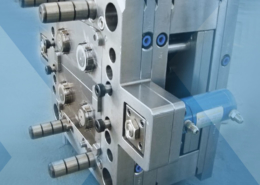
What are requirements of precision injection molding for ... - precision plastic
Author:gly Date: 2024-10-15
Depending upon the process parameters like volume and pressure, molds are generally made from steel alloys or aluminum alloys. For less intensive jobs, the material choice can include different plastics, resins, and rubbers.
Owing to its significance in aligning the assembly, tight accuracy and dimensional constraints are placed on their manufacturing.
Moreover, this portion of the injection mold also minimizes the formation of air gaps inside the molten metal. It keeps injecting molten metal into the cavity until most of the air inside the cavity exits the system via the venting system.
The venting system is arguably among the critical injection mold components. The cavity is an enclosed space filled with air and gases. These create air pockets in the part, deteriorating its quality and appearance. Moreover, certain plastics also generate compounds that are not healthy for the mold.
At WayKen, we take into account factors such as part design, material properties, production volume, and budget constraints to create customized solutions. By optimizing the design and strict quality control, we ensure efficient manufacturing processes and high-quality finished parts. Just upload your CAD files to start a new project!
The nozzle is like a pipe with a cross-section that gets narrow as it gets closer to the exit point (into the mold gate system). The sprue bushing is the component that holds the nozzle in place and ensures its alignment and centering.
Ejector pins design is an important aspect of mold production. The design engineer must include a sufficient number of ejection pins to safely share the ejection load. Moreover, since ejector pins come into contact with the part, their surface finish and placement are also matters requiring consideration. Generally, their location is set at points that are not visible on the part.
WayKen is a rapid manufacturing company providing one-stop rapid tooling services. Our experienced team and state-of-the-art manufacturing facility ensure that we can meet the needs of our clients when it comes to injection molding.
As far as plastic mold fabrication goes, the injection process has almost revolutionized the way in which things are produced in modern times. This process has made fabrication of plastic simpler and a lot faster. It will hardly be an exaggeration to state that the possibility of the use of this process is practically limitless. You might be wondering how this plastic injection molding machine actually works. To start the process, a design of the product is first developed. Then a metal mold is made and that mold is secured to the machine firmly.
There are several parts of an injection mold, each with specific functionality and role in the injection molding process.
These components are important parts of an injection mold. The nozzle regulates the flow of molten plastic into the mold, ensuring that it enters the mold at the correct pressure and speed. Furthermore, it also makes the flow laminar, allowing it to exit smoothly into the cavity.
The previous section explained the various parts of an injection mold in detail. Each part has its own function and manufacturing requirements. Therefore, the material choice can differ for individual mold components.
The core is the other half of the mold. It is responsible for creating internal features such as holes and recesses. The surface finish may not be the top concern for this side due to the internal features, but it is pertinent to mention here that this is not a hard and fast rule.
Injection molds are produced by machining. 5-axis machining is the most common technique as it can create difficult contours and can access hard-to-reach areas in molds. After machining, surface finishing methods like grinding and polishing may be used to achieve the required smoothness for the cavity surfaces.
Before the molding process begins, an operator places the insert at its location inside the mold cavity. It may require supporting fixtures to hold them in place. The mold then closes over it, and the injection process begins.
The cavity is one half of the mold which shapes the external features of the part. By external features, we mean the features that are visible to the user. Thus, the cavity is the component of the mold that gives the part its surface finish and external texture.
Moreover, the mold case acts as a central piece for integrating other components of the injection molding setup like the feeding unit and cooling system. As part of this role, the mold case ensures that all components align together precisely. Hence, its accurate production has a direct bearing on the accuracy of the part.
Injection molding is a widely used manufacturing process in a range of industrial applications. The mold is an important part of the injection molding setup. It houses the cavity inside which the molten material is filled and cooled down until it takes its final form.
The second part of this process requires that the granules or pallets of plastic material are poured into the heated barrel of the machine and it is forced into the cavity of the mold. In the third and final stage, after the cooling of the mold, the product is popped out. It sounds simple because it really is. This plastic mold fabrication process is efficient and enables the manufacturer to handle mass production of plastic products without spending a fortune on worker handlings. It saves effort, time and money and thus is enjoys uncompromised love from all manufacturers around the globe.
What is even more interesting is that the plastic mold fabrication process was invented more than a century ago. It was invented in the year of 1868 by John Wesley Hyatt. He had injected celluloid into a mold to create billiard balls then. Later on, he created an injecting molding machine by adding a plunger to the design. However, it was in 1946, that James Hendry took the initiative to modify Hyatt’s design of the machine by attaching a screw.
The cooling system, as the name suggests, is responsible for keeping the temperature of the mold under control. It includes a circuit of cooling channels circulating throughout the different parts of an injection mold. Mainly, they cover the areas in the vicinity of the cavity holding the molten plastic.
