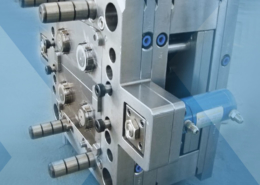
Australian meat trays changed from black to clear plastic to boost
Author:gly Date: 2024-09-30
Digital manufacturing company Proto Labs (Maple Plain, MN) announced today that it has added on-demand manufacturing of low-volume, high-mix products to its suite of services.
The medical device market is one beneficiary of this service because it often has products with fairly low total annual volumes and unpredictable demand, CEO Vicki Holt told PlasticsToday. But, she added, on-demand manufacturing reduces supply chain risk and brings value across all industries where there is either demand volatility or low- to mid-volume annual production quantities.
“Comparing the last two of these services, we find that 3D printing tends to work best for very complex designs that cannot be made in another process. For designs where this is not true, beyond a few [other] parts, the economics favor Proto Labs’ technology-enabled digital process for manufacturing a custom injection molded tool and molding the parts,” explained Holt. “Given our injection molding process and prices, our experience is that if the part is manufacturable via injection molding, it usually makes economic sense to build an injection mold tool and mold the parts rather than print them, unless you are making a small handful of total parts.” Proto Labs intends to play in both on-demand manufacturing of injection molded parts and 3D printed parts, said Holt.
Arburg also has another exhibit at its trade fair stand showing that high-grade plastic parts can also be manufactured from post-consumer recyclate (PCR): an electric Allrounder 470 A with a clamping force of 1,000 kN and equipped with the recyclate package from Arburg produces the same two handle halves for the toolbox. However, at the K 2022, PCR on the basis of PP (Dipolen) from mtm plastics (a 100% subsidiary of the Borealis Group) is used. Sensors monitor the internal pressure in the mould to ensure high part quality. The “aXw Control ReferencePilot” assistance function integrated in the Gestica control system ensures precise holding pressure and constant shot weights, whereas the new feature “aXw control RecyclatePilot" ensures a stable shot weight by means of adaptive process control. Moreover, the components are weighed directly after the demoulding. In this way, weight deviations can be detected and documented immediately after injection moulding, with good and bad parts sorted downstream. Handling is carried out by a Multilift V 10 with a load-bearing capacityof 10 kilograms. The new linear robotic system has a dynamic entry axis that reaches speeds of up to 4,000 millimetres per second.
The hybrid Allrounder 1120 H uses the Gestica control system and numerous smart functions. At the K 2022, Arburg will present for the first time the Varimos plug-in from Simcon, and the AI-supported variant analysis from Cadmould, where the injection moulding simulation is automated and learns which effects machine parameter changes have. Through the cross-linking of the software with the Gestica control system, even more precise machine parameters can be generated during the filling simulation with the "aXw Control FillAssist," and the configuration of moulded part and injection mould shortened from several weeks to a few days. A further assistance function for this application is the "aXw Control EnergyAssist," which helps to optimise switching on and off for all heating zones.
Among other features, over-moulded 3D design films on all eight corners of the toolbox provide the necessary styling and high-grade aesthetics. The film inserts from project partner, Leonhard Kurz, are positioned on workpiece carriers and fed into the production cell via a double sliding table. There, a new Scara robot from KUKA, which can be programmed via the machine control system, processes and positions them while observing the cavity distances of the injection mould. Then a linear robotic system gets into action: the Multilift V 40 picks up the inserts from the centring station, moves past an ionisation bar, which cleans them, and inserts them into the 1+1-cavity injection mould. Here, they undergo in-mould lamination in the insert moulding process. This is especially suitable for heavily profiled components. The robotic system then removes the two moulded parts and feeds the lid to a hot stamping station, where the embossed Arburg lettering is refined inline with a brushed and metallised decor. The lid is discharged together with the lower tray via a conveyor system.
“Since every manufacturing project is different, our two injection molding options let customers begin to focus on what is really needed from their tooling,” explained Becky Cater, Global Product Manager for injection molding at Proto Labs. “Whether it’s a product development need for molded prototypes or a strategic partnership for on-demand production parts, we now have a total solution for the entire life cycle of a product.”
