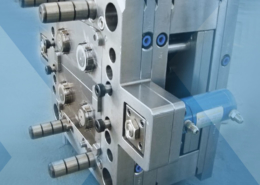
Two-Shot Molding vs. Overmolding Understanding the ... - two shot injection mold
Author:gly Date: 2024-10-15
By signing up, you agree to our Terms of Use and Privacy Policy. We may use the info you submit to contact you and use data from third parties to personalize your experience.
Our expertise in plastic injection moulding helps us to provide a complete turn-key solution for your plastic manufacturing needs, whether it’s an automotive part for bespoke custom builds or prototype construction for healthcare system components.
We exist to eliminate bottlenecks in new product development by integrating the people, processes, and platform you need to source custom parts.
By signing up, you agree to our Terms of Use and Privacy Policy. We may use the info you submit to contact you and use data from third parties to personalize your experience.
Please contact us if you would like to receive a quotation and/or to find our more about how we can provide the service you are looking for.
Class I medical devices are not intended to support or sustain life and will not present an unreasonable risk of illness or injury to a patient. Examples include wheelchairs, glasses, hospital beds, and test tubes.
Class III medical devices are usually designed to sustain or support life and may present an unreasonable risk of injury or illness. Examples include pacemakers, defibrillators, and implanted prostheses.
ISO 13485 outlines the requirements for a quality management system (QMS) when producing medical-grade products. It is the most common standard used in medical device manufacturing. ISO 13485 is not limited to plastic injection molding but rather covers the general requirements for all manufacturing technologies that are used to produce medical equipment. This standard was developed to ensure that consistent quality is maintained and that medical devices and equipment are produced in a safe and effective manner.
By signing up, you agree to our Terms of Use and Privacy Policy. We may use the info you submit to contact you and use data from third parties to personalize your experience.
Low-volume injection moulding uses softer aluminium moulds and inserts instead of hardened steel ones, which are usually simpler and less expensive to produce. These moulds are obviously not as durable as their hardened steel counterparts, but manufacturers benefit because they don’t always need to be when manufacturing low-volume components. Soft moulds, when used strategically, can lower tooling costs and shorten production times.
Access a wide breadth of capabilities through our highly vetted network.
Another important advantage of using softer injection moulds is that they rarely have a negative impact on component quality: when proper design requirements are taken into account, plastic parts made in low quantities are just as good as those produced using hardened steel moulds.
By signing up, you agree to our Terms of Use and Privacy Policy. We may use the info you submit to contact you and use data from third parties to personalize your experience.
For designers, it’s important to remember that not all polymers are suitable for medical devices. However, injection molding supports the use of many different materials, typically commodity plastics but also specialty plastics and polymer blends. Designers can also choose medical plastics that have specific trade names like ULTEM®, a polyetherimide (PEI) that can withstand repeated cycles in an autoclave. Below are some common injection molding plastics and their salient characteristics:
The ISO 10993 standard consists of 23 parts or subsections. This includes processes and procedures for animal welfare requirements, tests for carcinogenicity, reproductive toxicity, in vitro cytotoxicity, and various sterilization techniques. USP (United States Pharmacopeia) Class VI covers similar biocompatibility requirements for plastics and, as such, is sometimes used in place of ISO 10993 or as a supplement. For designers, this standard can play an important role in material selection.
The U.S. FDA (Food and Drug Administration), and the EU MDR (Medical Device Regulation) both divide medical devices into three classifications, where Class I refers to the lowest-risk medical devices and Class III refers to the highest-risk. The EU MDR further breaks down Class II devices into two subcategories: IIa and IIb.
In cleanrooms, the amount and size of airborne particles are carefully controlled to reduce the chances of exposing sensitive medical components to these particles. ISO 14644 also outlines specific requirements for designing, manufacturing, and maintaining cleanrooms for optimal performance. Designers may need an injection molder with a Class 7 or Class 8 cleanroom to limit the potential for contamination during manufacturing.
To achieve these goals, ISO 13485 outlines processes and procedures to manage risk and regulatory compliance while providing mechanisms to continuously improve the QMS whenever a gap or potential for improved performance is noted. The standard defines best practices for documentation, training, traceability, research and design, production, and how to handle non-conformances. For both the part designer and the injection molders, there are well-defined responsibilities.
Some of the cookies we use are essential for the site to work. We also use some non-essential cookies to collect information for making reports and to help us improve the site. The cookies collect information in an anonymous form. To control third party cookies, you can also adjust your browser settings.
At the same time, hardened steel, which is needed for conventional moulds, requires a substantial upfront time and financial investment. Moulds made of aluminium or lower-grade steel, on the other hand, are much less costly to make and can be made far quicker. Manufacturers may use these moulds to test and produce viable parts without having to commit to large minimum orders, allowing them to fine-tune component design and production as required. This enables producers to start manufacturing faster and, in many cases, greatly increase speed-to-market, reducing the time it takes to see a return on investment.
Medical injection molding can be used for prototyping or low-volume production, but it’s often used in high-volume manufacturing for medical devices. In part, that’s because products can be injection molded at-scale with consistent quality and with minimal human intervention. Here are some common examples of injection-molded medical products:
Accelerate development with instant quotes, expert DFM, and automated production updates.
Stephens Plastic has the expertise, knowledge, and experience to provide just what you need, whether it’s 10 or 100,000 plastic parts, thanks to its ability to provide both low and high volume injection moulding.
