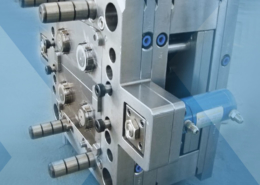
Anti-mold, self-cleaning superhydrophobic bamboo fiber/polypropylene
Author:gly Date: 2024-09-30
Beck points out that, while Hy-Lite can’t manufacture safety masks or blow-molded items (such as hand sanitizer bottles), the company has many other options for supporting PPE needs.
Performance cookies collect information about how you use a website, e.g. which pages you go to most often, and if you get error messages from web pages. These cookies don’t collect information that identifies you personally as a visitor, although they might collect the IP address of the device you use to access the site.
Browse the most current issue of Design World and back issues in an easy to use high quality format. Clip, share and download with the leading design engineering magazine today.
Copyright © 2024 WTWH Media LLC. All Rights Reserved. The material on this site may not be reproduced, distributed, transmitted, cached or otherwise used, except with the prior written permission of WTWH Media Privacy Policy | Advertising | About Us
“We understand manufacturers of personal protection equipment and other supplies are running at maximum capacity and are challenged to keep up with demand,” says Steve Beck, plant/technical manager for Hy-Lite, a U.S. Block Windows Company. “If we can be a small part of the solution in a national emergency, then we want to help.
Vice President of Environmental Responsibility at the LEGO Group, Tim Brooks said: “We are super excited about this breakthrough. The biggest challenge on our sustainability journey is rethinking and innovating new materials that are as durable, strong and high quality as our existing bricks – and fit with LEGO elements made over the past 60 years. With this prototype we’re able to showcase the progress we’re making.”
It will be some time before bricks made from a recycled material appear in LEGO product boxes. The team will continue testing and developing the PET formulation and then assess whether to move to the pilot production phase. This next phase of testing is expected to take at least a year.
Strictly necessary cookies allow core website functionality and the website cannot be used properly without them. These cookies include session cookies and persistent cookies.
Brooks said: “We know kids care about the environment and want us to make our products more sustainable. Even though it will be a while before they will be able to play with bricks made from recycled plastic, we want to let kids know we’re working on it and bring them along on the journey with us.
The patent-pending material formulation increases the durability of PET to make it strong enough for LEGO bricks. The innovative process uses a bespoke compounding technology to combine the recycled PET with strengthening additives.
We use cookies to give you the best experience and to learn about your use of our site for advertising and analytics purposes. Please continue if you are happy with this or view our Cookie policy to find out more. Change your cookie settings.
Top global problem solving EE forum covering Microcontrollers, DSP, Networking, Analog and Digital Design, RF, Power Electronics, PCB Routing and much more
Brooks said: “We’re committed to playing our part in building a sustainable future for generations of children. We want our products to have a positive impact on the planet, not just with the play they inspire, but also with the materials we use. We still have a long way to go on our journey but are pleased with the progress we’re making.”
“From downstream assembly to packaging and shipping, we make this process turnkey for the customers. We’re a Made in America company that wants to support the plastics needs of America during this difficult time.”
Keeping these cookies enabled helps us to improve our website and display content that is more relevant to you and your interests across the Google content network.
The recycled prototype brick is the latest development in making the LEGO Group’s products more sustainable. In 2020, the company announced it will begin removing single-use plastic from its boxes. In 2018, it began producing elements from bio-polyethylene (bio-PE), made from sustainably sourced sugarcane.
We want our products to have a positive impact on the planet, not just with the play they inspire, but also with the materials we use. We still have a long way to go on our journey but are pleased with the progress we’re making.
Session cookies keep track of your current visit and how you navigate the site. They only last for the duration of your visit and are deleted from your device when you close your browser.
“We’re offering both the expertise and machinery we have onsite to support the injection molding needs of inventors, plastic parts suppliers, and manufacturers — whether someone needs high volume parts or a small quantity of intricate pieces.”
This website uses cookies so that we can provide you with the best user experience possible. Cookie information is temporarily stored in your browser and helps our team to understand which sections of the website you find most interesting and useful.
