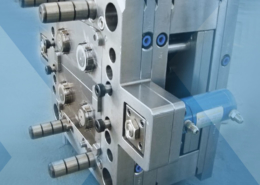
Two-Shot Injection Molding Services - two shot molding
Author:gly Date: 2024-10-15
Prototype production is a necessary part of the injection molding industry because the costs associated with producing a prototype are significantly less than going straight to large scale production. Injection molding prototyping is a tried and true method for ensuring the mold is accurately designed prior to reproducing hundreds, thousands, or even millions of parts. Nothing can compare to the feeling of confidence that comes with holding a nearly finished version of your product before entering the production phase. This will ensure what you have designed and engineered will be exactly what you receive.
UHMW has a wide range of applications across various industries, including automotive, aerospace, construction, and food and beverage. In the automotive industry, UHMW is used for wear-resistant parts such as gears, bearings, and bushings. In aerospace, UHMW is used for lightweight components such as the insulation around rocket boosters. In the construction industry, UHMW is used as a lining material for hoppers, chutes, and silos. In the food and beverage industry, UHMW is used for conveyor parts, food processing equipment, and packaging.
UHMW is a type of polyethylene that has a very high molecular weight, resulting in its excellent mechanical and chemical properties. Some of the key properties of UHMW include high abrasion and impact resistance, low coefficient of friction, high tensile strength, and good chemical resistance. UHMW also has a low density compared to other high-performance plastics, making it a lightweight option for many applications. Other notable characteristics of UHMW include its ability to sustain high loads over extended periods, its self-lubricating properties, and its good electrical insulation properties.
Prototype injection molding produces real injection molded parts for functional testing. Injection molding prototyping can also serve as bridge tooling to fill the manufacturing gap before production tooling or when production tooling goes down.
In conclusion, UHMW is a versatile material that offers an excellent combination of properties, making it an ideal choice for many applications. Its unique set of properties such as high abrasion resistance, low coefficient of friction, and good chemical resistance make it widely used in various industries. With its available processing methods, UHMW can be easily molded, extruded, or machined to meet the specific requirements of a given application.
A prototype mold is essentially the same as a production mold. It can produce the same parts as a production mold but is only warrantied for 10,000 cycles. Production molds will typically last for 100,000 cycles or more. The only real difference between prototype molds and production molds is the mold material. Prototype molds are made of softer steel that is easier to cut but does not last as long. ICOMold’s production molds are all made with high-strength steel and built to last.
Fast Part Quote and Molding Low Cost, Quick Build, and Good Quality Online Project Management Trouble-Free Part Modifications No Size Limitations Any Commercially Available Material and most standard Surface Finishes
The current manufacturing trend is to use 3D printing to produce prototype parts. While 3D printing is a quick and efficient way to produce prototypes, it does have some serious drawbacks. Material choice is the biggest limitation when using 3D printing for prototypes. 3D printing can only use very specific materials that may not hold up to the demands of testing. Prototype injection molding will produce usable parts in the same material as the final part. This will allow designers to test the form, fit, and function of the part without worrying about differences in the material characteristics.
All projects are assigned a dedicated project manager and engineer to ensure your prototype injection molding project is done on time and in budget. For more information, please check out ICOMold’s Online Project Management System.
UHMW can be processed using various methods such as compression molding, CNC machining, injection molding, and extrusion. Compression molding involves applying heat and pressure to reshape the material into the desired shape. Injection molding involves melting the UHMW pellets and injecting the molten material directly into a mold. Extrusion involves melting the UHMW material and passing it through a die to form a continuous profile. Each method has its advantages and disadvantages, and the choice of processing method will depend on the specific application requirements.
UHMW is an excellent choice for many parts applications due to its unique set of properties. Some common UHMW parts applications include wear strips, guide rails, rollers, seals, and gaskets. UHMW wear strips are used in conveyor systems to reduce friction and extend the life of the equipment. Guide rails made from UHMW are used in packaging machinery to ensure accurate product placement. UHMW rollers are commonly found in packaging, bottling, and material handling industries due to their low friction and abrasion resistance.
ICOMold’s fast-turn, low-cost, high-value injection molding enhanced by joining Fathom’s manufacturing platform. Learn More
Prototype plastic injection molding can be done very quickly. The initial part will have the shape and functionality a plastic prototype part would need for testing form, fit, and function, but may not have fine details like color or surface finish preference. Prototype molds are built to handle minimum of 10,000 cycles.
GETTING A QUOTE WITH LK-MOULD IS FREE AND SIMPLE.
FIND MORE OF OUR SERVICES:
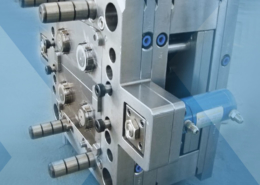
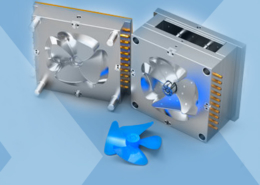
Plastic Molding

Rapid Prototyping
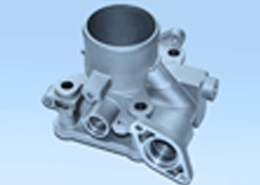
Pressure Die Casting
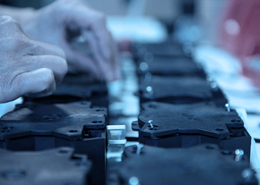
Parts Assembly
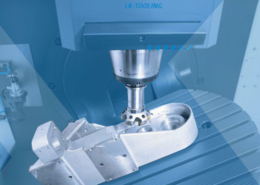