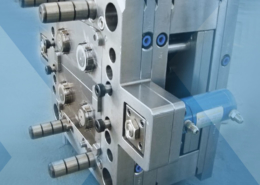
Understanding Injection Molding Cost for Manufacturers - injection molding mold
Author:gly Date: 2024-10-15
Want to learn more about plastic injection molding and why it may be the right choice for your product? Contact our production team here at Star Rapid® for a free project review.
A more demanding quality management system for products and services related to medical devices. Setting the bar just a little higher!
Get 7-day standard lead times on simple parts between 0.5 in. x 0.5 in. and 4 in. x 3 in. Upload your part to see if it’s eligible.
This depends on the complexity of the tool design and the type of material the tool is made from. Generally speaking, a very basic square shape made from relatively soft steel such as P20 can be made in less than one week. Very hard steels take longer to cut and to heat treat, while complex shapes or advanced surface textures can require three or more weeks to prepare.
At the tip of the barrel, a nozzle injects the liquid resin into the cavity of the mold. Once the plastic is then cooled and solidified, the mold opens and the finished part is ejected.
Using a multi-cavity mold can be more expensive than using a single-cavity mold, but it can also be faster and more efficient. If you need a large number of parts, or if your part is complex and has many features, a multi-cavity mold may be the best option.
We make tools and dies from S136H, 2316H, H13 hardened, 2316H, P20, 8407, and NAK80 semi-hardened steels. We offer standard SPI finishes, EDM texturing, and several different types of etched textures. We also have thousands of thermoforming plastics available – contact us for details.
As part of our design analysis, we’ll indicate any areas that might produce thermal stress, shrinkage, warping, or other avoidable defects in your injection molded parts. For more information, consult our manufacturing design guide on common defects and how to avoid them.
All orders are carefully reviewed by our tooling engineers to provide design for manufacturing optimization. We also work closely with outside design consultancies who can offer expert advice on the process of moving a product from the concept stage to production-ready.
Even small optimizations add up significantly over production lifetimes. An experienced molder provides valuable guidance.
The size and complexity of the mold are perhaps the most important factors in determining its cost. A simple mold for a small object may only cost a few hundred dollars, while a more complex mold for a larger object could cost several thousand.
When considering the size of a plastic mold, it is important to take into account the reasonable price for the project. Depending on the desired outcome, the size of the mold may need to be changed in order to accommodate for different parts.
If the mold is made of a more expensive material like titanium, then the price will increase as well. Also, if the mold is being produced in large quantities, then it will be less expensive per unit. The lead time should also be considered.
The finest production mold tools start with quality raw materials, strict process control, and expert toolmakers. Only a supplier with years of experience supporting Fortune 500 companies can ensure repeatable results for your production tooling needs. Here are some of the advantages that Star Rapid offers for high-volume production tool making and injection molding services.
There are a few ways to eliminate undercuts, but the best way is to design the part so that it can be molded without them. This can be done by using symmetrical geometry, designing bigger draft angles into the part, or using core pins.
If you’re looking for a way to save on production costs, you may want to consider using overmolding plastic mold. Overmolding is a process that allows you to mold two or more different materials together, which can help reduce waste and eliminate the need for separate assembly processes. Additionally, overmolding can improve the strength and durability of your products.
Our molding service is strengthened by our extensive expertise and a wide range of production capabilities. Our industry-leading facilities allow us to handle projects ranging from micromolding (10 tons) to large projects over 500 tons. This means we’re capable of producing parts ranging from millimeters to cubic meters in size. Our production of such a wide variety of parts enables us to best meet your needs. Further, we have unique access to tooling experts with decades of experience. They are available for video conferencing and customer support. We’re united in our efforts to help you have a satisfactory injection molding experience!
The cost of a plastic injection mold has changed significantly over time. In the early days of injection molding, the price of a mold was very high. This was due to the fact that the process was new and there were not many companies that knew how to build molds.
There are a few things to keep in mind when designing self-mating parts for injection molding. First, the part must be designed so that it can be easily removed from the mold. Second, the part must be designed so that it can be assembled and disassembled easily. Third, the part must be designed so that it can mate with other parts without any gaps or other problems.
Once a tool is made, plastic injection molding is the fastest and most cost-effective way of manufacturing hundreds of thousands of finished plastic parts. Molded parts have excellent surface finishes with reliable and repeatable dimensional tolerances. And there are resins available to suit most common applications.
A reputable manufacturer will positively identify all incoming raw materials, and will carefully control every stage of production to ensure process repeatability. Full ISO certification is a good demonstration of their commitment to excellence.
