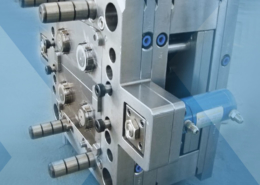
A Quantum Leap for Quality Control in Plastic Injection Molding - molding medica
Author:gly Date: 2024-09-30
Manufacturing four burr-free dental components every 25 seconds, a Sumitomo (SHI) Demag SAM-C5 robot performs the demoulding task. A special end of arm tool uses compressed air to delicately extract and place the dental covers into containers, ensuring hygiene standards are never compromised.
LSR tooling specialist RICO supplies the 256-cavity open tool system. The Elastosil LR 3844/50 material from Wacker Chemie is dispensed via a sophisticated yet compact Industry 4.0-ready LSR eTwin Connect dosing system engineered by another LSR expert - Reinhardt-Technik. This metering and static mixing system guarantees the perfect mixing ratio of two additives, ensuring 99.75% of the LSR material is processed.
On their main stand, the company highlights its multi-cavity LSR processing competence, including OPC-UA interface compatibility, on an all-electric IntElect 180/570-250 injection moulding machine. Visitors to the Reinhardt-Technik booth (Hall A3, Stand 3313) will have the opportunity to view another market where LSR processing is prevalent, the healthcare sector.
Supporting full connectivity, the OPC UA interface facilitates seamless communication between the IntElect machine control and the eTwin Connect dosing system. During every injection cycle, the intuitive, user-friendly multi-touch 15.6 inch HMI capturing all processing documentation, including material pressure, colouring and additive settings, to ensure high-level transparency and traceability.
At Fakuma 2023, visitors will get the opportunity to see Sumitomo (SH) Demag’s LSR processing competence in two live demonstrations.
Although from a long discontinued mobile phone, this flip slider and hinge barrel are two parts which mark a milestone in MIM’s adoption in the consumer electronics sector. This mechanism allowed a clamshell style phone cover to slide up and down and flip open in a single movement.
Thin thin-wall (<1 mm or 0.04 in.) intricate fibre optic connectors housings are often made from 17-4 PH stainless steel. The parts are used in a parallel optical module for ultra-high-speed transceivers in networking and telecom equipment. In addition to the very thin walls, the MIM housing are able to integrate numerous complex details.
To support the high-volume production of individual single wire seals, tooling partner Rico Group reveals its proprietary 256-cavitation LSR mould tool. Combining the direct injection system with double nozzle technology with the IntElect machines optimised clamp force, this LSR package successfully achieves the highest number of cavities in the most compact installation space. The turnkey system coordinates every processing step to efficiently manufacture 256 LSR parts every 15 seconds with minimal flash and material waste. “It’s the definition of high-volume sustainable production,” notes Aliyev.
In this report, Dr Paul A Davies, Sandvik Osprey Ltd, provides an overview of the evolution of the region’s MIM industry from a powder producer’s perspective. With selected application examples and data from the recent APMA 2017 conference, the report offers insights into the drivers for growth and how these have stimulated continued investment in capacity.
The eTwin servo-driven piston pumps save processors up to 80% energy compared to air-driven pumps. While the integrated cooling system and pulsation-free volume flow helps to optimise the filling behaviour and prevent the LSR material from curing too soon. The unit also performs automatic venting, purging air from the material before it is fed into the moulding machine and tool. Combined with the IntElect’s high injection dynamics, the repeatable process ensures the highest component quality is achieved time and time again.
Don't miss any new issue of PIM International, and stay up to date with the latest industry news. Sign up to our fortnightly newsletter.
Discover suppliers of these and more in our advertisers’ index and buyer’s guide, available in the back of PIM International.
Ensuring the material is exposed to a consistent temperature in all 256 cavities, the Rico tool is designed to run on a cold clamping force. This helps to avoid premature curing of the material before every cavity is filled. As a result, it reduces the risk of component and tooling damage, and consequently expensive machine downtime and costly tool repairs.
Reach a truly international audience that includes component manufacturers, end-users, industry suppliers, analysts, researchers and more.
The main Sumitomo (SHI) Demag stand (Hall B1, Stand 1105) features a fully electric IntElect 180/570-250 injection moulding machine equipped with an LSR package comprising a twin dosing system, robotics, and vacuum and venting peripheral equipment. In a cycle time of just 17 seconds, this IntElect LSR package manufactures 256 individual 0.06-gram single wire seals with absolute precision and stability. Despite this high throughput, the IntElect machine’s energy consumption remains one of the lowest on the market.
Few other technologies can compete with Metal Injection Molding’s combination of high volume capability and tight tolerances. This is just one of many MIM applications that can be found in smartphones and mobile devices produced by a wide range of OEMs.
“The market for liquid silicone is growing dynamically, both in terms of applications demanding skills in LSR, as well as volume," observes Rustam Aliyev, the company’s LSR expert and business development director of automotive & electronics.
