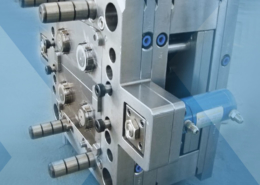
Understanding Insert Molding vs. Overmolding - overmolding injection molding
Author:gly Date: 2024-10-15
Certifications on all shipments: Drake Plastics provides a Certificate of Conformance with all products regardless of polymer composition at no charge. Special testing is also available at a reasonable cost.
High-Density Polyethylene (HDPE) is a thermoplastic polymer known for its high strength-to-density ratio. It's produced from petroleum and exhibits excellent resistance to chemicals, impact, and moisture, making it suitable for various applications, including packaging, pipes, and injection-molded products.
Our production team’s ideas have a major impact on our reputation for superior quality. Among their initiatives: dedicated dryers for each resin to avoid cross-contamination. And they know purging can’t eliminate all residue after a run, so they do a full tear-down, polishing the screw and cleaning all components that contacted the melted polymer in the prior run before starting the next job.
High-Performance Polymer: HDPE 8000F stands out as a high-performance grade, primarily due to its excellent stress crack resistance. This property makes it an optimal choice for manufacturing chemical containers, outdoor equipment, and products exposed to challenging environments.
Optimized Heat Deflection: With a heat deflection temperature of 85°C, HDPE 5000S is apt for applications with elevated temperatures. It produces kitchenware, automotive components, and products exposed to moderate heat sources.
Diverse Industrial Applications: HDPE 7000F's combination of properties makes it versatile for various industrial applications. It is used to craft large storage containers, material handling equipment, and industrial machinery components that withstand heavy loads and harsh environments.
Enhanced Flow: HDPE 6000F's improved melt flow characteristics make it a prime choice for manufacturing intricate components with complex geometries. Its versatility applies to applications like thin-walled parts, including intricate automotive components and electronic enclosures.
Excellent Impact Resistance: This grade's Izod impact strength of 30 J/m ensures resilience against impacts and shocks. It finds relevance in creating toys, household items, and industrial components that require impact resistance to withstand rough handling or accidental drops.
Low Shrinkage and Dimensional Accuracy: HDPE 8000F's low shrinkage rate of 0.8% enhances its ability to maintain precise dimensions during cooling.
Annealing PEEK and other ultra-high performance thermoplastic parts: Drake has extensive experience in annealing to relieve internal stresses that can impair a part’s properties or cause it to deform over time. Residual stresses occur as an advanced polymer rapidly transitions from its hot melt phase to ambient temperature. This is especially problematic for parts with heavy or varying cross-section thicknesses that cool at different rates. Annealing under controlled conditions resolves this: by heating parts above the advanced polymer’s Tg or softening point, then cooling very slowly to a point below its Tg, the polymer chains relax uniformly, relieving residual stresses. Drake offers annealing on a custom basis. It is often utilized for injection molded parts that require exceptional dimensional stability or a crystallinity level that maximizes the polymer’s strength, toughness and chemical resistance.
Mechanical Strength: With a tensile strength of 27 MPa and a flexural strength of 45 MPa, HDPE 6000F offers solid mechanical performance. It's an excellent fit for creating industrial components, agricultural equipment, and structural parts that demand a blend of strength and reliability.
Drake Plastics’ Quality Management System is certified to the worldwide aerospace industry’s AS9100D(2016) as well as ISO 9001:2015 standards. These stringent requirements apply to all products we manufacture. Our ability to meet these standards stems in large measure from our team’s experience and their commitment to achieving the highest attainable levels of quality. We also support our team by investing in the best inspection technology available, including:
Precision injection molding ultra high-performance plastics demands a solid understanding of each polymer’s unique behavior to avoid degradation and achieve optimum property and quality levels. Its melt characteristics and flow behavior must be factored into process conditions and hardware designs to preserve physical properties and achieve consistent quality in the high-pressure and high-temperature molding process.
Many customers describe our facility as the cleanest and most efficient they’ve experienced. Our all-electric injection presses yield precision parts from 0.03 to 20 oz. (0.85 to 570 grams). They use no hydraulics, adding to the cleanliness of our operation. Each machine is also equipped with a unique capability to compress or ‘coin’ parts during the molding cycle, enabling us to injection mold very heavy cross-sections without porosity or voids.
Our reputation as specialists stems from the millions of parts we’ve supplied in unfilled, glass, carbon fiber, bearing and wear grades of advanced polymer materials including:
Drake offers a diverse menu of services and capabilities to meet customer-specific requirements and industry compliance standards for injection molded parts. They include:
Moderate Tensile Elongation: HDPE 7000F's tensile elongation of 500% balances flexibility and strength, making it suitable for products requiring a blend of both attributes. This property is advantageous for producing hoses, tubing, and flexible containers.
Balanced Impact Resistance: An Izod impact strength of 35 J/m ensures robust resistance to impacts and shocks. This property is ideal for crafting items like safety equipment, consumer goods, and housings for power tools.
Drake’s process technology includes In-cavity pressure transducers and RJG Systems that monitor process parameters inside the mold cavities to maintain ideal conditions. This important control leads to high quality and exceptional repeatability in every Drake injection molded part equipped with RJG.
