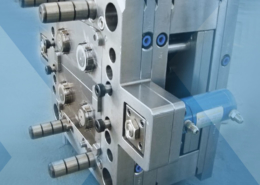
What Causes Short Shot in Plastic Injection Molding? - short mould in injection
Author:gly Date: 2024-10-15
Although PET injection moulding sounds simple and straightforward, the process involves a host of parameters. Material dryness, melt temperature, mould temperature, pressures, ventilation and injection speed must all be configured with the right values, set at the right times, to achieve perfect results.
Creating packaging solutions through PET injection moulding is an industrial precision craftThe vast majority of beauty packaging solutions are made of some kind of plastic. PET is a popular material, being recyclable, flexible and compatible with many kinds of formulations. Injection moulding allows it to be shaped into jars, rigid bottles and a host of other pack types. Here, we explain the process, its advantages and its challenges.First of all, what is PET?Polyethylene terephthalate (PET) is also known as thermoplastic polyester. It is an excellent packaging material, allowing a great deal of creative design when expertly injected.How does PET injection moulding work?Injection moulding allows PET to be shaped into rigid packaging formats. PET initially comes in small pellet form. During the injection moulding process, the pellets are heated in the machine and the molten material is injected into a mould cavity, which then cools and solidifies to form the desired product.How is it different from blow moulding?Blow moulding is used to make thin-walled products like water bottles, for example. Injection moulding allows greater wall thicknesses, to create products with a luxurious look and feel.What are the challenges in PET injection?Although PET injection moulding sounds simple and straightforward, the process involves a host of parameters. Material dryness, melt temperature, mould temperature, pressures, ventilation and injection speed must all be configured with the right values, set at the right times, to achieve perfect results.PET is very sensitive to water and must be meticulously dried before production. It is also sensitive to high temperatures, so it is critical to adhere to the established pressures, times and temperatures, to avoid quality defects like brittleness, dullness, burns, flashes and dimensional deviations.Originally, PET was mainly used in blow moulding to produce thin-walled products. Thick-walled products require injection moulding, however, and the process is more complex. The material properties have to be in perfect sync with the mould shape and design, as well as the injection moulding machine.Is injecting rPET the same as virgin PET?More or less, but it is important to align the processes to the material’s properties. Compared to virgin PET, recycled PET (or rPET or PCR PET) has its own characteristics: the melt flow rate is different and, being reused, its appearance is inevitably affected by impurities. It is possible to use a percentage of rPET – anywhere from 5% to 100%, depending on the shape and aesthetics required. In any case, rPET must always be tested with the formula, especially when dealing with a mix.What colours can a PET pack be?With virgin PET, all kinds of colours are possible. Limitations only exist with certain special colour batches, where additive separation can be visible. Colour choices depend on the purity of the material used, so they are far more restricted with rPET.How can brands choose between recycled and virgin PET for their packaging?The choice depends on the level of sustainability and quality they require, as well as time and volume. rPET has a lower environmental impact, but has restrictions in terms of lead times and aesthetics. Brands may choose to embrace rPET’s ‘imperfections’ to visually send a message on sustainability, although these can be mitigated with the right process parameters and decoration techniques.Volume is also a consideration. The final product quantities should ideally match the available material batch quantities, to avoid variations in the process parameters and the products’ final appearance. Consult our catalogue to see our full range of beauty packaging solutions in PET.
Meanwhile, the global market for injection molded plastics is expected to reach a value of $473.4 billion by the year 2027. Currently, the industry is valued at $339.3 billion.
With virgin PET, all kinds of colours are possible. Limitations only exist with certain special colour batches, where additive separation can be visible. Colour choices depend on the purity of the material used, so they are far more restricted with rPET.
How is it different from blow moulding?Blow moulding is used to make thin-walled products like water bottles, for example. Injection moulding allows greater wall thicknesses, to create products with a luxurious look and feel.
Blow moulding is used to make thin-walled products like water bottles, for example. Injection moulding allows greater wall thicknesses, to create products with a luxurious look and feel.
Volume is also a consideration. The final product quantities should ideally match the available material batch quantities, to avoid variations in the process parameters and the products’ final appearance.
• 8% of plastic mold manufacturers import raw materials, which is slightly lower than the 11% average across all manufacturers.• 76% of plastic mold makers focus on domestic distribution. This is slightly higher than the 70% of all manufacturers that sell their products on the domestic market.
Polyethylene terephthalate (PET) is also known as thermoplastic polyester. It is an excellent packaging material, allowing a great deal of creative design when expertly injected.
What are the challenges in PET injection?Although PET injection moulding sounds simple and straightforward, the process involves a host of parameters. Material dryness, melt temperature, mould temperature, pressures, ventilation and injection speed must all be configured with the right values, set at the right times, to achieve perfect results.
