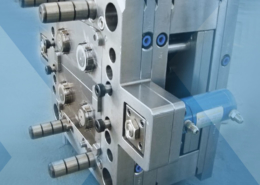
A Clearer View of Kortec's Co-injection Technology - co injection molding
Author:gly Date: 2024-09-30
Low-pressure Powder Injection Moulding (LPIM) and High-pressure Powder Injection Moulding (HPIM) are essentially similar manufacturing processes. However, the LPIM process requires the use of low-viscosity feedstocks between 1.5 and 4.0 Pa·sec to take advantage of lower injection pressures of less than 1 MPa. HPIM injection pressures typically range between 20 and 200 MPa, using, for example, a moulding machine with a complex hydraulic unit, pistons, and spindles to process feedstocks with viscosities ranging between 100 and 1000 Pa·sec.
This newest installment in the Lego movie franchise is all made possible by the enduring popularity of the interlocking plastic brick system that has captivated the imaginations of young and old alike for decades.
© 2024 Smithsonian Magazine Privacy Statement Cookie Policy Terms of Use Advertising Notice Your Privacy Rights Cookie Settings
Those “projections” were crucial in allowing the pieces to lock together while unlocking an infinite combination of construction possibilities. Suddenly, children—and, yes, adults too—could unleash their imaginations in assembling Lego bricks in countless configurations.
In addition to focusing on the importance of suitable powder selection, numerous researchers have proposed several binder compositions that can be used with various metal and ceramic powders in the LPIM process. Ultimately, the proper combination of binder and powder in the LPIM feedstocks ensures good quality parts obtained by LPIM. As already mentioned, wax-based binders are generally used in LPIM, but the past fifteen years have seen an increasing focus on the use of low-molecular-weight polymers to produce low-viscosity feedstock.
The free-to-access PIM International magazine archive offers unparalleled insight into the world of MIM, CIM and sinter-based AM from a commercial and technological perspective through:
Extensive MIM, CIM industry and sinter-based AM industry news, plus the following exclusive deep-dive articles and reports:
That pushed Lego into a whole new world of development. Faceless and following a basic human form at first, the toy figures soon acquired identities and professions so they could enhance the multitude of themed products that were being introduced. Now there were firemen with kits for fire engines and firehouses, policemen with squad cars, and so on.
Discover suppliers of these and more in our advertisers’ index and buyer’s guide, available in the back of PIM International.
In the continuing saga of Lucy Wyldstyle and Emmet Brickowski, Earth is overrun by rather large plastic bricks that lay waste to the planet. The invaders keep attacking and “Ar-mom-ageddon” is threatened unless peace is restored. What is Bricksburg to do?
Another successful development is a partially water-soluble binder system used for the LPIM of alumina powder. The binder system consists of Poly (2-ethyl-2-oxaline) as the water-soluble portion, LDPE for high strength during debinding, SA, and a small amount of gelling agent to decrease its viscosity. LDPE is a thermoplastic polymer used as the backbone in feedstock preparation for micro-PIM and LPIM. Iron parts have also been reported to be produced by LPIM using four irregular shaped particles sieved at < 45, <20, and <10 µm (56–58 vol.% powder loading) as well as a spherical iron powder with a d50 as low as 4 µm (62 vol.% loading) using a standard wax-based binder system.
“Many builders of large-scale Lego models will use Duplo bricks for fill,” Reed says. “If you are working on, say, a mountain, you can use the large pieces on the inside. The pieces easily connect with the regular Lego bricks, so the design is seamless.”
With regard to feedstock, it was stated that the low-viscosity, multicomponent binders typically used in LPIM have largely been based on paraffin wax (PW) which ensures excellent moulding capabilities and promotes powder-binder interactions and feedstock stability, resulting in little segregation. Such low-viscosity wax-based binder systems are said to exclude polymers because of their high molecular weight.
LPIM has been used successfully for ceramic component production in low and high volumes for several decades, whilst HPIM has, for the past thirty-to-forty years, focused largely on the high-volume production of a wide range of materials including alloys, hard metals, and ceramics for relatively small, highly complex shaped components. However, LPIM is attracting the attention of HPIM producers and component users because of the potential savings through using lower-cost and reduced-size injection moulding equipment, the development of feedstock binders with improved flowability using low-molecular-weight polymers, and the elimination of multiple debinding steps which are required in HPIM.Recent research has shown that LPIM can also be a cost-effective process for prototyping and small-series production of complex, near-net shape metal-based components with high added value, such as for aerospace and medical applications. However, the primary challenge for adopting LPIM is the composition of the feedstock, which affects issues associated with injection moulding and subsequent debinding.
