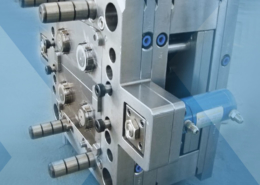
Athena: Robert Schad returns to injection molding - husky injection molding comp
Author:gly Date: 2024-09-30
The company routinely molds cannulas at volume with outside diameters of 0.035 in. (0.889 mm), inner diameters of 0.027 in. (0.6858 mm), and wall thicknesses measuring 0.004 in.(0.1016 mm). “We have achieved this through attention to material choice, several critical design for manufacturing operations, assembly considerations, maintaining a balanced aspect ratio to avoid challenges associated with flow dynamics, cooling, structural integrity, and importantly through the use of our proprietary micro-molding presses,” explained Runyan. “Micro molding thin-walled cannulas is a game changer for medical device manufacturers, overcoming the labor-intensive, time-consuming, and expensive traditional thin-wall cannula manufacturing processes such as extrusion, tipping, and gluing to a metal hub.”
“Accumold is rightly today acknowledged as the world leader when it comes to the manufacture of extraordinarily small plastic parts that require extreme precision — typically measured in microns,” said Paul Runyan, VP of sales and marketing. “The company is adept at the production of small-sized parts with micro features from 5 cm to less than 1 mm, and has specific expertise in insert molding, two-shot molding, and cleanroom molding using an array of materials including PEEK, liquid crystal polymers, and most engineering thermoplastics.”
The medical device industry demands absolute precision, totally repeatable manufacturing processes, and zero failure rates for products that are frequently used in safety-critical applications, notes Accumold in its announcement.
The hybrid Allrounder 1120 H from the Hidrive series features a clamping force of 6,500 kN and a size 7000 injection unit, making it the biggest Arburg injection moulding machine. The turnkey system also contains a Multilift V robotic system with 40 kilogram load.
Now that NPE2024 is history, there are some admittedly smaller but still worthy trade shows on the horizon for sourcing suppliers of plastics processing services. One that you may want to consider attending is Plastec South, co-located with Medical Design & Manufacturing (MD&M) alongside packaging, automation, design and manufacturing, and Powder Bulk Solids trade shows under the IME South umbrella in Charlotte, NC. In particular, a pioneer of medical micro molding will be exhibiting at the event in June.
The Arburg management team pose with the toolboxes in front of the Allrounder at a press event on the eve of the show's opening.
The innovative tool carrier is combined with a manual workstation outside the turnkey system. There the toolbox is completed: the centre section, handle, closing clips and the feet were pre-manufactured on Allrounders at Arburg in Lossburg. The black-grey components are made from Recopound® from Leonhard Kurz. This material is extracted from post-industrial recyclate (PIR) from PET films. Compared to new material, it uses up to 40 percent less CO2.
In booth 1911, Accumold will be showcasing some of the tiny titans it has produced to exacting specifications for medical device OEMs over its nearly 40-year history. A highlight are thin-walled cannulas that the company can now micro injection mold at volume.
IME South comes to the Charlotte Convention Center in Charlotte, NC, on June 4 to 6, 2024. In addition to more than 300 exhibitors on the show floor, the event features more than 40 educational sessions led by experts in 3D printing, medical technology, packaging, and smart manufacturing. A welcome reception is scheduled at the NASCAR Hall of Fame on June 4. Tickets are available for purchase when you register to attend.
The hybrid Allrounder 1120 H uses the Gestica control system and numerous smart functions. At the K 2022, Arburg will present for the first time the Varimos plug-in from Simcon, and the AI-supported variant analysis from Cadmould, where the injection moulding simulation is automated and learns which effects machine parameter changes have. Through the cross-linking of the software with the Gestica control system, even more precise machine parameters can be generated during the filling simulation with the "aXw Control FillAssist," and the configuration of moulded part and injection mould shortened from several weeks to a few days. A further assistance function for this application is the "aXw Control EnergyAssist," which helps to optimise switching on and off for all heating zones.