Hy-Lite services are available on a contracted basis with speedy turnaround. Beck, who has been with Hy-Lite for more than two decades directing the company’s injection molding and manufacturing operations, explains that Hy-Lite can supply products made with most thermoplastics.
The prototype is made from recycled PET sourced from suppliers in the United States that use US Food & Drug Administration (FDA) and European Food Safety Authority (EFSA) approved processes to ensure quality. On average, a one-litre plastic PET bottle provides enough raw material for ten 2 x 4 LEGO bricks.
For more details on working with Hy-Lite Injection Molding Services, contact Steve Beck at 888-256-2599 or visit www.hy-lite.com.
To help with the heightened demand for injection-molded products during the COVID-19 outbreak, Hy-Lite is making their Contract Injection Molding Services available to companies nationwide. Located in Pensacola, Fla., the Hy-Lite facility houses seven injection molding machines capable of small, specialty and slow run projects.
“Our team can take on injection molding projects for manufacturers running at capacity, whether it’s supplementing high-demand product production or taking over less-critical secondary lines that have had to be placed on the backburner,” says Beck. “We have three 300-ton, one 390-ton, and three 500-ton machines available at the place for 24/7 operation. This means we can tackle the small quantity runs and slow running parts because the machinery is always ready for projects.”
The LEGO Group’s focus on sustainable material innovation is just one of several different initiatives the company has in place to make a positive impact. The LEGO Group will invest up to US $400 million over three years to 2022 to accelerate its sustainability ambitions.
Lisa Eitel has worked in the automation industry since 2001. Her areas of focus include motors, drives, motion control, power transmission, linear motion, and sensing and feedback technologies. She has a B.S. in Mechanical Engineering and is an inductee of Tau Beta Pi engineering honor society; a member of the Society of Women Engineers; and a judge for the FIRST Robotics Buckeye Regionals. Besides her motioncontroltips.com contributions, she also leads the production of the quarterly motion issues of Design World.
Many LEGO sets contain elements made from bio-PE which is perfect for making smaller, softer pieces such as trees, branches, leaves and accessories for minifigures. Bio-PE is not currently suitable for making harder, stronger elements such as the iconic LEGO bricks.
The new prototype, which uses PET plastic from discarded bottles, is the first brick made from a recycled material to meet the company’s strict quality and safety requirements.
“Experimentation and failing is an important part of learning and innovation. Just as kids build, unbuild and rebuild with LEGO bricks at home, we’re doing the same in our lab.”
A team of more than 150 people are working to find sustainable solutions for LEGO products. Over the past three years, materials scientists and engineers tested over 250 variations of PET materials and hundreds of other plastic formulations. The result is a prototype that meets several of their quality, safety and play requirements – including clutch power.
Targeting cookies collect information about your browsing habits. They are usually placed by advertising networks such as Google. The cookies remember that you have visited a website and this information is shared with other organisations such as media publishers.
Persistent cookies last after you’ve closed your Internet browser and enable our website to recognise you as a repeat visitor and remember your actions and preferences when you return.
GETTING A QUOTE WITH LK-MOULD IS FREE AND SIMPLE.
FIND MORE OF OUR SERVICES:
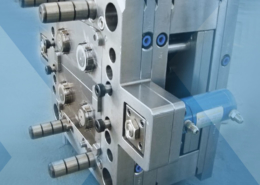
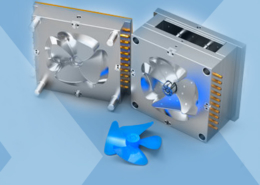
Plastic Molding

Rapid Prototyping
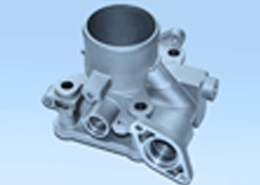
Pressure Die Casting
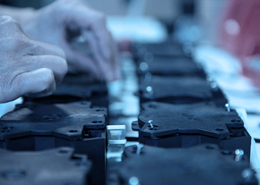
Parts Assembly
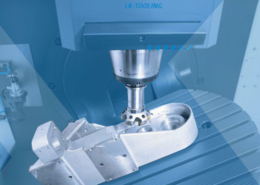