“Digital inspection reporting is a final checkpoint for the digital thread as it moves from CAD model to final part,” said Jeff Schipper, Director of Special Operations at Proto Labs, and lead engineer in the metrology lab. “We’ve always provided our customers with front-end design analysis on their CAD models really fast—digital inspections bookend this process by significantly reducing the cost and time associated with conventional inspection reporting.”
Proto Labs has also announced the opening of its first metrology lab for enhanced inspection reporting on end-use production parts. The lab houses a range of standard inspection equipment, as well as state-of-the-art 3D scanners that provide an automated 360-degree look at parts within minutes. In addition to the standard range of first article inspection reports, the company also offers a digital inspection report that includes a precision surface scan with a detailed color map for a direct CAD-to-scan comparison to quickly identify dimensional variances on parts.
The Arburg management team pose with the toolboxes in front of the Allrounder at a press event on the eve of the show's opening.
Editor in chief of PlasticsToday since 2015, Norbert Sparrow has more than 30 years of editorial experience in business-to-business media. He studied journalism at the Centre Universitaire d'Etudes du Journalisme in Strasbourg, France, where he earned a master's degree.
On-demand manufacturing capabilities are designed to address a gap in manufacturing services for low-volume, custom molded components.
“We serve leading companies across many industrial segments, where on-demand manufacturing can help manufacturers reduce working capital, respond to unpredictable customer demand or tap into revenue growth streams with lower volume end products tailored to specific customer needs,” said Holt. Beyond medical manufacturing, those segments include computer/electronics, aerospace, industrial equipment and even automotive, according to Holt. “My favorite examples are customers who have launched successful products because of Proto Labs that they could not previously afford to launch with their existing supply chain,” added Holt.
Just about a year ago, Proto Labs opened a 77,000-square-foot additive manufacturing hub in Cary, NC, which houses more than 70 machines and has room for 70 more. That is consistent with Proto Labs' strategy of offering a range of manufacturing services to meet demand for low-volume, high-mix plastic parts, noted Holt, including CNC machining, 3D printing and injection molding.
The innovative tool carrier is combined with a manual workstation outside the turnkey system. There the toolbox is completed: the centre section, handle, closing clips and the feet were pre-manufactured on Allrounders at Arburg in Lossburg. The black-grey components are made from Recopound® from Leonhard Kurz. This material is extracted from post-industrial recyclate (PIR) from PET films. Compared to new material, it uses up to 40 percent less CO2.
The hybrid Allrounder 1120 H from the Hidrive series features a clamping force of 6,500 kN and a size 7000 injection unit, making it the biggest Arburg injection moulding machine. The turnkey system also contains a Multilift V robotic system with 40 kilogram load.
The new capability is designed to address a gap in manufacturing services for low-volume, custom molded components, said the company in a press release. “Companies had to purchase in large volumes to meet the minimum order quantities often required by traditional manufacturers, and work with multiple vendors to address varied needs from prototyping to final part production,” said Proto Labs. By tailoring its offerings to specifically address the needs of both prototyping and on-demand manufacturing, Proto Labs is able to reduce cost and the time spent on parts procurement.
GETTING A QUOTE WITH LK-MOULD IS FREE AND SIMPLE.
FIND MORE OF OUR SERVICES:
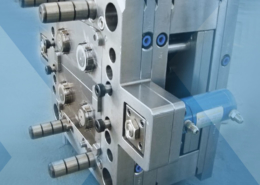
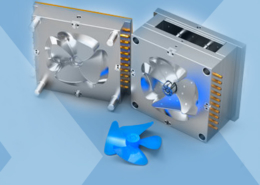
Plastic Molding

Rapid Prototyping
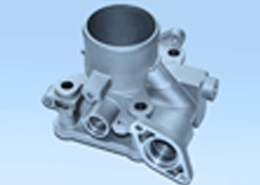
Pressure Die Casting
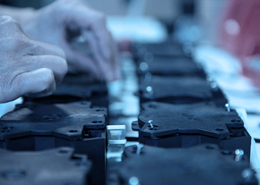
Parts Assembly
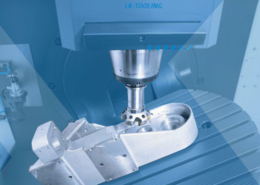