American Tool & Mold, Inc. produces plastic molds used by other manufacturers. This Clearwater, Florida, company has 180 employees and can create customized molds for a wide range of applications, including multi-cavity molds and precision molds.
CompanyCityState Number of EmployeesPlastek Industries, Inc.EriePA850LexaMar Corp.Boyne CityMI400Jones Plastic & Engineering Co., LLCLouisvilleKY300Hi-Tech Mold & Engineering, Inc.Rochester HillsMI200MMI Engineered SolutionsSalineMI192American Tool & Mold, Inc.ClearwaterFL180Ironwood Plastics, Inc.IronwoodMI155Seaway Plastics Engineering, LLCPort RicheyFL151AlwinClintonvilleWI150Decatur Mold, Tool & Engineering, Inc.North VernonIN150
This emphasis on the domestic market and local suppliers could indicate a potential for expansion on new markets for plastic mold manufacturers.
PET is very sensitive to water and must be meticulously dried before production. It is also sensitive to high temperatures, so it is critical to adhere to the established pressures, times and temperatures, to avoid quality defects like brittleness, dullness, burns, flashes and dimensional deviations.Originally, PET was mainly used in blow moulding to produce thin-walled products. Thick-walled products require injection moulding, however, and the process is more complex. The material properties have to be in perfect sync with the mould shape and design, as well as the injection moulding machine.Is injecting rPET the same as virgin PET?More or less, but it is important to align the processes to the material’s properties. Compared to virgin PET, recycled PET (or rPET or PCR PET) has its own characteristics: the melt flow rate is different and, being reused, its appearance is inevitably affected by impurities. It is possible to use a percentage of rPET – anywhere from 5% to 100%, depending on the shape and aesthetics required. In any case, rPET must always be tested with the formula, especially when dealing with a mix.
PET is very sensitive to water and must be meticulously dried before production. It is also sensitive to high temperatures, so it is critical to adhere to the established pressures, times and temperatures, to avoid quality defects like brittleness, dullness, burns, flashes and dimensional deviations.
Editor's Note: A version of this post was originally published in June 3, 2020. It has been updated to include current trends and statistics.
Hi-Tech Mold & Engineering, Inc. is located in Rochester Hills, Michigan. Its 200 employees work on components for vehicles, appliances, medical devices, and solutions for the aerospace and defense industries.
Located in Saline, Michigan, MMI Engineered Solutions employs 192 people. This manufacturer has an in-house design team and uses injection and blow mold techniques to produce powertrain, exterior and interior parts for the automotive industry.
Located in North Vernon, Indiana, Decatur Mold, Tool & Engineering, Inc. employs 150 people to produce military aircraft parts, car seats and automotive components.
Volume is also a consideration. The final product quantities should ideally match the available material batch quantities, to avoid variations in the process parameters and the products’ final appearance.
How does PET injection moulding work?Injection moulding allows PET to be shaped into rigid packaging formats. PET initially comes in small pellet form. During the injection moulding process, the pellets are heated in the machine and the molten material is injected into a mould cavity, which then cools and solidifies to form the desired product.
Alwin offers design and product development services to create customized solutions. This Clintonville, Wisconsin, manufacturer has 150 employees and also produces commercial towel and napkin dispensers.
What colours can a PET pack be?With virgin PET, all kinds of colours are possible. Limitations only exist with certain special colour batches, where additive separation can be visible. Colour choices depend on the purity of the material used, so they are far more restricted with rPET.
The vast majority of beauty packaging solutions are made of some kind of plastic. PET is a popular material, being recyclable, flexible and compatible with many kinds of formulations. Injection moulding allows it to be shaped into jars, rigid bottles and a host of other pack types. Here, we explain the process, its advantages and its challenges.
Originally, PET was mainly used in blow moulding to produce thin-walled products. Thick-walled products require injection moulding, however, and the process is more complex. The material properties have to be in perfect sync with the mould shape and design, as well as the injection moulding machine.
This Louisville, Kentucky, manufacturer has 300 employees. Jones Plastic & Engineering Co., LLC uses injection molding techniques to produce automotive parts, packaging, electronic components and products for the medical industry.
This Ironwood, Michigan, manufacturer creates molds for products with precise requirements. Ironwood Plastics, Inc. and its 155 employees use advanced techniques like pressure monitoring, laser scanning and mold flow analysis to create specialized molds.
As U.S. manufacturers continue to contend with disruptions to the global supply chain, manufacturers are looking to source more supplies at home. One study found that 62% of manufacturers plan to source more supplies domestically in 2021.
How can brands choose between recycled and virgin PET for their packaging?The choice depends on the level of sustainability and quality they require, as well as time and volume. rPET has a lower environmental impact, but has restrictions in terms of lead times and aesthetics. Brands may choose to embrace rPET’s ‘imperfections’ to visually send a message on sustainability, although these can be mitigated with the right process parameters and decoration techniques.
