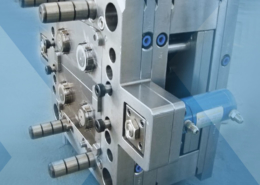
Two-Shot Injection Molding Services - two shot molding
Author:gly Date: 2024-10-15
Generally, multi-stage plasticizing temperature control is adopted, the feeding section is 180 ° C, the compression section is 190 ° C, the melting section is 200 ° C, the metering section is 200 ° C, and the nozzle is 190 ° C. The multi-stage control is beneficial to completely plasticizing without causing burns to the melt;
Overmolding is essentially a type of insert molding. However, overmolding vs. insert molding is, as the name suggests, plastic is molded over another molded part. The first component is made inside an injection mold, and it is then placed into a second mold to add the over-molded material. This technique combines multiple plastics for either practical or aesthetic purposes. For example, one might use different durometer plastics to mold a softer plastic over a more rigid one to make a part easier to grip. Using multiple colored plastics in an overmolded part can also distinguish the product from other brands. Overmolding is regularly used on the handles of tools like screwdrivers, power drills, or toothbrushes.
Once injection molding is chosen for a specific application, the next step is often whether to use insert molding, overmolding or just stick with plain injection molding. When trying to weigh the advantages of the processes, it is important to accurately define the product application. Each of these processes has specific use cases that are suited to different product types. It can be difficult to gauge which process will best suit your particular product, so itâs good to get expert advice early on. Contact a Xometry representative to leverage decades of vast manufacturing expertise. We will help steer your design decisions in the right direction so that you can choose between insert molding vs. overmolding or just injection molding.Â
Insert molding is a subset of injection molding techniques similar to overmolding where metal components are placed into a mold cavity before the actual plastic injection. The insert is precisely positioned inside the mold either manually or by a robotic arm. The mold then closes, and plastic is molded over the insert, creating a single part.
Injection molding, which includes the sub-processes insert molding and overmolding, is a versatile and low-cost manufacturing production process that is used in the large majority of consumer products. Injection molding often results in the lowest cost per part when compared to other manufacturing techniques like CNC machining and even 3D printing.Â
The content appearing on this webpage is for informational purposes only. Xometry makes no representation or warranty of any kind, be it expressed or implied, as to the accuracy, completeness, or validity of the information. Any performance parameters, geometric tolerances, specific design features, quality and types of materials, or processes should not be inferred to represent what will be delivered by third-party suppliers or manufacturers through Xometryâs network. Buyers seeking quotes for parts are responsible for defining the specific requirements for those parts. Please refer to our terms and conditions for more information.
PLA is dehydrated and polymerized from lactic acid. The stability of water is poor, and moisture causes lactic acid bond breakage. Therefore, it is necessary to sufficiently dry the raw material and control the humidity to 0.025% or less. Generally, it is vacuum dried for 2-3 hours under air humidity of 80 ° C, and needs to be sealed after drying;
Injection molding is a broad term used to describe one of the most important processes in the manufacturing industry. Itâs a process that requires a mold, typically made of metal with a cavity in the shape of the desired part. Molten plastic is injected into the mold and ejected. The process repeats to produce thousands of identical parts. Itâs safe to assume that every large-volume plastic part on the market has come from an injection molding machine because the benefits of using injection molding for production are numerous. These benefits include low cost per part, short cycle times, extensive materials, and compatible, in-tolerance parts.
Despite the many benefits of insert molding, a few disadvantages need to be considered before choosing to use this sub-process. Â
As a renewable and inexhaustible new raw material, corn plastic has an extraordinary significance in the history of plastics development. Increasing the development and application of PLA is conducive to the health and sustainable development of the injection molding industry. The exploration of the injection molding process for PLA is also an important task.
The viscosity of PLA is low, so the injection pressure does not need to be particularly high, and it is usually competent within 54Pa;
Depending on the product, the screw speed is selected between 20-100 rpm, and normal injection does not require excessive speed;
Since the crystallinity of PLA is very low and the melt strength is very small, it is required to be cooled using a mold temperature of 20-30 ° C. The mold must be equipped with a liquid cooling system to ensure that the mold temperature does not rise with the influence of the injection temperature;
We accept small batch custom molding services (Both thermoset and thermoform plastic). We CNC prototype, mold design, injection, silkscreen, engraver, assembly and packing as a whole.
The thickness of the product design is controlled within 4mm. The core, cavity or front and back stencils and sliders of the mold must be cooled by liquid to control the mold temperature;
Insert molding can also eliminate the need for fasteners by including the necessary metal parts in the mold, thus firmly securing the parts into a single bonded component.
If you has any tableware product by PLA injection molding, pls contact odin mould company,we already established a mature injection molding process for plant plastics, which will be further developed and improved in the future application and development.
There are various sub-processes within injection molding that add further capabilities to this already versatile technology. This article will explore insert molding vs overmolding and the advantages of each.
Various sub-processes add further capabilities to this already versatile technology. This article will specifically explore insert molding vs. overmolding and the advantages of each.
Despite the many benefits of overmolding, a few disadvantages need to be considered before deciding to use this process. Â
One of the most common applications for insert molding is the creation of metal attachment features for fasteners. Fasteners enable assemblies to be securely assembled and disassembled without product damage. Heat-set threaded inserts are molded into plastic to reduce the risks of thread damage during installation.
GETTING A QUOTE WITH LK-MOULD IS FREE AND SIMPLE.
FIND MORE OF OUR SERVICES:
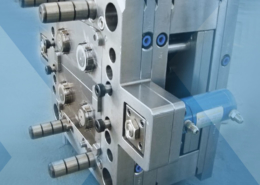
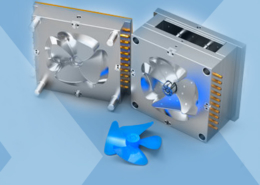
Plastic Molding

Rapid Prototyping
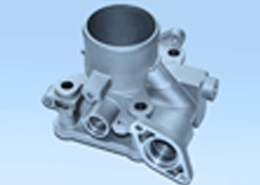
Pressure Die Casting
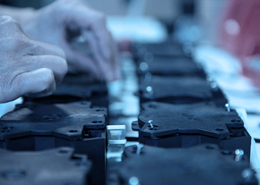
Parts Assembly
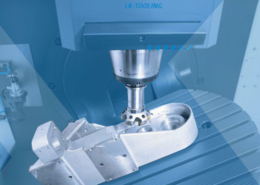