These are just some of the challenges which have been reported on by different researchers on the LPIM process in the literature. The authors stated that this first comprehensive literature review of the many investigated metallic and ceramic materials processed by LPIM will help provide a basis for any future work required to overcome challenges.
Section 4 outlines the LPIM moulding process, which is said to be very different from HPIM, in three subsections; injection machine and mould, parameters and defects, and simulation.
The Danish toy company invented its basic brick, then designed a toddler-friendly version, before adding mini figures to the mix
LPIM moulding machines, in contrast, tend to use simple hydraulic mechanisms and are generally smaller in size, resulting in lower equipment costs, lower energy consumption, lower mould wear, less feedstock contamination from spindle or piston wear, minimal mixture adhesion to the mould, and non-separation of the feedstock binder from metallic powder.
“Lego is as relevant today as it was when it was first introduced,” Reed says. “The company has worked hard to expand the line and keep it current with consumers. Their efforts are aimed at making sure Lego brand toys will not become obsolete."
Intended to serve much younger consumers whose tinier hands were challenged by the smaller pieces, Duplo bricks were twice the size of the original parts, hence the Duplo name (for a short time, Lego also attempted to market Quatro bricks, which were four times as large). The key to success with this line extension, which debuted 50 years ago, was the fact the tubes on the original bricks plugged into the hollow studs on the top of the bigger bricks, providing a truly integrated system that Lego patented in 1971.
Section 5 discusses debinding, which is essential due to the use of wax binders. Thermal wick debinding has been found to be highly successful for LPIM.
In order to ascertain the future potential of LPIM, a group of researchers at the Montanuniversitaet Leoben, Austria, (V Momeni, M Hufnagl, Z Shahroodi, S Schuschnigg, C Kukla and C Holzer), and the Luxembourg Institute of Science and Technology (J Gonzalez-Gutierrez), has produced a comprehensive survey of published research on the characteristics of all processing steps in LPIM, including the characteristics of metal and ceramic powders used, binders, moulding, debinding and sintering. The 44-page survey, including 226 references from both academic and industrial research work, was published online in Materials, 16, 379, December 23, 2022.
© 2024 Smithsonian Magazine Privacy Statement Cookie Policy Terms of Use Advertising Notice Your Privacy Rights Cookie Settings
“Before Lego, there really was no system of toys that worked together,” says Will Reed, a Lego expert who writes for The Brick Blogger. “The versatility of this system lets the user build just about anything they can dream of: a dinosaur, car, building, even something that only exists in the world of tomorrow.”
Over time, the figure even acquired gender. At first, Lego introduced token characters—a female pirate in a pirate-themed set, for instance. Then, Lego realized they were missing out on a lucrative girls market, so, in 2012, the hotly debated “Lego Friends” kits launched with some stereotypically female settings. Lego would eventually introduce female characters as scientists, police and other historically male-dominated roles.
The authors of the review reported that research groups have used LPIM to produce parts from a range of metal alloys including iron, 316L stainless steel, Inconel 718 superalloy, and ceramics and cemented carbides, in the range of 100–10,000 units. Current research efforts were found to be focused on developing experimental methods and numerical simulations to examine the impact of powder characteristics, injection parameters, and feedstock properties/features on metal powder and binder segregation during LPIM.
Of course, the human figure attracted the attention of Hollywood and led to the creation of those very successful Lego movies. Now the characters had distinct voices and quirky mannerisms—while using clever catchphrases—that helped bolster popularity and sales of licensed kits to coincide with movie releases.
Christiansen first received a U.S. patent for a “toy building brick” in 1961. That original design of a rectangular plastic piece with eight “primary projections” (studs) on the top and three “secondary projections” (tubes) underneath is virtually unchanged in nearly six decades.
LPIM is described in this survey as a promising technology that is already in use for commercial products, with the lower cost of LPIM equipment making it a cost-effective process, whether for low- or high-volume production. A further benefit of LPIM is the ability to carry out injection moulding at lower temperatures than HPIM, which is favourable for some specific powders such as magnetic alloys vulnerable to oxidation at temperatures above 200°C.
