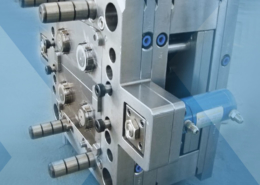
3D Printing—An Alternative to Injection Molding - low volume injection molding c
Author:gly Date: 2024-09-30
ColorStream works with all injection moulding, extrusion, and blow moulding machines and with all virgin resins, including PET. Visitors to Plastrac’s K show booth (Hall 10, Stand A01) will be able to see it in action.
Plastrac is thus ready to roll out the new blender, which began life as a customer service request by a major cable and wire manufacturer to eliminate the need for employees to climb ladders or stairs to clean and change out additive hoppers that are mounted high above the floor.
The $10-million, 121,000-square-foot expansion will be followed by the addition of more manufacturing space, slated to begin in the spring of 2022.
While Plastrac, a US-based manufacturer of blending systems, has been field testing its ergonomic ColorStream blending system, the US Patent Office has awarded the new unit patent approval.
The expansions follow a $20-million investment in the MGS Healthcare Center of Excellence in 2019. The center includes a 13,000-square-foot Class 8 cleanroom.
Colour changes and minimal maintenance occur on the plant floor. The cart can also be moved easily to ensure unhindered access to injection moulding machines and extruders when their maintenance is due. ColorStream’s low pressure transport air ensures there is nothing to clog and very little to clean.
“During a tumultuous year, our business has been very strong, particularly in healthcare, and we are expecting double-digit growth in 2021,” said MGS President Paul Manley. “Additional demand is driving the need for our expansions, and the operational and logistical improvements we are making will better service our customers.”
ColorStream’s cart can support, up to four additive feeders with the small footprint as a cart with one feeder, arranged radially around a collecting funnel for discharge of the additives into a vertically mounted, custom-made venturi that discharges downward into a transport hose.
Until she retired in September 2021, Clare Goldsberry reported on the plastics industry for more than 30 years. In addition to the 10,000+ articles she has written, by her own estimation, she is the author of several books, including The Business of Injection Molding: How to succeed as a custom molder and Purchasing Injection Molds: A buyers guide. Goldsberry is a member of the Plastics Pioneers Association. She reflected on her long career in "Time to Say Good-Bye."
At the upper end of the system, a compact but sturdy baffle box mounts to the feed throat of the plastics processing machine. The top flange of this box typically supports the customer’s central loader receiver and buffer hopper, which supply virgin material to the process. A cyclone-type receiver inside the baffle box separates the additives from the transport air, which is routed out of the baffle box laterally. A metal screen between the cyclone and the exhaust duct guarantees that stray additive granules cannot escape with exhaust air.
Plastrac President Ken Bullivant explained: “Our response was to develop an entirely new approach to the industry’s traditional blending methods. We successfully decoupled dosing and feed from the main resin, moving blending to the plant floor and streaming colours and other additives to the feed throat of injection moulding machines and extruders to mix synchronously with virgin resin in real time.”
Its blowers operate continuously for years, according to a press release, and deliver clean air because there are no contacting parts requiring lubrication. The venturi and transport hose are small enough to deliver sufficient air velocity to keep transported granules entrained in the air stream.
MGS recently broke ground on a 121,000-square-foot expansion at its headquarters campus in Germantown, WI. The additional space will be used by the vertically integrated supplier of manufacturing services for warehousing operations that are currently located at a rented facility in Oak Creek, about 35 miles southeast of Germantown. The $10-million expansion will bring the total size of the campus to approximately 380,000 square feet.
MGS is also planning a second expansion to its headquarters that will include 118,000 square feet of manufacturing space. Expected to begin in the spring of 2022, the $15-million expansion will consolidate MGS’s capabilities at its Germantown location, enhancing cross-functional collaboration, driving innovation, and improving speed to market, said the company.
GETTING A QUOTE WITH LK-MOULD IS FREE AND SIMPLE.
FIND MORE OF OUR SERVICES:
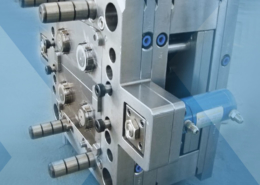
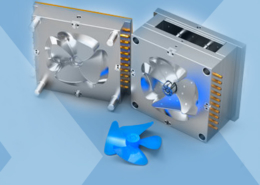
Plastic Molding

Rapid Prototyping
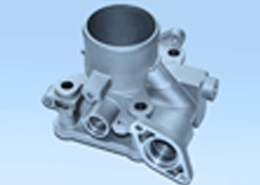
Pressure Die Casting
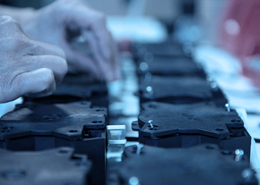
Parts Assembly
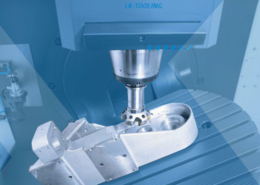