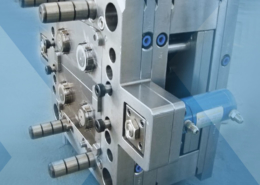
Two Shot - two shot moulding
Author:gly Date: 2024-10-15
Because of its ability to create intricate multi-material designs within a single production cycle, 2k injection molding is ideally suited for crafting electronic device casings with built-in buttons or grips. With double shot injection molding, manufacturers can incorporate both hard plastic for durability and soft rubber-like material for tactile buttons or grips. This seamless integration within a single part enhances the user experience without requiring separate assembly steps, offering an efficient way to create complex designs with high precision. The automotive industry also benefits from this technique, where dashboards and control panels can feature different textures and materials to enhance both aesthetics and functionality.
Overmolding, on the other hand, involves molding an additional layer of material over an existing part or substrate. Unlike double shot injection molding, where two materials are injected into a mold in sequence, overmolding often involves a separate molding operation on an already-formed part. This process can involve various techniques and is often used to add functionality, aesthetics, or protection to an existing part.
While similar, the processes differ somewhat significantly when you look at the details. Let’s look more closely at the processes step-by-step to enable a proper comparison.
Both double shot plastic injection molding and overmolding find applications in various industries, including consumer electronics, automotive, medical devices, and other consumer products like toothbrushes and kitchen utensils. However, they are often selected for specific applications due to their distinct strengths.
Understanding the more detailed aspects of 2k injection molding and overmolding helps engineers select the best approach for their manufacturing needs, ensuring high-quality products with unique characteristics and functionalities. Some of these special considerations include the following:
Nelson Miller Group is your go-to partner for injection molding and other thermoplastics manufacturing. We’ve got the expertise, capabilities, and equipment to make your project a success. Contact us today to discuss how we might be able to help you with your next plastic project.
Double shot plastic injection molding, also known as 2K injection molding, involves injecting two different materials into a single mold to create a single part. This method is ideal for producing parts with multiple colors or materials without requiring additional assembly. It allows for complex designs, reduction of manufacturing time and costs, and access to a broad range of injection molding applications.
While both double shot injection molding and overmolding require specialized tooling and equipment to ensure successful manufacturing, double shot plastic injection molding requires entirely different injection molding machinery. A machine equipped for 2k injection molding typically includes a rotating or shifting mold to allow for the secondary injection. This type of equipment demands precise control over multiple injection parameters, such as temperature and pressure, as well as additional controls for proper mold rotation and alignment.
Because of the process differences, double shot/2k injection molding and overmolding have their own benefits and drawbacks that must be considered when choosing between them:
With overmolding, design considerations must be made to achieve a proper fit between the existing substrate and the overmold. This often involves creating features like grooves or undercuts to enhance bonding or facilitate secure placement of the primary part in the mold.
NMG has more than 85 years of experience partnering with organizations to bring their industrial, IoT, lighting, medical, telecommunications, consumer, and aerospace products to life. We solve your most complex challenges in engineering design, manufacturing, and supply chain management.
In the case of double shot injection molding, the mold design has to account for both the primary and secondary injections to ensure the mold can accommodate the sequence of operations. Complex geometries, wall thickness, and material flow paths must be carefully engineered to prevent defects like warping or incomplete fills.
In overmolding, the equipment needs to support the placement of existing parts and provide reliable mechanisms for securing and overmolding them. This might require additional fixtures or custom-designed molds to accommodate varying shapes and substrates, but rarely requires new equipment altogether. The cost/availability of the right equipment may be the deciding factor for an engineer considering double shot plastic injection molding vs. overmolding.
Double shot plastic injection molding and overmolding are powerful techniques. By combining multiple materials, colors, or textures in a single part, these methods offer a high degree of design flexibility and efficiency. While both methods present unique challenges, their benefits make them valuable tools for engineers seeking innovative solutions for plastic manufacturing.
When determining which method is right for your project, you’ll need to understand how both processes work, as well as the benefits and challenges of each. In this guide, we’ll outline the most important considerations when you’re deciding whether double shot injection molding or overmolding is a better fit for your needs.
In both applications, the overmold material should be selected based on desired characteristics such as flexibility, texture, and color. Compatibility is not only about the physical properties but also the chemical interaction between the substrate and overmold. Proper bonding is essential to ensure the durability and integrity of the final product.
