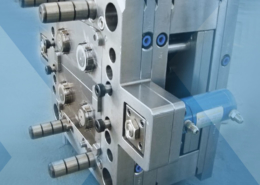
APG offers Metal Injection Moulding beginner’s guide for engineers - precision i
Author:gly Date: 2024-09-30
I tend to agree, based on my experience with every single piece of consumer electronic or electrical equipment I´ve purchased over the last 20 years...
More recently, work has been more heavily centred on pharmaceutical moulds, entailing machining of even greater complexity that requires multiple set-ups on a three-axis machine, the use of long cutters to access awkward areas from above, and repeated repositioning for side features to be included.
The advantage of using five-axis machining on some jobs is dramatic. For instance, one of the company’s products – an inhaler mould – was previously machined in a total of eight hours on a three-axis Roeders and an EDM machine in five operations. The five-axis HSC machine tackles the same job in a single set-up in one-quarter of the time – just two hours complete.
A move from electric discharge machining (EDM) to high-speed milling has helped Irish toolmaker Galway Tool & Mould (GTM) cut its lead times by up to 20 per cent.
In addition to its headquarters in Rochester, Atalys has manufacturing facilities in Asheboro, NC, and the Dominican Republic. The New York and North Carolina plants have multiple Class 8 cleanrooms for molding and assembly on site; the Santo Domingo site in the Dominican Republic offers cleanroom assembly and automation. The company said it adheres to scientific molding principles and is equipped with presses ranging in size from “near micro molding” to 1,400 tons.
In February, Atalys announced that it is tripling the size of its existing facility in the Dominican Republic from 15,000 to 47,000 square feet through the addition of a new 32,000-square-foot building. The company said that the new building will be dedicated to manual assembly with complementary injection molding, pad printing, tool repair, and warehousing. The existing facility will become the company's primary plastics processing site focused on cleanroom injection molding as well as secondary operations such as testing and packaging.
Editor in chief of PlasticsToday since 2015, Norbert Sparrow has more than 30 years of editorial experience in business-to-business media. He studied journalism at the Centre Universitaire d'Etudes du Journalisme in Strasbourg, France, where he earned a master's degree.
This has led to a doubling of turnover between 2012 and 2015 and an increase in floor area from 4,000 to 15,000ft2, with an extension of an additional 8,000ft2 currently being added.
The latest innovation off-line set-up of jobs on a coordinate measuring machine, which, when fully implemented, will add an extra 10 hours of production per week across the three Roeders machines.
"Our acquisition of Schnipke was driven by a focused strategy to deepen our capabilities, capacity, and technical superiority across the entire manufacturing process for medical device components,” said Vinc Ellerbrock, president and CEO of Atalys. “The addition of Schnipke adds two manufacturing sites for scalable growth, broadens our geographic presence and reach, enables us to serve a wider array of customers, and significantly augments our technical capabilities,” said Ellerbrock.
According to shop-floor manager Mark Walsh, since investing in three German-built Roeders machining centres supplied by High Wycombe firm Hurco Europe, the firm has shaved as much as 70 per cent off key areas of the manufacturing process.
With the medical sector demanding tight tolerances, excellent surface finishes and short lead times, the firm found that the EDM techniques it was using to produce moulds were becoming too time consuming, so it made the decision to instead use high speed machining wherever possible.
Plastics injection molder Atalys LLC announced yesterday that it has acquired Schnipke Engraving Co. LLC. Both companies provide injection molding and related services to medical device OEMs. Atalys, based in Rochester, NY, said the acquisition will enhance its manufacturing capabilities, technology, and geographical footprint.
Founded in 1967, Schnipke has established a reputation for building tools in-house and designing and engineering molds that meet the medical device industry's stringent requirements for precision at extremely tight tolerances, said the news release. The company claims on its website that it can mold within tolerances of +/-0.001 inches and as small as 0.02 grams in weight. Even smaller dimensions can be accommodated upon customer request.
In just over a year´s time, Microsoft will stop supporting Windows 10. I foresee that a lot of businesses (that tend to run slightly older hardware)...
A five-axis vertical machining centre (VMC) was the obvious solution, so in May 2015 a Roeders RXP601 DSH with a 96-tool magazine was installed, again with automation but this time provided by a 38-position pallet change system to allow longer periods of unattended running. A second RXP601 could be served by the same automation equipment if required in the future.
Alongside the move to high-speed milling, the firm has also invested in metrology equipment, recently opening a laboratory for tool validation and an in-house trial facility for moulds equipped with Fanuc electric moulding machines ranging from 100 to 300 tons capacity.
Earlier this week, another medical injection molder made news when Total Molding Services announced that it has been acquired by Haartz Family Holdings, changing its name to Moldgenix in the process.
The company – which employs 30 engineers at its Galway facility – specialises in the manufacture of high precision injection moulds for the medical, pharmaceutical and high-volume packaging sectors.
Schnipke has tooling and plastic injection molding operations at its headquarters in Ottoville, OH, and operates a second manufacturing facility in Tucson, AZ. The company is FDA registered and is certified to ISO 13485:2016.
GETTING A QUOTE WITH LK-MOULD IS FREE AND SIMPLE.
FIND MORE OF OUR SERVICES:
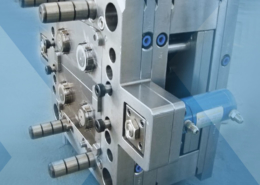
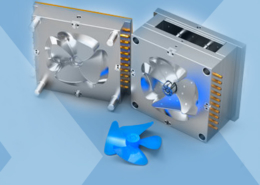
Plastic Molding

Rapid Prototyping
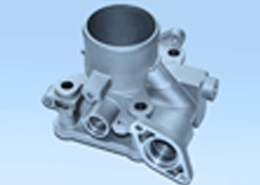
Pressure Die Casting
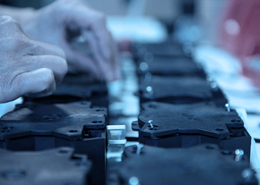
Parts Assembly
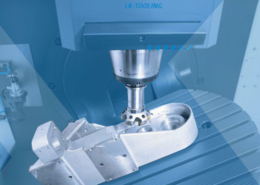