Get 7-day standard lead times on simple parts between 0.5 in. x 0.5 in. and 4 in. x 3 in. Upload your part to see if it’s eligible.
There are several benefits to choosing an on-demand production option for your plastic mold needs. Perhaps the most obvious benefit is that it allows you to only produce what you need, when you need it. This can help save on costs associated with inventory and storage. Additionally, on-demand production can help reduce lead times and improve flexibility in your supply chain.
Generally, the cost of a plastic injection mold starts at around $3,000. This is for a simple mold that is relatively small and does not have any intricate designs. If the mold is larger or more complex, the price will increase.
A core cavity approach to injection molding is a process whereby a mold is created with an inner core that forms the shape of the desired product. The molten plastic is then injected into the mold and allowed to cool, forming the product.
There are several reasons why a company might choose to modify a mold. In some cases, the original mold was not designed correctly and needs to be modified to fix the problem. Other times, a company may want to change the design of the part that is being produced.
As the years went by, and more companies began to specialize in mold building, the prices began to come down. Today, the cost of a plastic injection mold is much lower than it was in the past.
There are many advantages to plastic injection molding. These include the ability to make large volumes of parts quickly, high surface quality, many resins to choose from, color flexibility, and durable tooling that can last for years.
This approach has several benefits over traditional injection molding methods, including increased accuracy and precision, as well as decreased production time and costs.
Injection mold tools can be textured to provide a variety of functional and cosmetic features to molded parts. Learn how we do it in this Serious Engineering video.
In Episode 11 of Serious Engineering, Star Rapid CEO Gordon Styles takes us through a closer look at four of the most common resins used for plastic injection molded parts.
Injection molding is a process that was invented in the late 1800s, and it has come a long way since then. The first plastic injection molding machine was created in 1872 by John Wesley Hyatt, who was trying to find a way to make billiard balls without using ivory. Ivory was becoming increasingly expensive and difficult to obtain, so Hyatt came up with the idea of using a mold to create the balls from celluloid instead.
Plastic resins expand and contract because of temperature, mechanical stress and moisture. Our manufacturing tolerance guide gives you general information on the shrinkage characteristics of most common resin types to help guide your design decisions.
Get 7-day standard lead times on simple parts between 0.5 in. x 0.5 in. and 4 in. x 3 in. Upload your part to see if it’s eligible.
With all of these factors affecting the cost, it can be difficult to determine what is a “reasonable” price for a plastic injection mold. However, there are some general guidelines that can be followed.
Plastic products used in agriculture must be strong and durable, able to resist UV light and chemicals. Engineered plastic parts are used in conveyor belts, drive trains, feeders, water sprinklers, fencing, tools, and much more. Learn why plastic injection is a great solution for the agriculture industry.
We support your development goals by having no minimum order volumes or value for our injection molding production. In addition, we have a proprietary AI quoting algorithm that provides fast, accurate, and transparent pricing on every project, every time.
Components like circuit boards, switches, wires, batteries, and sensors must be placed in strong, lightweight, non-corrosive, and non-conductive housings to protect them while also safeguarding the user. Learn why plastic injection molding is an ideal solution to support the electronics industry.
Star Rapid is a world-class provider of advanced plastic injection molding services. We offer a complete manufacturing solution that covers every aspect of raw material verification, tool making, part fabrication, finishing, and final inspection. Our international team of manufacturing experts is committed to providing you with the highest level of professional support for plastic injection molding services of any size or complexity.
Plastic is very useful in the medical field. Resins are lightweight, non-toxic, inexpensive and can be reused or recycled. Applications include syringes, catheters, dispensers, tubing, and other appliances. For more information about plastic injection molding in the medical field, read our blog post.
Star Rapid operates a world-class manufacturing facility. Talk to our experts who will help you to make your design ideas a reality.
The steel,size and complexity of the mold will have the biggest impact on the price, but other factors like the material and the turnaround time can also affect the cost.
Depending on the complexity of the design and possible heat treatment, a plastic injection mold tool can be made in five days to two weeks.
Injection molding enables mass-producing plastic parts with consistency, detail, and efficiency. While a highly cost-effective process, developing an accurate budget requires evaluating numerous cost components. We’ll explore fixed and variable costs, quoting considerations, design strategies, tooling factors, and advice for minimizing overall expenditures without sacrificing part quality.
In this Serious Engineering video, Star Rapid CEO Gordon Styles offers some helpful strategies for dealing with weld lines and witness marks on plastic injection molded parts.
