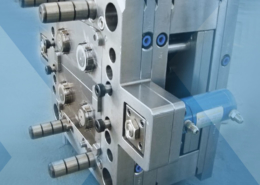
Volume Moulding | Plastic Mouldings | Hi-Technology - high volume injection mold
Author:gly Date: 2024-10-15
Resin drying is a crucial, but often-misunderstood area. This collection includes details on why and what you need to dry, how to specify a dryer, and best practices.
Sustainability continues to dominate new additives technology, but upping performance is also evident. Most of the new additives have been targeted to commodity resins and particularly polyolefins.
What are the common applications of injection molding? What sets it apart as a manufacturing process? This article covers the key benefits of injection molding and provides insight into whether injection molding is right for your industryâs applications.
In this article, weâll take a look at common factors that influence the cost of injection molding, including equipment, labor, and materials â as well as tips for reducing manufacturing costs.
Second quarter started with price hikes in PE and the four volume engineering resins, but relatively stable pricing was largely expected by the quarter’s end.
Mold inserts in aluminium frames: This is the most common 3D printed mold configuration and generally produces more accurate parts. The mold is 3D printed and then inserted into rigid aluminium frames which provide support against the pressure and heat of the injection molding nozzle. Aluminium frames also help preventing the mold from warping after repeated usage.
Join Engel in exploring the future of battery molding technology. Discover advancements in thermoplastic composites for battery housings, innovative automation solutions and the latest in large-tonnage equipment designed for e-mobility — all with a focus on cost-efficient solutions. Agenda: Learn about cutting-edge thermoplastic composites for durable, sustainable and cost-efficient battery housings Explore advanced automation concepts for efficient and scalable production See the latest large-tonnage equipment and technology innovations for e-mobility solutions
A summary of the cost (based on online quotes) of manufacturing the ABS fitting using the technologies discussed above is summarised in the table below. All prices do not include shipping.
Newly available is a line of aluminum master mold frames. With these, users can print their own mold cavities to fit within the frames that serve as a support structure for the mold. Galomb notes that some 3D CAD files of printable molds will be made available free download. By combining 3D printed molds with the Mix-Molder System, Galomb says users can produce real injection molded prototype parts in a much shorter time frame.
Exhibitors and presenters at the plastics show emphasized 3D printing as a complement and aid to more traditional production processes.
Learn what to consider when making a choice between 3D printing and injection molding, the benefits of each manufacturing method, and more.
Injection molding ABS parts with SLA 3D printed molds: High Temperature SLA resins are able to produce functional injection molds with a high level of accuracy that are best suited for low level production runs. SLA resins retail at around $150 - $170 per litre. A benchtop injection molding machine has been used for the calculations in this example with the 3D printed molds inserted into aluminium support frames. ABS pellets are used for molding the part that cost approximately $2 - $3
Want to learn more about die casting? In this article, weâll take a look at the process, its history and current uses, advantages, design guidelines, and more.
When, how, what and why to automate — leading robotics suppliers and forward-thinking moldmakers will share their insights on automating manufacturing at collocated event.
In many cases, decreasing the discharge temperature will improve product quality and perhaps even boost rate. Here are ways to do it.
Industrial FDM ABS 3D printing: Industrial FDM 3D printing has high repeatability and can produces parts with high dimensional accuracy and is able to print parts in small to medium batches. The cost of the ABS filament used in industrial FDM systems is typically around $90 - $110 per kg. The main restriction for any part produced via FDM 3D printing is its anisotropic mechanical performance: parts are significantly weaker in one direction. This means that a designer must have a good grasp on the loads the part will be subjected to and the orientation of the model in the print platform.
Find out about the manufacturing technique used to injection mold a second material over or around a part to create a new one.
This Knowledge Center provides an overview of the considerations needed to understand the purchase, operation, and maintenance of a process cooling system.
Formnext Chicago is an industrial additive manufacturing expo taking place April 8-10, 2025 at McCormick Place in Chicago, Illinois. Formnext Chicago is the second in a series of Formnext events in the U.S. being produced by Mesago Messe Frankfurt, AMT – The Association For Manufacturing Technology, and Gardner Business Media (our publisher).
Galomb Inc.’s Mix-Molder System includes the Model S-100 hand-operated injection molding machine and Model M-100 miniature polymer mixing device. The system allows users to mix small quantities of plastics, additives and fillers, and then immediately inject. Potential uses include experimenting with new polymer blends; making samples for tensile and Izod tests, among others; quality control and batch testing of recycled resins; creating prototypes and doing short production runs.
