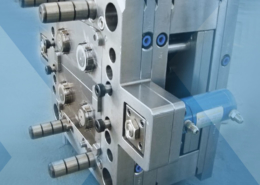
Understanding the Intricacies of Side Action Injection Molding ... - complex inj
Author:gly Date: 2024-10-15
The shortest achievable cooling time will be determined by how quickly heat can be transmitted at each stage of its journey; thus, the shortest achievable cooling time will be determined by the slowest stage. Because plastic is a poor thermal conductor, the first stage represents a bottleneck in the transfer of heat; the only method to speed up heat conduction is to lower the cavity wall temperature.
Traditional cooling channels are unable to precisely follow the geometric features of items and hence have a limited cooling effect. Conformal cooling channels, on the other hand, provide homogeneous cooling and are especially useful in complex molds.
Because conformal cooling channels are not constrained by standard cooling procedures, they can be constructed with great freedom. They meticulously adhere to the product profile to successfully address the issues of dead zones and heat accumulation. This benefit is especially noticeable when the channels are used for geometric goods.
To figure out how much each molding will cost, do the following: The cooling time in injection molding is included in the overall cycle time, which is used to calculate the molding cost.
Molds with conformal cooling channels are made using laser sintering, which is costly and consequently not widely utilized in general industries. Despite their high cost, conformal cooling channels are increasingly being employed because they can significantly shorten cooling times and improve molding operations quality.
As a company, Rosti has traditionally taken a conservative financial approach that allows it to operate from a position of stability and become a dependable partner to its customers even during a crisis. This approach continues to this day, with its secure position being bolstered by its relationship with Nordstjernan, a Swedish family-controlled, ethically strong, long-term investment company. In addition to its financial strength, Rosti has years of institutional and operational experience which makes it one of the most sought-after companies for plastics injection moulding and contract manufacturing. “Since 1944, we have succeeded by operating with integrity, excellence, and in close relationships with our partners. We have prospered for 75 years, and we intend to continue for at least another 75,” opines Mark.
Any additional cooling is ineffective (or barely effective) and will merely increase the cycle time unnecessarily. Finally, analytically predicting the required cooling time for your part can assist you to prevent both excessive and insufficient cooling time.
Quality control: Parts are inspected on-site to ensure appropriate manufacture and quality. Inadequate cooling time can result in part faults and rejections, which we will discuss momentarily.
The Healthcare Insights is a comprehensive guide to all things related to healthcare. We specialize in producing quality content for our readers on both digital and publication platform… Read More
Two years ago, Rosti invested 1MEUR into a new innovation lab in Asia and has recently made a second 1MUER investment and built a further innovation lab in Europe. It has also recently expanded into North America where a third innovation lab is being built. Rosti’s state-of-the-art innovation labs help to bring concepts to reality in just 72 hours. Each lab has a dedicated team of engineers who combine technical and production expertise to support customers in agile development programs that deliver ideas to market more rapidly and cost-effectively than traditional technologies.
According to Mark, Rosti’s greatest strength lies in its people that are open to walk the extra mile to fulfill customer expectations. Hence, the company strives to empower its employees by providing them with an exciting work environment, along with many opportunities for professional and personal development.
Mold cooling, as seen above, plays a significant role in injection molding cooling time. Mold design is also important in this case: Cooling channels may and should be incorporated into the mold wherever possible to aid in more efficient heat distribution.
Cooling time is an essential aspect of the injection molding cycle that consumes the majority of the cycle time. It has a significant impact on the end product/ service, and it is not an aspect where you should joke around taking shortcuts. Adequate cooling time is not just important for part quality; it is also the most time-consuming element of an injection molding cycle.
Traditional cooling is ineffective because it does not conform to the geometric outline of a product, limiting its cooling impact. Conformal cooling, on the other hand, produces an even cooling effect and exhibits its advantages in the case of complicated models.
To assist us in designing the mold’s cooling system: We need to know how efficient the cooling system needs to be to remove a specified amount of heat energy from the molten polymer in a given amount of time.
Ejection: Once the material has cooled and set enough to keep its shape, the part can be expelled using the mold ejector pins.
Heating of resin: The base resin is heated to temperatures that liquefy it and takes it to the proper viscosity and mass flow for injection during this initial stage.
Cooling channels of an injection mold cooling design should be placed as close to the surface of the mold as possible to reduce the amount of energy used to cool the mold while increasing the amount of energy used to cool the part. The goal of cooling is to solidify the part as soon as feasible. Using cooling effectively not only saves cycle time but also energy consumption.
