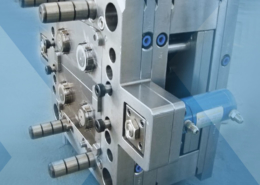
UK Plastic Injection Moulders, OGM: Your Plastic Moulding ... - plastic injectio
Author:gly Date: 2024-10-15
The mold plays a critical role in the quality of the final product. The mold material must exhibit excellent wear resistance and corrosion resistance. A well-designed gate and runner system is essential to guarantee balanced melt flow, minimizing internal stress and deformation.
To further enhance the quality and performance of the products, annealing treatment is often carried out. This process helps eliminate internal stress and improves the product's properties and stability. Annealing is typically conducted at a temperature of 70 - 80°C, with the annealing time depending on the thickness and size of the product. Additionally, surface treatments such as polishing and coating can be applied to improve the appearance and performance of the products.
In conclusion, the acrylic injection molding process is a complex yet rewarding manufacturing technique. Fine-tuning the parameters based on specific product requirements, equipment capabilities, and material characteristics is essential to achieving high-quality injection-molded acrylic products.
In the world of manufacturing, the injection molding process for acrylic, also known as polymethyl methacrylate (PMMA), is a technique that demands precision and expertise. Let's delve into the details of this fascinating process.
Barrel Temperature: This is typically controlled in three zones. The front zone ranges from 210 - 230°C, the middle zone from 220 - 240°C, and the rear zone from 200 - 220°C. Injection Pressure: A relatively high injection pressure, usually within the range of 80 - 130 MPa, is required to overcome the viscosity of the melt. Injection Speed: A fast injection speed is employed to reduce the melt's residence time in the mold cavity and lower internal stress. Holding Time and Pressure: Appropriate holding time and pressure help compensate for the melt's shrinkage, enhancing the product's dimensional accuracy and stability. Mold Temperature: It is commonly controlled at 60 - 90°C to facilitate the cooling and solidification of the product.
The first step in the acrylic injection molding process is the careful selection and preparation of materials. High-quality acrylic pellets are essential to ensure the final product's purity and stability. These pellets need to undergo a drying process, typically at a temperature range of 80 - 90°C for 2 - 4 hours. Moisture removal is crucial as it prevents the formation of bubbles and silver streaks during the injection molding process.
The dried acrylic pellets are loaded into the injection molding machine's barrel. The material is heated and plasticized until the melt achieves the desired fluidity. The melt is then injected into the mold cavity. Subsequently, the holding, cooling, and solidification stages take place.
Choosing the right injection molding machine is paramount. The machine should possess precise temperature control and adjustable injection pressure capabilities. A suitable screw is also necessary to ensure uniform plasticization of the material.
GETTING A QUOTE WITH LK-MOULD IS FREE AND SIMPLE.
FIND MORE OF OUR SERVICES:
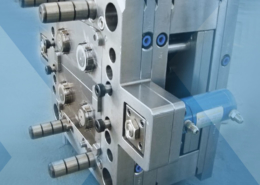
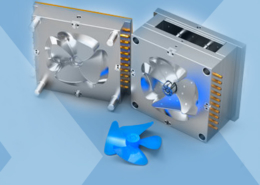
Plastic Molding

Rapid Prototyping
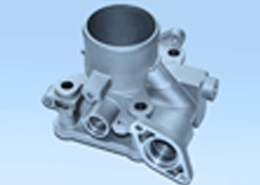
Pressure Die Casting
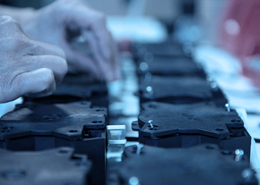
Parts Assembly
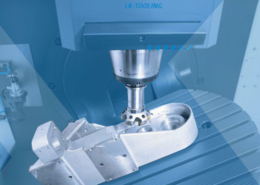