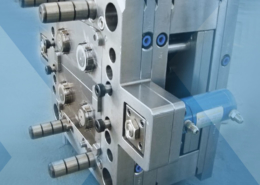
ALPLA strengthens injection moulding business with new ALPLAinject division - pl
Author:gly Date: 2024-09-30
The acquisition joins Pikes Peak Plastics and Altratek in a new plastics injection molding company serving the industrial, energy, electronics, medical, telecommunications, and automotive industries.
Japan’s Polyplastics says POM and PP can replace the likes of higher-cost PPS, which is typically used to channel coolant in internal combustion engines.
Certified to ISO 9001, ISO 14001, and IATF 16949, PMT manufactures precision-engineered, injection-molded plastic components and provides single-source molding from initial customer design to high-volume production. The company has nearly 50 years of experience serving an array of markets, including electrical, telecommunications, medical device, and automotive. Charles A. Sholtis, former owner and CEO of PMT, will stay on as an advisor to the company, said the announcement.
“PMT built a solid foundation as a solutions provider over nearly five decades,” said Sholtis. “I look forward to having the ability to expand our capabilities and capacity as a made-in-USA manufacturer. We have a longstanding reputation as a leading technical injection molder, from our beginnings as a family-founded business in New England to our relocation in 2003 to the US/Mexico border region. We decided to partner with Tide Rock to be able to achieve the next level of growth,” said Sholtis.
Stephen has been with PlasticsToday and its preceding publications Modern Plastics and Injection Molding since 1992, throughout this time based in the Asia Pacific region, including stints in Japan, Australia, and his current location Singapore. His current beat focuses on automotive. Stephen is an avid folding bicycle rider, often taking his bike on overseas business trips, and is a proud dachshund owner.
In addition to the aforementioned companies, Tide Rock’s plastics manufacturing and electro-mechanical contract manufacturing portfolio includes Interconnect Solutions Co. and Plastics Design and Manufacturing.
Replacing highly heat-resistant plastics such as PPS with POM and PP not only reduces material costs but also helps reduce the carbon footprint of materials and energy consumption during molding.
“The acquisition of PMT allows us to expand our footprint within the injection molding sector,” said group CEO Michael Engler. “We now can serve customers from multiple strategic locations, each with a highly skilled workforce and 95 total molding machines ranging from 20 to 500 tons. PMT diversifies our customer base, and also provides the platform for continued growth.”
During the past couple of years, PMT has made considerable investments in its business and, as of September, forecast a double-digit increase in sales in 2021. Last year, it took delivery of 10 new injection molding machines — an outlay of close to $1 million — to support key customers in the telecommunications, medical device, and electrical sectors. In 2020, it expanded its footprint in El Paso by 39,000 square feet for a total of almost 100,000 square feet. The previous year it made a million-dollar investment in new vertical and horizontal presses.
Tide Rock said in the news release announcing the acquisition of PMT that it will continue to actively invest across sub-component manufacturing industries, in addition to other manufacturing, distribution, business services companies.
When the temperature of an LLC is 100°C or lower, general-purpose engineering plastics like POM or PP can be used instead of metals or high-performance engineering plastics. In the case of PP, Polyplastics sees potential for PP-LGF (long glass fiber) instead of short glass fiber to increase strength, dimensional accuracy, and overall performance. It also offers Duracon bG-POM made with biomass as an eco-friendly option.
As the automotive industry moves from traditional ICE vehicles to BEVs, OEMs and part manufacturers are re-imagining the types of materials that can meet the new thermal management needs. Polyplastics believes that less-heat-resistant plastics like POM and PP have significant potential in the manufacture of EV cooling components.
Tide Rock Holdings has added another asset to its plastics manufacturing portfolio with the acquisition of Plastic Molding Technology (PMT). A full-service precision injection molding company located in El Paso, TX, PMT joins Pikes Peak Plastics and Altratek, which the San Diego–based holding company purchased in November 2021, in a new plastics injection molding group that serves the industrial, energy, electronics, medical, telecommunications, and automotive industries.
Editor in chief of PlasticsToday since 2015, Norbert Sparrow has more than 30 years of editorial experience in business-to-business media. He studied journalism at the Centre Universitaire d'Etudes du Journalisme in Strasbourg, France, where he earned a master's degree.
The Polyplastics Group, a global supplier of engineering thermoplastics, has introduced an approach for using less heat-resistant plastics for battery electric vehicle (BEV) cooling components. Polyplastics sees strong potential for plastics such as polyacetal (POM) and polypropylene (PP) for the production of EV cooling components.
Internal combustion engine (ICE) automobiles use a long-life coolant (LLC) that is primarily made of ethylene glycol. The coolant in engines is typically maintained at a temperature of 70° to 100°C but can rise to 120°C or higher if the engine overheats. Therefore, metals or high-heat-resistant plastics like polyphenylene sulfide (PPS) are used in the cooling components and lines.
BEVs do not have engines as heat sources and, therefore, require an LLC temperature of 100°C or lower to cool the battery. This allows for the use of less heat-resistant materials for BEV-specific components.
GETTING A QUOTE WITH LK-MOULD IS FREE AND SIMPLE.
FIND MORE OF OUR SERVICES:
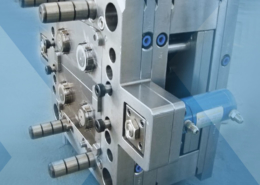
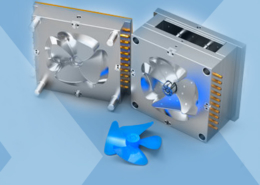
Plastic Molding

Rapid Prototyping
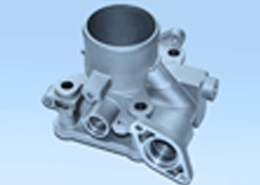
Pressure Die Casting
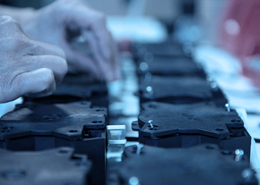
Parts Assembly
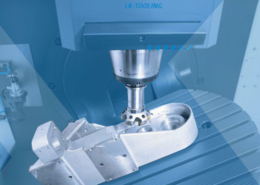