Designers also need to select plastics that meet medical industry standards. This article examines the standards that affect the production of injection-molded medical products. By selecting materials that meet these standards, designers do more than meet requirements from independent bodies and regulatory agencies — ultimately, they promote quality, performance, and safety.
Plastic injection molding is used in many different applications within the medical industry. Examples include enclosures for medical equipment, the overmolding of surgical tools, and spinal implants. Designers have a choice of materials, but the selected plastic must meet the application’s requirements. For example, plastics that will be sterilized with steam need to resist high temperatures and moisture, while those that will come into contact with patients must be biocompatible, meaning that they’re not harmful to living tissue.
We at Stephens Plastic are always looking for ways to improve our performance. That means working closely with and of our customers during the process, from design and prototyping to post-production and delivery, to ensure that they receive high-quality parts manufactured on a budget and delivered on time. Contact us today to learn more about how we can bring your ideas to life.
Class II encompasses any medical device for which general controls are deemed insufficient to provide reasonable safety and effectiveness. Examples include contact lenses, syringes, and pregnancy tests. The EU MDR adds two subcategories:
By signing up, you agree to our Terms of Use and Privacy Policy. We may use the info you submit to contact you and use data from third parties to personalize your experience.
The QSR (Quality System Regulations), also referred to as 21 CFR part 820, as outlined by the FDA, has many parallels with ISO 13485. In the United States, the QSR may be used as a supplement or replacement for the ISO 13485 standard.
Medical devices are classified according to their potential for causing harm to patients, the general public, or to other personnel who use or operate the medical device. This classification determines the degree of required regulatory oversight.
ISO 10993 focuses primarily on the biocompatibility requirements for medical devices. It encompasses products that are designed to come into direct or indirect contact with the body. The goal of ISO 10993 is to reduce the risk of adverse effects on patients when exposed to materials that include, but are not limited to, injection molded plastics. ISO 10993 compliant materials are non-toxic, do not affect the immune system, or do not potentially cause cancer.
Our trained employees ensure your parts will be delivered on time and to spec.
ISO 14644 regulates the use of cleanrooms during medical device manufacturing. It defines the various cleanroom classes from Class 1 to Class 9, where Class 1 has the most stringent cleanliness requirements.
Create high quality custom mechanicals with precision and accuracy.
Industry standards play an important role in the design and manufacture of medical products, especially medical devices. For designers, these standards help ensure that patients, the end-users of injection molded products, are not exposed to excessive risks during medical treatment. So injection molders must implement stringent processes and procedures to control all stages of production and comply with standards.
By signing up, you agree to our Terms of Use and Privacy Policy. We may use the info you submit to contact you and use data from third parties to personalize your experience.
Our Low Volume Injection Moulding is a specialised service that provides complete production-quality parts in quantities of 10,000 or less bits, depending on the method. Our low-volume moulding, also known as short runs, is closely supervised and regulated to ensure that all aspects of mould design and construction are met. Small and medium-sized companies, as well as small-batch manufacturing, benefit from this form of production.
By signing up, you agree to our Terms of Use and Privacy Policy. We may use the info you submit to contact you and use data from third parties to personalize your experience.
The medical device industry is tightly controlled to ensure patient safety. Listed below are some of the common standards that affect manufacturing, including plastic injection molding.
We have been established for many years and with our young and vibrant management team have vast experience in all aspects of plastic injection moulding – from the design stages through to the final packaged product.
Fictiv can produce injection-molded products for a wide range of medical applications. We have the resources, know-how, and manufacturing network to deliver the injection molded parts that you need, far faster than other manufacturers. And, we deliver 95.4% of orders on time and to spec, thanks to our network of highly-vetted partners, on-site quality engineers, and robust quality management system. Create an account and upload your medical device design today! Along with your quote, you’ll receive expert design for manufacturing (DFM) feedback and guidance to ensure you get great outcomes.
Of course, proper product design is also critical for medical devices, so check out our free Injection Molding Design Guide for best practices — it complements the info in this article. Download Fictiv’s Injection Molding Design Guide
We exist to eliminate bottlenecks in new product development by integrating the people, processes, and platform you need to source custom parts.
By signing up, you agree to our Terms of Use and Privacy Policy. We may use the info you submit to contact you and use data from third parties to personalize your experience.
By signing up, you agree to our Terms of Use and Privacy Policy. We may use the info you submit to contact you and use data from third parties to personalize your experience.
GETTING A QUOTE WITH LK-MOULD IS FREE AND SIMPLE.
FIND MORE OF OUR SERVICES:
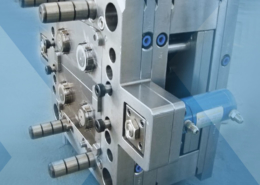
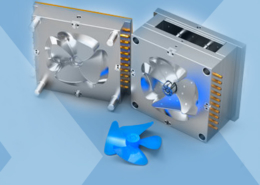
Plastic Molding

Rapid Prototyping
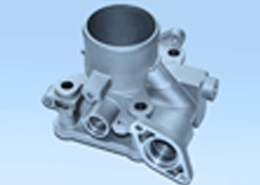
Pressure Die Casting
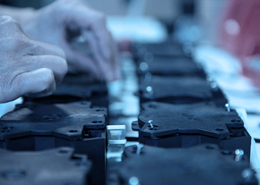
Parts Assembly
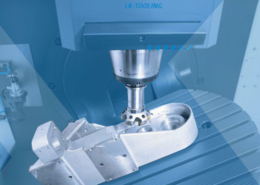