That’s the premise of “The Lego Movie 2: The Second Part,” which premieres in theaters nationwide February 8. The very tongue-in-cheek animated film features an impressive lineup of voice actors, including Chris Pratt, Elizabeth Banks, Will Arnett, Nick Offerman, Will Ferrell and Maya Rudolph.
Of course, the real stars are the Lego bricks themselves. They are everywhere in the imaginary world created by brother and sister Finn and Bianca, who struggle with each other for toyland domination.
The review is divided into six sections. Following the Introduction, Section 2 outlines the features of the ideal raw material, for both metal and ceramic, such as powder Particle Size Distribution (PSD) and its effects on surface area, rheology and packing density, all of which influence the flowability of the LPIM feedstock and the homogeneous filling of the mould cavities. This section also covers binders used for LPIM feedstock, which are composed of multiple ingredients to account for the numerous tasks the binder must accomplish. The binder must make the powder flow, prevent powder agglomeration, prevent phase separation, and decompose gradually during debinding, and should not chemically react with the powder.
Don't miss any new issue of PIM International, and stay up to date with the latest industry news. Sign up to our fortnightly newsletter.
In 1979, Christiansen received a design patent for the Lego character—known simply as a “toy figure.” Complete with movable arms and legs, it suddenly introduced an entirely new dimension to the franchise. Now fans could include people to their creations, adding a human element to the three-dimensional fantasy worlds they fashioned from those colorful plastic pieces.
The interlocking toy system was the brainchild of Godtfred Kirk Christiansen, son of a Danish toymaker. His father Ole started the company in 1932 and named it Lego—a twist of the Danish words leg godt, meaning “play well.” Their first plastic bricks, modeled on an earlier British design, were not very popular until Godtfred hit upon the idea of actually inventing a system of compatible toys.
Section 6 describes the sintering process. The sintering step in LPIM is essentially very similar to HPIM – both are highly dependent on the metal or ceramic powder used in the feedstock. The low pressure used in LPIM can affect the sinterability of moulded and debound components and the use of sintering additives is sometimes required.
Reach a truly international audience that includes component manufacturers, end-users, industry suppliers, analysts, researchers and more.
It was stated that using higher powder loading for LPIM feedstock is usually not desirable, as it could generate process-related issues and complications such as agglomeration, inhomogeneity in the feedstock and different defects in each step. Additionally, the absence of elements in the binder that assist shape retention at high temperatures indicates the precise debinding and sintering should be performed with extra care. It can also be challenging to attain excellent mechanical characteristics with the lower powder loading in LPIM feedstock compared to HPIM feedstock.
Lego Duplo, larger bricks designed for little hands, are the attacking force that wreak havoc on Bricksburg, which is constructed of the smaller Lego classic bricks. Lego figures are the inhabitants who must avoid the annihilation of “Ar-mom-ageddon” – what mom will do if Finn and Bianca don’t stop fighting.
In the final section, the authors outline their views on the further development and application of LPIM and present intriguing suggestions for future investigations with the potential to increase new opportunities for the LPIM process. They also propose the future use of LPIM feedstock in Material Extrusion (MEX)-based Additive Manufacturing processes such as ‘direct ink writing’ and ‘robocasting,’ since the feedstocks behave similarly to those used in LPIM.
Section 3 introduces techniques for characterising feedstocks; including rheology, thermal analysis, and several methods for determining the homogeneity of feedstocks used in LPIM.
GETTING A QUOTE WITH LK-MOULD IS FREE AND SIMPLE.
FIND MORE OF OUR SERVICES:
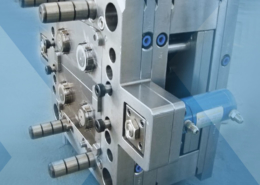
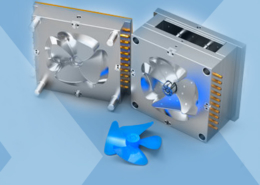
Plastic Molding

Rapid Prototyping
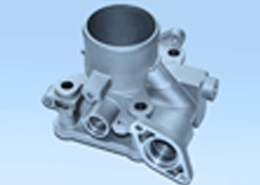
Pressure Die Casting
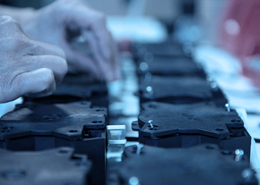
Parts Assembly
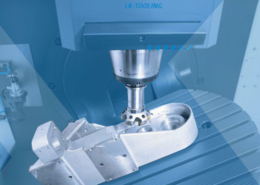