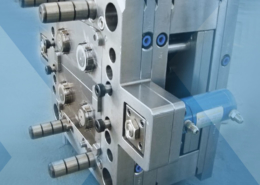
Automotive Plastics: New Thermoplastic Solutions Redefine ‘Performance’
Author:gly Date: 2024-09-30
The flagship all-electric range from TM Robotics is the SXIII all-electric series from Shibaura Machine. Shibaura Machine is the new name for Toshiba Machine — the Japanese manufacturer of industrial robots and injection mould machines. The SXIII range boasts faster injection speeds, enhanced sustainability and a streamlined design when compared to its hydraulic predecessors. What’s more, despite the perception of higher costs for all-electric machines, this range can improve cost efficiency by lowering the cost-per-part.
Leveraging a host of production equipment, lab testing, and engineering capabilities, DuPont has fine-tuned an overmolding process for bus bars that incorporates Zytel HTN material along with robust technical and processing support. Using sophisticated computer-aided analysis tools, DuPont collaborates with customers to reduce manufacturing time and cost yet maintain performance and safety standards.
The injection moulding process is responsible for up to 90 per cent of the Global Warming Potential (GWP) in the entire mould lifecycle. Recognising this, TM Robotics has championed investment in all-electric injection mould machines to replace older, more energy-intensive models.
DuPont Mobility & Materials will showcase these and other innovations at K 2022 in Düsseldorf, Germany, from Oct. 19 to 26. The company is exhibiting in booth C43 in Hall 6.
One notable observation is the prevalence of hydraulic legacy equipment that is still being used by UK manufacturers. The TM Robotics’ injection moulding servicing department has witnessed this first-hand and regularly visits manufacturing sites to service and maintain Shibaura Machine’s own hydraulic injection mould machines — some of which have been in action for up to three decades. On one hand, it is a testament to the resilience of these machines, but the industry must consider the environmental downsides of this ageing equipment.
This was demonstrated by TM Robotics’ customer Lotan, a manufacturer of plastic containers based in Leicestershire, UK. Lotan’s production facility exclusively uses all-electric injection mould machines from Shibaura Machine. The SXIII provides significantly faster injection speeds than traditional moulding equipment, providing 35% faster cycle times than conventional hydraulic servo IMMs.
Nigel Smith, managing director of TM Robotics, the international distribution partner of Shibaura Machine and the UK and Ireland distributor of its injection mould machines, explores the changing landscape of plastic's injection moulding sector and argues the case for investment in new technologies, both for better operational efficiency and improved sustainability.
DuPont Mobility & Materials is breaking new ground for manufacturers of xEV components with a combined material-process-service solution for overmolding bus bars with Zytel HTN polyamide (PA) material. Bus bars are a workhorse component essential for distributing power in xEV batteries, motors, and power electronics.
“Although small, bus bar components are numerous, and also critical to the efficiency and durability of xEV batteries, motors, and power electronics,” said Giacomo Parisi, Marketing Director for Automotive Electrification at DuPont. “Our goal is to provide an excellent material for the application, along with assisting customers in their bus bar design and overmolding, to help them achieve their performance and production goals.”
Zytel HTN has been identified as an elegant material solution in this area. For example, safety standards dictate that bus bars maintain a stable orange color indicating high voltage, even after repeated exposure to high heat. Zytel HTN accelerated aging tests show no noticeable color shifts, even at 130°C. It also contributes insulative properties for safer thermal runaway, and easily overmolds onto aluminum or copper, the most common bus bar metals.
Additionally, Zytel HTN insulation materials for bus bars resist multiple thermal shock cycles (typically 1000 cycles) at temperatures (-40° to 150°C) normally needed for motors and power electronics applications. This means the material resists cracks after being overmolded onto metal conductors. Further, the material is chemically resistant to the fluids used for thermal management and has a high comparative tracking index (CTI) at elevated temperatures.
There are over 5,800 companies operating in the UK plastics industry, contributing £25 billion to our economy each year. As a key player in Britain’s manufacturing sector, injection mould shops must embrace technological advancements in injection moulding machinery and accompanying automation for improved profit, productivity and sustainability.
Due to this lack of uptake, the UK industry is missing some of the potential benefits of industrial robots, including improved productivity, efficiency and throughput. As a primary distributor of Shibaura Machine robots in the UK, the TM Robotics team has spotted opportunities for the injection moulding sector to reap the rewards of robotic automation.
The most obvious application for robots in mould machine shops is for the loading and unloading of injection mould machines. However, many end users currently have relatively low robotic ability, having traditionally chosen Cartesian X-Y gantry style robots to unload injection moulding machines.
Another area of debate in the injection moulding world is robot integration. The UK seriously lags behind other developed countries for its number of robot installations. That’s not just for the world of injection moulding, but in the UK manufacturing sphere more widely. In fact, the International Federation of Robotics (IFR) reports that the UK has just 101 robots per 10,000 employees — rookie numbers compared to competitors in the US, China and Germany.
Injection moulding applications have long played a key part in the UK’s manufacturing industry, producing everything from medical components, automotive parts, food containers, packaging items and much more. Traditionally, our manufacturers have relied on hydraulic-powered injection moulding machines in their operations. However, the industry is now at a crossroads, faced with the imperative to embrace technological advancements for sustainability and cost-effectiveness.
Overmolded bus bars are found in virtually every xEV system. They transfer electrical energy from high-power battery packs to inverters, and inverters to e-motors, while insulating the conductor from ground or other phases. With the right materials, a bus bar can enhance a battery or e-motor energy density, durability, and electrical safety. However, it must be adequately insulated if the battery overheats, a condition known as thermal runaway, to help avoid module-to-module heat propagation.
GETTING A QUOTE WITH LK-MOULD IS FREE AND SIMPLE.
FIND MORE OF OUR SERVICES:
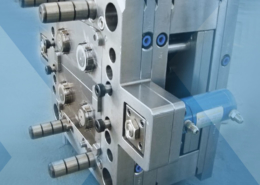
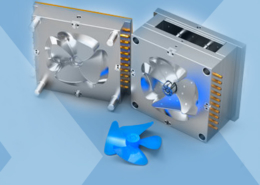
Plastic Molding

Rapid Prototyping
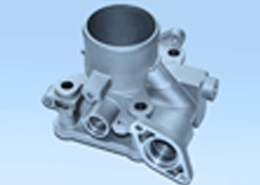
Pressure Die Casting
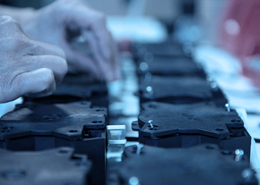
Parts Assembly
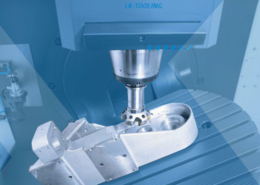