Rosti’s history of precision plastic injection moulding solutions roots back to 1944 when it began the production of buttons through injection moulding, shortly after the Second World War. This innovative and relatively new method provided increased production at a lower cost compared to conventional press moulding. Over time, the company grew and in 2010, its industrial division with activities in Europe and Asia was acquired by Nordstjernan, a Swedish family-controlled investment company and one of Sweden’s largest industrial conglomerates.
Before we get into the issue of cooling time, let’s go over the procedure. To dissolve plastic resin for injection, an extremely high temperature is needed, and the cooling process could take up to four-fifths of the cycle time, if not longer. The temperature altering steps leading up to the final output are represented by the following plastic injection molding elements:
ACIS®, Autodesk Inventor®, CATIA® V5,Creo™ Parametric, IGES, Parasolid®, Pro/ENGINEER®,Siemens PLM Software’s NX™, SolidEdge®, SolidWorks®, STEP
Cooling time can be determined using an equation that involves wall thickness and the thermal conductivity, density, and energy needed to increase the temperature of the plastic. The projected time is also determined by the choice of thermoplastic used, as each has a distinct melt and mold temperature. This is a complex equation, but if you’re working with an experienced injection mold manufacturer, they’ll be familiar with it.
Medical and life science products play a critical role in the health, safety, and wellbeing of patients. As such, ensuring the quality of the products and the components throughout the manufacturing process starting from design to final inspection is essential. Therefore, it is vital to partner with a reliable plastic injection mould company that emphasizes on quality and creates safe and durable products. One such prominent company that is dedicated to providing optimal injection moulding services for each and every part of the production process, from concept development all the way through to delivery with the highest levels of accuracy and reliability is Rosti. Founded in Denmark by two industry veterans, Rolf Fahrenholtz and StigJørgensen, Rosti Group is a global injection-moulding company and contract manufacturer to some of the world’s leading manufacturers in the packaging, consumer appliances, business machines, home automation, medical and automotive sectors. Its ISO 13485 Medical facilities, ISO 14644-1 certified classroom, solid quality systems, and robust and validated precision manufacturing processes make it a global, agile, and trusted partner for many producers of life science devices. The production environment at Rosti includes ‘white rooms’ to certified cleanroom class 8 environment (ISO-14644-1) to meet specific customers’ requirements. Each of its products is designed and manufactured to meet the highest standards in safety, quality, and environmental sustainability. Such utmost level of care and attention to detail makes it ideally optimal for life science product manufacturing and packaging.
There are a variety of considerations you need to look into while developing or contracting injection molding services. If you need any help, please contact us to get professional plastic injection molding service.
The above-mentioned process details each requirement of the injection molding cooling process. And it cannot be emphasized enough that cooling time in plastic injection molding must not be hurried despite taking up a large portion of the cycle time. To develop a cooling time that results in maximum manufacturing speed, a blend of patience, precise mould design, and precise mathematics is required.
The most serious problem that improper or insufficient injection molding cooling time may cause is faulty and rejected parts. Parts that have not yet hardened sufficiently to keep their shape will most likely be damaged by the firing of the ejector pins.
Cooling typically accounts for 80 to 85 percent of total cycle time. When you realize that the cooling portion of the cycle is the inverse of the enormous amount of heat necessary to liquefy the plastic resin during the injection process, the 80+ percent figure sounds reasonable.
New cooling approaches, including conformal cooling and pulsed cooling, enable cooling channels to be more effectively dispersed throughout the mold, resulting in lower cooling loads, cooling periods, and cycle times. Conformal cooling can also be used in conjunction with evaporative cooling to significantly minimize the cooling demand.
Injection molding cycle time is a crucial component in the efficacy of mold manufacturing process, and hence a huge influence on the cost and bottom-line consequences of any injection molding project you undertake. In short, the faster your cycle time (while keeping an acceptable degree of quality), the more components you can make with less machine time and the cheaper your overall expenses.
Packing and holding: Injection continues as some of the previously injected material cools and shrinks. The pack/hold stage injects extra material into the cavity to ensure that it is filled, and then “holds” the material in place to prevent backflow.
