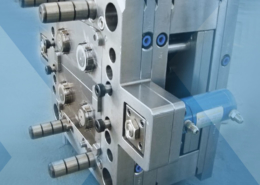
Upmold: Plastic injection mould maker | plastic injection ... - plastic injectio
Author:gly Date: 2024-10-15
Patents for cellulose acetate were first deposited by Solvay Acetow in 1911 – the year of the first Solvay Conference, prestigious meetings of the world’s leading scientists still held today. In recent years Solvay Acetow diversified its product portfolio based on its acetylation know-how.
As an international chemical group, SOLVAY assists industries in finding and implementing ever more responsible and value-creating solutions. The Group is firmly committed to sustainable development and focused on innovation and operational excellence. Solvay serves diversified markets, generating 90% of its turnover in activities where it is one of the top three worldwide. The group is headquartered in Brussels, employs about 29,000 people in 55 countries and generated 12.4 billion euros in net sales in 2012. Solvay SA SOLB.BE) is listed on NYSE Euronext in Brussels and Paris (Bloomberg: SOLB.BB- Reuters: SOLBt.BR).
At its core, thermolator injection molding relies on the principle of heating and cooling materials to facilitate the shaping of molds. Through a series of precise temperature controls and hydraulic mechanisms, molten materials are injected into molds, where they solidify to form finished products. This intricate process demands meticulous attention to detail and advanced technological infrastructure to achieve optimal results.
About Solvay SOLVAY ACETOW is a cellulose acetate tow leader in filtration applications for consumer goods as well as in plastic and textile. Acetow is a worldwide producer with five production sites and has almost a century of experience in his core competence acetylation. Its innovation strategy is based on two pillars: improving core business and diversification.
Unlike many bio-plastics, Ocalio™, as a cellulose acetate bio plastic, only uses wood pulp. An entirely renewable resource and thus does not compete for food resources. It also has a much lower CO2 manufacturing footprint when compared to petroleum-based products.
“Solvay has over a century of experience developing and manufacturing commodity and high performance specialty plastics and polymers and the addition of bio-plastics is a natural progression,” explains Marc Michels, Marketing Director Solvay Acetow. “Our company’s renewable chemistry platform studies the potential of bio-based chemistry with the objective of identifying opportunities for improving, advancing, and expanding Solvay’s existing product offering to meet consumer’s demanding expectations in an evolving society.”
In conclusion, thermolator injection molding represents a paradigm shift in modern manufacturing, offering unparalleled precision, efficiency, and cost-effectiveness. By understanding its principles, advantages, and challenges, manufacturers can leverage this transformative technology to achieve sustainable growth and competitive advantage in an ever-evolving global market.
One of the primary benefits of thermolator injection molding is its ability to produce intricate and precise components with minimal margin for error. By maintaining consistent temperature profiles throughout the molding process, manufacturers can achieve unparalleled levels of accuracy and repeatability, ensuring uniformity across production batches.
Despite its efficiency and precision, thermolator injection molding raises environmental concerns related to energy consumption and material waste. The energy-intensive nature of heating and cooling processes contributes to carbon emissions and resource depletion, highlighting the need for sustainable manufacturing practices and renewable energy sources.
Compared to traditional molding techniques, thermolator injection molding offers significantly faster cycle times, allowing for higher throughput and increased productivity. The precise control of temperature parameters minimizes downtime associated with cooling and reheating, enabling continuous operation and swift turnaround times.
Thermolator injection molding stands at the forefront of modern manufacturing, offering innovative solutions to streamline production processes across various industries. This article delves into the intricacies of thermolator injection molding, shedding light on its significance, functionality, and implications for the manufacturing landscape.
Maintaining consistent quality standards is paramount in thermolator injection molding, given the criticality of temperature control in the molding process. Deviations from optimal temperature ranges can result in defects and imperfections, compromising product quality and reliability. Implementing robust quality assurance protocols is essential to mitigate such risks and ensure compliance with industry standards.
