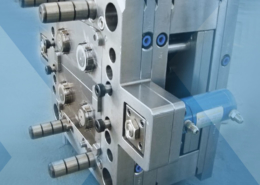
Arburg Demos Medical In-mold Labeling Application at NPE - polypropylene molding
Author:gly Date: 2024-09-30
For instance, in 2020, Comar, a US manufacturer and designer of innovative plastic solutions, announced locating a custom facility in Rancho Cucamonga, CA. The 230,000-square-foot facility is Current Good Manufacturing Practice regulation (cGMP)-compliant, ISO 13485-certified, and FDA-registered, with dedicated injection blowmolding, injection-stretch blowmolding, and injection-molding cells.
Companies are investing in research and development to produce new industrial plastics to keep up with market competitiveness and meet evolving end-user demands.
The new facility offers a full-service mold prototyping lab as well as a specialized mold sample and development machine, allowing customers to quickly move from concept through design, prototype, and full production.
For the packaging sector, AIMPLAS presented results of projects that included biodegradable barrier packaging made from food waste, plastic film derived from coffee waste, active packaging that extends the shelf life of cheese and is made from cheese-industry waste, and cartridges for 3D food printing.
Asia-Pacific was the largest region in the blow-molded plastics market in 2021 and is expected to remain the largest through the forecast period.
Polypropylene is used in a variety of applications, including plastic packaging, machinery and equipment parts, and fibers and textiles. Extrusion, injection, and stretch are the various technologies used in blowmolding plastics for packaging, consumables, electronics, automotive and transport, building and construction, medical, and other applications.
Producing hollow plastic products from thermoplastic materials is a quick manufacturing solution and offers versatile products with broad industrial appeal. Markets include food suppliers, medical and pharmaceutical companies, and others.
The global blow-molded plastics market grew from $89.39 billion in 2022 to $92.93 billion in 2023 at a compound annual growth rate (CAGR) of 4.0%. The blow-molded plastics market is expected to grow to $108.75 billion in 2027 at a CAGR of 4.0%, according to a report published in February by Reportlinker. The market consists of sales coveringcompound blowmolding and compression blowmolding.
In October 2021, Recycler EFS-plastics Inc., a Canada post-consumer plastics recycler with a focus on processing bales of low-value plastics, acquired Exi-Plast Custom Moulding for an undisclosed amount. Through this acquisition, EFS can directly manufacture finished products with high levels of post-consumer recycled plastic for its customers. Exi-Plast Custom Moulding is a Canadian company that provides custom plastic molding services, particularly in blow-molded solutions for designers, manufacturers, and distributors.
Major types of blow-molded plastics are polypropylene, acrylonitrile butadiene styrene (ABS), polyethylene, polystyrene, polyvinyl chloride PVC, PET, and others. Polypropylene (also known as propane or propylene) is a tough, rigid, crystalline thermoplastic derived from the monomer propane or propylene.
Success stories at the seminar included the biodegradability of proprietary bioplastic material; biopolymer solutions for sustainable agriculture; and a method for measuring biodegradation in compost, fresh and waste waters, soil, and marine environments.
Bio Plast Pom has worked with the Gdańsk University of Technology and other scientific centres to design a compostable and biodegradable material based on potato starch – aspiring for reduced environmental impact, lower CO2 emissions, and energy efficiency.According to Bio Plast Pom, NOPLA is not a synthetic material. It is reportedly free of both artificial ingredients and plastics and is not thought to leave behind microplastics when it decomposes.Apparently, the patent-protected material is biodegradable and compostable in a household composter, salt water, freshwater, and soil. It is designed to comply with the EN 13432 composting standards and claims to degrade in 3 to 6 months under household composting conditions.The company says that NOPLA products sink to the bottom of bodies of water and, instead of causing harm to bottom sediments, provide sustenance for living organisms. Furthermore, the material aligns with EU Directive 904/2019 SUP, meaning it can be used to manufacture products like cutlery and straws. It is approved for food contact, with the Polish Institute of Hygiene running tests to ensure it does not migrate. Bio Plast Pom adds that NOPLA products have a footprint of 1.7kg of CO2 per kilogram, compared to the 3.5kg emitted by polypropylene. It is said that the manufacturing process consumes around 30% less energy, leading to a smaller carbon footprint and lower costs. Rather than utilizing chemicals, it is physically and mechanically modified. NOPLA’s biogranulate is suitable for injection moulding, blow moulding, and thermoforming on existing machinery, which is expected to help manufacturers pursue sustainability in their product lines. Also, it is set to avoid recycling fees that are being implemented for plastic products across Europe. Bio Plast Pom has designed, built, and copyrighted an original production line for the biogranulate, and production commenced in May 2023. In a similar development, The National University of Malaysia and Tunku Abdul Rahman University of Management and Technology’s starch-based biopolymer film for application as active and intelligent food packaging was previously nominated for a Sustainability Award under the pre-commercialized Active and Intelligent category.Last year, researchers from Michigan State University’s School of Packaging claim to have enhanced the compostability of PLA by fusing it with starch. The result was hoped to improve the plastic’s compatibility with home and industrial composting processes, thus keeping plastic waste out of landfill.Other companies have also sought to source their packaging materials from natural substances. This includes RAW Packaging’s 'zero tree' concept, in which crop waste like wheat and sugar cane bagasse is converted into packaging – a concept that Jimmy’s Iced Coffee has now adopted across its e-commerce product line.
GETTING A QUOTE WITH LK-MOULD IS FREE AND SIMPLE.
FIND MORE OF OUR SERVICES:
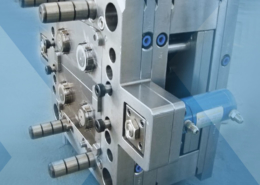
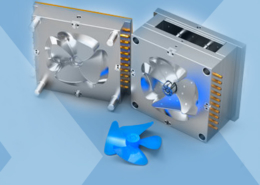
Plastic Molding

Rapid Prototyping
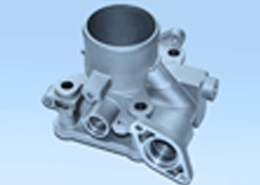
Pressure Die Casting
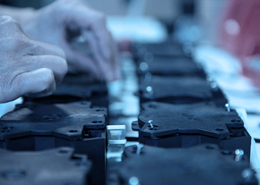
Parts Assembly
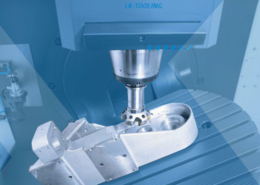