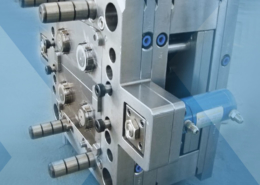
Army researchers use cutting edge 3D printers - star rapid injection molding
Author:gly Date: 2024-09-30
Netstal is displaying a lightweight, thin-wall, injection compression moulded cup for dairy products, reportedly made of 100% polypropylene, at Fakuma.
Reportedly, the filling volume of the cup is 200g, its part weight 5.4g, and its wall thickness 0.3mm. Injection compression moulding, or ICM, claims to reduce the cup’s weight by 34% and, when combined with product optimization, lowers packaging volume by 27%.
Injection molding technologies are always evolving to meet the latest consumer demands and design requirements. As manufacturers push the boundaries on design and performance, existing technologies often can’t meet these needs, resulting in reduced design freedom and issues with production efficiency, part cost and part quality. Packed with real-world examples, this visual guide showcases some of the recent advancements in injection systems enabling manufacturers to overcome these challenges, with precise control over the injection process.
The thin wall is manufactured in four cavities at a cycle time of 2.7 seconds in an Elion 1750 injection moulding machine with a hybrid injection unit. Adaptive system pressure reduction has also been applied in an effort to increase the efficiency of its hybrid machines.
Netstal will also provide mould partner Ceylan with an all-electric Elion 2200, which will produce 150g margarine trays with IML decoration in four cavities. Eurasia Robotic created the IML system with side removal, camera control, and packaging unit.
A collaboration between Plastiques Venthenat, Amcor, Olga, Cedap, and Arcil-Synerlink has also resulted in a form-fill-seal yoghurt pot that claims to be fully recycle-ready. Its 98.5% polystyrene content is expected to smoothen the sorting and recycling processes.
Previously, ENGEL, ALPLA Group, Brink and IPB Printing collectively produced thin-walled containers made of PET and rPET in a single injection moulding process step; and Sumitomo (SHI) Demag expanded its IntElect S all-electric high-performance injection moulding machine range to explore low part weights, narrow tolerance components, and other product applications.
Additionally, Netstal is showcasing Axos 9, the newest generation of its control technology. Set to be applied to the Elion and Elios series machines, the technology comes with an operating concept expected to maximise performance.
When operating in automatic mode, the control system identifies the optimum point at any time and adjusts the pressure in the hydraulic system. Netstal states that, depending on the application, this adjustment can minimize the energy consumption required to reach the appropriate system pressure.
Due to its mono-material design, it is said to be easy to recycle. The label apparently comes apart from the rest of the pack during the recycling process – unlike a conventional in-mould label – and the printing ink particles are separated from the pure polypropylene to keep the recycling stream from becoming contaminated.
It offers a show weight of 42g and a cycle time of 3.8 seconds, and the turnkey production line will run at Ceylan’s booth at Fakuma.
Smart Operation, only available as a paid option in past models, has been implemented into the scope of delivery from Axos 9. It claims to facilitate the fast, safe, and effective operation of Elion and Elios machinery.
Glaroform, Beck Automation, SABIC, IPB Printing, motan, Regloplas, and Uniform Color also contributed to the creation of the pack, with dairy product bottler Emmi AG also serving as a development partner. The cup’s previous appearance has been maintained while its specifications have been tailored to Emmi’s requirements.
GETTING A QUOTE WITH LK-MOULD IS FREE AND SIMPLE.
FIND MORE OF OUR SERVICES:
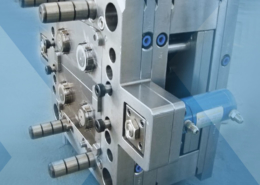
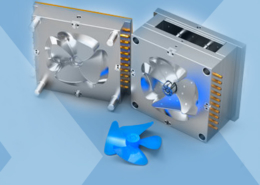
Plastic Molding

Rapid Prototyping
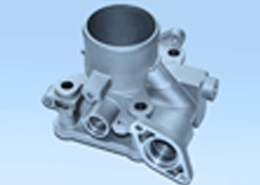
Pressure Die Casting
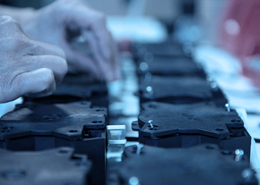
Parts Assembly
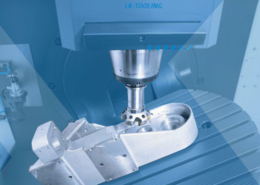