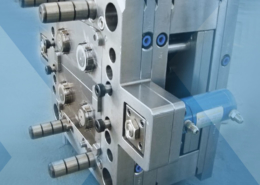
Using Aluminum for Injection Molds? - injection moulding aluminium
Author:gly Date: 2024-10-15
Acetal plastic is renowned for its exceptional mechanical properties, including high strength, stiffness, and wear resistance. Injection molded acetal parts can withstand significant loads and repeated use, making them ideal for applications that require durability and longevity.
Acetal plastic is resistant to many chemicals, solvents, and oils, making it suitable for applications where exposure to harsh environments is a concern. Injection molding allows for the production of complex geometries that can withstand these challenging conditions.
Yes, acetal can be molded into complex shapes with tight tolerances, thanks to its excellent dimensional stability and low shrinkage. However, proper mold design with draft angles is important for smooth part ejection.
Ready to take your product to the next level? BOYI injection molding services offer unmatched precision, dimensional stability, and strength for your high-performance parts. Whether you need durable gears, bearings, or custom components, our team delivers top-quality acetal parts with fast turnaround times and ISO-certified manufacturing. Contact us today to discuss your project needs!
This article provides a comprehensive overview of the acetal plastic injection molding process, its benefits, and considerations for successful implementation.
The design of the mold is critical to the success of the injection molding process. Factors such as mold material, gate location, and cooling channels must be carefully considered to ensure efficient filling, cooling, and ejection of the part.
Affordable high precision plastic molds and machined parts available for any order size | Contact our experts or engineers now for a quote!
For any questions or inquiry about Mold manufacturing/Injection molding/Over molding/Insert Molding/Die casting , please contact one of our knowledgeable applications engineers at [email protected]
While the initial investment in tooling can be significant, injection molding offers low per-part costs for high-volume production. The process is highly automated, reducing labor costs and improving production efficiency.
Regular quality inspection of the final products is crucial to ensure that they meet the required specifications. Inspection methods may include visual inspection, dimensional measurement, and mechanical testing.
Acetal plastic is a thermoplastic polymer with a repeating formaldehyde unit in its chemical structure. It comes in two primary forms: homopolymer (POM-H) and copolymer (POM-C). Both types offer excellent mechanical strength, rigidity, and low moisture absorption. However, homopolymer acetal generally provides higher tensile strength and better dimensional stability, while copolymer acetal offers improved impact resistance and chemical resistance.
While acetal plastic offers many advantages, it is important to select the appropriate grade for the specific application. Different grades of acetal plastic have varying properties, such as impact strength, wear resistance, and thermal stability.
No, acetal and Delrin are not exactly the same, but they are closely related. Acetal refers to a family of thermoplastics, including both homopolymers and copolymers, known for their strength and low friction. Delrin, a brand name by DuPont, is a specific type of acetal homopolymer with slightly superior mechanical properties and dimensional stability compared to generic acetal copolymers.
For any questions or inquiries regarding rapid prototyping, CNC machining, sheet metal fabrication, or vacuum casting, please contact coco at [email protected].
Precise control of the injection molding process parameters, including temperature, pressure, and timing, is essential for producing high-quality parts. Regular monitoring and adjustment of these parameters are required to maintain process stability and consistency.
Choose nylon if you need a tough, impact-resistant material that performs well under abrasive conditions and is more cost-effective. It’s suitable for applications where some dimensional changes due to moisture absorption can be tolerated.
Choose acetal if you need high precision, a smooth surface finish, and parts that maintain dimensional stability under varying conditions. It’s ideal for applications requiring low friction and high mechanical strength.
This table provides a comprehensive overview of Acetal Plastic’s key attributes and the critical injection molding parameters necessary for producing high-quality components.
Successful acetal plastic injection molding requires attention to several key factors to ensure high-quality, precise, and reliable parts. Below are the essential considerations for achieving optimal results in the injection molding process:
Selecting the appropriate grade of acetal for injection molding depends on the specific requirements of your application, including strength, stiffness, impact resistance, and temperature conditions. Celcon M90 provides a good balance for general applications, while the glass-filled acetals (RTP 800 GB 10 and 20) offer enhanced properties for more demanding environments.
Here’s a comparison table for acetal and nylon injection molding: This table summarizes which material excels in each category to help you decide based on your project’s specific requirements.
Acetal should be processed with a melt temperature of 190–230°C, a mold temperature of 80–110°C, and moderate to high injection pressure (700–1500 psi). Proper material drying (80°C for 2–4 hours) is also crucial.
Acetal homopolymer offers higher strength and stiffness, while acetal copolymer has better chemical resistance and thermal stability, making it suitable for applications exposed to hot water or chemicals.
Here’s a comparison of the key material properties for these grades of acetal, measured according to standard testing methods:
Acetal plastic has low moisture absorption, which minimizes dimensional changes due to humidity. This property, combined with the precision of injection molding, results in parts with tight tolerances and excellent dimensional stability.
Acetal plastic, also known as polyoxymethylene (POM), is a semi-crystalline engineering thermoplastic that boasts exceptional mechanical properties, chemical resistance, and dimensional stability. Its versatility and durability make it an ideal material for various applications, including automotive parts, gears, bearings, and consumer electronics. Injection molding, a highly efficient and cost-effective manufacturing process, is commonly used to produce acetal plastic parts.
Injection molding allows for the production of parts with complex geometries and intricate details. Acetal plastic’s good flow properties make it easy to mold into intricate shapes, opening up a wide range of design possibilities.
Yes, Delrin can be injection molded. Delrin’s ease of processing and ability to produce precision parts with tight tolerances make it suitable for a wide range of applications in industries like automotive, electronics, and consumer products.
This article was written by engineers from the BOYI team. Fuquan Chen is a professional engineer and technical expert with 20 years of experience in rapid prototyping, mold manufacturing, and plastic injection molding.
Common challenges include thermal degradation if the material overheats, difficulty in mold release due to acetal’s rigidity, and potential warping if the cooling process isn’t optimized.
Acetal stands out for its low coefficient of friction and high wear resistance, making it more durable than many other plastics, especially in parts that experience constant movement or friction.
Injection molding allows for the production of complex geometries and tight tolerances with high precision. This versatility enables the manufacture of intricate acetal plastic parts with intricate features, such as undercuts, threads, and ribbing, all in a single operation.
GETTING A QUOTE WITH LK-MOULD IS FREE AND SIMPLE.
FIND MORE OF OUR SERVICES:
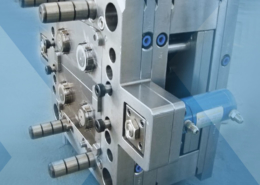
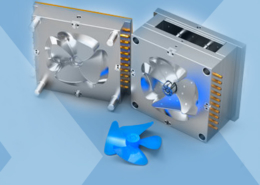
Plastic Molding

Rapid Prototyping
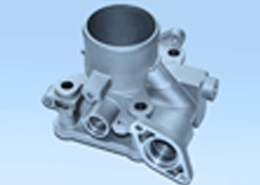
Pressure Die Casting
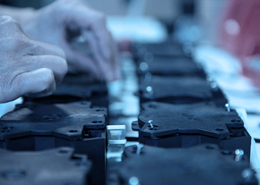
Parts Assembly
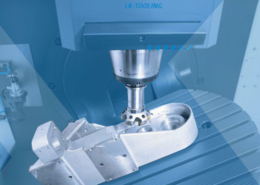