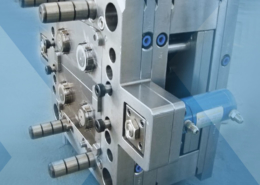
3D-printed Injection Molds Save Medical Device OEMs Time and Money - prototype p
Author:gly Date: 2024-09-30
Some of the German group’s key OEMs customers include Daimler, BMW, VW Group, and the Stellantis Group as well as industrial clients such as Schüco.
European researchers claim to have successfully demonstrated the embedment of organic PV (OPV) modules into structural plastic parts via large-scale industrial injection molding (IM).
Creative's customer base of blue-chip tier-1 suppliers for the North American automotive industry complements Meteor’s customer base of automotive OEMs, it also noted.
The researchers first created modules in roll-to-roll printing, using a photoactive blend known as P3HT:O-IDTBR. This blend was chosen due to its morphological and thermal stability, which are relevant to the later injection molding process.
“This acquisition will enable us to serve our renowned US customer base with a broader technology focus,” explained Robert Roiger, CEO of the Meteor Group.
As for mechanical and operational stability, the scientists found an average of more than 35% increase in the maximum stress point in the IM-OPV samples. The first fracture on the control devices occurred at 10–30% of strain, whereas this value jumped up to 70–150% on the IM-OPV modules. In addition, a power conversion efficiency retention of more than 90% was found after 50,000 cycles in the molded modules.
“From the selection of 64 roll-to-roll printed modules, 32 of them were injected, and the other 32 modules were kept as references,” the researchers explained. “On average, the IM-OPV modules retained 98.1 of the original performance. Only 2 samples failed, and 28 samples preserved over 90% of the original performance, which sets the yield of the IM process close to 90%.”
Headquartered in Tipp City, Ohio, Creative has more than 40 years of experience in custom plastics and rubber profile extrusion and injection moulding, said a 30 Nov Meteor statement.
With 2020 sales of $180 million (€158 million), Meteor operates from locations in Germany, the US, and Romania – specialising particularly in the manufacture of elastomer seals and sealing systems for automotive and industrial markets.
IM is a manufacturing technique for producing parts by injecting molten material into a mold and has the ability, according to the research group, to enable the development of in-mold plastic solar cells with improved performance and stability.
“With the acquisition, Meteor will be able to offer its clients a comprehensive portfolio of rubber and plastic sealing solutions,” according to the German manufacturer.
A French-Spanish research team developed organic photovoltaic modules embedded into plastic parts through high throughput injection molding. The researchers injected thermoplastic polyurethane in the modules and found it enhances their mechanical stability while keeping a high flexibility.
Bockenem, Germany – Meteor Group has acquired US-based profiles manufacturer Creative Extruded Products, the German engineered rubber products company has announced.
In particular, Creative will add key know-how and technology in thermoplastic products such as PVC, ABS and polycarbonate, as well as thermoplastic rubber (TPR) and thermoplastic vulcanisates (TPVs), said Meteor.
Their findings were introduced in the paper “Injection Molding Plastic Solar Cells,” published in Advanced Science. The researchers come from the Eurecat Technology Centre of Catalonia, the University of Pardubice and the Centre for Organic Chemistry in the Czech Republic, as well as from French nano-metal producer GenesInk and Spanish injection molding provider Aitiip.
The addition will also reinforce Meteor’s “already strong” portfolio of EPDM rubber for both dense and sponge materials, the Bockenem-based group added.
This content is protected by copyright and may not be reused. If you want to cooperate with us and would like to reuse some of our content, please contact: editors@pv-magazine.com.
Meteor expects the acquisition to expand its technological capabilities and solidify its presence in North America, as the two entities “have a substantial product and customer complementarity.”
“Due to their very thin layout, flexible solar cells can be sensitive to mechanical abrasiveness and, therefore, might require additional protection and integration strategies,” the research group explained. “Embedding a printed solar module into a plastic part simplifies integration challenges, while providing additional mechanical protection, shape adaptability, and streamlined contacts for connections.”
Featured Articles Tire & rubber machinery sector bounces back 09 June 2024 A roadmap for AI in the tire industry 07 June 2024
“This work represents the first demonstration of in-mold plastic solar cells and opens new possibilities for organic photovoltaics to enable specific applications that require simultaneous high optoelectronic and structural performances,” the researchers said. “We believe that future focus on injection plastic materials could further extend the benefits of in-mold photovoltaics in regards to structural and device stability, or even providing additional optical functionalities.”
You may revoke this consent at any time with effect for the future, in which case your personal data will be deleted immediately. Otherwise, your data will be deleted if pv magazine has processed your request or the purpose of data storage is fulfilled.
Your personal data will only be disclosed or otherwise transmitted to third parties for the purposes of spam filtering or if this is necessary for technical maintenance of the website. Any other transfer to third parties will not take place unless this is justified on the basis of applicable data protection regulations or if pv magazine is legally obliged to do so.
The scientists inserted the modules horizontally into an injection mold of polyether copolymer-based thermoplastic polyurethane. This material was chosen due to its low process temperature, broad substrate compatibility, and flexibility. The injection was done using a 120 mm × 120 mm × 2 mm cavity insert, at a 90 mm −1s speed.
The cookie settings on this website are set to "allow cookies" to give you the best browsing experience possible. If you continue to use this website without changing your cookie settings or you click "Accept" below then you are consenting to this.
“OPV product development demands photovoltaic materials with high morphological stability under thermal stress, such as the P3HT:O-IDTBR blend,” the academics emphasize. “In that respect, higher performing materials with such stability are urgently needed.”
GETTING A QUOTE WITH LK-MOULD IS FREE AND SIMPLE.
FIND MORE OF OUR SERVICES:
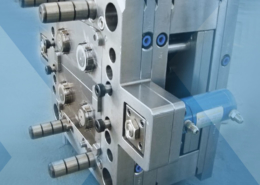
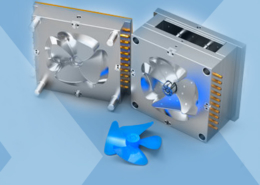
Plastic Molding

Rapid Prototyping
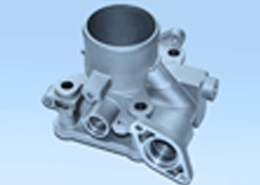
Pressure Die Casting
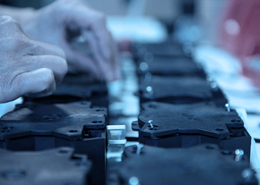
Parts Assembly
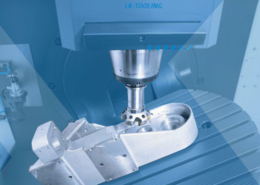