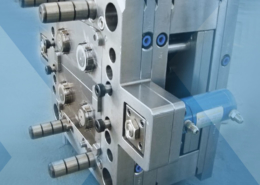
Two-Shot Molding vs. Overmolding Understanding the ... - 2 shot molding
Author:gly Date: 2024-10-15
This technique is particularly useful for larger or intricate parts where traditional gating might struggle to fill the mold entirely.
Visual Inspection: One of the quickest ways to detect short shots is by examining the part for incomplete filling, voids, or thin areas.
If the fill volume is too low or the pack and hold pressure settings are incorrect, the material won’t fill the entire mold.
However, be cautious when adding lubricants—they should improve flow without restricting the material’s ability to fill the mold.
In hot runner systems, discrepancies in temperature control can freeze flow channels, further preventing proper filling.
Improving Mold Design: In cases where the mold design is causing the issue, solutions include enlarging gates and runners, optimizing venting to avoid trapped air, or simplifying the part geometry to ensure even flow.
Additionally, flow restrictions caused by narrow runners or improperly placed gates can limit how well the material reaches all parts of the mold.
It occurs when the molten plastic doesn’t fully fill the mold, leaving voids or incomplete sections in the final product.
Main Products: Machine Part, Machining Part, Turning Part, Hardware, Injection Part, Mold, Plastic Part, Rivet, Casting Part, CNC Machining Part
Common signs of a short shot include visible gaps, weakened structural integrity, and parts that fail to meet dimensional specifications.
The primary cause of short shots is excessive flow resistance, which prevents the molten plastic from fully filling the mold cavity. Several factors contribute to this issue, including part wall thickness, mold and melt temperatures, injection pressure, and material properties. When these factors are not properly managed, short shots can occur, leaving parts incomplete.
By opening and closing gates in sequence, these systems allow for better material distribution, reducing the risk of short shots in hard-to-reach areas of the mold.
Using mold flow simulations allows engineers to refine the mold design and manufacturing process, minimizing defects from the outset.
To avoid short shots, manufacturers can optimize material selection by using materials with suitable flowability and adjusting melt temperatures. Machine settings like injection pressure and speed should be fine-tuned to ensure proper flow. Additionally, mold designs can be enhanced by enlarging gates and runners, improving venting, and ensuring consistent temperature control to prevent premature plastic solidification.
Process Monitoring: Monitoring the injection pressure, temperature, and speed during the molding process helps catch short shots in real-time, allowing for adjustments before defects occur.
Adjusting Process Conditions: Increasing injection speed or pressure can improve material flow and ensure the mold is fully filled. Sometimes, fine-tuning the melt and mold temperatures can prevent premature cooling and solidification of the plastic.
In this article, we’ll explore the causes behind short shot injection molding, how to troubleshoot them effectively, and strategies to prevent them.
Addressing short shots is crucial for maintaining high product standards and ensuring efficient production processes, saving both time and costs in the long run.
Additionally, always verify that the machine’s injection capacity matches the design and material requirements to avoid short shots caused by insufficient power or pressure.
Also, maintaining consistent mold cooling will prevent early solidification of the plastic, reducing the risk of short shots.
HITOP is committed to assisting customers by offering a comprehensive one-stop solution, encompassing product design enhancement, initial sample creation, mold fabrication, injection molding, and product assembly.
Reach out to our team today for expert guidance and solutions to enhance your production efficiency and product quality!
Progressive Short Shot Tests: This involves stopping the injection process partway through to see how far the molten plastic is filling the mold. This method helps identify problem areas in the mold design or flow.
Low melt or mold temperatures can cause the plastic to solidify before it fills the mold, leaving voids or incomplete sections.
By understanding the causes—such as material flow, machine settings, and mold design—you can implement effective solutions to optimize production and prevent these issues.
Hi, I am Sparrow Xiang, COO of the HiTop company, me and my team would be happy to meet you and learn all about your business, requirements and expectations.
Short shots happen when the molten plastic fails to fill the entire mold cavity during the injection molding process. This results in incomplete parts, often with voids or missing sections, such as a missing prong on a plastic fork. Short shots are typically caused by improper material flow, inadequate machine settings, or mold design flaws.
A short shot in injection molding occurs when the molten plastic doesn’t fully fill the mold cavity, leaving parts incomplete or missing material.
Short shots in injection molding can cause significant defects in plastic parts, impacting their quality and functionality.
Identifying and addressing short shots early on is crucial to ensuring the quality and performance of your plastic products.
We are committed to helping you elevate quality standards, fostering enterprise growth, and actualizing your internationalization strategy.
Dimensional Analysis: Measuring the part’s dimensions can reveal areas where the mold wasn’t completely filled, especially if the part is out of spec.
These tools help to identify potential problem areas, optimize gate placement, and adjust runner designs, all of which can significantly reduce the likelihood of short shots.
Before starting production, many manufacturers now use simulation software to test how the plastic will flow through the mold.
Additionally, using an undersized machine or one with insufficient capacity for the material can result in incomplete parts.
GETTING A QUOTE WITH LK-MOULD IS FREE AND SIMPLE.
FIND MORE OF OUR SERVICES:
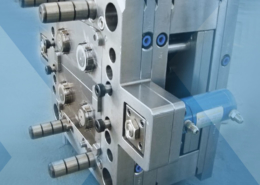
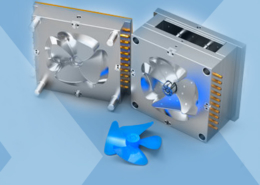
Plastic Molding

Rapid Prototyping
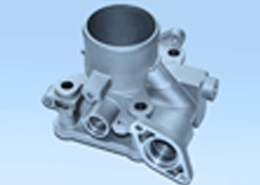
Pressure Die Casting
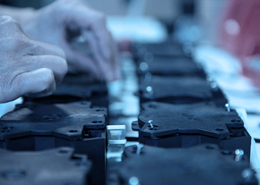
Parts Assembly
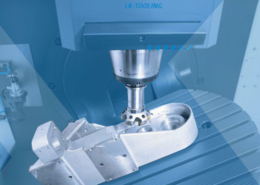