Plastics Technology Top Shops Benchmarking Survey provided both unanimous responses and divided results, but pervasive throughout is the sense of an industry still grappling with the aftermath of 2020’s global pandemic.
In this collection of content, we provide expert advice on welding from some of the leading authorities in the field, with tips on such matters as controls, as well as insights on how to solve common problems in welding.
The high initial setup costs associated with injection molding make this technology cost-effective only at high volumes. These costs can range between $10,000 and $100,000 and are associated mainly with the very high requirements in designing, engineering and manufacturing the injection molding dies. Because of this injection molding is typically only used to produce very high volumes of identical parts at a low cost. A typical run can involve the production of thousands or sometimes millions of components.
Want to learn how to design undercuts that donât cause damage to your parts? Check out our article, which offers tips and tricks for DFM with undercuts, examples of when you might need them, and more. Undercuts in injection-molded parts present a host of challenges to designers and manufacturers. In this article, weâll take a look at the definition of undercuts, their purpose, applications, and tips for designing parts with them.
Mold maintenance is critical, and with this collection of content we’ve bundled some of the very best advice we’ve published on repairing, maintaining, evaluating and even hanging molds on injection molding machines.
Thousands of people visit our Supplier Guide every day to source equipment and materials. Get in front of them with a free company profile.
If designing for an aluminium frame, add 0.125mm of extra thickness to the back of the mold plates to account for the compression forces and to ensure a complete seal. Increasing the clamping force in the vise can also help mitigate flash, as can polishing the molds’ split plane to give it as flat a surface as possible.
Galomb’s Mix-Molder System hand-operated injection molding machine now offers a line of aluminum master mold frames to support 3D-printed mold cavities.
Flash is the name given to the material that comes out between the two halves of the mold during the injection process. This generally occurs when the two mold halves do not mate perfectly together, are not perfectly flush and flat or the mold is overfilled. Runners are used in the mold design to help reduce the likelihood of flash.
Due to the relatively fragile nature of the materials used in 3D printed injection molds compared to traditional molds, applying excessive force to remove a part from the mold can lead to rapid mold deterioration. Including a release compound on the surfaces of the mold cavity before the injection stage can assist greatly with part removal.
Mixed in among thought leaders from leading suppliers to injection molders and mold makers at the 2023 Molding and MoldMaking conferences will be molders and toolmakers themselves.
While the major correction in PP prices was finally underway, generally stable pricing was anticipated for the other four commodity resins.
While prices moved up for three of the five commodity resins, there was potential for a flat trajectory for the rest of the third quarter.
Learn about the advantages and disadvantages of various methods of industrial 3D printing, materials that are commonly used, and more
Gifted with extraordinary technical know how and an authoritative yet plain English writing style, in this collection of articles Fattori offers his insights on a variety of molding-related topics that are bound to make your days on the production floor go a little bit better.
In the past, 3D printing was used in the design and manufacturing process to only create and verify prototypes that would be later injection molded. Nowadays, technology developments in printer accuracy, surface finish and materials allow 3D printers to also directly manufacture the molds.
Want to learn more about exactly how an injection molding machine functions, as well as its individual parts? This article puts injection molding machines under the microscope, with detailed descriptions of their components and an in-depth guide to the injection molding process.
Currier Plastics had a major stake in small hotel amenity bottles until state legislators banned them. Here’s how Currier adapted to that challenge.
Mike Sepe has authored more than 25 ANTEC papers and more than 250 articles illustrating the importance of this interdisciplanary approach. In this collection, we present some of his best work during the years he has been contributing for Plastics Technology Magazine.
technotrans says climate protection, energy efficiency and customization will be key discussion topics at PTXPO as it displays its protemp flow 6 ultrasonic eco and the teco cs 90t 9.1 TCUs.
Take a deep dive into all of the various aspects of part quoting to ensure you’ve got all the bases—as in costs—covered before preparing your customer’s quote for services.
There are five specific areas that designers and manufacturers need to consider to realize the potential of these unique materials.
The term low-run injection molding typically applies to runs of 10 - 100 parts. Traditionally, such small runs were not financially feasible due to the very high costs associated with manufacturing the tooling (the injection molding dies).
This CW Tech Days virtual event will explore the technologies, materials and strategies used by composites manufacturers working in the evolving space market. Presentations from industry experts will emphasize the use of composite materials in applications requiring the weight savings, structural benefits and ability to withstand extreme temperatures that only composites can provide.
Learn about sustainable scrap reprocessing—this resource offers a deep dive into everything from granulator types and options, to service tips, videos and technical articles.