It’s not just the manufacturing, technological, and management capability that put Rosti ahead of its competitors. It’s the way the company brings value to its customer through active listening and supporting them to overcome their current and future challenges is what makes it a go-to partner in the market. Along with accredited facilities, state-of-the-art equipment, and experienced people, Rosti also brings passion, a medical mindset, innovative thinking with a long-term partnership, and a high customer focus mentality. “At Rosti, we emphasize certain core values: passion, integrity, partnership, and excellence. We invest in our people, in our systems, and in innovation to maintain a competitive advantage in our industry. Our ethos is to bring customer solutions from Concept to Reality,” asserts Mark.
Another thing to keep in mind is that proper cooling temperature does not imply attaining, say, room temperature or being cold to the touch. A part should only be cooled when it retains its shape and can be securely extracted from the mold.
Cooling: The cooling stage is deemed to have commenced once the packing/holding stage is completed. Although the material starts to cool as soon as it leaves the heating injection nozzle and penetrates the mold cavity, cooling time should only be determined after packing and holding. The liquefied resin begins to re-solidify and take on the shape of the mold cavity at this time.
Cooling time in plastic injection molding must not be hastened despite taking up the bulk of the cycle time. Patience, mold design, and precise calculations are required. For the sake of simplicity, it is assumed that cooling begins only when the mold has been filled. It is also expected that at the start of cooling, the melt has the same temperature throughout the cavity and that the cavity wall temperature remains constant throughout the cooling process.
If you evaluate the heat pathway in the cooling process: from the material to the mold, to the ambient surrounding environment, the need for proper mold cooling becomes clear. Efficient mold cooling equates to effective overall cooling.
If cooling channels are incorporated into the mold’s design, they can aid in heat dissipation and lower the temperature of the cavity wall, resulting in even cooling. Excessive cooling, on the other hand, might result in an unacceptably long cycle time, which is why molding producers must be capable of precisely calculating cooling time.
Speaking of the positive impact of the acquisition, Mark Wrigley, the Executive Vice President of Sales and Marketing at Rosti affirms, “Ownership has provided us with the benefits of resources, financial security and the solid reputation of both past and present partners. In turn, this provides our customers with security and peace of mind.” Today, Rosti stands tall as an international organization, with about 3000 employees working at production sites and offices across Europe and Asia.
While the injection molding cycle time is a significant contributor to your company’s overall performance, it is a procedure that should not be rushed. This article aims at providing a deeper understanding of the injection molding cycle and how injection mold cooling affects the overall outcome of the process.
When cooling is not done properly, the plastic portion does not firm sufficiently, resulting in injection molding defects from the firing ejector pins. The cooling process can be influenced by the design of a mold, resulting in enhanced shrinking, sinking, discoloration, warping, and delamination.
Improper or insufficient cooling, as well as improper mold design, can result in part faults such as warping, shrinking, sinking, and other issues. A consistent, well-engineered cooling rate is one of the most important actions you can take to improve the quality of your completed products and lower your failure rate.
“We are an agile, resourceful player that is big enough to deliver on large-scale projects, yet small enough to focus on flexibility and care to meet all your needs. From single components to finished goods, Rosti offers a diverse portfolio of services. With precision, performance, flexibility, and care at the core of everything we do, Rosti is shaping a brighter future,” concludes Mark.
The base resin is liquified by being exposed to high temperatures, and after melting to the suitable viscosity, it is poured into the mold.
GETTING A QUOTE WITH LK-MOULD IS FREE AND SIMPLE.
FIND MORE OF OUR SERVICES:
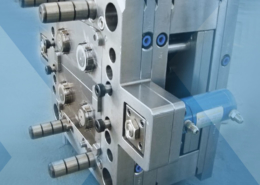
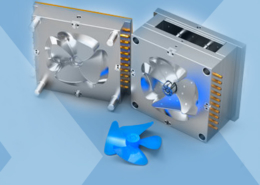
Plastic Molding

Rapid Prototyping
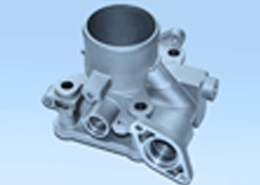
Pressure Die Casting
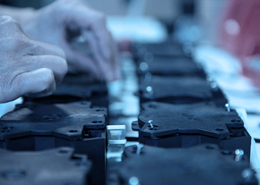
Parts Assembly
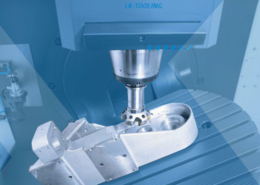