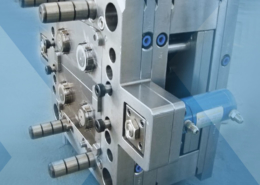
3D printing has a plastic problem - plastic part manufacturer
Author:gly Date: 2024-09-30
In general, structural foam molding requires less energy and raw material, and uses lower clamping forces, than conventional injection molding. The dissolved blowing agent improves flowability of the molten plastic. In addition, the foam molding pressure, which is independent of the location, enables molding of thicker ribs. These effects can be used to reduce wall thickness, which has a positive effect on the required cooling time and, in turn, on the cycle time.
We keep our content available to everyone. Consider supporting Science X's mission by getting a premium account.
Engel is improving the cost effectiveness of structural foam molding with its new e-foam XL gas supply units that support multiple production cells.
Further, the combination of new system technology by Engel and MicroJect Advanced leverages unprecedented efficiency and sustainability potential in structural foam molding, according to Engel. Structural foam molded parts no longer need to be painted, and there is no need for additional energy-intensive process technology, such as intermittent mold heating, for parts in customer-facing applications.
Molding is a popular method for the mass production of objects. Essentially, two (or more) mold pieces are conjoined, leaving the shape of the desired object as a cavity. During fabrication, a fluid is introduced into this cavity and is allowed to harden. Once the fluid has solidified, the pieces of the mold are removed, leaving behind the molded object. While the process is fairly simple, creating the mold to produce an object is extremely difficult, and a multitude of considerations go into its creation. How should the object be oriented and divided to ensure that the pieces of the mold can be removed? If the finished object is hollow, how should it be decomposed into pieces? Figures with loops or holes add further complications, as do aesthetic considerations, such as avoiding a parting line through a face. In mass fabrication, the high costs of the initial mold design are offset by the low per-unit cost of production. For a small-scale designer, however, or a novice interested in experimenting with injection molds, hiring a professional mold designer is impractical, and creating the molds unaided is infeasible. Similarly, 3-D-printing the desired number of objects would be far too time- and resource-intensive.
Together with Tier 1 supplier Faurecia, Engel is demonstrating the potential of structural foam molding technology at its K booth. Sample parts with a sophisticated surface structure are being produced on an Engel duo 1000 injection molding machine. The new MicroJect Advanced process developed by Faurecia Interiors (Hagenbach, Germany) and Eschmann Textures International (Gummersbach, Germany) is being used in this application. The process makes it possible to produce lightweight, visible components with a high-quality Class A surface using only structural foam molding.
The team has already tested some of their molds at an injection-mold factory near Linz. "The factory employees were surprised at how easy it was to extract the finished objects, as well as how durable the 3-D-printed molds were. Even after creating a hundred objects, the molds were still working," says Auzinger. The team already has further improvements in mind. One idea is the inclusion of connectors that snap together to ease the final assembly of the object.
CoreCavity, a new interactive design tool, solves this problem, and allows users to quickly and easily design molds for creating hollow, free-form objects. Created by Kazutaka Nakashima, a Ph.D. student at the University of Tokyo visiting IST Austria, Thomas Auzinger (IST Austria), Emmanuel Iarussi (CONICET, IST Austria), Ran Zhang (IST Austria), Takeo Igarashi (University of Tokyo), and Bernd Bickel (IST Austria), this software tool opens up opportunities for small businesses and enthusiasts. The software analyzes a 3-D scan of the object, and creates a "thin shell," essentially a hollow version of the object, in which particularly small gaps are considered solid—another of the team's innovations. The software then proposes a decomposition of the object into pieces; each piece is created by one mold, then joined together at the end. Moreover, the program is able to suggest slight modifications to the original design, for instance, to eliminate tiny hooks that might complicate unmolding. "Previous tools were unable to suggest such changes," says Thomas Auzinger, a postdoc at IST Austria. The user can adjust the decomposition simply by clicking, and choose to accept or reject any proposed modifications. When the user is satisfied, the software automatically produces the mold templates, which can then be 3-D-printed and used for molding.