Seaway Plastics Engineering, LLC has 151 employees and is located in Port Richey, Florida. This company specializes in engineering and low-volume runs. It creates products for the packaging, defense, medical, transportation and electronics sectors among others.
According to MNI, the century-old data compiler that powers IndustrySelect's industrial database subscription, the plastic injection mold industry is a fairly small and specialized sector with 555 US-based companies. Half of these manufacturers are located in the Midwest.
The industrial marketplace IndustryNet continues to see heightened domestic sourcing activity, including greater demand for plastic injection molding services, which reported thousands of searches from industrial buyers interested in plastic injection molding in 2020. Year-over-year category searches on the industrial marketplace IndustryNet were up 27% in 2020, while requests-for-quotes rose 102.1% and catalog downloads increased 21%. This trend reflects the growing number of manufacturers looking for domestic supplies, including plastic injection molding companies.
Quadpack is a global cosmetics packaging manufacturer and provider for beauty brands. With offices and production facilities in Europe, the US and the Asia Pacific region, and a strategic network of partners, Quadpack develops sustainable and innovative packaging for skincare, make-up and fragrance customers. With extensive manufacturing expertise in airless bottles, cosmetics jars, wooden packaging and decoration, Quadpack is proud to offer complete solutions to help beauty brands perform.
The choice depends on the level of sustainability and quality they require, as well as time and volume. rPET has a lower environmental impact, but has restrictions in terms of lead times and aesthetics. Brands may choose to embrace rPET’s ‘imperfections’ to visually send a message on sustainability, although these can be mitigated with the right process parameters and decoration techniques.
The vast majority of beauty packaging solutions are made of some kind of plastic. PET is a popular material, being recyclable, flexible and compatible with many kinds of formulations. Injection moulding allows it to be shaped into jars, rigid bottles and a host of other pack types. Here, we explain the process, its advantages and its challenges.
Are you looking for sales leads in the the plastic injecton molding industry or the manufacturing world at large? Access comprehensive profiles of 500,000 industrial businesses and one million executives with IndustrySelect. Try a free demo of IndustrySelect and reach new prospects in the industrial world!
First of all, what is PET?Polyethylene terephthalate (PET) is also known as thermoplastic polyester. It is an excellent packaging material, allowing a great deal of creative design when expertly injected.
Located in Boyne City, Michigan, LexaMar Corp. employs 400 people. This manufacturer uses rubber and plastic to produce exterior parts for the automotive industry.
IndustrySelect provides clients with touch-point data for potential leads, including direct executive contact information and other actionable data among 500,000 companies in the manufacturing and energy sector.
Today we're taking a quick look at some additional facts on the plastic injection molding industry and exploring the top ten plastic injection companies in the United States.
Injection moulding allows PET to be shaped into rigid packaging formats. PET initially comes in small pellet form. During the injection moulding process, the pellets are heated in the machine and the molten material is injected into a mould cavity, which then cools and solidifies to form the desired product.
Plastek Industries, Inc. has locations in four countries. Its Erie, Pennsylvania, headquarters is the largest plastic mold manufacturing facility in the US with 850 employees. They manufacture products like packaging for the beauty and cosmetics industry, food and beverage products, stock packaging options, and pharmaceutical packaging.
More or less, but it is important to align the processes to the material’s properties. Compared to virgin PET, recycled PET (or rPET or PCR PET) has its own characteristics: the melt flow rate is different and, being reused, its appearance is inevitably affected by impurities. It is possible to use a percentage of rPET – anywhere from 5% to 100%, depending on the shape and aesthetics required. In any case, rPET must always be tested with the formula, especially when dealing with a mix.
GETTING A QUOTE WITH LK-MOULD IS FREE AND SIMPLE.
FIND MORE OF OUR SERVICES:
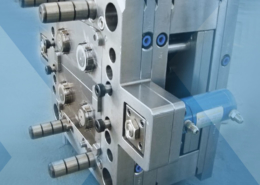
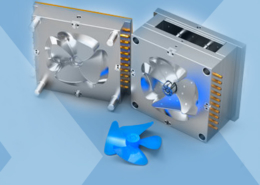
Plastic Molding

Rapid Prototyping
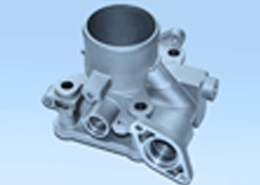
Pressure Die Casting
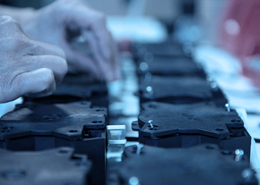
Parts Assembly
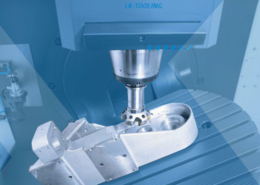