Injection molding undercuts can be a difficult and costly problem to fix. They are caused by the mold not being able to release the part from the mold cavity. Undercuts can also lead to the material not flowing properly into the mold cavity.
Ultimately, the decision of what size plastic mold to use should be based on what is most likely to produce the desired results at a reasonable price. Taking into account all of these factors will help ensure that the final product is exactly what is needed.
In general, small and simple molds can start at around $1,000, while larger and more complex molds can cost tens of thousands of dollars. The price of the mold is just a small part of the overall cost of manufacturing a product though. It is important to factor in the cost of materials, labor, packaging, and shipping when determining the final price of a product.
One reason why the cost of a plastic injection mold has decreased is because of advancements in technology. In the past, molds had to be built by hand which was very time consuming and expensive. Today, molds can be built using CNC machines which are much faster and less expensive.
The cost of a plastic injection mold is mainly driven by the part geometry, the material being molded, and the complexity of the mold.
In order to produce a high quality product, it is important to get rid of unnecessary features and simplify the design injection molding.
At Star Rapid we specialize in producing high-quality plastic injection molded parts and mold tools. We offer machining and finishing services to make tools from various materials and can produce 50 to 100,000+ finished parts in a wide variety of plastics. Our international team of engineers and technicians is dedicated to making your custom parts using the most advanced equipment and techniques including Plastic Injection Moulding, CNC Machining, 3D Printing and Vacuum Casting. We’re here to make your product ideas a reality!
Our quality-control system includes several steps to ensure safe, high-performing products for our clients. As with all of our services, we conduct comprehensive material verification and testing before molding begins. This includes the metal used in our molds and the plastics used in production. During production, we carefully control all processing conditions — including temperature and humidity — to maintain repeatable results. Many molding companies neglect to do this, which can lead to flaws in the finished parts. We also 3D scan complex shapes to ensure accuracy.
The mold constitutes a significant upfront fixed cost, so minimizing its expense is crucial. Factors influencing mold costs include:
This will minimize the potential for defects and improve the overall efficiency of the production process. There are a few key things to keep in mind when simplifying a design for injection molding:1. Remove any features that are not absolutely essential to the function or aesthetics of the final product.
A comprehensive design for manufacturing review comes with every tool and product design project. You’ll receive superior results while saving time and money.
When it comes to the cost of a plastic injection mold, there is no definitive answer. The reason for this is because there are so many variables that can affect the price. Some of these variables include:
As the world increasingly moves away from traditional manufacturing methods, on-demand production is becoming a more popular option for businesses. Plastic molding is one area where on-demand production can be a great option for businesses. There are many benefits to choosing on-demand production for your plastic molding needs, including a reasonable price.
Plastic injection molding is the process of filling a mold tool with liquid plastic resin under great pressure. The tool may comprise a single cavity or hundreds of cavities in order to make indefinite numbers of parts. Once the mold tools have been carefully designed and manufactured, the molding process consists of the following basic steps:
A product developer should be looking to save money on the cost of a mold tool. In most cases, a less expensive tool is going to be of poorer quality, less durable, with looser tolerances and a bad surface finish. These are not cost-savings. Instead, they’re expensive mistakes. Rather, savings can be made long-term through production efficiency, fast cycle times, and process stability. As volumes increase, the relative cost of the tool goes down until it’s almost free.
The steel material the mold is made from also plays a role in its cost. Molds can be made from various metals, plastics, or even composites. Molds are generally more expensive when made of more expensive steel, like S136, which costs three times as much as P20.
Raw plastic pellets are first dried and, if necessary, mixed with coloring agents. Inside the machine the pellets are heated and mixed until the resin is semi-liquid. This liquid is then injected under high pressure through a nozzle and into the gate and runner system of the mold. Resin fills the cavity, forming the shape of the part. It’s then cooled, the part ejected, and the process begins again.
Unless otherwise specified, we comply with the DIN 16742 standard tolerances for injection moldings. Ensuring the highest quality is an important part of our production process. Be sure to read about the visual quality standards guide that we apply to injection molded parts.
The cost of a plastic injection mold tool can be a significant percentage of the total order for small volumes. However, this cost can be amortized over larger volumes so that it doesn’t become an issue. Rather, plastic resin and cycle times become the main cost drivers for larger volumes.
After receiving your drawings, our engineers will analyze your custom plastic injection molding parts right away. We actively work with you to clarify all details before providing a quote that is both economical and accurate.
We use plastic every day for work and play. Plastic compounds with different chemical properties are found in computer keyboards and mice, game controllers, headphones, toys, home appliances and kitchen gadgets – anywhere you look. Learn more about plastic used for consumer products.