Arburg also has another exhibit at its trade fair stand showing that high-grade plastic parts can also be manufactured from post-consumer recyclate (PCR): an electric Allrounder 470 A with a clamping force of 1,000 kN and equipped with the recyclate package from Arburg produces the same two handle halves for the toolbox. However, at the K 2022, PCR on the basis of PP (Dipolen) from mtm plastics (a 100% subsidiary of the Borealis Group) is used. Sensors monitor the internal pressure in the mould to ensure high part quality. The “aXw Control ReferencePilot” assistance function integrated in the Gestica control system ensures precise holding pressure and constant shot weights, whereas the new feature “aXw control RecyclatePilot" ensures a stable shot weight by means of adaptive process control. Moreover, the components are weighed directly after the demoulding. In this way, weight deviations can be detected and documented immediately after injection moulding, with good and bad parts sorted downstream. Handling is carried out by a Multilift V 10 with a load-bearing capacityof 10 kilograms. The new linear robotic system has a dynamic entry axis that reaches speeds of up to 4,000 millimetres per second.
Vertical integration enables the company to operate as a one-stop partner in the development and manufacture of medical devices and components, added Runyan. “Under one roof, Accumold offers design and material assistance, micro tool fabrication, proprietary micro-molding services, cutting-edge metrology, assembly, and automation, and this facilitates the streamlining of customer’s medical product development process, and the attainment of optimal outcomes in terms of timeliness, cost, and accuracy.”
Editor in chief of PlasticsToday since 2015, Norbert Sparrow has more than 30 years of editorial experience in business-to-business media. He studied journalism at the Centre Universitaire d'Etudes du Journalisme in Strasbourg, France, where he earned a master's degree.
Exhibitor Accumold will explain how micro molding thin-walled cannulas reduces labor requirements and cost compared with conventional production methods.
Among other features, over-moulded 3D design films on all eight corners of the toolbox provide the necessary styling and high-grade aesthetics. The film inserts from project partner, Leonhard Kurz, are positioned on workpiece carriers and fed into the production cell via a double sliding table. There, a new Scara robot from KUKA, which can be programmed via the machine control system, processes and positions them while observing the cavity distances of the injection mould. Then a linear robotic system gets into action: the Multilift V 40 picks up the inserts from the centring station, moves past an ionisation bar, which cleans them, and inserts them into the 1+1-cavity injection mould. Here, they undergo in-mould lamination in the insert moulding process. This is especially suitable for heavily profiled components. The robotic system then removes the two moulded parts and feeds the lid to a hot stamping station, where the embossed Arburg lettering is refined inline with a brushed and metallised decor. The lid is discharged together with the lower tray via a conveyor system.
The ISO 13485–certified company is sufficiently large to offer affordable pricing and the capacity and infrastructure to ramp up to full mass-volume manufacturing, he added.
GETTING A QUOTE WITH LK-MOULD IS FREE AND SIMPLE.
FIND MORE OF OUR SERVICES:
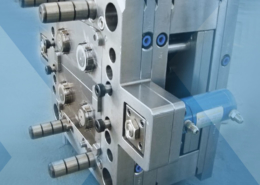
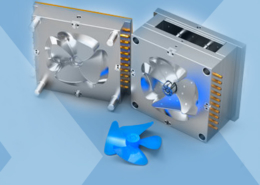
Plastic Molding

Rapid Prototyping
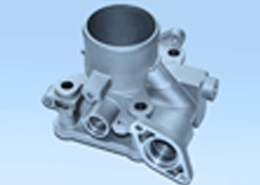
Pressure Die Casting
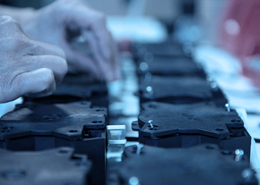
Parts Assembly
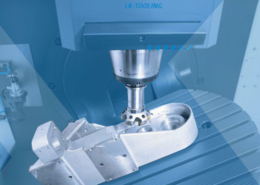