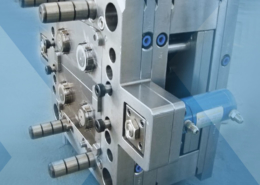
Two Shot Injection Molding Design Guide - 2 shot molding
Author:gly Date: 2024-10-15
Nylon plastic injection molding material can be used in a great diversity of application projects, including clothing, rubber material reinforcement such as car tires, applications as a rope or a thread, as well as a great number of plastic injection molded vehicle parts and mechanical equipment. It is especially strong, resistant to abrasions, moisture absorption and chemicals, as well as durable, elastic and easy to clean. Nylon is able to be used to replace the low strength metal materials. By virtue of its strength, temperature resilience and chemical compatibility, it is the ideal plastic material for production of vehicle engine components.
Since we have already known the purposes of the nylon plastic injection molding material, now let’s take a look at some of its key properties and features. The Nylon plastic is a condensation copolymer that consists of several different types of monomers combined with each other. It is able to be produced in many different ways, usually starting with distillation from crude oil, but is also able to be made from biomass. Nylon falls into the thermoplastic (as opposed to “thermoset”) material classification, which describes how the material responds to heat. When heated to their melting temperature, the thermoplastic materials will liquefy (a temperature as high as 220 degrees Celsius for the Nylon plastic). One of the major advantages of the thermoplastic materials is that there will be no significant degradation after they go through the process of heating to their melting temperature, cooling and reheating. Thermoplastics like the ABS plastic will not burn. Instead, they will become liquid, so they can be easily injection molded and then recycled. On the contrary, the thermoset plastic materials only allow for one-time heating (especially during the plastic injection molding process). When being heated for the first time, the thermoset materials will set (like a 2-part epoxy), leading to a chemical alteration that is impossible to reverse. If you ever try to heat a thermoset plastic material to a very high temperature for a second time, it will burn. This is the characteristic that defines the thermoset plastics.
Despite the fact that the Nylon injection molding plastic was first discovered and patented by Dupont’s Wallace Carothers, it was not produced (as Nylon 6) until 3 years later in 1938 by a German research chemist, Paul Schlack who then worked at IG Farban, by employing a different approach. At present, it is now produced by a great number of companies worldwide, each usually having their own manufacturing processes, exclusive formulas and trade names.
In addition, the nylon material is also able to be negatively affected by exposure to UV rays mainly from direct sunlight. As a result, before the plastic injection molding process, a UV stabilizer is usually added to the plastic.
The Nylon plastic injection molding is also able to be used in conjunction with a great number of additives for production of various variants with an extensive range of different features and properties. Now, let’s take a look at how a composite gear is made by combining both Nylon and carbon.
With regard to unfilled nylon grades, the shrinkage rate is usually between 0.01 and 0.015 mm/mm (1 – 1.5%). The addition of glass fibers is able to limit the shrinkage rate to 0.3% in the flow direction (but may be up to 1% in the cross-flow direction). Mainly, the crystallinity and moisture absorption levels are the 2 factors that affects the post-molding shrinkage rate, while the actual shrinkage rate is a result of multiple combined conditions, including part design, wall thickness and processing environment.
Nylon, usually referred to as “PA” (chemical designation, e.g. PA 6 or PA 6/66), often comes in black, white or its natural color (off white or beige). Nylon 6/6 is perhaps one of the most commonly seen variants for engineering applications. Thanks to the fact that it can be extruded, nylon 6/6 is a good choice for both plastic injection molding and 3D printing. Its high melting point makes the material an ideal replacement for metals in applications under high temperature conditions (e.g. in the engine compartment of a car).
The most commonly used types of nylon are Nylon 6, Nylon 6/6, Nylon 66 and Nylon 6/66. The numerals in the nomenclature indicate the quantity of carbon atoms between acid and amine groups, while the single digits, such as 6 mean that the plastic is produced from a single monomer in conjunction with itself (i.e. the molecule in general is a homopolymer), the two digits, such as 66, mean that the plastic is produced from several monomers in conjunction with one another (comonomers), and the slash means that the plastic is made up of multiple comonomer groups in conjunction with one another (that is to say it is a copolymer).
GETTING A QUOTE WITH LK-MOULD IS FREE AND SIMPLE.
FIND MORE OF OUR SERVICES:
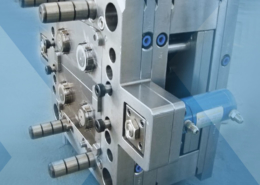
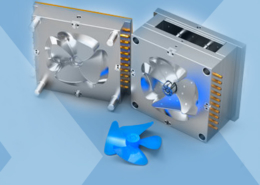
Plastic Molding

Rapid Prototyping
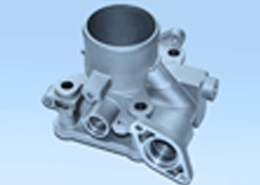
Pressure Die Casting
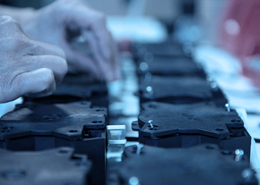
Parts Assembly
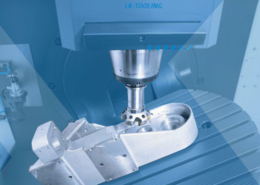