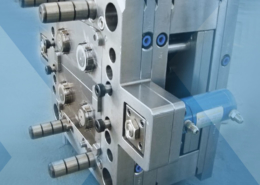
Types of Plastic Molding - molded plastic products
Author:gly Date: 2024-10-15
This website uses cookies so that we can provide you with the best user experience possible. Cookie information is stored in your browser and performs functions such as recognising you when you return to our website and helping our team to understand which sections of the website you find most interesting and useful.
Our medical device injection molding product finishing capabilities include hot stamping, banding, pad printing, silk screening, flaw coating, conductive painting, cosmetic painting, metalizing, and plating.
Our precision injection molding options, including medical device injection molding, include scientific molding, R&D molding, high-cavitation molding, micro molding, over molding, and insert molding.
Structural foam is a manufacturing material which pairs a foamed core with a solid outer layer. It is lightweight and flexible but maintains the good strength and stiffness compared with traditional polymers. Here is a list of the top 6 advantages when thinking about structural foam.
Our mold maintenance plans for projects that include medical device injection molding services ensure each mold undergoes regular cleaning and review at predefined intervals based upon the number of setups and cycles. Mold inspections, general mold maintenance, major mold maintenance and preventative maintenance are standard operating procedures.
This website uses Google Analytics to collect anonymous information such as the number of visitors to the site, and the most popular pages.
For the consumer market, including medical device injection molding, we specialize in the automated production of high-volume disposables, unit-dose packaging, caps and closures, and over-the counter diagnostics and drug delivery applications.
One of the biggest challenges in any new product development effort is identifying skilled people who can contribute significantly to the project, including the vendors who support the process. Ensuring the success of a new product demands the freedom to use new materials and new suppliers, as complex design and production challenges arise.
Far more than the simple application of additives, the key to success in this molding type is the ability to incorporate structural foam into a custom design.
Our assembly and joining capabilities include product filling, foil/heat sealing, ultrasonic welding, heat staking, mechanical assembly, pinning & UV/hot melt gluing, custom packaging/kitting, and pouching. And this includes medical device injection molding.
Our molding experience covers the knowledge of good Design for Manufacturability, a comprehensive understanding of all thermoplastic resin families, and custom injection-mold design expertise. Typically, we stock more than 150 varieties of resins at any given time in our 200,000-square-foot facility, conveniently located to the major markets of the Midwest and East Coast.
Ferriot’s structural foam molding process manufacturer services extend through final production, complete with custom color, cosmetic finishing, and assembly.
Each development project requiring medical device injection molding services is managed by a Project Engineer who monitors and controls deliverables and provides regular status updates.
Our mid to high-volume automated and semi-automated manufacturing of plastic, including medical device injection molding, injection-molded components and assemblies for single-use, metered-dose, and multi-use disposables for the drug delivery, consumer packaging and diagnostics industries offer high quality at economical value.
The production molds for medical device injection molding projects include high cavitation SPI Class 101 and 102 molds constructed from hardened steel. Cold, runner, hot sprue, and hot runner molds are designed with up to 128 cavities.
We have developed hundreds of products, some with medical device injection molding, and manufactured millions of parts annually for the medical industry. Medical devices include point of care diagnostics, microfluidics, and pharmaceutical drug delivery applications.
We provide medical device injection molding services in New York, New Jersey, Connecticut, Pennsylvania, Florida, California, Illinois, Oregon, Maryland, Massachusetts, Colorado, and Michigan and other regions.
As one of the few “systems houses” in North America, Ferriot can step in at any point in the manufacturing process because our engineering, design, molding, and tooling, and finishing technologies can be applied to products in concept development or at any other stage of production.
With our highly experienced team of engineers, we design and engineer custom structural foam solutions that didn’t exist yesterday (except in the minds of our customers).
Clients trust Natech to be the medical device injection molding experts in engineering and manufacturing. Our engineers’ experience includes mold qualifications in medical IQ/OQ/PQ, high volume automation in consumer packaging, and engineering-grade resins and ultra-polymers in electronics.
Natech’s projects that include medical device injection molding services are supported by MoldFlow Analysis, a Viscosity Curve, a Cavity Balance Study, a Pressure Window Characterization, a Gate Seal Time Study, and a Cooling Time Study. Natech engineers are masters of insert configuration and design single-cavity R&D molds with steel inserted areas. Interchangeable plates, inserts, and sub-inserts allow for more rapid design iterations at LOWER cost than creating new molds for each feature variation. SPI Class 103 and 104 molds are constructed from P20 steel and aluminum with hot runners and cold runners.
Ferriot’s experienced engineers are here to guide you through every critical step in your injection molding journey, from concept to completion.
As structural foam injection molding process gains increased attention, you may be wondering whether it’s time to replace metal or traditional plastic components with lighter and stronger engineered plastics.
We are an ISO-certified, family-owned provider of engineering, custom injection molding, and contract manufacturing. Our clients bring demanding applications requiring medical device injection molding services and best served by expert engineers.
Overall, structural foam molding offers a compelling combination of strength, lightweight construction, cost-effectiveness, design flexibility, and enhanced performance properties, making it a preferred choice for various industrial applications.
When the design is just right, the result is high productivity, cost savings, and lighter plastic components that are exceptionally rigid on the exterior and foamed at the core.
Contact us to discuss the advantages and benefits of a custom design for structural foam-molded components to optimize performance.
All our injection molding presses are equipped with servo-driven robotics for high-speed automation and medical device injection molding production.
In the electronics market we draw upon deep experience in comprehensive analysis and testing for evaluation and verification to design and build lighter, more durable electronics components.
If you disable this cookie, we will not be able to save your preferences. This means that every time you visit this website you will need to enable or disable cookies again.
We take pride in the workmanship of our medical device injection molding services. All Natech tools and production parts are made in the USA. We run three shifts per day, five days per week, and weekends are run on an as-needed basis.
Indeed, the measure of Ferriot’s true capacity is our institutional expertise in resin selection to support innovative solutions.
GETTING A QUOTE WITH LK-MOULD IS FREE AND SIMPLE.
FIND MORE OF OUR SERVICES:
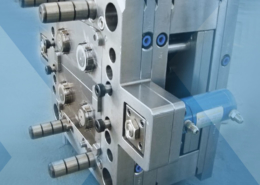
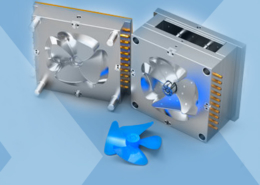
Plastic Molding

Rapid Prototyping
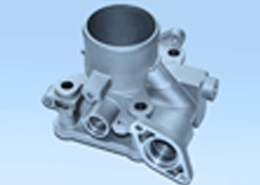
Pressure Die Casting
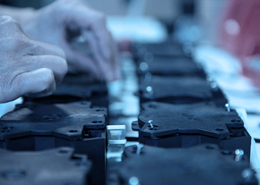
Parts Assembly
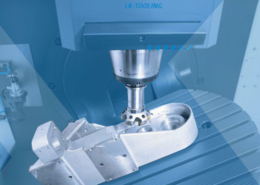