The sprue bushing and nozzle act as the interface between the mold and the feeding system. This is the entry point of the molten plastic into the mold.
Injection molding utilizes water or oil as the cooling media. Water is by far the most popular choice. However, oil is sometimes better for high-temperature applications. Moreover, internal baffles are also sometimes used to increase heat transfer.
The guiding system ensures that the various injection mold parts assemble with precise alignment. It consists of guiding pins and bushing on the mold halves that fit together to locate the parts with each other.
The interlocks can mean a range of locking features in the mold part like pins, grooves, and slots. Their actuation can be mechanical or hydraulic. Hence, there is no specific definition for mold interlocks, but their common purpose is well-understood.
Inserts are special injection mold components that are separately placed inside the cavity to create specific geometric features in the molded part. They are individual components. That is, they are not a part of the core and cavity halves of the mold.
Plastic – whether one hates it or likes it; there is no denying that every single day or lives are guided by quite a few things which are made out of plastic. But did you know that most plastic objects are manufactured through a process called injection molding? Do you want a few examples? Well, washers, pulleys, valves, bottle caps, gears, keyboards, computer monitors are all made by this process. So are knobs, power tools, furniture and car panels. While these things are so varied – both in shape and in use, they are all made by the same process. Fascinating, isn’t it? This process of plastic mold fabrication is so popular because it is cost effective, especially when plastic products are being manufactured at a mass scale.
Injection molds have a complicated design procedure owing to their critical function and extreme working conditions. There are numerous injection mold components that engineers must take into account during design and the process. In this article, we will highlight the purpose of various injection mold parts and discuss the material selection for their manufacturing.
This push comes from the ejector pins. The moving side of the mold carries these ejector pins, which only emerge from its surface when it retracts away from the stationary part. Thus, as it retracts, the pins push the part out of the mold, and it is then ready for another molding cycle.
There is a network of grooves, channels, and pins in the venting system that facilitate the air escaping the cavity. They are kept very narrow to confine the plastic inside and have minimal effects on the surface finish. Furthermore, engineers place them at possible air entrapment points like the parting line to maximize venting efficiency.
The sprue bushing injects the molten plastic into the runner system. This is a distribution network that guides molten plastic to the cavity in a seamless, uniform way. Its function becomes very important when multi-cavity molds are used, where the equal and swift distribution of raw material is critical for molding efficiency.
The mold base is one of the most critical injection molding parts. Its other names are mold plate or mold frame. This part serves as the basic infrastructure for the entire mold assembly. It provides strength and rigidity against the intense pressures of the injection molding process.
Injection mold design is a complicated task with numerous considerations. The main design decisions include the material choice, gate and runner design, draft angles, wall thickness-to-depth ratios, tolerancing, and sink mark and parting line locations.
Mold interlocks are injection mold parts that ensure proper locking and alignment of other injection mold components. Mainly, this refers to the cavity and core halves of the mold. Without adequate interlocking, the chances of molding errors like flashing, warping, and dimensional errors increase significantly.
Inserts can be plastic mold components or metallic if strength is necessary. Typically, their main functions include creating threads in the part, specific surface features or textures, and reinforcing certain mold components.
Injection mold components are vital parts of the injection molding setup and have a direct effect on the quality of the part. Designers and production engineers need to manage and maintain injection molds effectively to get the best results.
The runner system is like a network of roads to each cavity. At the end of the runner, there are gates, which are key injection mold parts. It is an opening into the actual cavity, from the runner. Its main function is to guarantee a smooth entry of raw material into the cavity, prevent flashing, and maintain uniform pressure.
The ejector pins come into play when the molding process ends. After the part solidifies and is ready for ejection, the mold opens. However, due to the pressures and surface tension between the part and the cavity surface, they stick to each other and need a force for proper ejection.
GETTING A QUOTE WITH LK-MOULD IS FREE AND SIMPLE.
FIND MORE OF OUR SERVICES:
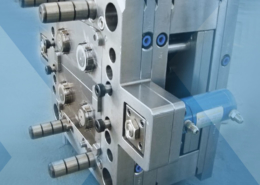
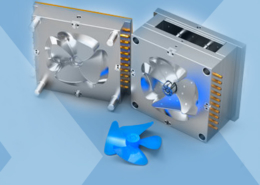
Plastic Molding

Rapid Prototyping
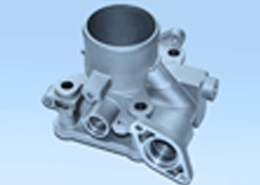
Pressure Die Casting
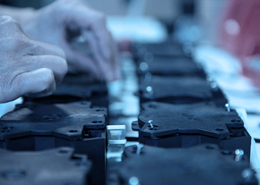
Parts Assembly
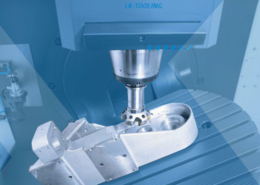