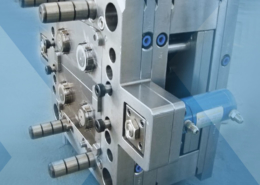
3D-printed Injection Molds Save Medical Device OEMs Time and Money - plastic inj
Author:gly Date: 2024-09-30
Avient’s portfolio of Gravi-Tech materials combine the aesthetics of metals with the processability of polypropylene (PP), acrylic butadiene styrene (ABS), polyamide (PA), polybutylene terephthalate (PBT), polyphenylene sulfide (PPS), and other thermoplastic materials. These materials are currently manufactured in Asia and are available globally.
Omega Plastics Group, an integrated plastic injection moulding group has announced the addition of new injection moulding press capacity at both Signal Plastics and Omega Plastics.
The trial cell offers a dedicated area for comprehensive testing, allowing for analysis of key characteristics such as fill patterns, thermal imaging, gate freeze studies, cycle time efficiencies, and their direct influence on final product quality. By introducing this dedicated trial resource, Omega Plastics can support customers by providing insights and expert validation of tooling solutions.
During that time investments have also been made in the toolroom, including the acquisition of a Puma GT 2100 CNC Lathe, a new surface grinder, an Agie Carmilles EDM drill and a Fanuc ROBOCUT wire EDM, as well as in metrology software and capabilities. These investments allows Omega Plastics to aim to consistently meet customer demands and provide cutting-edge tooling solutions.
New high-impact polypropylene (PP) grades, part of Avient’s Gravi-Tech density-modified portfolio of materials, are designed to replace die-cast or machined metals in premium-brand applications. They replicate the look and weighted feel of metal, including enhanced metallic surface finishes and handles, for personal, oral, skin, and cosmetic products.
The trial cell is equipped with two injection moulding machines, including a 40-tonne machine and a 100-tonne machine. This dedicated resource ensures optimal flexibility and precision during tooling validation processes, enhancing the overall customer experience.
Over the past five years, the group has added seven additional injection moulding machines, significantly expanding its injection moulding machine capacity from 23 to 30 machines, ranging from 40T to 1,300T. Further significant investments have been made in warehousing, and material handling systems to support the additional moulding capacity.
These recent investments in additional injection moulding capacity and dedicated tooling resources are part of Omega Plastics Group's ongoing commitment to continuous improvement and customer satisfaction.
In addition to the press expansion, Omega Plastics based in Gateshead, has established a dedicated tool trial cell to support its UK toolroom and in-house tool manufacture, operating independently of planned production activities. This specialised validation facility enables Omega Plastics to test and validate new tools without any impact on ongoing production processes.
Signal Plastics, based in Washington, has recently acquired a state-of-the-art Yizumi 700-tonne injection moulding press. This strategic acquisition aims to bolster production capabilities and meet the increasing demand from an existing customer as part of their production ramp-up. Equipped with a Sepro robot for demoulding and a conveyor belt to enhance productivity, the new 700-tonne press will significantly contribute to meeting customer requirements efficiently and effectively.
A cost-effective alternative to metal, the new formulations pass strict drop test requirements and provide excellent low-temperature impact performance, according to Avient. The materials’ flowability, combined with injection and impact strength, make them a good fit for complex, thin-wall moldings while also providing design and processing freedom. In addition to pre-colored options and application-specific surface effects, the new Gravi-Tech materials are available in special grades for vacuum metallization.
Across the wide press range, Omega Plastics Group can produce components with shot weights ranging from less than 1g to 4kg. The group has capability to mould complex technical hand loads and overmoulds through to fully automated robot demoulding with integrated conveyor systems.
“We identified a growing need for high-density injection molding solutions that will help brand owners, designers, and manufacturers create weighted premium products with more complex designs than possible when using metals, while simultaneously meeting higher demands on impact strength,” said Matt Mitchell, Director of Global Marketing, Specialty Engineered Materials. “Our new high-impact Gravi-Tech formulations can be customized to be as light as plastic or up to four times as heavy as aluminum with excellent weight distribution. As injection molding materials with good flowability, they deliver finished components in one single process step, helping to facilitate easy assembly.”
The ability to mold finished weighted components without requiring further assembly and post-treatment saves energy, which can then reduce the carbon footprint of end products, said Avient. Moreover, molded-in colors eliminate the release of potentially hazardous volatile organic compounds (VOCs) associated with painting.
Peter Sayer, group commercial director at Omega Plastics Group, said: "At Omega Plastics Group, our mission is to provide high-quality plastic injection mould tooling, components, assembly, and technical solutions on time and with exceptional customer service. These recent expansions and investments in our capabilities and resources demonstrate our commitment to our customers, ensuring we continue to exceed their expectations and deliver innovative solutions."
GETTING A QUOTE WITH LK-MOULD IS FREE AND SIMPLE.
FIND MORE OF OUR SERVICES:
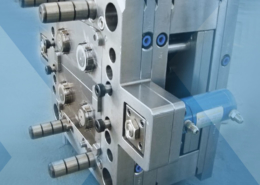
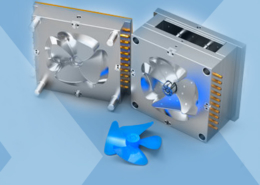
Plastic Molding

Rapid Prototyping
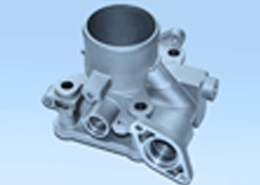
Pressure Die Casting
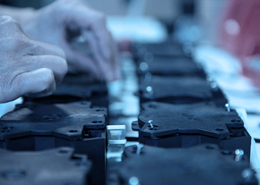
Parts Assembly
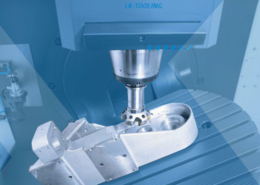