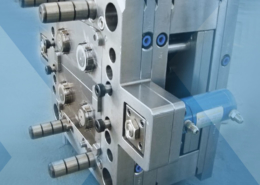
Two-Shot Molding and Tool Design - double shot molding
Author:gly Date: 2024-10-15
Our helpful design aid demonstrates part features that are too thin or too thick, bad bosses, right and wrong ribs, and other considerations to be mindful of while designing parts for injection molding.
Depending on your application's requirements, you can choose from the following when requesting an injection molding quote.
Our thermoplastic injection molding is a standard process involving an aluminum mold with no heating or cooling lines running through it, which means cycle times are a bit longer. As part of the scientific molding process, our molders independently optimize and monitor fill speed, hold pressure, and hold time, and periodically inspect part quality and cosmetics. During the molding process, we use an automated inline CMM to ensure dimensional accuracy, as well as generate a detailed process capability study and FAI report.
Prototype mould is made for pre-testing of large production, such as product structure, part function analysis and produces small lot parts for other process verification. It can reduce errors in design and risks in the development, and reduce the time for training users, which improves the system's practicality, correctness and user satisfaction.
This complete reference guide walks you through everything from quoting, design analysis, and shipment to best practices that ensure your model is optimized for molding.
Tough Black (Loctite Henkel 3843) and Ceramic-Filled (BASF 3280) are two new advanced photopolymer materials now available for 3D printing.
It's most often used for the manufacturing plastic parts at scale due to its low material waste and low cost per part. It’s an ideal manufacturing process for industries like medical devices, consumer products, and automotive.
It has been very enlightening to us here at HP that we are able to get parts so rapidly out of the actual materials that we're going to use in the final production.
Tolerances: Typically, Protolabs can maintain a machining tolerance of +/- 0.003 in. (0.08mm) with an included resin tolerance that can be greater than but no less than +/- 0.002 in./in. (0.002mm/mm).
The demand for plastic parts in the automotive industry is increasing day by day. No matter how extreme the operating temperatures are and how harsh the chemicals, Hanking can provide a variety of engineering-grade thermoplastics.
Get machined parts anodized and chromate plated with our quick-turn finishing option. Eligible materials include aluminum 6061/6082 and 7075.
Our basic guidelines for plastic injection molding include important design considerations to help improve part moldability, enhance cosmetic appearance, and reduce overall production time. View our design guidelines page for more details.
The industrial mold is an unbeatable benefit amplifier. Machining products with molds greatly improve production efficiency, and also saves raw materials, reduces energy consumption and costs, and maintains high product consistency. It includes side plate mould, pinpoint plate mould, three plate mould, reverse gating mould and stack mould.
Injection molding is a manufacturing process that consists of filling a metal mold cavity with liquid plastic resin, which then cools and forms a plastic part.
Want to learn more about injection molding? Sign up to receive a Design Cube. This physical aid demonstrates how to properly design features commonly found on molded parts.
The plastic injection mold industry is an important part of the national high-tech industry and a valuable technical resource. We optimize the structural design of the mold system and make it more intelligent, improve the forming process and mold standardization of the part, improve the precision and quality of the mold manufacturing, and reduce the amount of grinding and polishing of the surface of the part. Our plastic injection mold can be the development trend of mold production technology in the next decades.
Our digital factories create prototypes and low-volume parts fast, while our manufacturing network, offers advanced capabilities and volume pricing.
Household appliances plastic parts basically include interior plastic parts mold and the exterior plastic housing and case, which we use on a daily basis.
Hanking Plastic Injection Moulds includes automotive mold, electronic mould, home appliance mould, medical mould, insert molding, industrial mould, prototype mold, 2K mould, multi-cavity mould and precision mould, and they can be applied in various lines such as industry, automotive, environment, electronic, and consumers.
Our plastic injection molding process produces custom prototypes and end-use production parts with lead times as fast as 1 day. We use aluminum molds that offer cost-efficient tooling and accelerated manufacturing cycles, and stock about 200 different thermoplastic resins.