To ensure proper alignment and bonding, both processes require detailed planning in the design phase. Proper mold design is critical to ensure successful manufacturing in both processes.
Like selecting any manufacturing partner, finding the right manufacturer for double shot plastic injection molding and overmolding is critical. Here are some things to consider as you evaluate potential partners:
The primary substrate serves as the foundational layer onto which additional materials are applied. The choice of substrate largely depends on the required properties of the final product, such as strength, rigidity, and thermal resistance. Common primary substrate materials in double shot injection molding include ABS (acrylonitrile butadiene styrene), PC (polycarbonate), and PA (polyamide). These materials are valued for their structural stability and compatibility with a variety of overmold materials. With overmolding, substrates can be even more diverse, including metals and other plastics.
Overmolding is often used to add a protective or functional layer over an existing substrate. For example, one common application is in the production of power tool handles, where the base handle is molded from a rigid plastic, and a softer, shock-absorbent rubber is overmolded for added comfort and grip. This approach is also suitable for integrating electronics, where a circuit board or metal component can be securely encased with a protective plastic layer to shield it from environmental factors. The versatility in dealing with different substrate materials provided by overmolding allows for additional customization and flexibility in design, making it ideal for applications where the base part requires a unique coating or enhanced functionality through an additional layer.
To achieve a strong and durable connection between materials, both 2k injection molding and overmolding require a proper curing and bonding process. Of course, quality control is vital in both processes—thorough testing is required to ensure proper curing and bonding. Factors such as surface preparation, injection speed, and curing time play significant roles in achieving a successful bond.
Because double shot injection molding takes place in one production cycle, curing occurs at the conclusion of that cycle. Precise control over temperatures, pressures, and injection timings is necessary, and proper curing temperatures and duration ensures proper chemical and mechanical adhesion. In overmolding, the bonding mechanism often involves additional bonding agents or coatings to enhance adhesion.
Choosing the right overmold material is crucial for achieving a successful bond with the primary substrate and ensuring overall product durability. In double shot plastic injection molding, compatibility between the two materials is key. Common overmold materials include TPE (thermoplastic elastomer), TPU (thermoplastic polyurethane), and various types of softer plastics. Overmolding allows for greater versatility in overmold material selection, enabling the use of materials that might require additional processing or specific conditions to bond effectively with the substrate. Material selection also plays a significant role in adding tactile features, aesthetics, or protection to the product. Common overmold materials in overmolding include silicone rubber PP (polypropylene), and transparent acrylic-based polymers.
2k injection molding involves only one mold and production cycle, in which the primary substrate is injected first, followed by a secondary injection of the overmold material.
In contrast, overmolding is a two-step process that involves molding an additional layer onto an existing part, which can be plastic, metal, or other materials. Overmolding is often used to add protective coatings, soft-touch grips, or other functional enhancements to existing products.
Double shot injection molding and overmolding are two high value-added techniques used in plastic injection molding. Both methods are used to create complex parts with multiple colors, materials, or textures, often eliminating the need for additional post molding operations. While they’re often thought of in the same category, though, these techniques differ substantially in terms of process and have their own unique benefits and drawbacks.
GETTING A QUOTE WITH LK-MOULD IS FREE AND SIMPLE.
FIND MORE OF OUR SERVICES:
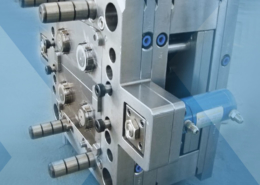
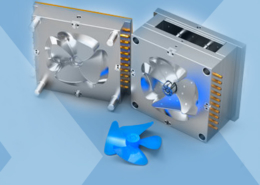
Plastic Molding

Rapid Prototyping
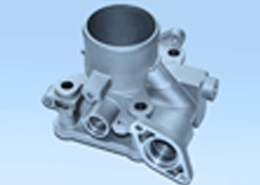
Pressure Die Casting
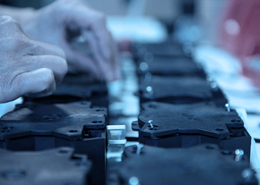
Parts Assembly
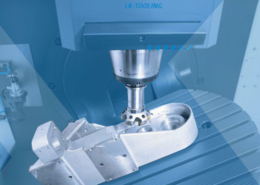