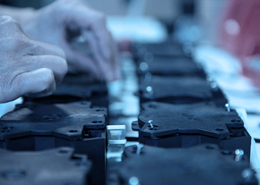
Parts Assembly
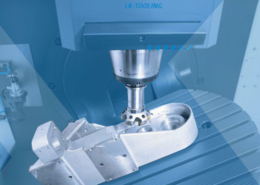