The manufacturing process for molded parts is complex. Before your parts are even molded, we're there to help you with comprehensive manufacturability feedback and consultative design services, so you can avoid mold design pitfalls before the resin hits the mold. From there, our production process is documented and optimized using scientific molding so you get high-quality parts consistently and reliably with every production run.
Insert molding refers to a molding process in which we prepare an empty cavity on two or more mold-specific metals, and metal material inserts into a mould and then injecting the plastic resin, and the molten material is bonded to the insert, cooled and solidified.
While the molds themselves are similar, part quantities, lifetime maintenance, quality documentation, and pricing vary depending on which service option is chosen. The right one depends on your project needs.
Resin pellets are loaded into a barrel where they will eventually be melted, compressed, and injected into the mold’s runner system. Hot resin is shot into the mold cavity through the gates and the part is molded. Ejector pins facilitate removal of the part from the mold where it falls into a loading bin. When the run is complete, parts (or the initial sample run) are boxed and shipped shortly thereafter.
No one ever said that designing and manufacturing molded parts was easy. Our goal is to get you through it quickly and with quality parts. A good starting point is our Design for Moldability Toolkit.
In HanKing Mould, we have a complete set of high-precision measurement equipment, they are all of the strict size requirements, product consistency, complex structure and durability. Our precision mould can offer full dimension FAI measurement reports. We have high-quality injection plastic molding molds for sale, contact us now.
We have wide selection of more than 100 thermoplastic and thermoset materials. And if you're looking for alternative material options, check out our guide to resin substitutes for ABS, PC, PP, and other commonly molded plastics.
Proto Labs, Inc. 5540 Pioneer Creek Dr. Maple Plain, MN 55359 United States P: 877-479-3680 F: 763-479-2679 E: [email protected]
At present, more than 90% of plastic products in our daily life are injection molded. The market prospect, capacity, and application are large and wide. The following are the basic review of plastic injection moulds' classifications.
The multi-cavity mould can produce multiple workpieces in one injection cycle for increased efficiency. It comprises a multi-cavity of the same plastic part and a multi-cavity of different plastic parts.
As the population is increasing, the medical segment is one of the fastest-growing markets, including disposable medical products as well as medical equipment internal parts.
Plastic electronic enclosures are used throughout our daily lives, such as remote control housing, plug plastic housing, electrical machine plastic cover, router housing, office appliances case, adapter charger housing mould, terminal block, mobile phone housing, terminal devices, computers products.
Critical-to-quality (CTQ) dimensions you call out on models let us know what areas are most crucial to the success of your parts. Once the parts start molding, the process and samples are qualified using automated inline CMM technology, generating a detailed FAI and process capability study with no additional lead time.
GETTING A QUOTE WITH LK-MOULD IS FREE AND SIMPLE.
FIND MORE OF OUR SERVICES:
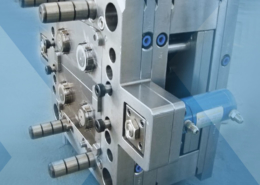
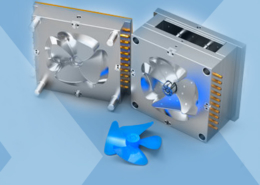
Plastic Molding

Rapid Prototyping
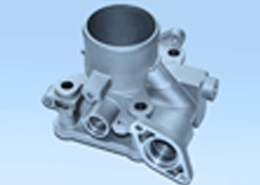
Pressure Die Casting
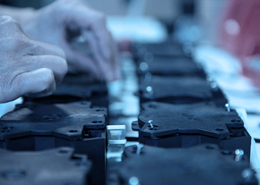
Parts Assembly
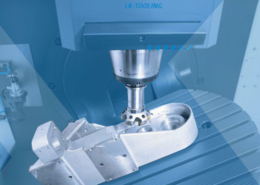