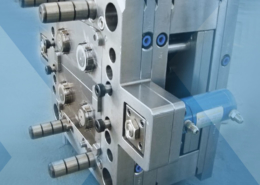
USA Manufacturer | Custom Injection Molding & CNC ... - injection mold manufactu
Author:gly Date: 2024-10-15
When SUMIKASUPER LCP is molded by injection molding, its molecules can be easily oriented in the flow direction due to shear flow. As a result, a molded product with high strength and modulus can be obtained, but at the same time, it must also possess anisotropy. It is important to pay close attention to how the flow pattern in the cavity will be when designing the mold.
Injection molding is a popular technology used by many household product manufacturers today. Some may be surprised that many everyday items they use are made using this technology. Everything from flower pots, packaging containers, phone cases and medical syringes are all injection molding products. Sometimes, these things make you wonder how to mold plastic at home.
These items are some of the most common products made by injection molding. Plastic glasses and cups are lightweight, durable and reusable, making them a practical choice for everyday use. In addition, these items can be designed for casual and formal use.
E = Excellent : Application examples to SUMIKASUPER LCP are available. G = Good : Applicable to SUMIKASUPER LCP. A = Average : There are no examples of application to SUMIKASUPER LCP. B = Bad : Not applicable to SUMIKASUPER LCP
Since the properties of SUMIKASUPER LCP molded products are highly dependent on the resin temperature during molding (cf. Figure 4-1-2), it is necessary to mold SUMIKASUPER LCP at an appropriate resin temperature. On the other hand, as the standard molding temperature for SUMIKASUPER LCP is extremely high (320 to 400°C), there may be a discrepancy between the setting temperature of the molding machine and the actual resin temperature. In this case, the potential of SUMIKASUPER LCP can not be fully utilized. In order to prevent such problems, it is recommended that the resin temperature in the cylinder be monitored. The actual resin temperature can be measured, for example, by using an infrared radiation thermometer that can measure the temperature of a small area.
During long-term continuous molding, resin can remain in dead spaces inside the molding machine, and the remaining resin may deteriorate or become colored. LCP can easily remain in such dead spaces since it has an extremely low melt viscosity. Therefore, when applying hot runners, it is necessary to pay sufficient attention to prevent black spots and cold slag caused by resin retention.
When you drop and break your remote control, sometimes it can make you wonder if it is worth learning how to mold plastic at home so you can fix it yourself. Many remotes we use at home are encased in injection molded plastic shells, providing protection for the electronic parts.
This is another one of the most common injection molding products people use daily. Many toothbrush handles are made using a thermoplastic polymer such as polypropylene. These materials are lightweight, durable, impact-resistant, recyclable and food safe.
SUMIKASUPER LCP can be molded using both the standard inline type and plunger (preplasticating) type of injection molding machines. However, for E5000 series, it requires a higher molding temperature (up to 420°C), and thus the injection molding machine with high temperature specifications (450°C) is required.
Injection molding allows manufacturers to create robust CD cases designed to protect and store compact discs and similar data storage items. These cases can be made using transparent or opaque plastic, which allows you to see or label each disc contained in the case. These materials feature a hinged design, allowing for easy access to the disc held within while providing protection from scratches and dust that can damage the item within.
Many packaging containers have plastic molded parts. The most common containers produced using this technology include storage boxes, cosmetic jars and food containers. These lightweight containers are designed to be stackable, making them easy to store and organize. They also feature secure closures, which ensure the safety of their contents. In addition, many of these packaging containers are made from recyclable materials.
As SUMIKASUPER LCP has a rapid solidification nature when cooled, it does not easily cause flashes during injection molding although its melt viscosity is very low. However, when molding ultra-thin-walled products (< 0.2mm), there are cases where the resin solidifies in the thin-walled part and sufficient flow length cannot be obtained. As a countermeasure in such cases, the injection molding machines with high speed and excellent injection response characteristics, such as electric injection molding machines or hydraulic injection molding machines with accumulators, are effective.
Injection molding technology allows manufacturers to create aesthetically pleasing features for your car’s interior and other parts. In addition, the process allows for the rapid production of complex shapes in various dimensions, which meet the high demands of the automotive industry.
Injection molding offers plenty of benefits for everyone, which is why it is the preferred manufacturing method for producing many everyday items:
Many toys and toy parts are made using injection molding technology. This technology is often used to produce toy figurines of various sizes. Manufacturers can produce intricate details and a wide array of designs and apply multiple colors. Due to their versatility and affordability, toy figurines have become popular among enthusiasts and collectors alike.
All-Plastics offers the latest injection molding technology. We create products in a zero-defect environment, increasing production efficiency while reducing production costs. Please fill out our online contact form to request a quote or ask a question.
Phone cases can have plastic molded parts offering essential properties such as scratch and impact resistance. They can be designed in various styles, allowing access to ports and buttons.
Injection molding plays a vital role in the field of medicine, where various items and pieces of equipment need to be designed precisely according to certain specifications. Syringes and other medical equipment undergo strict quality control in compliance with today’s medical standards.
Many parts of your car were manufactured using injection molding technology. This precise and accurate process can be used to make everything from the door knobs to dashboard components and interior trim pieces. Plastic car components are designed for heat resistance and durability.
The system must be capable of producing high levels of heating with a uniform temperature distribution. Heater integrated type is preferable. The manifold and nozzle temperatures should not be maintained too high. The areas coming into contact with the mold (gate areas) must be maintained at high temperatures.
(As shown above, when compared to general-purpose molding machine, the high speed molding machine provides the high injection speed in the initial period and thereafter molding is performed at the specified injection speed.)
The keys on your keyboard are manufactured using ABS plastic. It can be shaped into various forms and provide good tactile feedback.
As the weld strength of SUMIKASUPER LCP is lower than that of other engineering plastics, it is necessary to limit the number of gates to only 1 to 2 places and give careful consideration to where to locate the gate, in order to avoid the formation of welds.
Injection molding allows for the precise manufacturing of various parts of medical equipment. Manufacturers can produce thousands of these essentials to meet the needs of hospitals and other healthcare centers. Furthermore, this process can produce sterile components that are safe to use in different medical procedures.
GETTING A QUOTE WITH LK-MOULD IS FREE AND SIMPLE.
FIND MORE OF OUR SERVICES:
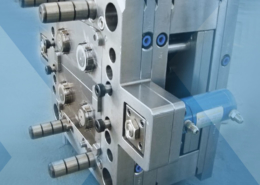
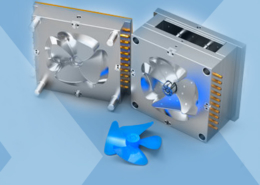
Plastic Molding

Rapid Prototyping
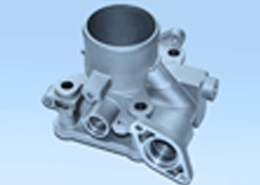
Pressure Die Casting
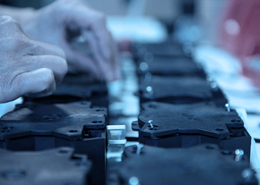
Parts Assembly
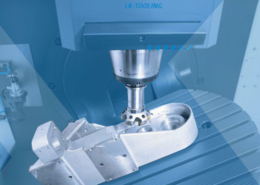