The Mix-Molder System’s miniature polymer mixing device can combine small quantities of molten plastics, additives and fillers, while mold frames support 3D-printed cavities.
Is low-run injection molding with 3D printed molds the best solution for your application? Then there are two ways for you to move forwards with you project:
If you have access to an injection molding machine and the know-how to design the mold, then 3D printing the mold in a heat resistant material is an option. An article discussing the advatages and disadvatages of the two most commonly used 3D printing materials for manufacturing low-run injection molds can be found here.
ð Please note: Protolabs Network does not manufacture 3D printed molds, but does manufacture custom injection molded parts
When producing parts with injection molding, understanding the range of materials that are available is crucial. Find out more about those materials, their properties, and factors to consider when choosing a material for injection molded parts.
The 3D printing technologies that cover best these requirements are SLA and Material Jetting. These technologies can produce parts with high dimensional accuracy and are ideal for prints intricate details and very fine features. Speciality materials that are available in these technologies, like Formlabs High Temperature resin or Stratasys Digital ABS, are ideal for molding and tooling applications. An outline of the properties that are most relevant to injection molding for these two materials is shown below.
In a time where sustainability is no longer just a buzzword, the food and beverage packaging industry is required to be at the forefront of this innovation. By adopting circular packaging processes and solutions, producers can meet regulatory requirements while also satisfying consumer demand and enhancing brand reputation. Join Husky to learn more about the broader implications of the circular economy — as well as how leading brands are leveraging this opportunity to reduce costs, increase design flexibility and boost product differentiation. Agenda: The cost and operational benefits of embracing circularity Key materials in circular packaging — including rPET and emerging bioplastics How to design a circular food and beverage package Strategies for selecting sustainable closures to future-proof packaging solutions Optimization and streamlining of production processes for enhanced efficiency How Husky Technologies can enable your sustainable success
Ultradent's entry of its Umbrella cheek retractor took home the awards for Technical Sophistication and Achievement in Economics and Efficiency at PTXPO.
Injection molding is the most common method for mass producing plastic parts. It is ideal for producing rapidly very large numbers of identical parts with tight tolerances.
This article discusses the benefits of using 3D printing for manufacturing low-run injection molds and gives advice on the possible mold configurations, the available 3D printing mold materials and the best design practices for creating 3D printed injection molds.
This month’s resin pricing report includes PT’s quarterly check-in on select engineering resins, including nylon 6 and 66.
An overview on the use of chemical foaming agents (CFAs) to successfully foam single and multilayered rotational molding parts, this webinar will illustrate the multiple benefits rotational molders can achieve, including reducing resin consumption, decreasing part weight, enhancing wall thickness and improving structural rigidity. Agenda: Charging the mold Dosing ratios Venting Optimal decomposition temperatures, cycle times and drop times for drop box applications Cooling considerations
Modifications to the common core pin can be a simple solution, but don’t expect all resins to behave the same. Gas assist is also worth a try.
Join Wittmann for an engaging webinar on the transformative impact of manufacturing execution systems (MES) in the plastic injection molding industry. Discover how MES enhances production efficiency, quality control and real-time monitoring while also reducing downtime. It will explore the integration of MES with existing systems, emphasizing compliance and traceability for automotive and medical sectors. Learn about the latest advancements in IoT and AI technologies and how they drive innovation and continuous improvement in MES. Agenda: Overview of MES benefits What is MES? Definition, role and brief history Historical perspective and evolution Longevity and analytics Connectivity: importance, standards and integration Advantages of MES: efficiency, real-time data, traceability and cost savings Emerging technologies: IoT and AI in MES
Improvements in nozzle design in recent years overcome some of the limitations of previous filter, mixing, and shut-off nozzles.
Join KraussMaffei for an insightful webinar designed for industry professionals, engineers and anyone interested in the manufacturing processes of PVC pipes. This session will provide a comprehensive understanding of the technology behind the production of high-quality PVC pipes: from raw material preparation to final product testing. Agenda: Introduction to PVC extrusion: overview of the basic principles of PVC pipe extrusion — including the process of melting and shaping PVC resin into pipe forms Equipment and machinery: detailed explanation of the key equipment involved — such as extruders, dies and cooling systems — and their roles in the extrusion process Process parameters: insight into the critical process parameters like temperature, pressure and cooling rates that influence the quality and consistency of the final PVC pipes Energy efficiency: examination of ways to save material and energy use when extruding PVC pipe products
What are the most common defects in the injection molding process and how do you avoid them? This article provides six essential design tips for avoid production defects while reducing the cost and lead time of your molded parts.