Despite the initial investment required for implementing thermolator injection molding systems, the long-term cost savings are substantial. By optimizing material usage, reducing scrap rates, and enhancing production efficiency, manufacturers can achieve significant economies of scale, ultimately driving down per-unit costs and enhancing profitability.
Thermolator injection molding is a sophisticated manufacturing technique that involves the precise control of temperature during the injection molding process. By maintaining optimal temperature conditions, thermolators ensure the uniformity and quality of molded products, significantly enhancing efficiency and reducing production costs.
“When compared with other bio-plastics, Ocalio™ plasticized cellulose acetate displays an exceptional balance of properties providing better mechanical and heat resistance, enhanced transparency and outstanding processability,” says Louis Cozzari, Business Development Manager Solvay Acetow. “It can be easily moulded and is designed for a wide range of consumer goods end-use such as containers for cosmetics and personal care, food packaging,electronic devices, toys and mobile phones.”
Brussels, October 16, 2013 — Solvay today announced the introduction of Ocalio™ cellulose acetate bio-plastic manufactured using wood pulp, an entirely renewable resource obtained from SFI(1) certified forests. This new and amorphous engineering bio-plastic is a non-toxic material.
In addition to the beneficial range and balance of mechanical properties and ease of processing, Ocalio™ plasticized cellulose acetate displays excellent surface aesthetics such as a high gloss, smooth and silky tactile qualities and an exceptional depth of colour, for both opaque and transparent grades.
The evolution of thermolator injection molding can be traced back to the mid-20th century, with advancements in materials science and engineering driving its development. Initially utilized in the production of plastic components, thermolator injection molding has since expanded its applications to encompass a diverse range of industries, including automotive, electronics, and medical devices.
While thermolator injection molding offers numerous benefits, its implementation presents inherent challenges, particularly regarding technological complexity. The integration of temperature control systems, hydraulic actuators, and precision molds necessitates sophisticated engineering expertise and substantial capital investment.
Manufactured in Europe in back integrated and completely self-sufficient facilities, Ocalio™ cellulose acetate compounds will be commercially available in Q1 2014.
With technical properties and performance more than comparable to oil-based plastics, Ocalio™ cellulose acetate compounds can not only replace applications made with engineering plastics such as polymethyl methacrylate (PMMA) and acrylonitrile butadiene styrene (ABS) but also polycarbonates (PC).
As manufacturing technologies continue to evolve, the role of thermolator injection molding is poised to expand further, driving innovation and efficiency across diverse industries. By embracing advancements in materials science, automation, and sustainability, manufacturers can harness the full potential of thermolator injection molding to unlock new opportunities and address emerging challenges.
GETTING A QUOTE WITH LK-MOULD IS FREE AND SIMPLE.
FIND MORE OF OUR SERVICES:
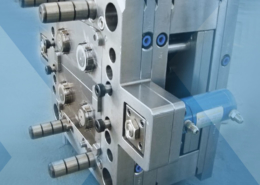
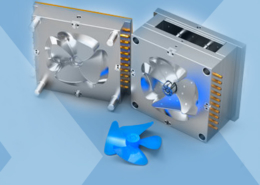
Plastic Molding

Rapid Prototyping
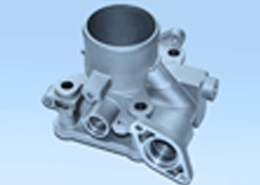
Pressure Die Casting
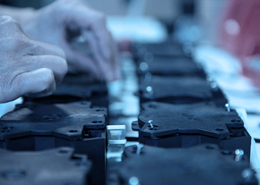
Parts Assembly
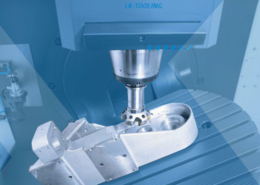