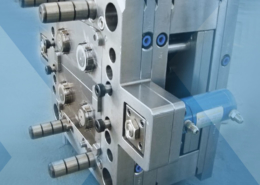
3D-printed Injection Molds Save Medical Device OEMs Time and Money - injection m
Author:gly Date: 2024-09-30
A project to convert passenger jets to cargo planes during the Covid pandemic, using thermoplastic window plugs instead of metal, will be on display at KraussMaffei’s booth at NPE2024 in Orlando, FL, from May 6 to 10.
KraussMaffei “has not only set up a machine with multiple capabilities, but has also been actively helping us on-site with process development,” said Dr. Waruna Seneviratne, director NIAR Atlas. “Our students also gain a tremendous amount of hands-on experience and get to interact with the supply chain for several new capabilities we introduced in recent years. Our goal is to transfer the efficient processes such as FiberForm from automotive production to aviation.”
At NPE, the injection molding machine maker will display thermoplastic window plugs for cargo planes developed in partnership with the National Institute for Aviation Research.
The new grades use Elix Polymers base polymers: standard ABS, high-heat ABS, ABS/PC or PC/ABS – and because their key properties remain the same, this does not affect existing OEM approvals of Elix grades. Furthermore, as the shrinkage of the materials stays the same, current molds can be used without further need for modifications.
Stephen has been with PlasticsToday and its preceding publications Modern Plastics and Injection Molding since 1992, throughout this time based in the Asia Pacific region, including stints in Japan, Australia, and his current location Singapore. His current beat focuses on automotive. Stephen is an avid folding bicycle rider, often taking his bike on overseas business trips, and is a proud dachshund owner.
The project is the subject of a technical paper, “Ultra-High-Rate Manufacturing of Thermoplastic Window Plug Using Hybrid Overmolding,” which won first place in the outstanding technical paper awards at the SAMPE 2024 advanced materials and process engineering conference and exhibition.
Elix Polymers (Tarragona, Spain) has developed a range of specialty grades of acrylonitrile-styrene-butadiene (ABS) and polycarbonate (PC)/ABS to reduce the squeak that is generated when plastic parts come into contact with other plastic parts, leather, PVC foil, or other products. These undesirable noises can negatively affect the driver’s comfort and the car’s quality impression.
Typical critical automotive interior parts affected include door handles, seating parts, cup holders, and air vents. The newly developed grades may also be suited for other segments such as E&E, white goods, or consumer goods.
Mr. Herter added: “This new development is the result of our close partnership with leading OEMs. Together, we identified the need to address this issue and we were able to develop tailor-made solutions. This approach is fully in line with our strategy to focus on specialty added-value materials.”
The new grades underwent stick-slip tests at several premium automotive OEMs according to the VDA230-206 standard using testing machines from Ziegler Instruments, with very positive test results: a 10-point scale is used where 10 is the highest risk level. The new Elix grades managed toscore 1 – the lowest risk level. Tests were conducted with different forces (10 N, 40 N) and speeds (1 mm/s and 4 mm/s) at several temperatures.
According to Fabian Herter, Industry Manager Automotive at Elix Polymers, with these new grades, significant cost savings are possible: “Until now, in many instances, fabrics or grease had to be added afterwards to reduce squeak and rattle. However, this involves additional costs and manual labor – and therefore is not ideal. Now, thanks to these new Elix grades, we are able to offer a more competitive solution when compared to other resins that are currently available.”
Geoff Giordano is a tech journalist with more than 30 years’ experience in all facets of publishing. He has reported extensively on the gamut of plastics manufacturing technologies and issues, including 3D printing materials and methods; injection, blow, micro and rotomolding; additives, colorants and nanomodifiers; blown and cast films; packaging; thermoforming; tooling; ancillary equipment; and the circular economy. Contact him at [email protected].
Designed with the same oval geometry as the metal plugs, the thermoplastic replacements featured ribs added to increase stiffness that could withstand cabin pressure. In this case, the 16-ply organosheet was made of LM-PAEK reinforced with AS4 carbon fibers; the overmolded ribs were made of 30% chopped-fiber-filled PEEK. The final plugs were produced on a GXW 450-2000/1400 injection molding machine with a swivel platen.
The two-year partnership between KraussMaffei and the National Institute for Aviation Research (NIAR) at Wichita State University used KraussMaffei’s FiberForm technology to produce a 20% lighter alternative to the previous 590-gram metal plugs.
Next, the NIAR team is working toward further weight reduction, making the thermoplastic plugs 40% lighter than the metal parts. And, NIAR is performing further tests to certify the plugs for series production — informed by KraussMaffei’s experience in high-production automotive applications.
In the FiberForm process, a fully consolidated fiber-reinforced thermoplastic sheet, called organosheet, is inserted into the forming tool and overmolded with a thermoplastic.
Using this process, 40 window plugs can be produced in an hour, thanks to the shorter cycle time of fast injection molding vs. metal machining. And, the thermoplastics used in the FiberForm process allow for the welding of components, in addition to demonstrating high impact strength, resistance to high temperatures and chemicals, and flame retardance.
GETTING A QUOTE WITH LK-MOULD IS FREE AND SIMPLE.
FIND MORE OF OUR SERVICES:
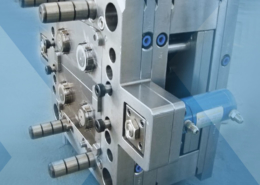
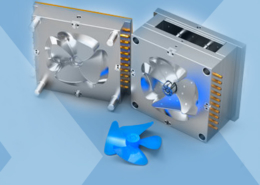
Plastic Molding

Rapid Prototyping
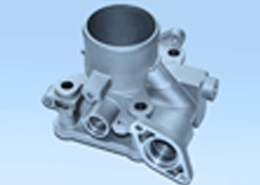
Pressure Die Casting
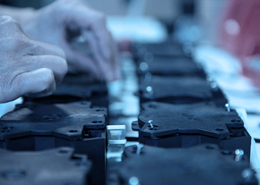
Parts Assembly
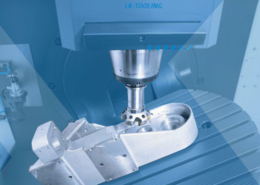