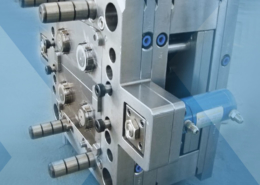
3D Printing Patterns, Cores & Molds for Casting Metal - plastic casting molds
Author:gly Date: 2024-09-30
Paragon possesses a 19,000-sq. ft. tool fabrication facility and a 24,000-sq. ft. tryout/part run facility in Fraser, Michigan.
Wittmann Battenfeld will demonstrate its latest injection moulding technology at Compamed, the international medical technologies fair in Düsseldorf on 13–16 November
“This acquisition expands our North American capabilities and footprint allowing us to better serve our customers,” says Brueckner Group USA's President Steven D. Hoenig. “With the addition of Paragon's locally manufactured tools and support, the Kiefel division of Brueckner Group USA will be able to offer a complete manufacturing solution for the important North American market.”
The machine on display comes as a full-fledged cleanroom production cell, equipped with a rotary table, parts removal handling device, integrated quality inspection by image processing, as well as a cleanroom module, which produces class 6 clean air according to the ISO 14644-1 standard. The parts are all injected, quality-inspected and deposited inside the cleanroom.
At the Compamed in Düsseldorf, the company will demonstrate its competence in medical technology by producing a micro filter made of POM with an 80 μm grid and a part weight of 1.1 mg, which can be used in micro pumps or inhalators. The micro filter will be manufactured on a MicroPower 15/10 with a clamping force of 150 kN. It is produced in a 2-cavity mould with 3-platen injection.
David M. Smoger and Daniel V. Smoger, former Owners of Paragon will take on roles of Vice President Operations and Vice President Tooling of the Kiefel Automotive Division of Brueckner Group USA and will be responsible for all Kiefel automotive activities for the NAFTA market.
The encasement of MicroPower machines also provides sufficient space for the integration of various equipment options, such as a rotary table, robot, material dryers or temperature controllers. All drive modules of the all-electric drive system including all mechanical components are encapsulated in easy-to-clean housings.
Cleanroom Technology keeps decision-makers worldwide updated on contamination control via digital, live, and print platforms. Our articles span the cleanroom lifecycle, from design to maintenance, including monitoring and compliance. Editors deliver breaking news, product launches, and innovations, and also commission exclusives on technical trends from industry experts
Stephen has been with PlasticsToday and its preceding publications Modern Plastics and Injection Molding since 1992, throughout this time based in the Asia Pacific region, including stints in Japan, Australia, and his current location Singapore. His current beat focuses on automotive. Stephen is an avid folding bicycle rider, often taking his bike on overseas business trips, and is a proud dachshund owner.
Brückner Group USA acquired Paragon Molds Corporation on January 1, 2017 in order to increase the automotive business of its affiliate Kiefel in the US market. With headquarters in Fraser, Michigan Paragon has served many well-known suppliers to the US automotive industry since 1973.
“In 2016 the [Kiefel] Automotive Technology Center in Livonia, MI, commenced operation. Besides laboratory facilities for laminating and punching there is also a milling robot cell and the equipment for prototype and pre-series products at our customers’ disposal”, says Kiefel’s CEO Thomas J. Halletz. “Paragon, along with the technology center, will raise Kiefel’s operations in the USA to a new level and will significantly increase the market presence.”
This applies in particular to the MicroPower, which has been specially developed for manufacturing micro parts. This all-electric machine model, designed as a completely enclosed inner cell, is ideally suited for production under cleanroom conditions by the very nature of its design.
Paragon has 33 employees and develops and manufactures tools for the production of automotive interior components such as door panels, instrument panels and center consoles using a lamination process, as well as tools for foamed and back-foamed components.
Headquartered in Vienna, Austria, Wittmann Battenfeld designs injection moulding machines to a minimum emissions level making them especially suited to medical technology injection moulding.
GETTING A QUOTE WITH LK-MOULD IS FREE AND SIMPLE.
FIND MORE OF OUR SERVICES:
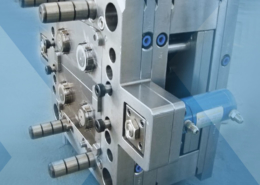
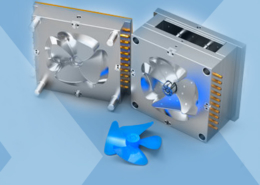
Plastic Molding

Rapid Prototyping
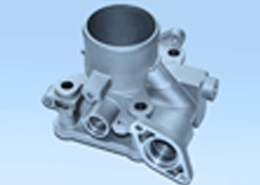
Pressure Die Casting
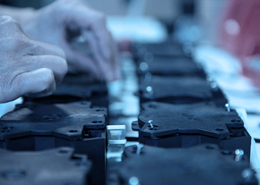
Parts Assembly
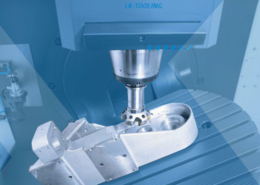