Whereas each injection molding machine previously required its own gas supply, Engel now offers the e-foam XL multi, a central unit for supplying several injection molding machines with highly compressed nitrogen for structural foam molding. Only the plasticizing and control technology remain decentralized on the individual machines. This new solution sees Engel significantly reduce the capital outlay for structural foam molding and makes a major contribution to reducing unit costs. The new modular Engel e-foam XL multi systems, based on Trexel's MuCell technology, are offered exclusively by Engel.
Structural foam molding is more popular than ever. It saves raw material, energy, and weight, supporting the objective of producing and using plastic parts in a more sustainable way. At K 2022, Engel (hall 15, booth C58) is presenting a new technology for plastics processors who produce parts in parallel on several production cells using the structural foam molding process.
More information: Kazutaka Nakashima et al, CoreCavity, ACM Transactions on Graphics (2018). DOI: 10.1145/3197517.3201341 Project page: visualcomputing.ist.ac.at/publ … ons/2018/CoreCavity/
Your email address is used only to let the recipient know who sent the email. Neither your address nor the recipient's address will be used for any other purpose. The information you enter will appear in your e-mail message and is not retained by Phys.org in any form.
Among other things, a new tool technology is responsible for this leap in development. Ceramic coatings in the cavities prevent the otherwise typical foam streaks, weld lines, tiger stripes, or gloss differences from appearing on the surface of the foam molded part. Additionally, different surface structures can be created directly in the injection mold via the cavity coating.
In addition, new materials developed by Faurecia Interiors for structural foam molding contribute to the surface quality. An IniCycle talc-filled polypropylene grade with 30% recycled material content will be processed during the K show. IniCycle is suitable for all physical and chemical foam molding processes.
Get weekly and/or daily updates delivered to your inbox. You can unsubscribe at any time and we'll never share your details to third parties.
Use this form if you have come across a typo, inaccuracy or would like to send an edit request for the content on this page. For general inquiries, please use our contact form. For general feedback, use the public comments section below (please adhere to guidelines).
The decompositions suggested by the design tool are often surprising: "The computer is able to find solutions that are very unintuitive," says Bernd Bickel, professor at IST Austria. "The two halves of the rabbit, for instance, have a curving, complicated connection—it would have been extremely difficult for a human to come up with that." Industry designers, as well as previous design programs, generally rely on straight cuts through the object. In practice, this often leads to a larger number of pieces, as well as "unnatural" divisions. "The software tool could also be extremely useful in industry—it would fit seamlessly into the production process," adds Bickel.
Most of the plastic objects we see are created using injection molding, but designing such molds is a difficult task, usually requiring experts. Now, computer scientists from the Institute of Science and Technology Austria (IST Austria), the University of Tokyo, and CONICET have created an interactive design tool that allows non-experts to create molds for an object of their choice. The software will be presented at this year's prestigious SIGGRAPH conference, one of IST Austria's five successful submissions.
GETTING A QUOTE WITH LK-MOULD IS FREE AND SIMPLE.
FIND MORE OF OUR SERVICES:
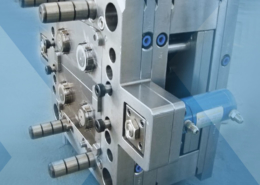
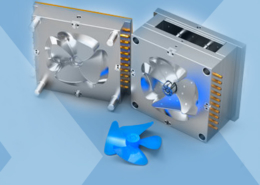
Plastic Molding

Rapid Prototyping
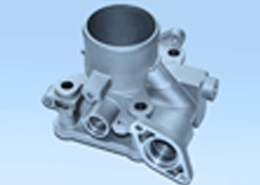
Pressure Die Casting
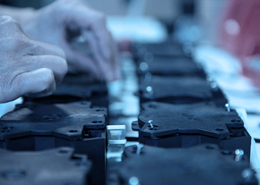
Parts Assembly
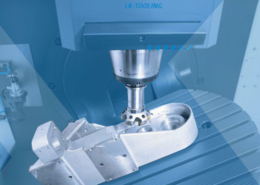