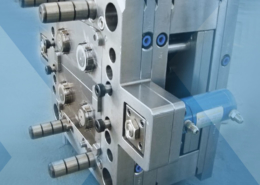
Exploring Low Volume Plastic Injection Molding
Author:gly Date: 2024-06-08
Introduction
Low volume plastic injection molding is a manufacturing process that has gained significant attention due to its versatility and cost-effectiveness in producing small to medium quantities of plastic parts. In recent years, its importance has grown in various industries, including automotive, medical, consumer goods, and electronics. This article aims to provide a comprehensive overview of low volume plastic injection molding, exploring its processes, advantages, limitations, applications, and future prospects.
Process Overview
Plastic injection molding involves the melting of plastic pellets and injecting them into a mold cavity under high pressure. In low volume molding, smaller production runs are feasible, typically ranging from a few hundred to several thousand units. The process begins with the design of the mold, followed by material selection, mold fabrication, injection molding, and finally, post-processing and quality inspection.
The injection molding machine consists of a hopper, barrel, screw, and injection unit. The plastic pellets are fed into the hopper, where they are heated and melted in the barrel. The molten plastic is then injected into the mold cavity through the screw, where it cools and solidifies into the desired shape. Once the part is ejected from the mold, it undergoes secondary operations such as trimming, surface finishing, and assembly if necessary.
Advantages
Low volume plastic injection molding offers several advantages, including cost-effectiveness, rapid prototyping, design flexibility, and high repeatability. With lower tooling costs and shorter lead times compared to traditional molding methods, it enables manufacturers to bring products to market faster and at a lower cost. Additionally, the ability to quickly iterate designs and produce custom parts makes it ideal for prototyping and small-scale production.
Moreover, injection molding allows for intricate part geometries, tight tolerances, and a wide range of material options, including thermoplastics, elastomers, and engineering resins. This versatility makes it suitable for diverse applications across various industries, from aerospace and automotive to medical devices and consumer electronics.
Limitations
Despite its advantages, low volume plastic injection molding also has some limitations to consider. One of the main challenges is the initial tooling cost, which can be prohibitive for small-scale projects or prototypes. Additionally, the complexity of the molding process requires skilled operators and proper equipment maintenance to ensure quality and consistency.
Furthermore, the economies of scale may not always favor low volume production, as unit costs can be higher compared to high-volume runs. Manufacturers need to carefully evaluate the cost-benefit analysis and consider alternative manufacturing methods for larger quantities.
Applications
Low volume plastic injection molding finds applications across a wide range of industries, including:
Automotive
: for interior and exterior components, dashboard panels, and lighting fixtures.
Medical Devices
: for disposable instruments, surgical tools, and drug delivery systems.
Consumer Goods
: for household appliances, electronic enclosures, and toys.
Electronics
: for connectors, housings, and components for smartphones, computers, and wearables.
The ability to produce custom parts with short lead times makes it valuable for prototyping, product development, and niche markets where customization is paramount.
Future Prospects
Looking ahead, the future of low volume plastic injection molding is promising, driven by advancements in material science, automation, and digital technologies. Additive manufacturing techniques such as 3D printing are complementing injection molding, offering new possibilities for rapid tooling and hybrid manufacturing processes.
Moreover, the growing demand for sustainable solutions and biodegradable materials is driving innovation in eco-friendly plastics and recycling technologies. As the industry continues to evolve, collaboration between manufacturers, material suppliers, and technology providers will be crucial in pushing the boundaries of low volume plastic injection molding.
Conclusion
In conclusion, low volume plastic injection molding is a versatile and cost-effective manufacturing process that enables the production of small to medium quantities of plastic parts with high precision and repeatability. While it offers numerous advantages such as rapid prototyping and design flexibility, it also poses challenges in terms of tooling costs and economies of scale. However, with ongoing technological advancements and increasing demand for customization, the future prospects of low volume plastic injection molding remain bright, promising continued growth and innovation in the manufacturing industry.
GETTING A QUOTE WITH LK-MOULD IS FREE AND SIMPLE.
FIND MORE OF OUR SERVICES:
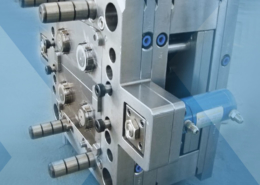
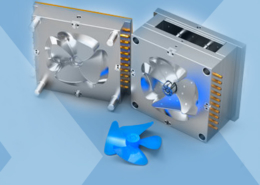
Plastic Molding

Rapid Prototyping
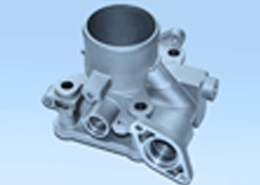
Pressure Die Casting
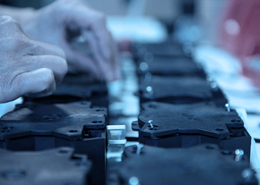
Parts Assembly
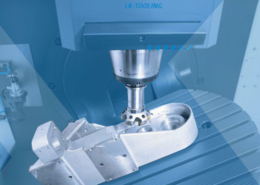