The ongoing miniaturisation of electronic devices calls for ever smaller parts with better performance at lower cost. This is where Metal Injection Moulding can put forward its strengths.
“Integrating a high precision dosing system with the IntElect machine and the optimal heat balance attained by the Rico dual tip nozzle delivery system ensures unprecedented distribution of the 15 gram shot weight. The result of the high machine dynamics means that part weight accuracy of 0.059 grams is repeatably replicated in the fastest possible cycle time,” explains Aliyev.
The sheer number of small cooling pins in such applications, all packed within a small confined space, maximise the overall surface area and hence optimise thermal efficiency.
Given that each dental article weighs just 0.425 grams, and with an LSR shot weight of just 1.7 grams, the exhibit features Sumitomo (SHI) Demag’s smallest IntElect injection unit. An LSR eTwin Connect from Reinhardt-Technik delivers material to the needle gate nozzle tool. Material is then injected into each of the four cavities twice. Metering data directly connects to the IntElect processing data via OPC-UA, ensuring a fully traceable and stable production process.
Extensive MIM, CIM industry and sinter-based AM industry news, plus the following exclusive deep-dive articles and reports:
LSR is regarded as a unique material, in that it remains flexible and elastic down to -50°C, yet also retains its properties up to 200°C. As a result, LSR is used extensively in electronic components, cables etc. where insulation is required, as well as in medical and healthcare products and the consumer goods sector. To support these markets, in the last five years Sumitomo (SHI) Demag has made significant investments developing an all-electric LSR package that inevitably delivers the cleanliness and precise shot control required to handle this low viscosity material. This year’s Fakuma exhibits demonstrate the company’s advanced proficiency in moulding high-specification LSR components, exclaims Aliyev.
The MIM industry in Asia is the world’s largest, whether considered in terms of number of parts produced, sales turnover or production volume. China alone is reported to offer half of the world’s installed MIM capacity, with production predominantly focused on 3C applications.
Copper coldplates produced by Metal Injection Moulding leverage the full benefits of the MIM process, with shaping capability that gives designers maximum flexibility for innovative design concepts. In this type of pin geometries, which provides optimum thermal performance.
Visitors to the Reinhardt-Technik booth (Hall A3, Stand 3313) will have the opportunity to view the healthcare sector where LSR processing is prevalent. Manufacturing surgical dental protection covers demands a combination of the thinnest walls and thicker beaded geometries. To accomplish this level of 3-dimensional LSR moulding precision, specialists in healthcare applications EMDE MouldTec supplies the gated 4-cavity mould tool, which fits into the generous tool space of the IntElect 75/420-65.
Metal Injection Molding is used to produce Apple’s Lightning connector, a component that is produced in the tens of millions per week at peak production. Such small, complex, high volume components can be produced in multi-cavity molds to net-shape.
The parts were made from 17-4 PH stainless steel and the MIM process allowed very thin walls, overhanging structures and a complex overall design. The parts also demonstrated the high quality polished finish that can be achieved.
Modular by-design, the LSR eTwin Connect allows for quick configuration of programs and instant software upgrades. To support quick drum changes and for ease of maintenance, the system also features a roll in device and automatic drum locks.
The free-to-access PIM International magazine archive offers unparalleled insight into the world of MIM, CIM and sinter-based AM from a commercial and technological perspective through:
The thermal performance of the MIM coldplate therefore bring a competitive edge when compared with other manufacturing processes.
The electronics industry is a major user of Metal Injection Molded parts, resulting in Asia accounting for more than 50% of global MIM parts sales. Smartphone camera housings, buttons, hinges for folding phones, and connectors of complex geometries are now staple MIM products.
GETTING A QUOTE WITH LK-MOULD IS FREE AND SIMPLE.
FIND MORE OF OUR SERVICES:
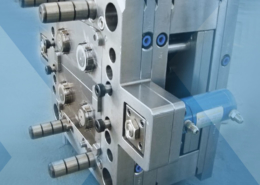
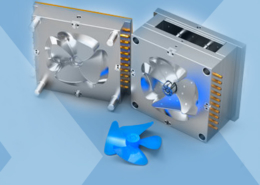
Plastic Molding

Rapid Prototyping
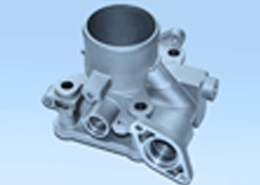
Pressure Die Casting
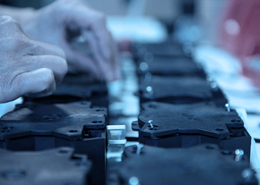
Parts Assembly
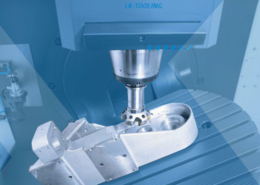