Near-net shapes provide an efficient, economical bridge between machining low part quantities from stock shapes and molding high volumes that require a significant investment in tooling. These forms or blanks are molded in low-cost tools and approximate the part’s as-designed dimensions. They are then machined to exact part dimensions. Using near-net shapes when production requirements reach the right levels yields a major savings in material vs. machining from rod or plate.
Enhanced Stiffness: Boasting a flexural modulus of 1300 MPa, HDPE 7000F excels in applications that demand stiffness and structural integrity. It is ideal for creating items like furniture, automotive components, and machinery parts where robustness is essential.
Post-curing Torlon PAI parts: Every Drake-produced Torlon PAI product goes through an engineered post-curing processes, a key factor in realizing the full performance potential of this advanced polymer. This final step before shipment achieves Torlon PAI’s typical core Tg (glass-transition temperature) midpoint value of 540°F (282°C). In our decades of experience with the material, we’ve optimized curing cycles to produce Torlon PAI parts to achieve maximum structural strength, toughness, and resistance to wear and chemicals.
Superior Impact Strength: With an Izod impact strength of 50 J/m, HDPE 8000F ensures exceptional resilience against impacts and shocks. It finds relevance in creating challenging and durable items like tool cases, industrial bins, and protective equipment.
Dimensional Stability: HDPE 5000S exhibits low shrinkage (1.5%) and maintains its shape during cooling, contributing to the accurate and consistent production of precision parts.
The best production and quality practices deliver maximum value to customers only when backed up by consistently exceptional service. Drake’s customer-centric culture is evident in our rapid response to requests for information, support and problem-solving. Drake’s on-time delivery performance is 98% or better. Our team sets 100% customer satisfaction as the norm and sustaining it determines our ongoing service-based investments.
Drake invests in the best available molding and process equipment and control technology for materials like Torlon PAI, PEEK, Ultem PEI and other high-performance polymers. Our production team also takes extreme measures to achieve the highest levels of quality and performance in molded parts.
Elevated Heat Deflection: Featuring a heat deflection temperature of 100°C, HDPE 8000F is ideal for applications subjected to higher temperatures. It produces parts for automotive engine compartments, outdoor fixtures, and products with moderate heat exposure.
Elevated Heat Deflection: HDPE 6000F's heat deflection temperature of 90°C makes it suitable for applications that face moderate thermal challenges. It is employed in crafting items like automotive interior parts, kitchen utensils, and electrical components that withstand elevated temperatures without deformation.
Balanced Strength and Flexibility: HDPE 5000S combines a commendable tensile strength of 30 MPa with a high elongation of 600%, rendering it suitable for manufacturing durable yet flexible products.
Drake’s extensive in-house molding and machining capabilities combine to offer customers molded parts with complex geometries and features not possible with injection molding alone. Precision finish-machining adds deep undercuts, side or angled holes or ports, zero or negative draft sidewalls and other design elements that are impossible or impractical to mold. Our CNC machining also yields tighter part tolerances than can be achieved in molding. For example, machined feature tolerances on a molded part can be held to +/-0.0005 inch (+/-0.02mm).
High Molecular Weight: With an elevated molecular weight, HDPE 7000F offers improved mechanical properties and durability. It finds application in crafting industrial components, tanks, and agricultural equipment that require enduring performance under demanding conditions.
With decades of experience in melt-processing ultra high-performance thermoplastics, injection molding specialists, Drake Plastics has fine-tuned process conditions, designed and built specialized components for our molding equipment and invested in the technology needed to produce consistently high-quality injection molded parts in Torlon PAI, PEEK and similar advanced polymers.
Drake Plastics’ support capabilities can be especially beneficial to customers transitioning from a machined plastic or metal component to injection molding:
Insert molding integrates functional metal components into injection molded parts during the molding process. The inserts are fixed in the mold cavity, and the polymer melt flows around the metal component as the molding process takes place. Electrical conductors, threaded fasteners, structural reinforcements and protective caps made from titanium, stainless steel and other metals are only a few of the possibilities for insert molding, and the technique is incorporated into many high-performance parts made from the advanced polymers Drake routinely molds. Other advantages include reduced assembly time in the customer’s operation and more secure integration of the molded-in metal component in the part.
GETTING A QUOTE WITH LK-MOULD IS FREE AND SIMPLE.
FIND MORE OF OUR SERVICES:
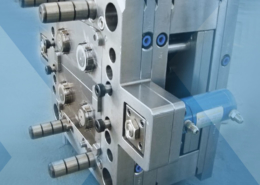
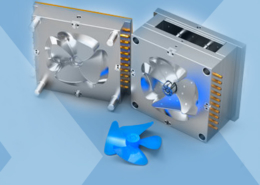
Plastic Molding

Rapid Prototyping
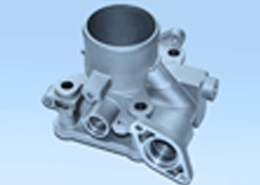
Pressure Die Casting
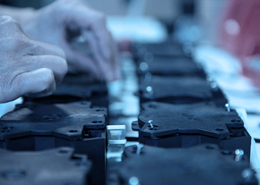
Parts Assembly
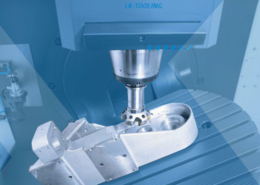