In this collection, which is part one of a series representing some of John’s finest work, we present you with five articles that we think you will refer to time and again as you look to solve problems, cut cycle times and improve the quality of the parts you mold.
Multiple speakers at Molding 2023 will address the ways simulation can impact material substitution decisions, process profitability and simplification of mold design.
Stand alone molds: In this mold configuration the mold is fully 3D printed and a rigid aluminium support frame is not used. This way intricate cooling channels can be integrated in the mold, but molds manufactured using this approach require more 3D printing material (increasing the print cost and time) and are more prone to warping after extensive use.
Describing specific technical design of mold features (such as gates, runners, air vents etc) is out of the scope of this article. An internet search will reveal a large amount of information on the subject. This post by Seattle Robotics is a good starting point for those new to injection mold design.
Across all process types, sustainability was a big theme at NPE2024. But there was plenty to see in automation and artificial intelligence as well.
Otherwise, you can outsource the production to a professional injection molding manufacturer. Protolabs Network offers access to a global network of Injection Molding service providers, who are able design a mold for your part and produce volumes from 100 to 10,000+ units.
This 1-day technical conference and exhibition showcases innovative developments in materials, processing and equipment for the additive manufacturing industry. This conference is specifically designed to inform, update and educate plastic processors about implementing new additive manufacturing technologies. Hear technical presentations on the newest advances in additive manufacturing related to: design, materials development, processing equipment and enabling technologies, new applications and more. See exhibits from engineering plastic suppliers, compounders, molders, design and engineering firms and machinery suppliers. Experts will show you how to apply the latest technologies to your next project or program. The conference includes a full day of technical presentations, plenary and keynote presentations on business trends; breakfast, lunch and breaks; exhibits of advanced technologies and an evening networking reception. Note: Additive Manufacturing Media executive editor Stephanie Hendrixson will moderate the Supporting AM Adoption in Northeast Ohio panel at 11:20 a.m.
What is Delrin and why is it unique among the many manufacturing materials available? Delrin, or POM-H (homopolymer acetal), is used in CNC machining, 3D printing and injection molding to create durable, precise components. This article explores Delrinâs properties and how to get the most out of the material.
For industrial applications, desktop SLA is not suitable. An in-depth article comparing the two most commonly used industrial 3D printing materials for mold manufacturing (Digtal ABS and Somos PerFORM) can be found here.
Plastics Technology covers technical and business Information for Plastics Processors in Injection Molding, Extrusion, Blow Molding, Plastic Additives, Compounding, Plastic Materials, and Resin Pricing. About Us
AIM Processing has parlayed small part molding expertise and aggressive automation, even for short run production, into a highly successful custom molding business.
Multi Jet Fusion (MJF) is a 3D printing process for building prototyping and end-use parts fast. This article explains how MJF works and its main advantages.
Join this webinar to explore the transformative benefits of retrofitting your existing injection molding machines (IMMs). Engel will guide you through upgrading your equipment to enhance monitoring, control and adaptability — all while integrating digital technologies. You'll learn about the latest trends in IMM retrofitting (including Euromap interfaces and plasticizing retrofits) and discover how to future-proof your machines for a competitive edge. With insights from industry experts, it'll walk you through the decision-making process, ensuring you make informed choices that drive your business forward. Agenda: Maximize the value of your current IMMs through strategic retrofitting Learn how to integrate digital technologies to enhance monitoring and control Explore the benefits of Euromap interfaces and plasticizing retrofits Understand how retrofitting can help meet new product demands and improve adaptability Discover how Engel can support your retrofitting needs, from free consultations to execution
The Plastics Industry Association (PLASTICS) has released final figures for NPE2024: The Plastics Show (May 6-10; Orlando) that officially make it the largest ever NPE in several key metrics.
Introduced by Zeiger and Spark Industries at the PTXPO, the nozzle is designed for maximum heat transfer and uniformity with a continuous taper for self cleaning.
It is important to consider whether a mold is going to be used to make 20 or 20,000 parts. Historically molds needed to be CNC machined to a very high tolerance from metal (most commonly aluminium or steel). These materials provide good wear resistance to the repeated injection, opening and closing of the mold and the temperature gradients that they were exposed during the injection molding process. However, metal molds do require a initial large investments at the setup stage.
After successfully introducing a combined conference for moldmakers and injection molders in 2022, Plastics Technology and MoldMaking Technology are once again joining forces for a tooling/molding two-for-one.