The cost of injection mold can vary based on a number of factors, but the median cost is around $3,000. The price range can be as low as $1,000 or as high as $10,000, so it’s important to get quotes from multiple companies before making a decision.
Thousands of companies of every size from around the globe have chosen to work with Star Rapid to help them develop new injection mold tools and finished parts. Your success is the foundation of our reputation.
Understanding how to accurately estimate and minimize injection molding costs is key for creating viable, cost-optimized plastic products. This comprehensive guide covers the factors comprising total molding costs and advice for effective budgeting.
Estimating injection molding costs requires understanding the diverse factors comprising the total expenditures. Simplifying part geometries, standardizing tooling, and optimizing processes offer significant savings over a program lifespan. Collaboration between product developers and molders, combined with emerging technologies, ensures cost-effective, quality plastic part production.
When it comes to injection molding, the design of self-mating parts is an important consideration. This is because self-mating parts must be able to fit together perfectly in order to function properly. Injection molding is a process that can create very precise parts, so it is important to take advantage of this when designing self-mating parts.
In the plastics industry,modifying and reusing molds is a common practice. It can be done with either new or existing molds and can save companies time and money.
On-demand production can save businesses money in the long run by reducing inventory costs and eliminating the delivery time. In addition, on-demand production can help businesses respond quickly to changes in customer demand.
It is also necessary to take into consideration how the plastic mold will be used. If it is for a one-time project, then a smaller size may be more cost effective. On the other hand, if the mold will be used multiple times, then a larger size may be necessary in order to avoid having to replace it frequently.
Some plastic injection molding suppliers offer “automated” DFM analysis, which is necessarily limited to only the most basic part designs on tools with no cooling circuits. This severely limits your design freedom. At Star Rapid, every project receives a personalized DFM review tailored to your exact needs.
When it comes to injection molding, there is no single “right” answer when it comes to finding the best value. However, there are a few tips and tricks that can help you save on injection molding costs. The first tip is to work with an experienced and reputable company. This will ensure that you get the best possible price for your project. The second tip is to be realistic about your project’s design and budget. Injection molding can be a complex and time-consuming process, so it’s important to have a clear understanding of your project’s requirements before getting started. By following these tips, you can be sure that you’re getting the best value for your injection molding project.
The price of a multi-cavity mold can vary depending on the size and complexity of the mold. However, in general,multi-cavity molds are more expensive than single-cavity molds.
Your regulatory compliance and your peace of mind are assured with our industry-leading positive material identification department. People trust Star Rapid when the job absolutely must be right.
We offer more than just tool making and molding services. Our complete package includes every manufacturing process you need for a total product development solution.
Mold costs can vary greatly, depending on a number of factors. A plastic mold can cost anywhere from $1,000 to $10,000. The exact cost depends on a number of factors, including the size and complexity of the mold, the material it is made from, and the company that makes it.
Simpler molds with standardized, interchangeable parts cost substantially less. Partnering with an experienced mold maker is vital for optimizing these tradeoffs.
Finally, the company that makes the mold can also affect its cost. Typically, an experienced manufacturer that makes molds for many industries and types of products will have experience and be able to make the mold in less time, which can bring down your cost.
The molder then factors in their production capabilities, overhead, and desired margins when preparing a detailed quote. Leave buffer for potential changes in the design process.
GETTING A QUOTE WITH LK-MOULD IS FREE AND SIMPLE.
FIND MORE OF OUR SERVICES:
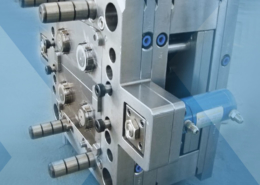
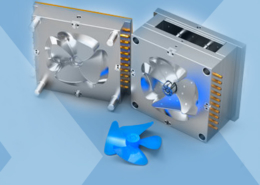
Plastic Molding

Rapid Prototyping
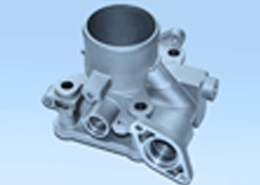
Pressure Die Casting
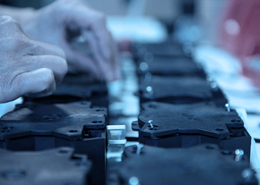
Parts Assembly
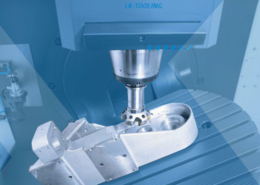