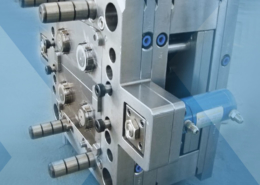
Universal Plastic Mold: Plastic Injection Molding - Full-Service ... - plastic m
Author:gly Date: 2024-10-15
This in turn manufactures the product at a cost-effective price, low lead time and also helps to develop the product more consistently as it reduces and can also completely eliminate manual assembly.
At VEM Tooling, we understand that 2K molds are complex and need a high level of expertise. We are equipped to help you with the 2K injection molding process in order to effectively reduce assembly time, combine various material properties and finally, develop a strong connection between the materials in order to deliver high quality products that are durable.
At VEM Tooling, we understand the importance of following regulations to meet quality. We build molds within our unit which is why we have complete control over steel quality and testing of the molds. This enables us to incorporate all the experience that we have gathered over the last 20+ years now, in 2K molds.
The 2K injection molding process is incorporated when you want the plastic parts of your product to be formed out of two materials to improve the use case and the aesthetics of the product. These 2 materials could be either of different colors or different textures thus, giving you a wide variety of options to customize your product.
The chemical bonding between the two components is due to 1 of the following reasons: The components either merge into one another or the first component is designed such that the second component bonds mechanically to the first.
VEM Tooling is committed to providing our clients with the best end result of the product. At VEM, we emphasize upon delivering a high-quality product at low manufacturing costs and low lead times.
PEEK is widely regarded as one of the best performing thermoplastic materials on the market. PEEK is a semi crystalline thermoplastic with excellent wear resistance, chemical resistance, and hydrolysis resistance. In many cases, additives are not required. PEEK injection molded products have been widely used in fields such as aerospace, automotive industry, electronics and electrical, and medical machinery.
In addition to the various aesthetic possibilities and advanced design options, another advantage of the 2K Injection molding process is that it also designs for assembly which is why an assembly step can be eliminated.
We support product developers that require 2K injection molding services with end to end solutions. We support them with both, precise, high-quality 2K molds and 2K injection molding services.
Our manufacturing experience and input during an early product design phase has helped our clients to save upon resources and time.
2K Injection molding services can be used to improve the aesthetics of a product to make it more appealing to the end consumer. They can also be used to design and integrate multiple features into your products. Thus, 2K technologies can drastically reduce part costs and improve quality for mass production.
The temperature of PEEK injection molding is about 320~390 degrees; Drying temperature 160-185, 5H-8H; The temperature of the injection mold is 140~180. The molding temperature of this material is too high, which can cause serious damage to the screw. When setting the screw speed, the speed should not be too fast. After the molding is completed, the screw should be quickly cleaned with PE wax, and the PEEK material should not stay on the screw, otherwise the damage to the raw materials for secondary heating of the internal structure will be more severe. When choosing PEEK material for injection molding screws, it is essential to use high-quality alloy screws.
By partnering early during the product design phase development, we have eliminated common errors and mitigated redesign issues that may arise due to complexities thus, we encourage manufacturers to partner with us during the product design phase stage.
Standardization and quality are part of our companies core values. We deliver the best possible experience and product to our customers, every single time consistent. Take a look at our certificates!
We have the expertise, technical knowledge and skill-set to combine plastics to build aesthetically appealing products that have excellent adhesion. This is achieved by combining different materials that have a strong chemical bond between them thus, increasing the durability of the product.
Since we do not outsource molds and build them in-house, we eliminate the layer of communication mistakes that you might have often experienced with out-sourcing.
VEM’s Tooling Factory encompasses an extensive industry experience in terms of developing an aesthetically pleasing product keeping the technicalities of the manufacturing standards in accordance.
By building in-house molds, we can also ensure better lead times and incorporate any type of minor or easy modification that the mold may require. We are also up to date with drawings and if required, we can also incorporate corrections in the mold and provide you with spare parts.
To better understand how VEM Group can help you with the 2K injection molding process, contact us or request a quote today. We are looking forward to becoming your trusted tooling supplier and injection molding partner.
The chemical bonding between the two materials provides an excellent adhesion thus, the 2K injection molding process enables us to integrate with multitude options.
GETTING A QUOTE WITH LK-MOULD IS FREE AND SIMPLE.
FIND MORE OF OUR SERVICES:
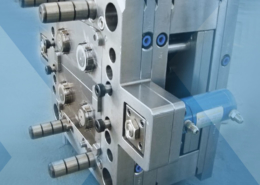
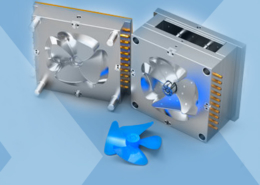
Plastic Molding

Rapid Prototyping
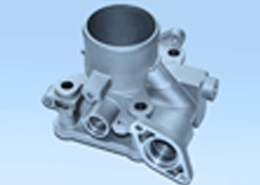
Pressure Die Casting
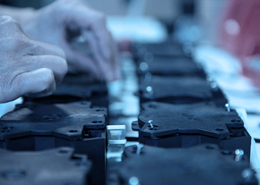
Parts Assembly
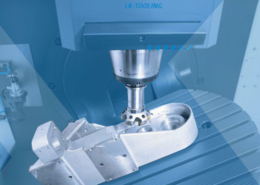