Traditional injection molded ABS part: Traditional injection molded parts have a very high level of accuracy, excellent surface finish and a very high level of repeatability. The main downsides of traditional injection molding is the high initial setup cost and the number of design restrictions enforced in the designing of the molded part (draft angles, constant wall thickness etc). The cost of the ABS pellets is the same as above.
August 29-30 in Minneapolis all things injection molding and moldmaking will be happening at the Hyatt Regency — check out who’s speaking on what topics today.
Despite price increase nominations going into second quarter, it appeared there was potential for generally flat pricing with the exception of a major downward correction for PP.
What are the basic building blocks of plastics and how do they affect the processing of that material and its potential applications in the real world? Meet the repeat unit.
More than four years on, there are aspects of the COVID-19 pandemic that linger in their impacts to the plastics market and are made visible in our annual survey.
For low-run molding, wear resistance is no longer the most critical factor. Certain 3D printing technologies, such as Material Jetting and SLA, are able to produce parts to a high accuracy with excellent surface finish. When this is coupled with the modern temperature resistant 3D printing materials and the design freedom 3D printing enables, it means that 3D printed molds are now a viable option for manufacturing low-run injection molding dies. 3D printed molds also allow the quick verification of the mold design, mitigating the financial risk of investing in an expensive metal mold.
Injection molding is the process of creating a components by injecting under pressure melted material into a die. The material fills the hollow cavities of the mold and when it cools it solidifies, taking the form of the die. The die then opens, the solid part is ejected and the process repeats. Automating the this process can yield very high production rates. The materials commonly used in injection molding are thermoplastic polymers, but it is possible to mold certain thermosetting plastics.
In this three-part collection, veteran molder and moldmaker Jim Fattori brings to bear his 40+ years of on-the-job experience and provides molders his “from the trenches” perspective on on the why, where and how of venting injection molds. Take the trial-and-error out of the molding venting process.
Specific restrictions on design will depend upon the injection molding machine that is used. However Stratasys suggest that molds made via their Material Jetting printers should be used to produce parts with maximum volume of 165 cm3 in 50 to 80 ton molding machines or manual hand presses.
Fast turnaround times (1-2 week opposed to 5-7 weeks). Applications where production quantities are low (50 - 100 parts). Mold designs where changes or iterations are probable. Parts that are relatively small (less than 150 mm).
Discover how artifical intelligence is revolutionizing plastics processing. Hear from industry experts on the future impact of AI on your operations and envision a fully interconnected plant.
Plastics Technology’s Tech Days is back! Every Tuesday in October, a series of five online presentations will be given by industry supplier around the following topics: Injection Molding — New Technologies, Efficiencies Film Extrusion — New Technologies, Efficiencies Upstream/Downstream Operations Injection Molding — Sustainability Extrusion — Compounding Coming out of NPE2024, PT identified a variety of topics, technologies and trends that are driving and shaping the evolution of plastic products manufacturing — from recycling/recyclability and energy optimization to AI-based process control and automation implementation. PT Tech Days is designed to provide a robust, curated, accessible platform through which plastics professionals can explore these trends, have direct access to subject-matter experts and develop strategies for applying solutions in their operations.
This case study will compare manufacturing a custom plastic fitting for a motor housing. The requirements of the design are:
This article discusses the use of 3D printing to print molds for low run injection molding. Design considerations, materials, molds configurations and a comparative case study are all included
In this collection of articles, two of the industry’s foremost authorities on screw design — Jim Frankand and Mark Spalding — offer their sage advice on screw design...what works, what doesn’t, and what to look for when things start going wrong.
GETTING A QUOTE WITH LK-MOULD IS FREE AND SIMPLE.
FIND MORE OF OUR SERVICES:
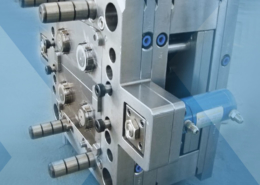
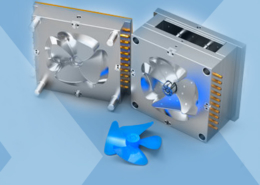
Plastic Molding

Rapid Prototyping
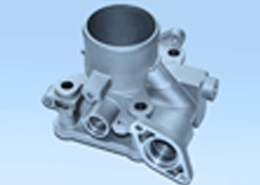
Pressure Die Casting
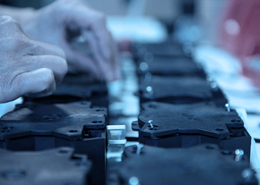
Parts Assembly
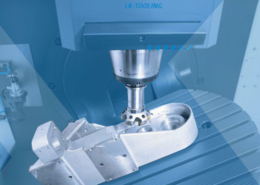