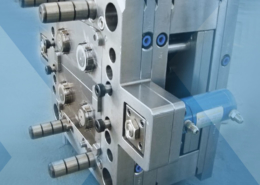
Injection Tray Plastic: A Versatile Solution for Packaging Needs
Author:gly Date: 2024-06-08
Introduction:
In the dynamic world of packaging, injection tray plastic emerges as a versatile and efficient solution for a wide range of applications. From food packaging to electronic components, injection-moulded plastic trays offer unparalleled versatility, durability, and customization options. In this comprehensive exploration, we delve into the realm of injection tray plastic, uncovering its applications, benefits, manufacturing process, and future prospects.
Unveiling the Applications of Injection Tray Plastic
Injection tray plastic finds applications across various industries, including food and beverage, pharmaceuticals, electronics, and agriculture. In the food industry, plastic trays are commonly used for packaging fruits, vegetables, meat, and dairy products, offering protection, hygiene, and convenience for both producers and consumers. In pharmaceuticals, plastic trays serve as blister packaging for tablets and capsules, ensuring dosage accuracy and tamper-evidence.
The Benefits of Injection Tray Plastic
The adoption of injection tray plastic offers numerous benefits for manufacturers, retailers, and consumers alike. Plastic trays are lightweight yet sturdy, reducing shipping costs and minimizing environmental impact. Moreover, they are customizable in terms of size, shape, and color, allowing for branding opportunities and product differentiation. Additionally, plastic trays are recyclable and reusable, supporting sustainable packaging practices and reducing waste.
The Manufacturing Process of Injection Tray Plastic
The manufacturing process of injection tray plastic involves several steps, including mould design, material selection, injection moulding, and finishing. Mould design is crucial to ensuring the desired shape, dimensions, and functionality of the plastic tray. Material selection depends on factors such as product requirements, environmental considerations, and regulatory compliance. Injection moulding, the heart of the process, involves injecting molten plastic into a mould cavity under high pressure, where it solidifies to form the desired shape. Finally, finishing processes such as trimming, cutting, and assembly may be performed to refine the appearance and functionality of the plastic tray.
Future Prospects and Innovations
Looking ahead, the future of injection tray plastic is bright, with ongoing innovations in materials, technologies, and sustainability practices. Advances in biodegradable plastics, recycled materials, and compostable packaging offer promising alternatives to traditional plastics, addressing concerns about plastic pollution and environmental sustainability. Moreover, digitalization and automation are revolutionizing the manufacturing process, enabling greater efficiency, accuracy, and customization in the production of plastic trays.
Conclusion:
In conclusion, injection tray plastic stands as a versatile and efficient solution for a wide range of packaging needs. Its applications span across industries, offering benefits such as versatility, durability, and customization options. By embracing innovations in materials, technologies, and sustainability practices, injection tray plastic can continue to meet the evolving needs of the packaging industry while minimizing environmental impact and maximizing efficiency.
GETTING A QUOTE WITH LK-MOULD IS FREE AND SIMPLE.
FIND MORE OF OUR SERVICES:
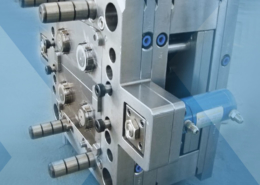
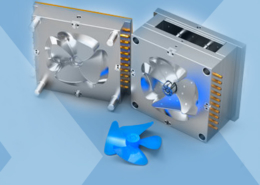
Plastic Molding

Rapid Prototyping
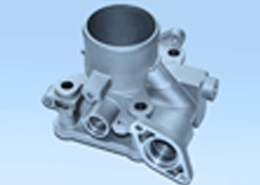
Pressure Die Casting
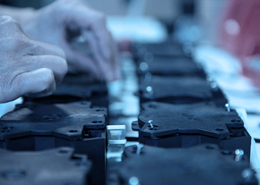
Parts Assembly
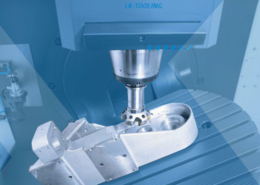